Balancing Performance in Waterborne Coatings

It is no surprise that waterborne coatings dominate the North American architectural coatings segment, a fact that is mainly due to their environmental friendliness and ease of consumer use. In a 2017 independent architectural paint market study, the size of the North American architectural waterborne paint segment was more than 4.7 million metric tons. 1 The residential repaint and remodel market, which includes consumer Do-It-Yourself (DIY) and contractor paints, accounts for more than 67% of that segment. This breakdown highlights that the number of new homeowners, existing homeowners and contractors painting is increasing every year.
For those segments, high value is placed on balanced performance. These performance and application targets are highlighted in the products label claims. Through a survey of those claims from 14 top-tier paint lines, one can see that stain resistance, durability and one-coat hide are three of the most highly valued performance benefits. Figure 1 shows that those top claims are frequently highlighted multiple times on the same product, emphasizing their value. Additionally, all sheens emphasized identical claims, indicating good cross-sheen performance. A benchmarking lab study will be presented here to evaluate those claims.
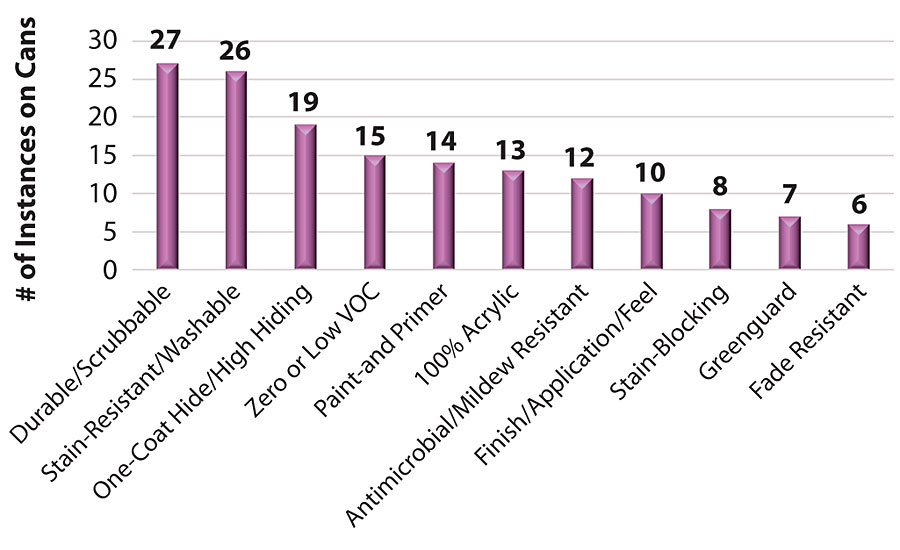
The challenges for polymer developers and paint manufacturers, though, is achieving both improvements in and balance of those claims. The challenge of achieving balanced performance is partly due to the fact that some of these performance attributes commonly oppose one another. Identifying the performance targets to optimize, understanding the test methods to utilize, and delivering innovative solutions are central to successful product development. This article will outline challenges and present both polymer and paint formulation solutions to achieve those goals.
Methods for Evaluating Commercial Paint Label Claims
It is not surprising that such an overwhelming value is put on durability, stain resistance and one-coat hide, as they all relate to practical aspects of a paint’s role to protect and beautify. This section highlights both their significance and the methods used to evaluate those benefits.
Consumers value durability as a primary feature of an interior wall coating, expecting a long-lasting finish that retains its appearance long after it is first painted. To evaluate durability, much of the industry relies on standardized methods like ASTM D2486 to test the resistance of a dried coating to wear and abrasion.
One-coat hide is central to a consumer’s ability to easily change a wall color and is related to rheology, coat weight and TiO 2 dispersion stability. Tint strength is a relative measurement of TiO 2 dispersability and is evaluated using internal test methods, wherein colorant is added to a finished paint, and a drawdown is measured colorimetrically.
Lastly, organizations like Consumer Reports, ASTM and MPI all have established test methods to evaluate stain resistance, also referred to as washability or cleansability. Each method consists of four aspects: type of stains evaluated, stain residence time, washing media and method for evaluating stain resistance. All focus on resistance to both hydrophilic and hydrophobic stains, with stain residence times ranging from 10 min to 24 hrs. Washing media also varies greatly, from the use of standard or commercial abrasive or non-abrasive cleaners. Several methods are employed to evaluate stain resistance, ranging from quantitative to qualitative techniques. Color difference (ΔE) relates light/dark, red/green and yellow/blue for the stained versus unstained areas, while subjective measurements using a numerical scale can also be employed. Alternatively, customer-specific methods can be utilized where evaluation of household stains is common.
In summary, one can see that utilizing representative test methods to evaluate paint performance is a challenge due to the variety of procedures. Because of the value placed on durability, stain resistance and one-coat hide, adopting the appropriate test method represents a challenge to improving coating performance.
Experimental Methods for Benchmarking and Polymer Development
Scrub Resistance Method
Relative scrub resistance was evaluated by applying a 7-mils-thick wet paint film onto a black Leneta chart next to a scrub control, drying for 7 days at 25 C/50% relative humidity (RH), then scrubbing on a Gardner Wear Abrasion machine using Leneta SC-2 scrub media. The scrub cycles to failure was recorded and the mean of three values from the same chart were compared, results being reported as a percentage of the control.
Washability Test Methods
A multi-stain method assessed the removal of hydrophilic stains (hot coffee and Carlo Rossi Burgundy California Table wine) and hydrophobic stains (#2 pencil, blue crayon, Bic ink pen, and Covergirl Hot Chaleur 305 red lipstick) from commercial flat and semigloss paints. A 7-mils-thick wet drawdown was prepared on a black Leneta chart and dried for three days. Stains were applied and sat on the paint film for 2 hrs, then washed for 100 cycles using nonabrasive Leneta SC-1 cleanser. After drying, stain resistance was assessed by measuring the ΔE values against the unstained portion using a BYK Gardner spectrophotometer. This method is represented by Figure 2. In the benchmarking study, a 1-10 rating was used, where 10 represents complete removal of the stain and 1 represented no stain removal.
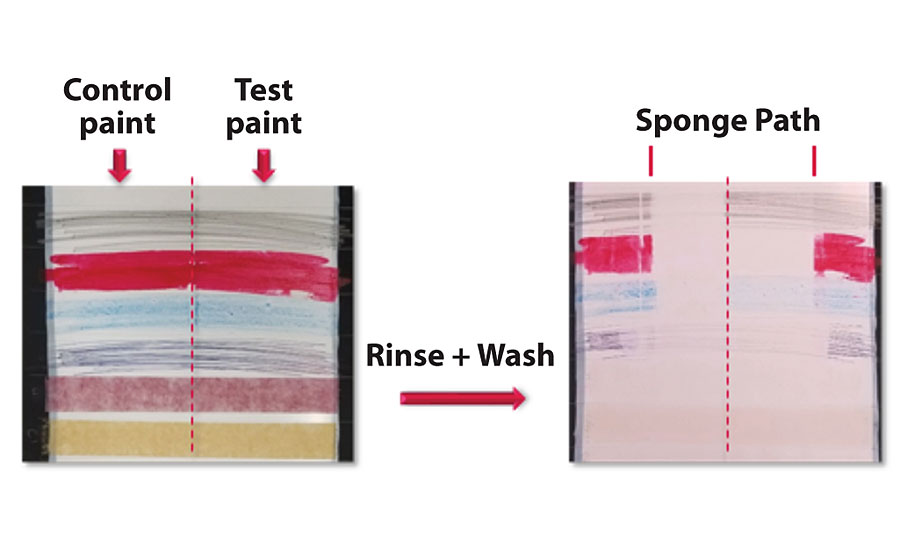
Tint Strength Method
Tint strength was evaluated by adding a control amount of black colorant to a FlakTek cup, followed by a control amount of paint, which was then mixed via a speed mixer for 30 sec. A 3-mils-thick wet drawdown was applied to an opacity chart and allowed to air-dry at 25 C/50% RH overnight. Four %Y reflectance measurements were made for the sealed areas of the paint film, and the Kubelka-Munk (KM) value was calculated for each. Tint strength for each paint was reported as a percentage of the KM value for the control paint.
Commercial Product Label Claims and Benchmark Testing to Identify Performance Gaps
This section outlines the benchmarking of eight paints from the above section to better understand the actual balance in performance and gaps in durability and stain resistance. Tint strength was not evaluated due to the varying amounts of TiO 2 utilized in commercial paints.
Figure 3 shows the stain resistance results for the flat and semigloss paints. In these charts, paints with all stains removed receive a rating of 10, thus with six total stains, the highest rating for a paint was 60.
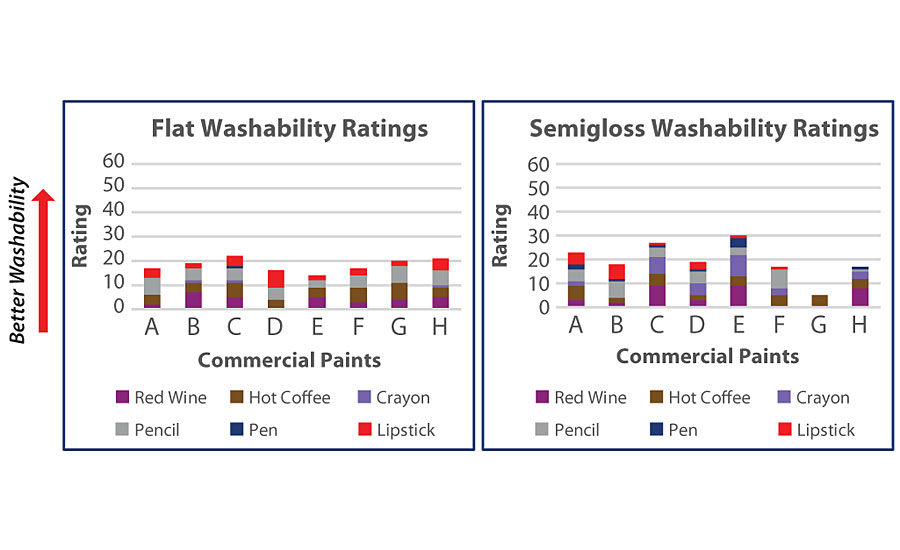
One item of note is that while most paints claim excellent stain resistance, all were rated at less than 50% of the maximum and most achieved less than 20 out of 60. Additionally, as flats are formulated to a higher pigment volume concentration (PVC), the pigment and extender type and level can impact stain interactions. Lastly, some stains are particularly challenging, such as pen and wine in both sheens, and lipstick in semigloss paints.
Figure 4 outlines scrub resistance results, with the red lines delineating 1,000 scrub cycles, which is commonly acceptable for interior paints. As Fig 4 demonstrates, though, only half matched or exceeded 1,000 cycles. Semigloss paints, on the other hand, offer greater durability. This is not surprising, since the higher level of resin in a semigloss formulation results in greater particle-particle interaction and interdiffusion, thus improving film formation and coating durability.
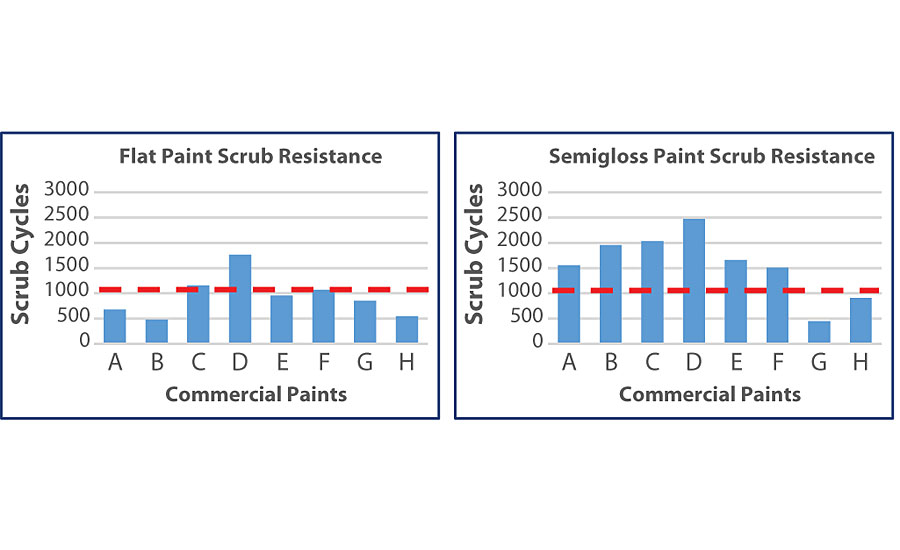
In summary, stain resistance and durability were evaluated in the benchmarking of eight top-tier interior paint lines. Based on product label claims, the expectation was that those paints would perform exceptionally well for washability and scrub resistance; however, lab testing indicated deficiencies in scrub resistance of flat paints, and washability was variable across both sheens.
Our Approach to Balanced Multi-Sheen Performance
The remainder of this article outlines development of a resin that provides a balance of washability, scrub resistance and tint strength in interior coatings. These attributes are optimized through the careful selection of bulk monomer, functional monomer type and level, as well as process conditions and surfactant selection. Additionally, the role of the various components of a waterborne paint formulation on stain resistance is presented. It should be emphasized that there are a vast number of tools in the product developer’s toolbox, but the proper use of those tools is critical for achieving balanced performance.
Proper Selection of Bulk Polymer Composition to Drive Scrub and Stain Resistance
The proper selection of bulk monomers in an emulsion polymer is related to many aspects of coatings performance, including the glass transition temperature (Tg), MFFT and hydrophobicity. Outlined here is how the proper selection of bulk monomer had an unexpected impact on coating performance. More specifically, we observed an unexpected improvement in both scrub resistance and washability with an alternative bulk monomer. This is noteworthy because those two attributes commonly contradict one another.
As demonstrated in Fig 3, red lipstick is a challenging stain, one that is composed of highly colored phenolic pigment in a hydrophobic media. Figure 5 outlines the lipstick washability when the bulk monomer composition was modified. On the left in each panel is a commercial acrylic resin in a semigloss screening formulation, where the right represents the experimental resins. For a polymer containing only BA and MMA bulk monomers, the lipstick washability has a ΔE of 1.29 (lower is better). By introducing a third comonomer while maintaining the Tg, the ΔE is improved to 0.59.
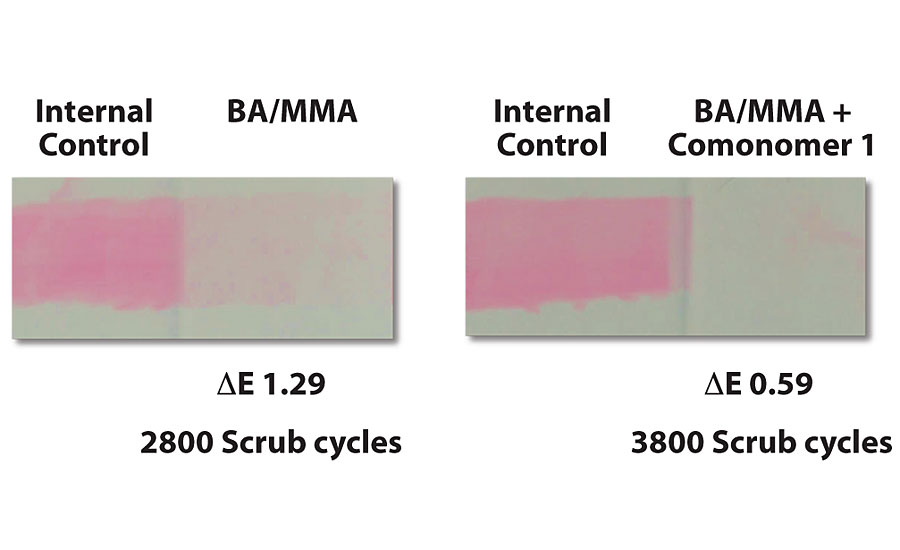
Another benefit of this alternative bulk monomer composition is that the durability of the coating is greatly improved. Shown also in Fig 5, a 36% boost in scrub resistance is observed with this change in bulk monomer composition. This is attractive because the additional scrub cycles permit greater formulation flexibility and helps to support claims of durability.
To conclude, through optimization of the bulk monomer composition, we have identified a powerful lever that is complementary to improving both stain resistance and durability.
Proper Selection of Functional Monomer Type and Level to Drive Durability and Stain Resistance
Functional monomers are used at low levels to impart functionality in a coating or stability in the emulsion polymer. They cover a wide range of functionality and chemistry, from (meth)acrylic acid, phosphorous and sulfur-containing vinyl and (meth)acrylic monomers, hydrolyzable silanes, (meth)acrylamides, ureido (meth)acrylates, and ambient crosslinkers.
This section outlines how the type and level of functional monomer affect durability and stain resistance. In Table 1, a base polymer without functional monomer attains a base level of scrub resistance. However, an almost 50% boost in scrub resistance is achieved with a low level of comonomer 2, while a higher level results in a 130% increase. Utilizing the same high level of a functional monomer with similar chemistry, comonomer 3 results in only a modest improvement in scrub resistance. Additionally, comonomer 2 affords improved washability toward two challenging stains, pen and lipstick (Figure 6).
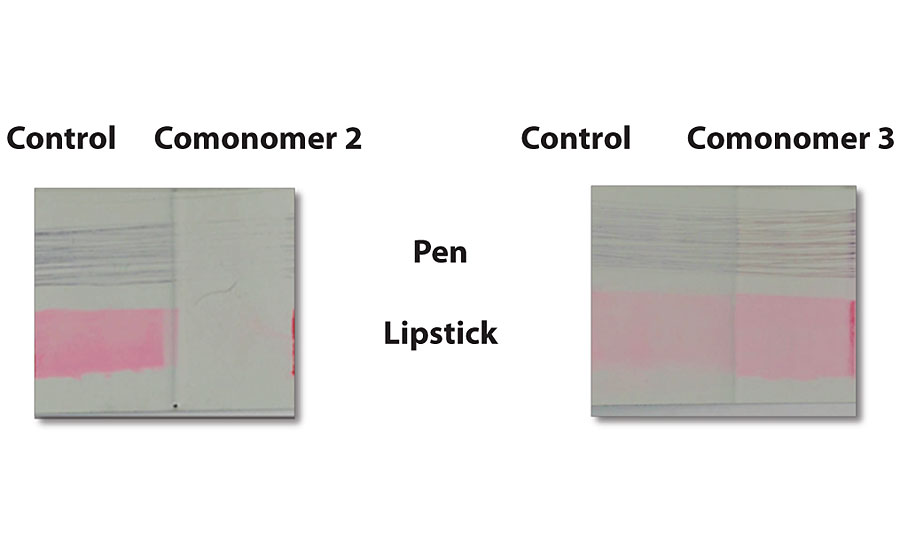
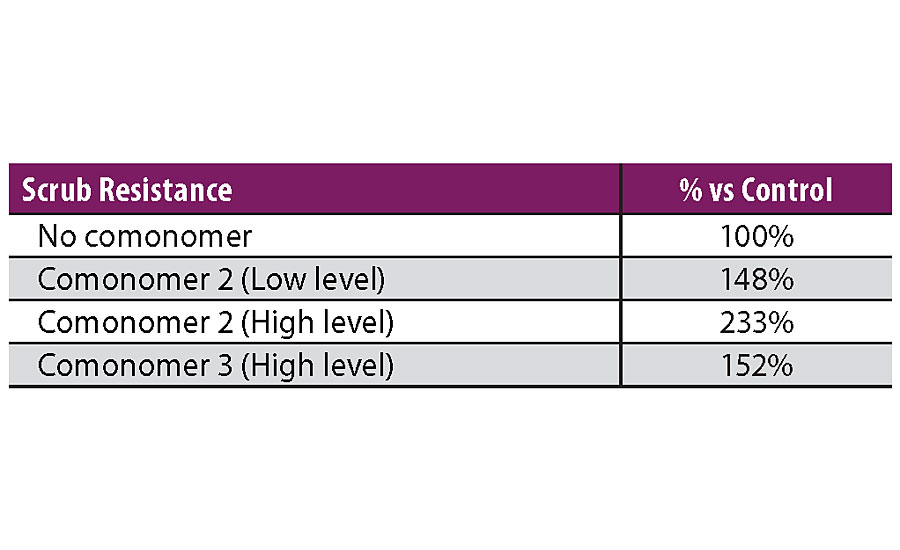
In conclusion, through screening the type and level of functional monomers, we have identified another lever for simultaneously improving both stain resistance and durability.
Balancing Functional Monomer Composition and Process to Improve TiO 2 Efficiency
One-coat hide is a highly valued product label claim related to TiO 2 dispersion stability. Pigment stability is quantified through evaluation of tint strength, as outlined in the experimental section. Though dispersants are incorporated in a formulated paint to facilitate pigment wetting and stabilization, polymer interaction also contributes to this stability, as highlighted in this section.
Table 2 outlines the levers we have identified to improve tint strength. As a benchmark, when comonomer 4 is absent and a control process is implemented, tint strength is at a control level. Through addition of a low level of a functional monomer, a tremendous improvement in tint strength (24%) was noted. Moreover, changing the process while maintaining the same level of comonomer 4 resulted in a negative shift in tint strength. These ranges can be compared to a commercial emulsion polymer from Arkema, which attains a 109% tint strength in the same semigloss formulation.
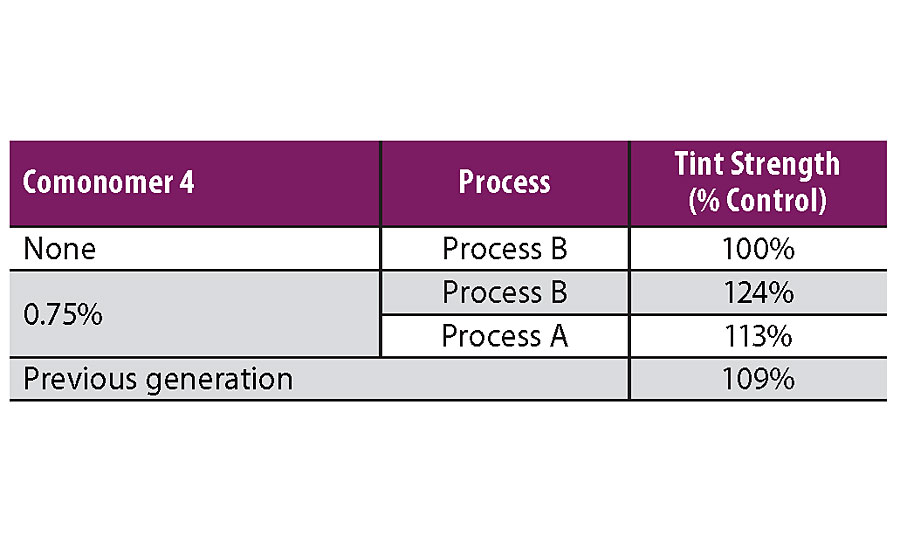
In conclusion, we have identified a functional monomer that can be used to improve TiO 2 dispersing efficiency when process conditions are additionally optimized. This represents another lever to facilitate improved paint performance.
The Role of Latex Surfactant on Colloidal Stability and Washability
While bulk and functional monomers play a primary role in emulsion polymer performance, the polymerization surfactants are also responsible for performance, aside from their primary role as stabilizers. This section highlights two cases where surfactant type was evaluated to improve reaction cleanliness, though the resulting change also had an impact on stain resistance.
As highlighted in the benchmarking study, red wine and coffee are challenging household stains. The panel on the left in Figure 7 represents the washability observed when a co-surfactant was used to improve reactor cleanliness. In the bottom half of the panel, stain resistance was excellent, while the cleanliness of the emulsion polymerization was poor. However, the addition of only 0.2% of an anionic surfactant resulted in a much cleaner process. Unfortunately, that low level of anionic surfactant had a negative impact on coffee and wine washability, as shown in the top half of the panel. The ΔE measurements shown in the fig. are using the bottom half as a reference.
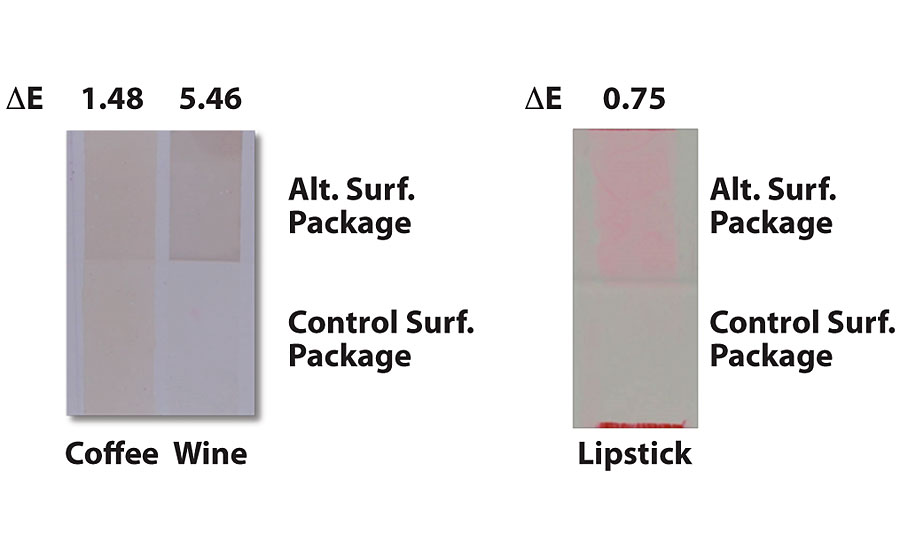
Similarly, the panel on the right side of Fig 7 represents the red lipstick washability when the primary surfactant was changed to improve reactor cleanliness. Here too, the main surfactant used in the control latex system (bottom) was found to result in excellent washability toward lipstick, though the reactor cleanliness was poor. Cleanliness was improved with the use of a different anionic surfactant; however, as shown in the top half of the panel on the right, lipstick washability was poorer, with a ΔE of +0.75.
To conclude, proper selection of the surfactant package is critical for the optimization of both latex stability and performance, where washability can be dramatically affected.
The Role of Paint Formulation Components on Washability
In the product development cycle, a major focus is the impact of the binder on paint performance; however, the components of the paint formulation are equally important. This is due to the wide array of the chemistries and properties available in the pigments and additives in a paint formulation, and their impact on paint performance.
The three washability panels in Figure 8 show the impact that changing paint formulation components can have on coffee and red wine washability. The lower portion of each panel is a coating prepared with a binder in an optimized semigloss formulation. The top portion of each represents a change in the paint formulation, as delineated above the panels. In all three cases, the change negatively affects both the coffee and red wine washability. These three panels demonstrate the importance of identifying both an emulsion polymer composition and paint formulation that highlight the desired performance. As one can imagine, compounding these effects within the same formulation could lead to very poor paint performance.
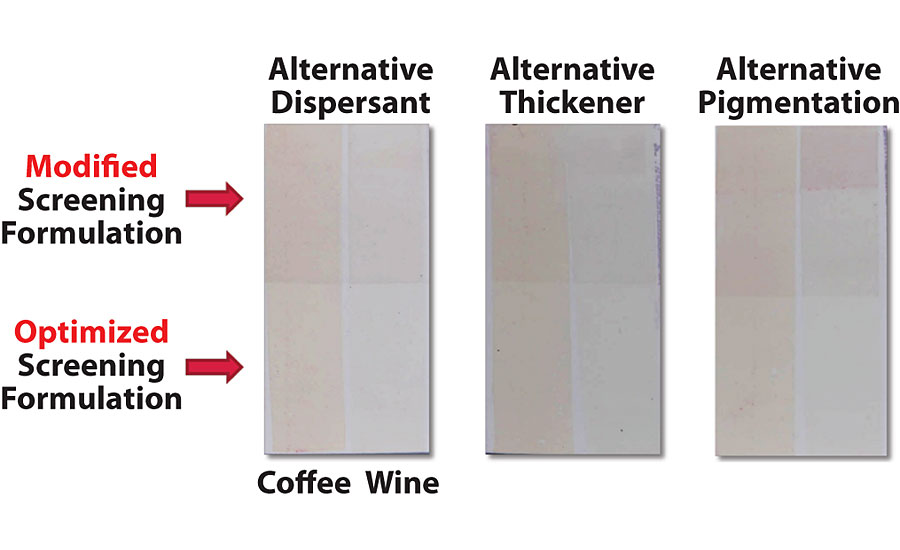
Balanced Multi-Sheen Performance in an Interior Coating
As discussed, the components of an emulsion polymer were optimized to result in excellent durability, stain resistance and tint strength in a semigloss paint formulation. Figure 9 demonstrates how an emulsion polymer comprising the bulk monomer, functional monomer, process conditions and surfactant stabilization packages as discussed above affords excellent performance in both flat and semigloss sheens. Compared to the commercial resin, shown in the bottom portion of each panel, the prototype resin demonstrates improved stain resistance to lipstick, pen, crayon, coffee and red wine. Additionally, the prototype resin demonstrates excellent scrub resistance, with greater than 1,000 scrub cycles in a flat paint and 2,500 scrub cycles in a semigloss paint. Also, tint strength over the current commercial resin was 12-15%, representing significant cost savings at the customer level.
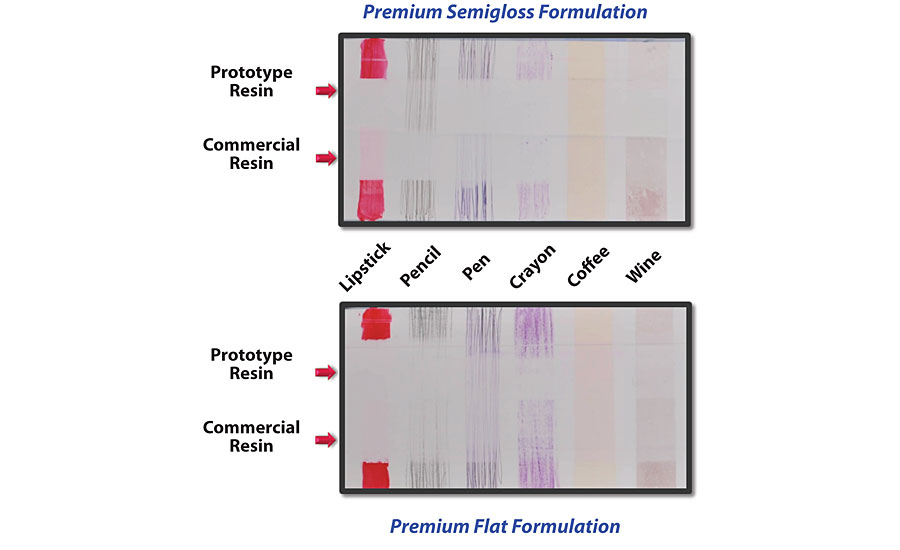
Conclusions
The North American architectural coatings segment is largely dominated by the residential remodel and repaint segment, which is where commercial DIY paints fit. These products are marketed by their product label claims, where durability, stain resistance and one-coat hide are highly valued, as seen through a summary of those claims. It is evident from this work that the actual performance does not correlate completely with the product label claims when testing for washability and scrub resistance.
To design an emulsion polymer with improved and balanced performance in the interior paint segment, Arkema has identified both polymer and formulation drivers to improve the above three performance targets. By optimization of bulk polymer composition, functional monomer type and level, process conditions, and stabilization package, the prototype resin demonstrates an excellent balance of performance. Paint formulation optimization was also shown to have a significant impact on coating performance, wherein dispersant, thickener and pigment selection is critical. Performance balance across multiple sheens can be achieved with this resin, where flat and semigloss paints demonstrate excellent performance.
Reference
1 K. Furst, E. Kriz and S. Shaw, Freedonia Industry Study #3493, Architectural Paint Market in the US, Feb 2017; https://www.freedoniagroup.com/brochure/34xx/3493smwe.pdf, accessed March 18, 2019.
For more information, e-mail jeremy.grove@arkema.com.
Looking for a reprint of this article?
From high-res PDFs to custom plaques, order your copy today!