High Performance and Ultra-Low VOC
Self-Healing Technology Eliminates the Tradeoff

Coatings have long been used to protect critical assets from corrosion. These protective coatings serve to lengthen the service lives of metal assets used in industrial, infrastructure, transportation, machinery, oil and gas, and military applications.1-3 Unfortunately, the use of protective coatings has typically exposed people and the environment to toxic chemicals including solvents, which contribute to increasing levels of volatile organic compounds (VOCs) in the environment. While the most toxic chemicals such as hexavalent chromium have gradually been regulated out of most applications, most protective coatings still incorporate solvents that contribute VOCs into the environment.
Alternatives to solventborne coatings exhibit a number of limitations. Thermal, ultraviolet (UV) radiation and infrared (IR) radiation-cured coatings are limited by the size of the assets these coatings can be used to protect, while ambient-cured systems like waterborne coatings have historically exhibited inferior adhesion, mechanical and anti-corrosion properties.4 As such, the fulfillment of increasing demand for more eco-friendly protective coatings for the protection of large assets necessitates the improvement of waterborne coatings. In this article, we describe the use of self-healing technology to design a waterborne coating formulation with anti-corrosion properties eclipsing solventborne versions, thereby eliminating the trade-off between high-performance and low environmental impact.
Autonomic Materials Inc. (AMI) is a global leader in the development of self-healing functionality for protective coatings. Our technology platform has demonstrated significant improvement in corrosion resistance and maintenance of adhesion after damage in coating systems including silicone coatings, zinc-rich primers and powder coatings.5-7 Damage to coating systems incorporating AMI’s technology initiates a healing response via the rupture of microcapsules embedded within the coatings and subsequent release of the microencapsulated healing agent into the site of damage. Once in the site of damage the healing agent polymerizes, restoring the coating’s protective function.
In the development of AMP-UP™ 100, a low-VOC, self-healing epoxy hybrid primer, we leveraged AMI’s self-healing technology to design a waterborne protective primer with an unprecedented combination of corrosion resistance and eco-friendliness. This waterborne primer exhibits a VOC of less than 50 g/L and self-healing functionality that facilitates excellent corrosion resistance after damage.
In this article we discuss the corrosion performance of AMP-UP 100 on disparate substrates following exposure to ASTM B117 and ASTM D 5894-16 conditions, and benchmark its corrosion performance and VOC relative to a selection of incumbent coating formulations.
Coating Evaluations
To demonstrate the efficacy of the self-healing functionality incorporated into AMP-UP 100 for the corrosion protection of various substrates, we compared its performance relative to a high-performing commercially available waterborne (WB) epoxy primer. In order to assess corrosion performance, three-coat systems including two coats of primer followed by a single coat of a low-VOC acrylic topcoat were applied on cold rolled steel (CRS) panels with SSPC-SP3 surface preparation, blasted steel panels with SSPC-SP10 surface preparation, galvanized steel and aluminum alloy (Al2024-T3) panels. A schematic of the coating system is shown in Figure 1. All the substrates except galvanized steel were cleaned with acetone using a lint-free cloth, and compressed air was applied over the surface to remove any remaining dust particles prior to application of the coating system.
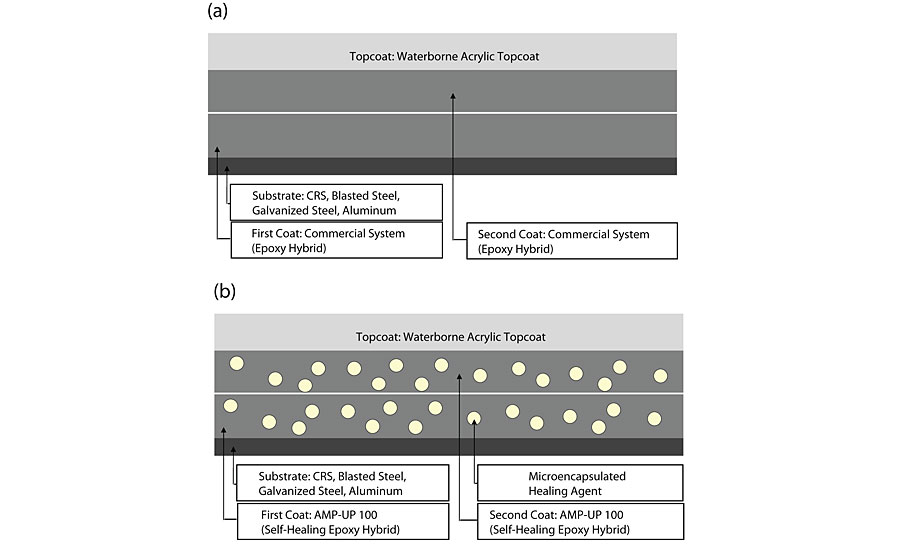
The coatings were applied via a gravity feed conventional spray gun with a 1.8-mm nozzle and 60 psi air pressure. The dry film thicknesses (DFTs) of the primers, build coats and topcoats were measured at 2.5 mils, 2.5 mils and 2 mils respectively. Quick drying properties of AMP-UP 100 (tack-free in less than 1 hr, handle within 2-4 hrs and recoat/topcoat within 1-3 hrs) facilitated completion of the coating system application within a window of 5-8 hrs. The fully coated substrates were allowed to cure at ambient temperature for 7 days prior to testing.
Each panel was scribed using a 156-µm and a 500-µm scribe tool. The panels were allowed to equilibrate at room temperature for 24 hrs. Uncoated areas of the panels (backs and edges) were sealed using a clear polyester sealing tape. The scribed panels were exposed to ASTM B117 salt spray for up to 2,000 hrs. After ASTM B117 exposure, the panels were evaluated for loss of adhesion as outlined in ASTM D1654, Procedure A, Method 2. A rounded spatula held perpendicular to the panel surface and parallel to the scribe was used to remove loosely adhered coating. A sliding caliper was used to measure the loss of adhesion (creep) from six points along the scribe. Three panels were evaluated for each condition and all measurements for each coating system/substrate combination. Representative images of the panels were acquired after 2,000 hrs. The corrosion performance results for abraded CRS, blasted steel, galvanized steel and aluminum alloy Al 2024-T3 panels are summarized in Figures 2-5 respectively.
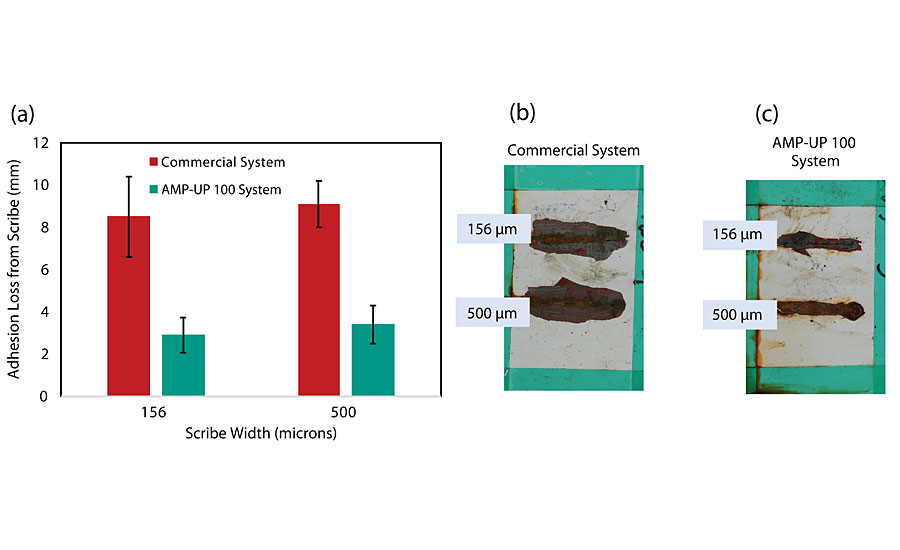
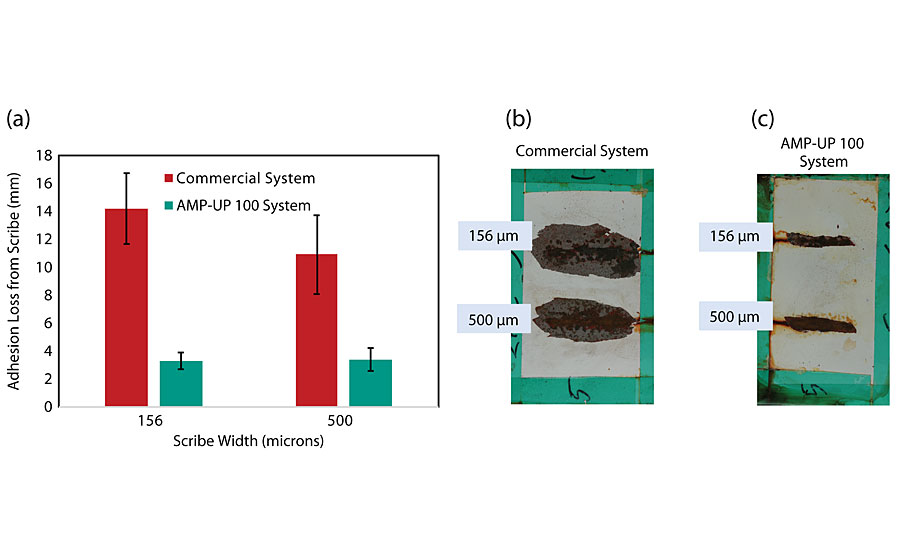
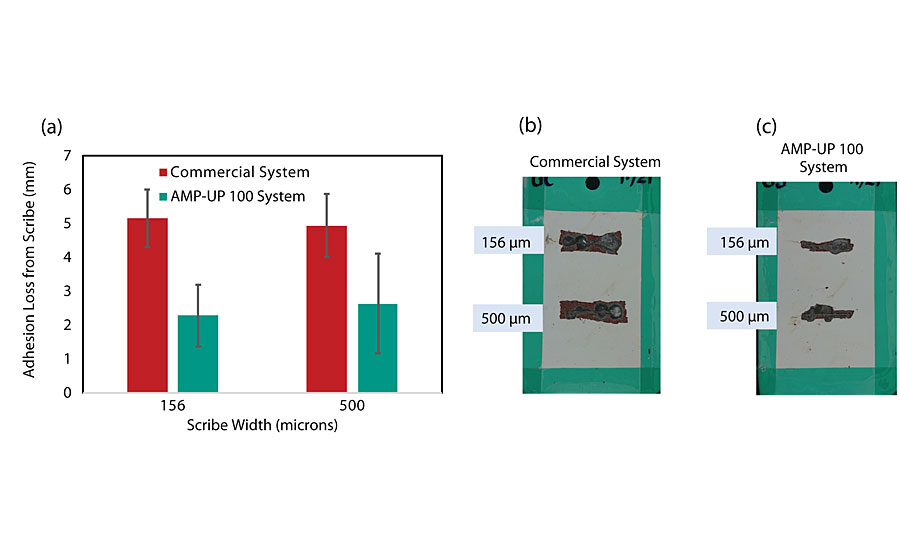
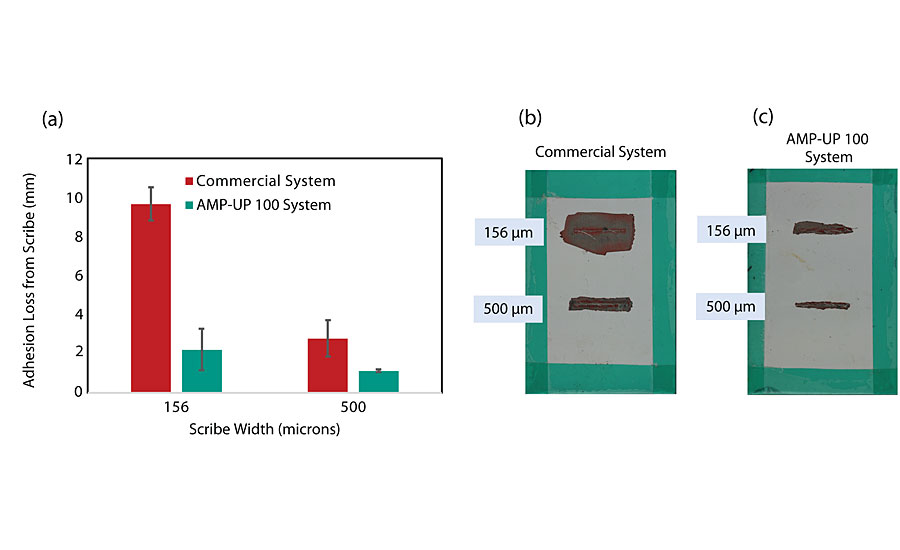
From Figures 2, 3, 4 and 5, it is evident that regardless of the damage size (scribe width), substrate type and preparation, the new protective primer with self-healing functionality exhibits significant improvement in adhesion maintenance and corrosion creep around the scribe. A decrease in adhesion loss from the scribe damage of at least 50% was observed relative to the control coating. The corrosion resistance of the coating system incorporating AMP-UP 100 was further evaluated via cyclic corrosion testing in accordance with ASTM D5894-16. Following curing, coated blasted steel substrates were scribed using a 500-μm scribe tool prior to exposure to ASTM D5894-16 conditions. A decrease in average creep of 46% relative to the control was observed for the new primer, demonstrating consistency in the performance across disparate corrosion tests. A summary of the corrosion testing results including ASTM B117 and ASTM D5894-16 exposures is provided in Table 1.
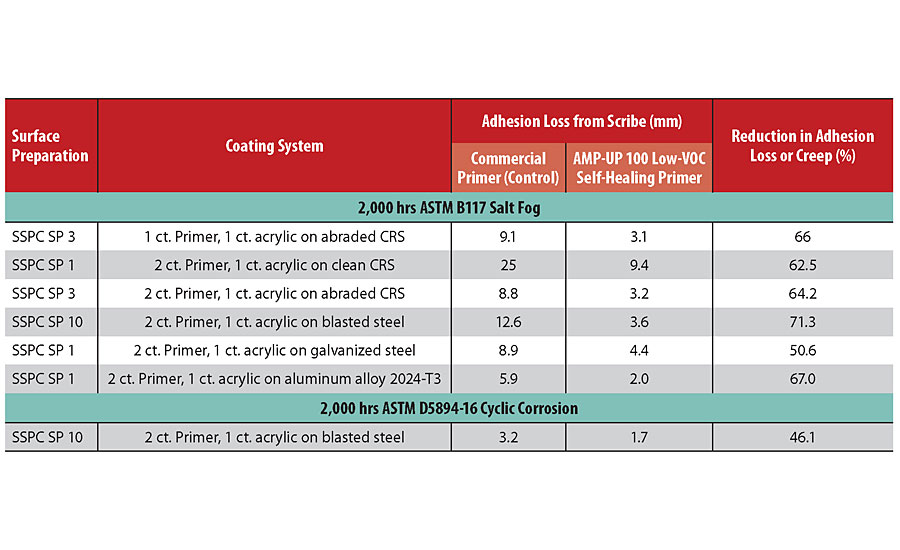
Low VOC Vs. High Performance: No Trade-Off Required
Figure 6 exhibits the ASTM D1654 performance ratings of the AMP-UP 100 system along with disparate commercial systems as a function of their respective VOCs per 100 sq. ft at the recommended DFT. The ASTM D1654 performance ratings of the systems reported in this figure were obtained following 2,000 hrs of ASTM B117 salt spray exposure. As shown in the figure, the new system exhibits the best combination of low VOCs and high performance, eliminating the need for a tradeoff between these two critical properties and thereby providing a viable replacement for solventborne high-performance protective coatings.
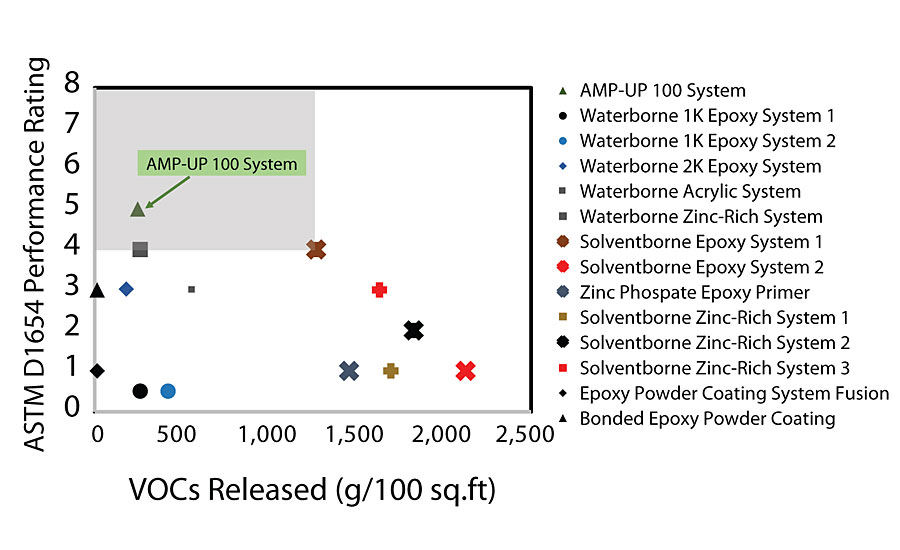
Additional Benefits
Indicating its versatility as a universal primer, we have observed similar efficacy of AMP-UP 100 on other substrates such as concrete and wood. The improvement in substrate protection afforded by this primer comes with a lower environmental impact due to its low VOC component, and since the coating is waterborne, applicators are not exposed to harmful solvents during coating application. Furthermore, the one-component configuration of the formulation improves stoichiometric precision and reliability. The coating is also fast drying, allowing shorter application time for multiple coats and the ability to quickly complete coating projects. Given the corrosion resistance exhibited by the AMP-UP 100 primer, it is a suitable replacement for solventborne epoxies and other direct-to-metal coatings used in a range of light to heavy industrial applications.
Conclusions
Key takeaways of our evaluation of the AMP-UP 100 primer and its performance relative to other waterborne and solventborne coatings include the following:
- A significant reduction in corrosion creep and adhesion loss was achieved via the new waterborne protective primer. The performance improvement is attributed to the self-healing functionality incorporated in the primer, which facilitates the ability of the coating to maintain its adhesion after damage, leading to less moisture ingress and subsequent corrosion creep.
- Regardless of the substrate type, surface preparation, and damage size adhesion and corrosion resistance after damage is significantly improved with the use of AMP-UP 100. Significant improvements were realized on various substrates including CRS, blasted steel, galvanized steel and aluminum in testing up to 2,000 hrs of salt fog exposure.
- Performance evaluation results from cyclic corrosion testing suggests that the new primer exhibits good corrosion resistance in a range of corrosive environments.
- Fast drying, one-component application, superior performance and ultra-low VOC properties all combine to render AMP-UP 100 suitable for a broad set of applications demanding high corrosion performance.
References
1 Schweitzer, P.A. Paint and Coatings, Applications and Corrosion Resistance, Ed.; CRC Press, Taylor and Francis Group, Boca Raton, 2006.
2 Li, W.; Calle, M.L. Review of pH And Electrochemical Responsive Materials for Corrosion Control Applications, Paper Np. 08214, NACE International 2008 Conference and Expo.
3 Montemor, F.M. Functional and Smart Coatings for Corrosion Protection: A Review of Recent Advances, Surface Coatings and Technology, 258, 17-37, November 2014.
4 Challener, C. Heavy-Duty Transportation Segment Driving Towards More Durable and Sustainable Coating Solutions, CoatingsTech, October 2019, 28-34.
5 Navarro, A.G.; Kasisomayajula, S.; Wilson, G.O. Designing Self- Healing Functionality into Silicone-Based Protective Materials, Paint and Coatings Industry, June 2019, 34-38.
6 Kasisomayajula, S.; Dayton, C.R.; Wilson, G.O. The Next Generation of Zinc-Rich Primers: Improved Versatility and Performance via Self-Healing Functionality, Paint and Coatings Industry, March 2019, 50-55.
7 Wilson, G.O.; Ebbert, B.R.; Andersson, H.M. Improved Corrosion Resistance in Powder Coatings via Microencapsulated Self-Healing Agents, Paint and Coatings Industry, March 2017, 49-59.
Looking for a reprint of this article?
From high-res PDFs to custom plaques, order your copy today!