Leveraging Self-Healing Polymer Technology in Coating Design

Since White et al. first reported a demonstration of self-healing functionality in a polymer system1 it has become a growing field of research and technology development with a diverse set of technologies adding new functionality to polymeric materials. This article provides an overview of the classes of technologies that have been developed and their ongoing and/or potential uses in the design of coating systems.
Research on healing in polymeric materials goes back to the late 1970s and early 1980s when Wool and O’Connor extensively studied semicrystalline polymers, amorphous glassy polymers, block co-polymers, elastomers and fiber-reinforced composites at temperatures ranging from 50 ºC below glass transition temperature (Tg) up to 100 ºC. In these studies, healing after damage in the form of a crack in the polymer was facilitated by heating above the glass transition temperature.2-4 Wool later provided a framework describing the stages of healing,5 which when applied to his earlier work suggests heating above Tg provided the energy for (1) molecular rearrangement on opposing crack faces, (2) approach of the crack faces towards each other, (3) wetting, which describes polymer chains on opposing crack faces coming in contact with each other, (4) diffusion through discrete volumes occupied by polymer chains on opposing crack faces, and (5) diffusion to an equilibrium distance and randomization. A schematic of these stages is provided in Figure 1. From the late 1980s into the 1990s, researchers began using solvents to initiate the stages of healing described above by swelling the polymers.5 It became clear that whether through the application of heat or a solvent, mobility within a polymeric material was essential to initiate a healing response.
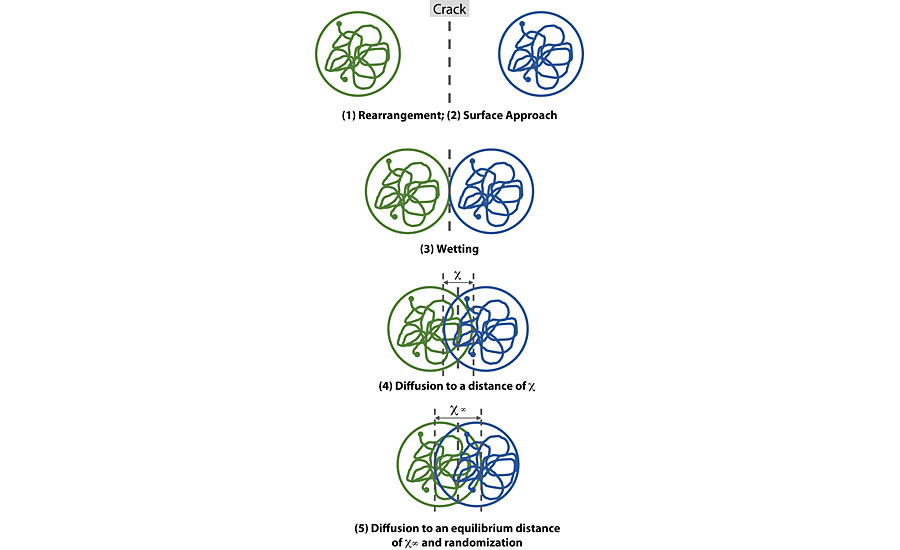
Notably, while the application of heat and solvents provided breakthrough insight into how polymers could be healed, these efforts still required external intervention, and the healing response did not occur autonomically. In other words, the healing did not constitute a self-healing response. The first significant step towards eliminating the need for external intervention in a polymer healing process came from the work of White et al., where dicyclopentadiene (DCPD) was microencapsulated and embedded within an epoxy matrix along with particles of Grubbs catalyst. Damage to the epoxy matrix ruptured the capsules, releasing the DCPD monomer into the site of damage. Once in the site of damage, the monomer reacted with the Grubbs catalyst, initiating a ring opening metathesis polymerization (ROMP) that restored structural continuity to the matrix. Recovery of up to 75% of the original fracture toughness of the matrix was reported.1 The work of White et. al. also led to helpful definitions of the concept of self-healing and characterization of self-healing performance exhibited during quasi-static or dynamic failure modes.6
Extrinsic vs. Intrinsic Functionality Design
Since the demonstration of self-healing functionality in an epoxy matrix using ROMP chemistry, a range of self-healing concepts have been conceived, developed and tested. From a design perspective, these concepts can be classified as extrinsic or intrinsic. In extrinsic design, the self-healing functionality is added to the material as a separate, compartmentalized component within the polymer matrix. The mobility required for healing, described in the stages of healing above, is achieved by the release of a healing agent formulation from a compartment such as a microcapsule,1 or a hollow host material such as a hollow fiber.7
Examples of extrinsic self-healing functionality design include microcapsule-based self-healing technologies that have been designed by researchers at the University of Illinois at Urbana-Champaign,8-11 and those developed by Autonomic Materials, Inc.12,13
For intrinsic design, the self-healing functionality is designed into the material but is not a distinct phase from the bulk material. The mobility required to heal matrices exhibiting intrinsic self-healing functionalities typically stems from a combination of chemical functionality designed into the material and energy supplied to the material system. Healable supramolecular polymers reported by Burnworth et al. are an example of intrinsic healing functionality design in a polymeric material.14 In their work, they described a metallosupramolecular polymer that is mendable by exposure to light. Their design included non-covalent metal-ligand bonds that disengage upon exposure to ultraviolet light, allowing for the mobility within the polymer that initiates the healing process. A summary of the differences between extrinsic and intrinsic healing functionality design is provided in Figure 2.
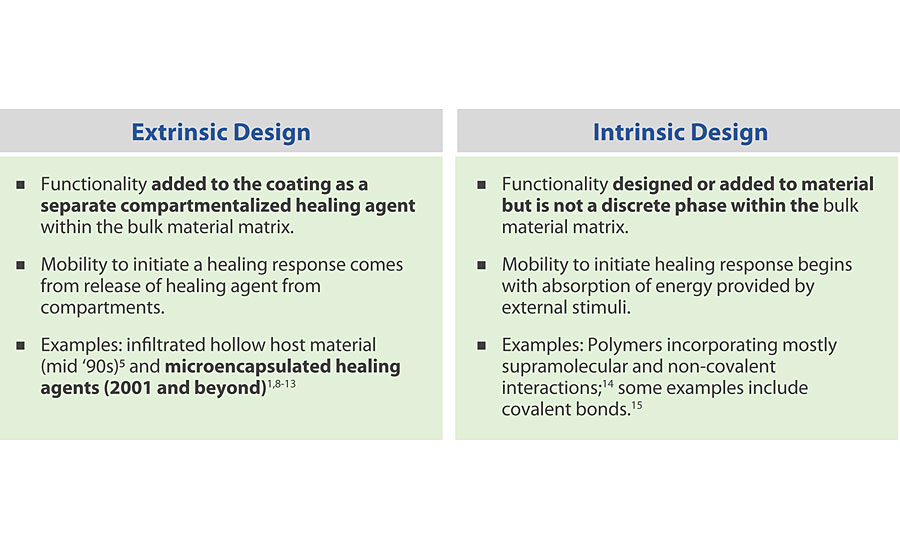
Autonomic vs. Non-Autonomic Healing
Where coating design is concerned, it is perhaps more useful for the classification of approaches to designing healing functionality into polymeric materials to account for the target application. Coatings are generally used for some combination of aesthetic and protective purposes. As such, the choice of the most relevant healing technologies to consider when designing new coating systems should take into consideration whether the coating is to be used for aesthetic or decorative purposes, or primarily for the protection of the substrate. Within this context, the more important characteristic of the healing functionality is not how it is designed but how it functions; and how healing functionalities function can broadly be classified into autonomic and non-autonomic healing.
Autonomic healing in polymeric materials can best be defined as their ability to respond to damage by exhibiting repair without any external intervention. In other words, other than leveraging what is already available in the environment of the material system, no additional energy is required to initiate the mobility necessary for a healing response. Several microcapsule-based healing motifs have demonstrated the autonomic nature of this approach to healing. These include the original ROMP-based healing system reported by White et al. and chemistries based on silanol polycondensation,8 hydrosilylation,9 solvent-induced healing10,11 and isocyanates.16 In all these examples, damage initiated the mobility required for healing by rupturing microcapsules embedded in a matrix, causing the healing agent to be released into the site of damage where it was crosslinked by another reactant also released into the site of damage, present in the matrix or present in the environment. Although they can also be designed to be non-autonomic, extrinsic healing functionalities represent the most likely path to autonomic healing. This approach to designing “self-healing” into materials also represents the highest level of fidelity to its biomimetic inspiration as well as to the moniker itself.
Substrate protection typically requires high-performing binders. This is particularly the case where the protection of metal substrates is concerned. Furthermore, protective coatings are used on large metal assets that are not always accessible such as wind turbines, offshore oil and gas platforms, ballast tanks, etc. These applications are more likely to benefit from autonomic healing functionality incorporated into familiar and well-tested resin systems, thus maintaining tried and true properties while exhibiting value-added self-healing response to damage.
Non-autonomic healing in polymeric materials is characterized by the need for additional external stimuli beyond what is readily available in the environment of the material system. Examples include the metallosupramolecular polymers reported by Burnworth et al., discussed earlier. Non-autonomic healing functionalities are better suited to decorative applications such as the coatings on devices and consumer goods, which by virtue of their size and the way they are used, make the identification of damage and, therefore, the application of external stimuli required to initiate a healing response more practical. A sample segmentation of autonomic and non-autonomic healing technologies by protective or aesthetic application is provided in Figure 3.
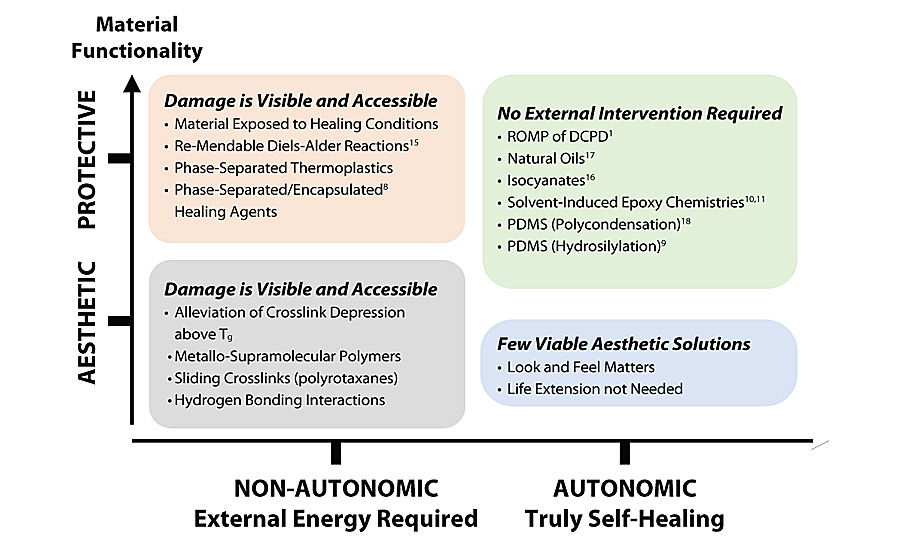
Application to the Design of Protective Coatings
The value proposition offered by self-healing technology resides in the ability to maintain the function provided by a coating, whether decorative or protective, after it is damaged. As such, the utility of these technologies is maximized when they are autonomic and do not require external stimuli, as regardless of the application, no additional effort or energy would be necessary to identify the damage and stimulate the healing response. However, the applications that stand to benefit the most are those operated in remote locations and for which labor associated with maintenance and downtime are costly. These applications include oil and gas, infrastructure and general industrial applications where coatings protect structural metals from corrosion (Figure 4). In these applications, self-healing functionality that arrests damage prevents undercutting at the coating/substrate interface, maintains coating adhesion to the substrate, thereby protecting the substrate after damage. The ability to maintain the protection of an asset following damage to the coating keeps the asset in service for a longer period of time, extending maintenance cycles and minimizing costly downtime.
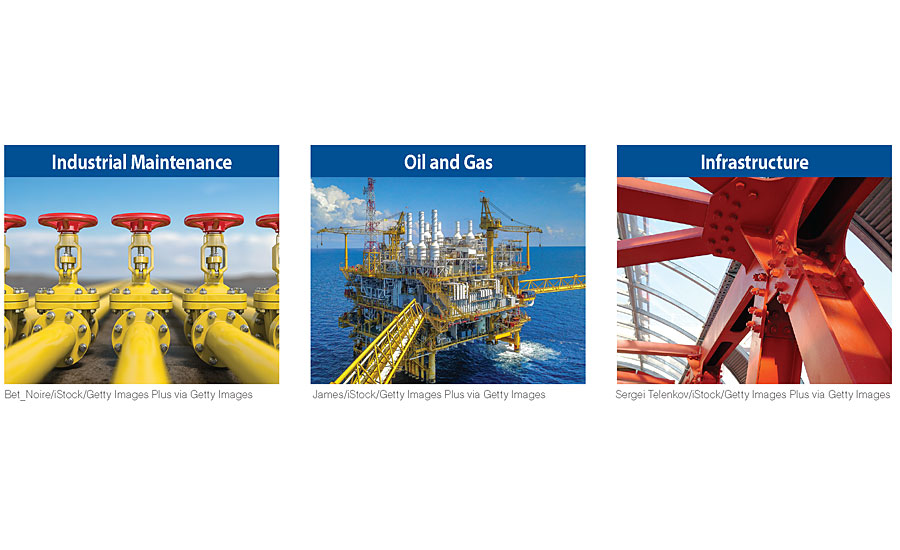
Targeting these applications, Autonomic Materials, Inc. has developed a number of self-healing technologies for protective coatings. Examples include microencapsulated healing agents for use in zinc-rich primers,12 powder coatings19 and waterborne epoxy coatings.20 A team including Chevron, Rust-Oleum and Autonomic Materials has also demonstrated a self-healing solventborne epoxy primer for offshore applications.21 These technologies can also be used in adhesives and sealants that require both joining and substrate protection capabilities.
Application to the Design of Decorative Coatings
Commercial applications of self-healing for decorative coatings have mainly utilized non-autonomic healing functionalities. This is partly because there are currently no technologies that combine Class-A surface aesthetics with autonomic healing functionality, as microcapsule-based technologies that facilitate autonomic healing will generally cause some decrease in the gloss of a coating. Using new non-autonomic healing chemistries to design healing functionality into clear coats for automotive and consumer electronic applications (Figure 5), is consistent with the fact that damage on these items can be more easily located, and external stimuli required for initiating a healing response can be more easily applied. Nissan and NEI have both introduced coatings designed to eliminate fine scratches with the application of heat.22,23
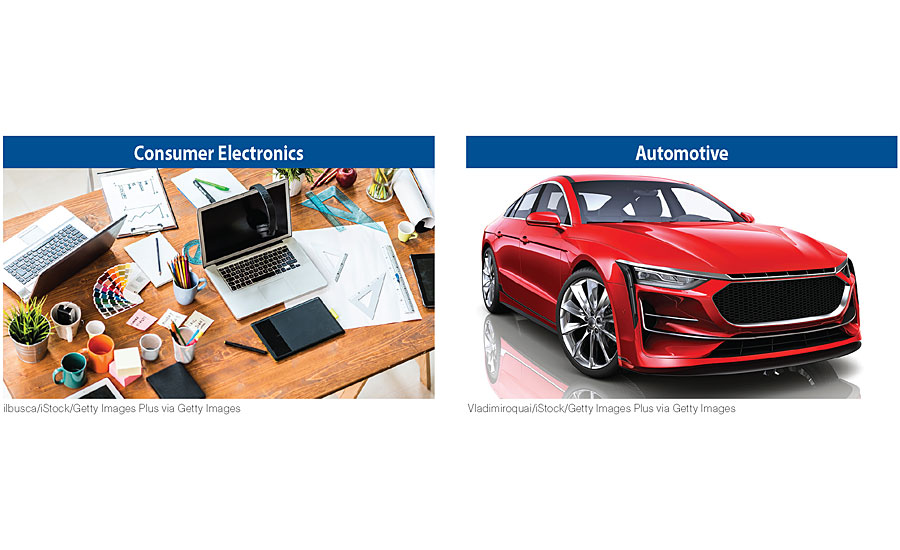
Outlook
From keeping critical assets in service for a longer period of time without disruption, to keeping our electronic devices and vehicles looking good even after damage, the promise offered by self-healing technologies will see interest in them continue to grow. As evidence of this interest, consider that according to a study conducted by n-tech Research, the market for self-healing materials is expected to reach $2.4 billion by 2022.24 As early adopters continue to prove their value in the field, we can expect these technologies to become fixtures in the toolkits of coating formulators.
References
1 White, S.R.; Sottos, N.R.; Geubelle, P.H.; Moore, J.S.; Kessler, M.R.; Sriram, S.R.; Brown, E.N.; Viswanathan, S. Autonomic Healing of Polymer Composites, Nature, 2001, 409, 794-797.
2 Wool, R.P. Material Response and Reversible Cracks in Viscoelastic Polymers, Polymer Engineering and Science, 1978, 18, 1056-1061.
3 Wool, R.P. Crack Healing in Semicrytalline Polymers, Block Copolymers and Filled Elastomers, Polymer Science and Technology, 12A, 341, Lieng-Huong Lee, In Adhesion and Absorption of Polymers, Part A, Plenum Publishers, New York, pp 341-362.
4 Wool, R.P.; O’Connor, K.M. Craze Healing in Polymer Glasses, Polymer Engineering and Science, 1981, 21, 970-977.
5 Wool, R.P. Self-Healing Materials: A Review, Soft Matter, 2008, 4, 400-418.
6 Wilson, G.O.; Andersson, H.M.; White, S.R.; Sottos, N.R.; Moore, J.S.; Braun, P.V. Self-Healing Polymers, Encyclopedia of Polymer Science and Technology, (Ed.). doi:10.1002/0471440264.pst469.
7 Blaiszik, B.J.; Kramer, S.L.B.; Olugebefola, S.C.; Moore, J.S.; Sottos, N.R.; White, S.R. Self-Healing Polymers and Composites, Annual Review of Materials Research, 2010, 40, 179-211.
8 Cho, S.H.; Andersson, H.M.; White, S.R.; Sottos, N.R.; Braun, P.V. Polydimethylsiloxane-Based Self-Healing Materials, Advanced Materials, 2006, 997-1000.
9 Keller, M.K.; White, S.R.; Sottos, N.R. A Self-Healing Poly(dimethylsiloxane) Elastomer, Advanced Functional Materials, 2007, 17, 2399-2404.
10 Caruso, M.M.; Delafuente, D.A.; Ho, V.; Moore, J.S.; Sottos, N.R.; White, S.R. Solvent-Promoted Self-Healing Materials, Macromolecules, 2007, 40, 8830-8832.
11 Caruso, M.M; Blaiszik, B.J.; White, S.R.; Sottos, N.R.; and Moore, J.S. Full Recovery of Fracture Toughness Using a Non-Toxic Solvent-Based Self-Healing System, Advanced Functional Materials, 2008, 18, 1898-1904.
12 Kasisomayajula, S.; Dayton, C.R.D.; Wilson, G.O. The Next Generation of Zinc-Rich Primers: Improved Versatility and Performance via Self-Healing Functionality, Paint and Coatings Industry, March, 2019.
13 Navarro, A.G.; Kasisomayajula, S.; Wilson, G.O. Designing Self-Healing Functionality into Silicone-Based Protective Materials, Paint and Coatings Industry, June, 2019.
14 Burnworth, M.; Tang, L.; Kumpfer, J.R.; Duncan, A.J.; Beyer, F.L.; Flore, G.L.; Rowan, S.J.; Weder, C. Optically Healable Supramolecular Polymers, Nature, 2011, 334-337.
15 Bergman, S.D.; Wudl, F. Mendable Polymers, Journal of Materials Chemistry, 2008, 18, 41-62.
16 Huang, M.; Yang, J. Facile Microencapsulation of HDI for Self-Healing Anticorrosion Coatings, Journal of Materials Chemistry, 2011, 21, 11123-11130.
17 Kumar, A.; Stephenson, L.D.; Murray, J.N Self-Healing Coatings for Steel, Progress in Organic Coatings, 2006, 55, 244 - 253.
18 Cho, S.; White, S.R.; Braun, P.V. Self-Healing Polymer Coatings, Advanced Materials, 2009, 645-649.
19 Wilson, G.O.; Ebbert, B.R.; Andersson, H.M. Improved Corrosion Resistance in Powder Coatings via Microencapsulated Self-Healing Agents, Paints and Coatings Industry, March 2017, 49-59.
20 Shukla, S.; Dayton, C.R,D.; Kasisomayajula, S.; Navarro, A.G.; Wilson, G.O. High Performance and Ultra-Low VOC: Self-Healing Technology Eliminates the Trade-Off, Paint and Coatings Industry, November, 2020.
21 Cibotti, F.; Chaloner-Gill, B.; Badgley, M.; Ferraro, N.; Cervantes, F.; Wilson, G.; Kasisomayajula, S.; Andersson, M.; Al-Borno, A. Incorporation of Self-Healing technology into Protective Coatings as a Maintenance Solution for Offshore Oil and Gas Assets, Paint and Coatings Industry, July 2020.
22 https://techcrunch.com/2012/01/17/nissan-scratch-shield/, Accessed November 8th, 2020.
23 Ou, R.; Eberts, K.; Skandan, G. Phase Separated Self-Healing Polymer Coatings, US Patent 8,987,352 B1.
24 Self-Healing Materials Market to Reach $2.4 billion by 2022.
Looking for a reprint of this article?
From high-res PDFs to custom plaques, order your copy today!