Eco-Friendly Hyperbranched Polyaspartic Polyol and Polyurethane-Urea-Polyurea Hybrid Coatings
for Corrosion Mitigation and Functional Applications

Development of eco-friendly, sustainable and high-solid (low-VOC) coatings have received a lot of attention due to environmental concerns and legislative issues.1,2 Hyperbranched polymers (HBPs) are suitable for low-VOC coating formulations as they exhibit a globular shape, high molecular mass at lower viscosity and high solubility.3,4 HBPs contain a highly branched structure with a large number of reactive functional end groups, which result in their versatility and multi-functional properties. HBPs can be designed based on specific needs and economically bulk synthesized. They can be further modified for useful applications and improve functionality.4-8 Polyurethanes (PUs) are termed as one of the most versatile engineering polymers due to ready availability of raw materials for their synthesis and a wide range of properties offered by them. PUs based on HBPs are suitable for high-solid, multi-functional and high-performance protective coatings.9-11 Vegetable oil-based polyols are widely used in PU formulations for being sustainable, economical, biodegradable and eco-friendly.12-14 Polyureas are formed by rapid reaction of amine and isocyanate, and exhibit a broad range of excellent coating properties with fast drying.15,16
Polyureas have a very short pot life, which either limits their application or can impact cost. To improve pot life without compromising drying time, polyaspartic (PA) polyurea coatings were developed. They were developed from polyaspartic ester polymers that contain hindered secondary aliphatic amine in the backbone, as shown in Figure 1. The structure resembles polyaspartic acid ester as seen in the red encircled part of the figure. Polyurethane-polyurea hybrid coatings exhibit better properties than polyurethane or polyurea alone.17-19
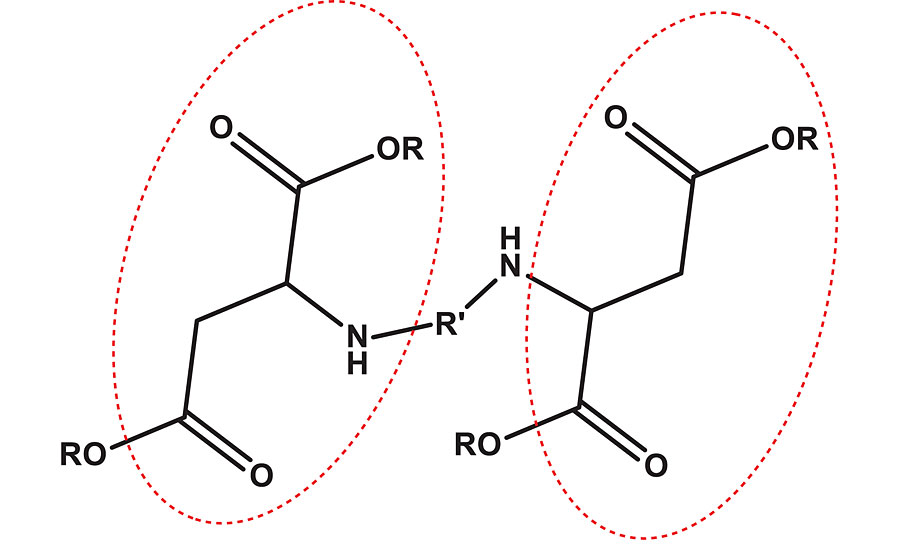
Addition of inhibitors to a coating system improves the corrosion resistance. Polymeric inhibitors have been reported to be excellent for corrosion prevention. Hyperbranched polymers have more advantage due to the presence of multiple atoms and functional groups aiding in inhibition efficiency.20-22
In this work, we have synthesized novel, hyperbranched polyols by melt polycondensation of A3+B3 type monomers. Further modification of HBP with amine was carried out to form PA, which was used to develop a high-solid, moisture-cured PU-urea-polyurea (PUU) coating with H12MDI. The polymers were confirmed by NMR, ESI-mass and FTIR spectra. To make the coating more sustainable and cost efficient, we have developed hybrid polyaspartic ester-soybean PU-urea-polyurea coatings using modified hydroxylated soybean oil (HSO). We have added 10, 20, 30 and 40 percent of HSO with respect to AP to form various hybrid coatings. We have studied thermo-mechanical, gloss, abrasion, rheological, NIR-reflectance and anti-corrosion (mild steel coated) properties of various coatings. Corrosion inhibition ability of PA was carried out in 0.1N HCl solution by weight loss, potentiodynamic polarization and electrochemical impedance spectroscopy (EIS).
Experiment Details
Characterization Techniques
Gel permeation chromatography (GPC) was carried out on a Shimadzu system (RI detector). Calibration was done by polystyrene standards. Rheological behavior was measured on an Anton Par, MCR 103 (U.S.) instrument at room temperature (25 °C). Thermal stability of coating films was observed using a TGA Q500 Universal TA instrument (U.K.). The viscoelastic behavior (DMTA) of coatings was measured by DMA Q800 (TA Instruments, U.S.) at a heating rate of 10 °C min-1. Tensile strength was done with UTM, AGS-10kNG, SHIMADZU system. Abrasion resistance was measured by Taber instrument Model 5131 (USA). H-10 wheels were used for 1,000 cycles with a load of 1 kg on each arm. Gloss measurements were done at 60° incidence on a Rhopoint, Novogloss Glossmeter (England). NIR reflectance was measured on a Varian Cary 5E UV-Vis-NIR spectrophotometer.
An electrochemical study was done on a Potentiostat-Galvanostat (PGSTAT 302N, Autolab, Japan) electrochemical workstation, and results were analyzed by NOVA 1.11.1.9 software. A potentiodynamic polarization study was done in the potential range of -250 to +250 mV versus open circuit potential (OCP), and corrosion rates were determined using Tafel slopes. The mild steel panels were used as working electrode, a saturated calomel electrode as reference electrode and a platinum plate as a counter electrode. A Tafel study of coated mild steel panels and PA inhibition study were done in 3.5% NaCl solution and 0.1N HCl solution respectively. For the inhibitor study, PA test solutions of 25, 50, 100 and 250 ppm were prepared in 0.1N HCl solution. A weight loss study was performed after 24 hrs immersion in 0.1N HCl in the absence and presence of various inhibitor solutions at room temperature (25 °C). An EIS study was done at Eocp in the frequency range of 0.01 Hz to 100 kHz with 10 mV of amplitude. SEM and XRF studies were performed after 12 hrs immersion of mild steel panels in various test solutions. SEM was done on Hitachi-S520, Japan. X-Ray Fluorescence (XRF) was performed on WDXRF, Bruker (Model- S4/Pioneer) instrument.
Methods
Synthesis of Polyaspartic Ester Polymer (PA)
A novel trifunctional novel monomer (A3) was synthesized and used to form HBP by a solvent-less polycondensation reaction with B3 monomer. The reaction mixture (A3+B3) was taken in stoichiometric ratio, and p-TSA (0.2 weight %) was used as catalyst. The reaction was monitored based on acid value as described in our previous publication.9 The atom economy of reaction was very high, and water was formed as the only by-product. Thus, green chemistry principles were followed in synthetic methodology. The HBP was then converted to polyaspartic ester polymer by Michael reaction using an amine. No purification of product was needed, and the formation was confirmed by NMR, FTIR and ESI-mass techniques. The degree of branching of HBP was found to be about 71%, and equivalent weight with respect to (OH, NH) for PA was about 90.
Development of Polyaspartic Polyurethane-Urea-Polyurea (PUU)
PA polymer and SO hybrid-based polyaspartic PU-urea-polyurea prepolymers were formed with H12MDI, as shown in Figure 2. For this, moisture-free PA was dissolved in a mixture of dimethyl formamide and methyl isobutyl ketone, and H12MDI was added dropwise to this mixture (NCO: (OH, NH) = 1.4:1). The reaction was carried out at 80-85 °C and was monitored by isocyanate (NCO) value measurement. After 7 hrs, DBTDL catalyst was added, and the reaction continued for one more hour. A similar process was followed for the PA and SO mixture (10, 20, 30 and 40% SO with respect to PA) based, NCO-terminated prepolymer formation. The coating free films were obtained by casting prepolymers onto a tin foil and then allowing to moisture cure under ambient condition for more than 15 days until the NCO peak disappeared in the FTIR spectra. The prepolymers were also cast on cleaned mild steel panels and moisture cured to carry out the corrosion study.
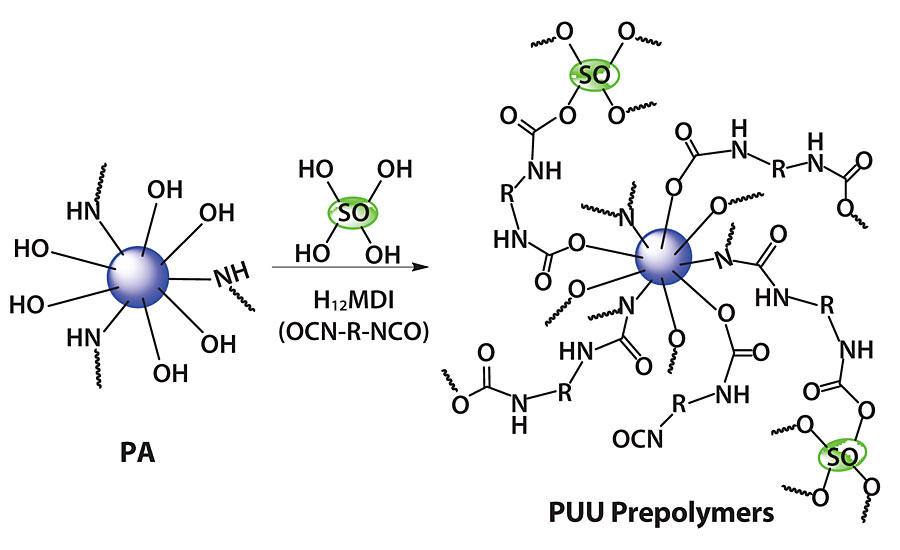
Results and Discussion
GPC and Rheological Behavior of Polyaspartic Ester
Polymer properties largely depend on molecular weight and its distribution, called polydispersity. GPC molecular weight of water-soluble polymers depends on hydrodynamic volume. PA molecular weight (Mn) was obtained to be 13,727 g/mol with a polydispersity index of 1.15. High molecular weight and low polydispersity of a polymer assures good physical properties, which makes it highly suited for coating applications.
HBPs exhibit unique three-dimensional architecture with low chain entanglements. This property leads to lower viscosity of HBPs as compared to linear polymers, thus widening their application potential. Lower viscosity is especially useful for coating applications. We can observe from Figure 3 that viscosity of PA remained constant up to a shear strain of 40 s-1, indicating Newtonian behavior. Beyond this point, viscosity slowly decreased, which indicates shear thinning behavior.
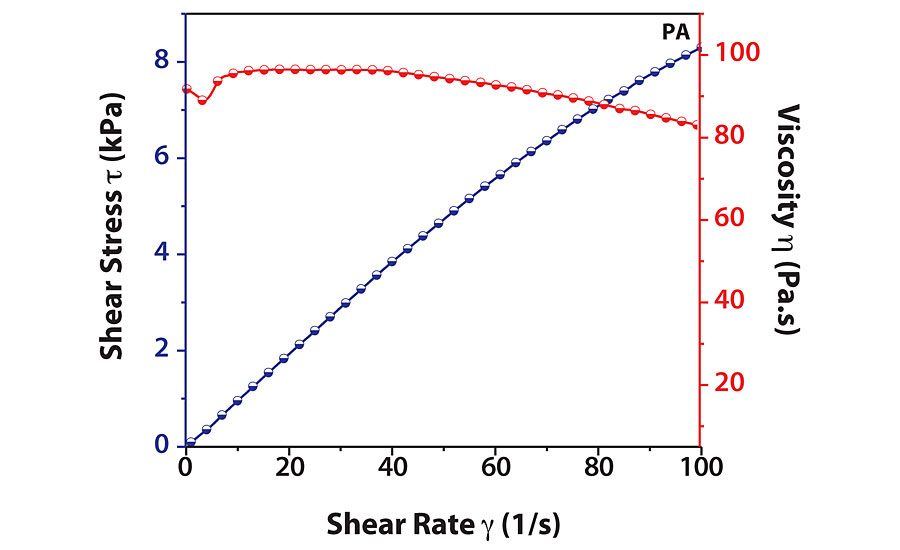
Thermal Behavior
The thermal stability of all PUUs was determined by thermogravimetric (TGA) analysis of PUU coating films. TGA thermograms of PUU, PUU2 and PUU4 are shown in Figure 4, and results are summarized in Table 1. TON is the onset decomposition temperature; TMAX is the temperature at which maximum weight loss has occurred and T50% is the temperature at which 50% weight loss has occurred. The thermogram indicates two major degradation patterns. TON starts after 250 °C and the maximum value was observed for the PA-based coating (PUU), which gradually decreases with increasing HSO content. The first major degradation occurs due to urethane-urea segment with the T1MAX value of PUU being higher than other coatings. The second degradation step at about 450 °C relates to polyester groups. It was observed that thermal stability of the PPU coating remained better than HSO hybrid coatings. Addition of HSO first caused a decrease in thermal stability, which eventually improved with increasing HSO content.
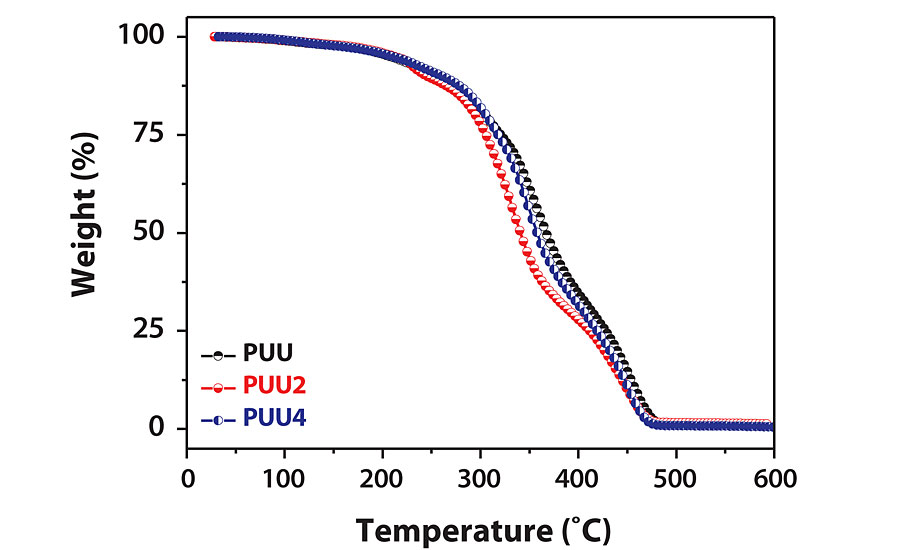
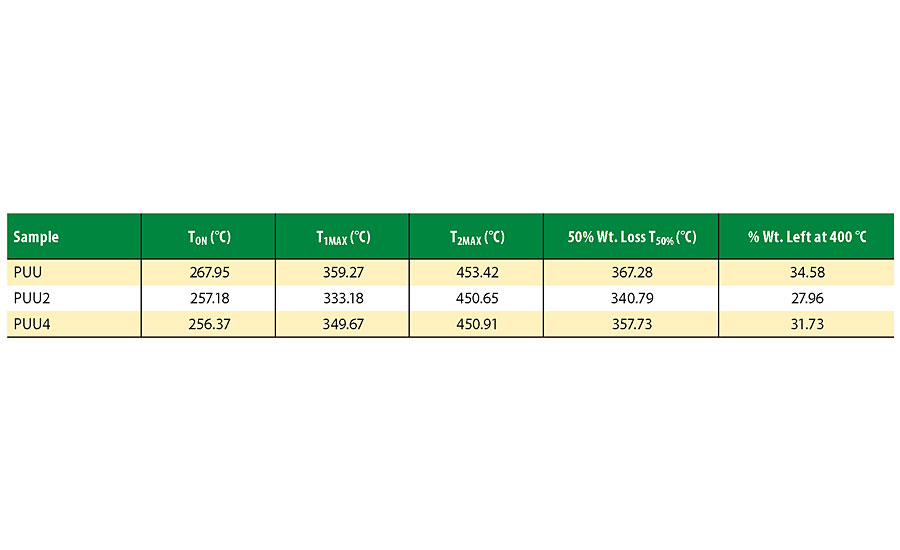
Thermomechanical Properties: DMTA and UTM
Storage modulus (E¢) and loss tangent (tan d) versus temperature curves are depicted in Figure 5, and DMTA study results are summarized in Table 2. UTM measurements of coating films are also given in Table 2. Glass transition temperature (Tg) is the temperature at which tan d curve has a maximum. The viscoelastic behavior of a coating depends on many factors, such as crosslinking, hydrogen bonding, phase size, phase mixing/separation and chain entanglements.9,23 The coatings are highly rigid and stiff at lower temperature in the glassy region as their storage moduli at 50 °C are very high. With an increase in temperature, storage modulus sharply decreases, and after Tg, it slowly moves toward a rubbery plateau region.
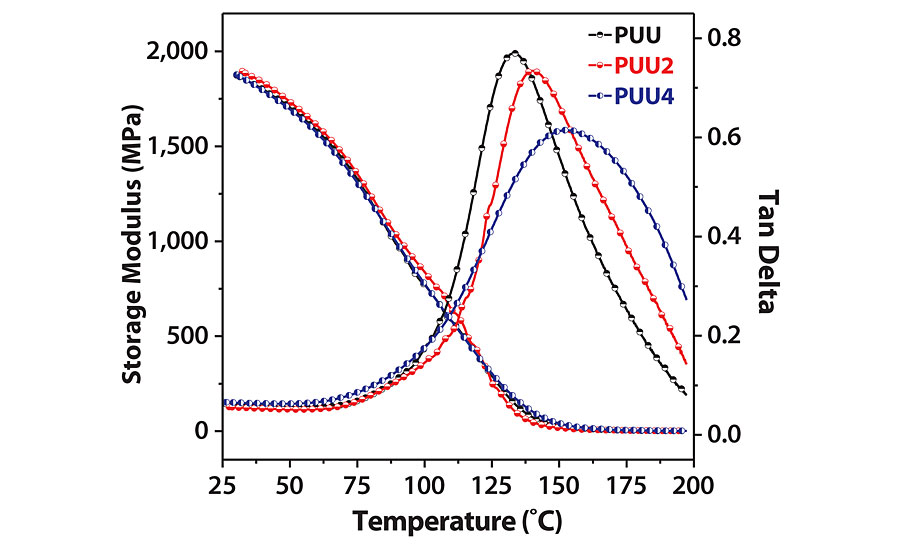
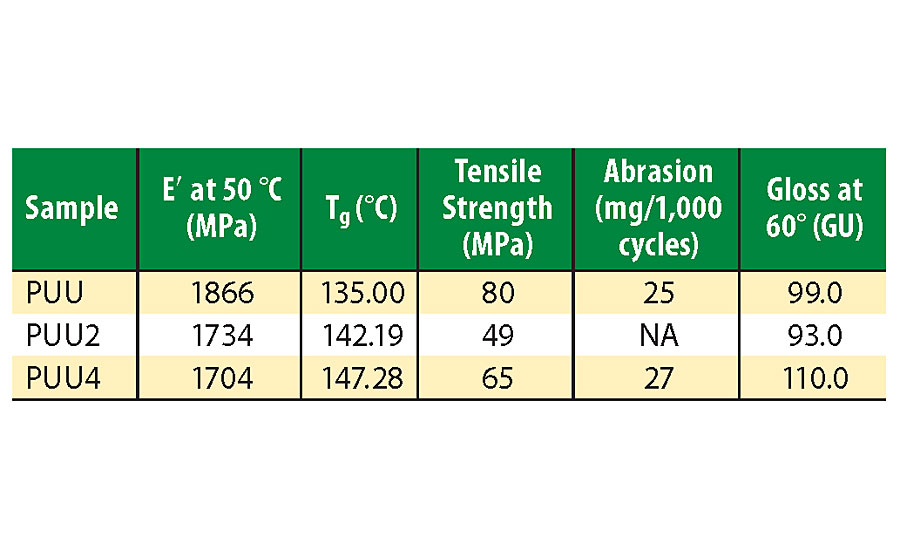
The E¢ value for PUU is higher than their SO hybrid counterparts, PUU2 and PUU4. This might be a result of poor compatibility between PA and soybean oil, or flexibility caused due to long chains of soybean. PUU exhibited excellent tensile strength of 80 MPa and high Tg value (>135 °C), which makes it suitable for high-performance applications. Tensile strength first decreased with SO hybrid, PUU2, and then increased for PUU4, which differs from storage modulus variation. This might be due to the decrease in storage modulus of PUU2 near Tg. Chain entanglement due to SO addition might have resulted in an increase of Tg values for hybrid coatings.24
Abrasion Resistance and Gloss
Abrasion resistance and gloss (60° incidence) results are summarized in Table 2. Abrasion resistance depends on hardness, toughness and surface properties of the material.25 The coatings exhibited excellent abrasion resistance, which is suitable for a wide range of applications. The abrasion value did not change much on addition of SO, indicating that hardness of hybrid coatings does not change upon its addition. The coating films exhibited a glossy nature, which first decreased with the addition of SO but later increased with increasing SO content up to 110 GU for PUU4. This type of variation might be caused by a change in surface morphology of coatings and better homogeneous distribution of hard phases in the polymer matrix.26
Electrochemical Corrosion Evaluation
PU and polyurea coatings are highly efficient against corrosion by providing a barrier protection against corrosive chemicals and solvents.10,27 The anti-corrosive ability of mild steel (MS)-coated panels was evaluated by a potentiodynamic polarization test. The test was performed after dipping the coated panels in 3.5% NaCl solution for 10 days. The test was performed in 3.5% freshly prepared NaCl solution. The resultant Tafel plots are shown in Figure 6, and various corrosion parameters are given in Table 3. The Icorr value for PUU is lowest, which increased for PUU2 and again decreased for PUU4. It indicates that PUU provides better protection than SO hybrids, and with an increase in SO content the corrosion resistance increases. The same result is supported by other test parameters listed in Table 3.
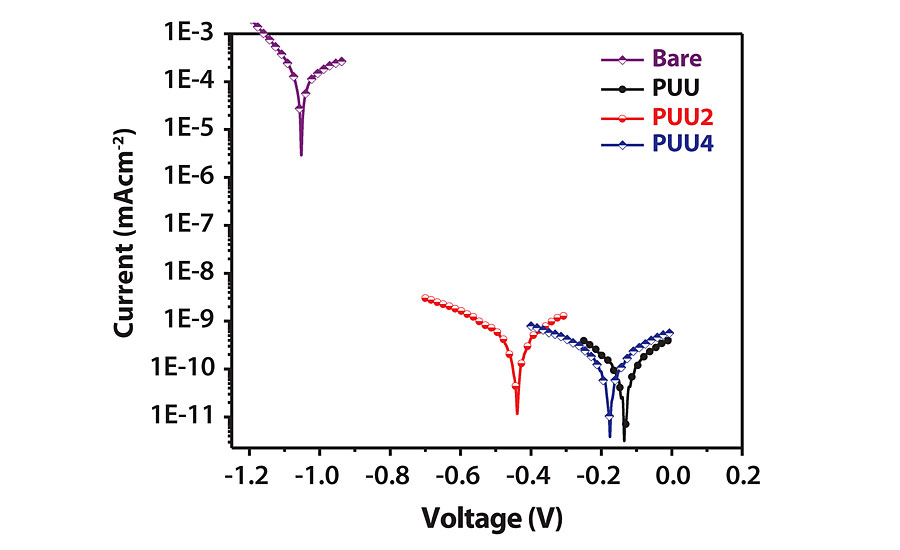
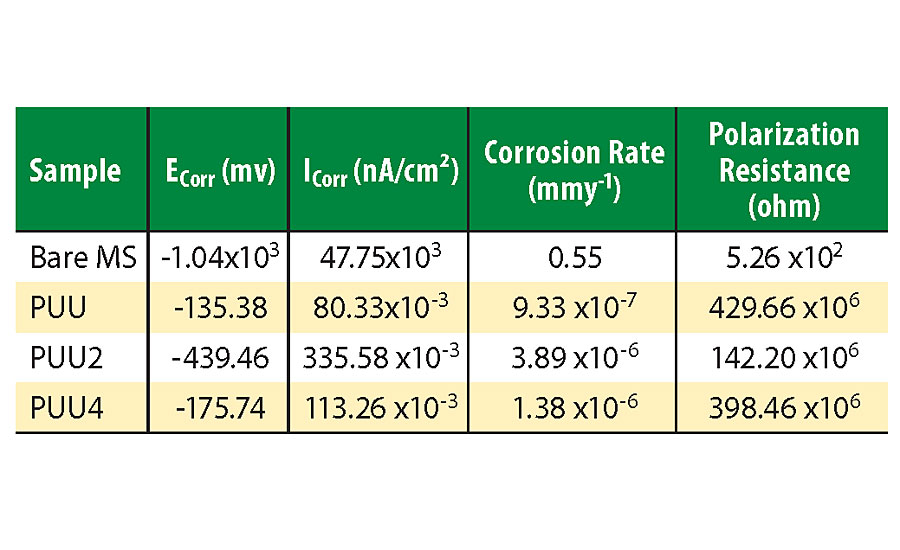
NIR Reflectance
NIR reflectance of PUU was measured in the 750-2,500 nm range using elemental sulfur as standard, and the curve is displayed in Figure 7. A NIR reflectance maximum of about 88% was observed in the spectrum. The reflectance remains more than 80% in the major part of the observed NIR spectrum. So, the coating itself showed impressive NIR reflectance without use of any additive. Thus, coatings can effectively reduce cooling energy burden by acting as a heat shield to save from NIR solar radiation.28
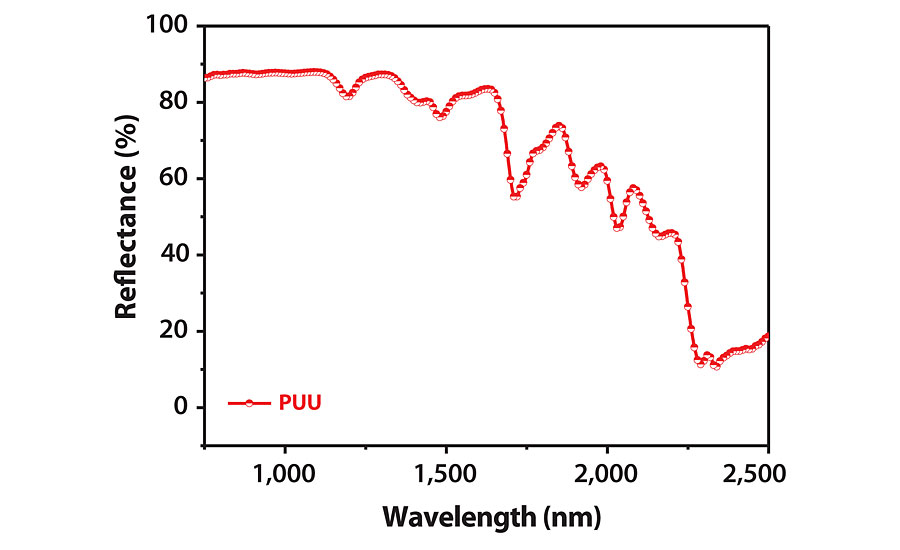
Corrosion Inhibition Study
Experimental Details
Mild steel panels of dimension 2.5x2.5x1 cm3 were used for the inhibitor study by weight loss, potentiodynamic polarization and electrochemical impedance spectroscopy. Panels were cleaned and polished for a smooth and shiny finish before the experiment. The study was carried out in 0.1N HCl and PA polymer dispersions as inhibitors having 100 ppm (PA1) and 250 ppm (PA2) concentration in 0.1N HCl.
Weight Loss Inhibition Measurement
The weight loss inhibitor study was done based on ASTM G31-72 (2004). Steel panels of known weight (gm) were immersed in 100-mL beakers containing 0.1N HCl and other PA dispersions mentioned earlier. Three sets of tests were performed at room temperature for 24 hrs. The panels were cleaned to remove corrosion products, dried and weighed again. The weight loss (gm) and inhibition efficiency (hw) in percentage was determined by the following equation.29
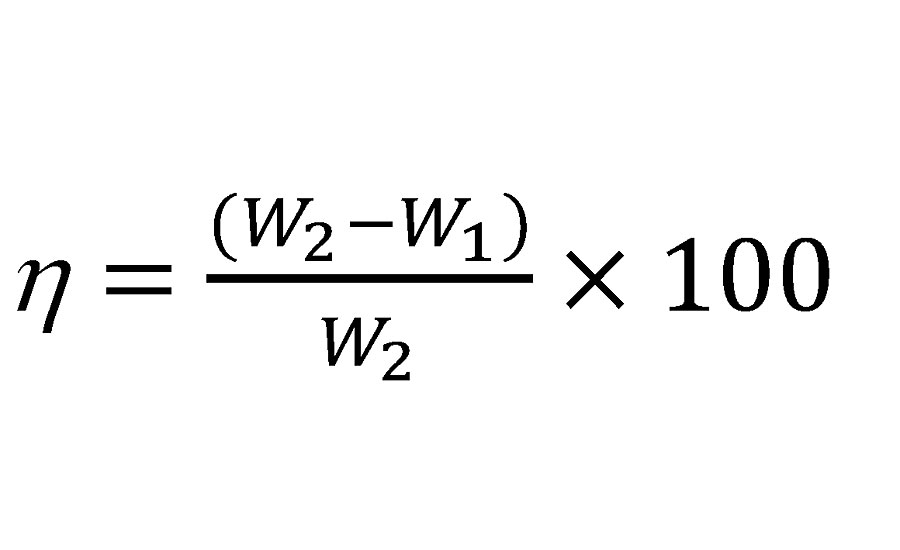
Where, w1 and w2 are the weight loss of mild steel panels in 0.1N HCl solution with and without inhibitor respectively. The results of the inhibition study are given in Table 4. Inhibition efficiency increases with increasing PA concentration due to higher surface coverage. 250 ppm polymer dispersion exhibited excellent efficiency of 97.91%. Excellent inhibition by hyperbranched PA was caused by swift adsorption of polymer on the metal surface through heteroatoms and non-bonded electron pairs.30
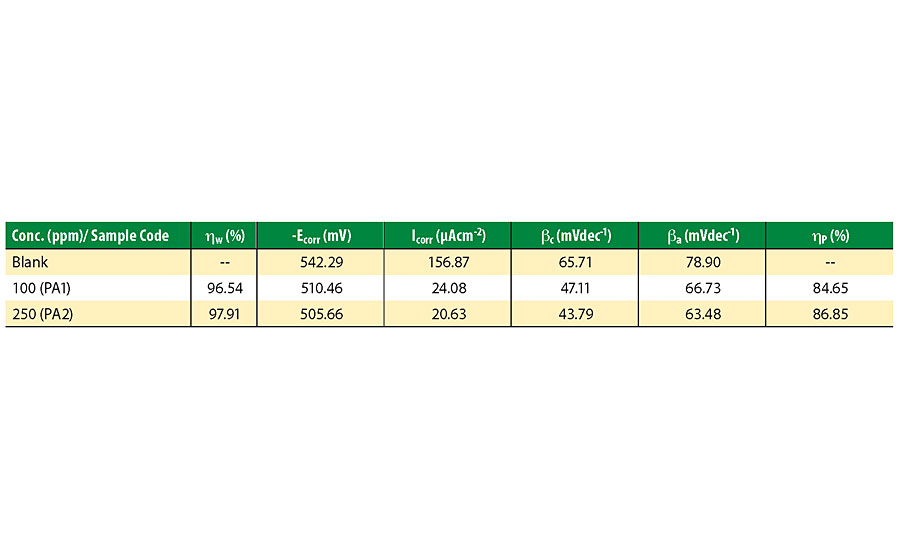
SEM and XRF Study
The SEM images shown in Figure 8 were taken after 12 hrs immersion of mild steel in 0.1N HCl and 100 ppm (PA1) inhibitor concentration. Figure 8a indicates that mild steel has corroded in an uninhibited test solution. The magnified image of the same mild steel in Figure 8b indicates a highly porous corroded surface, confirming the occurrence of severe corrosion. The inhibited mild steel surface in Figure 8c appears smoother and non-corroded. But, the magnified image of the inhibited panel in Figure 8d indicates uniform distribution of adsorbed polymer on the metal surface. So, homogeneous surface coverage of mild steel by polymer leads to excellent inhibition efficiency.
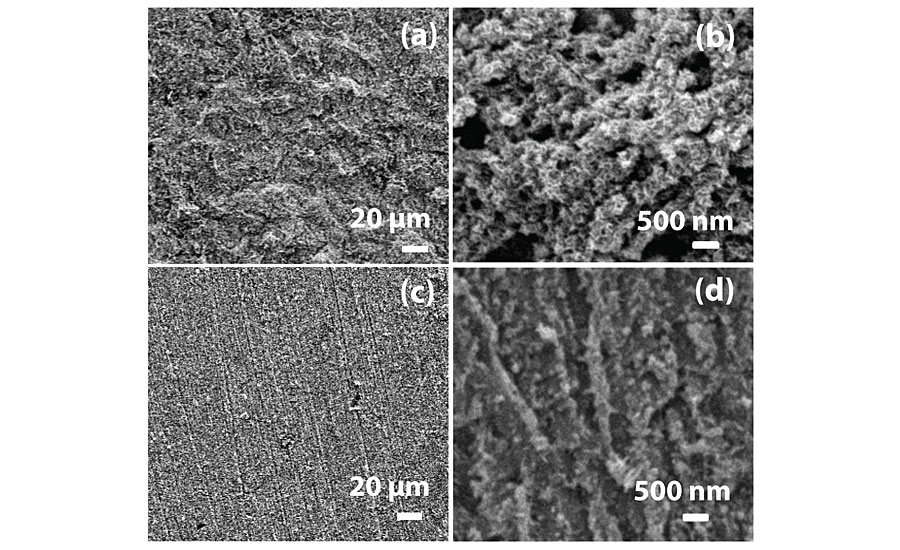
XRF study was carried out for untested mild steel, uninhibited steel and inhibited steel panels to understand formation of corrosion products and its severity. Untested mild steel and inhibited steel panels were completely free of corrosion as there was no trace of chlorine on them. About 0.014% of chlorine was present on the uninhibited panels due to formation of corrosion products.
Potentiodynamic Polarization Measurements
The potentiodynamic polarization study was done on mild steel panels with 0.1N HCl and various inhibitor (PA) concentrations. The results are displayed in Figure 9, and the data is summarized in Table 4. Inhibition efficiency (hp) was calculated using the following equation.31
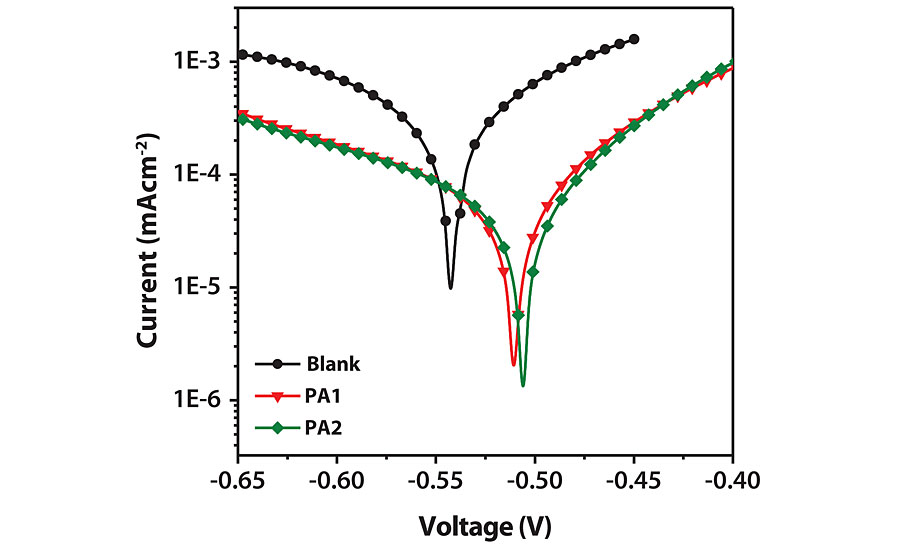
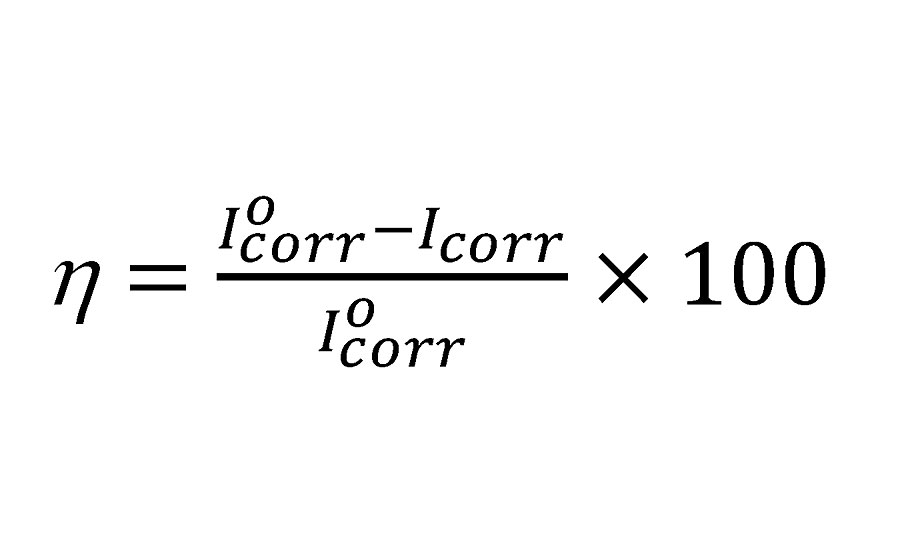
Where Iocorr and Icorr are the corrosion current densities in the absence and presence of inhibitor respectively. A large decrease in Icorr value for inhibited mild steel was observed, indicating excellent corrosion inhibition. The inhibition efficiency of PA1 is 84.65%, which increases with an increase in concentration. The shape of the Tafel curves remains similar, indicating that the mechanism of corrosion is the same for inhibited and uninhibited panels. There is not much difference between Ecorr values of the uninhibited and inhibited samples. This indicates that PA behaves as mixed type inhibitors, and hence both anodic and cathodic reactions are inhibited by surface coverage of metal.31,32
Electrochemical Impedance Spectroscopy
The Nyquist and Bode modulus plots for mild steel corrosion are shown in Figures 10a and b. Semi-circular capacitive type Nyquist loops indicate that inhibitor forms an interface between mild steel surface and HCl solution. The loops are slightly depressed due to the roughness and inhomogeneity of mild steel surface.31 The loop diameter increases with increasing inhibitor concentration, indicating improved surface coverage. The shape of all loops remains similar, indicating that corrosion mechanism does not change by inhibitors.33 Impedance parameters were obtained by curve fitting to get an equivalent circuit, as shown in Figure 11. The circuit consists of solution resistance (RS), polarization resistance (Rp) and constant phase element (CPE) as defined in the work done by F. Zhang et al.31 Inhibition efficiency (hI) was calculated by the following equation.31
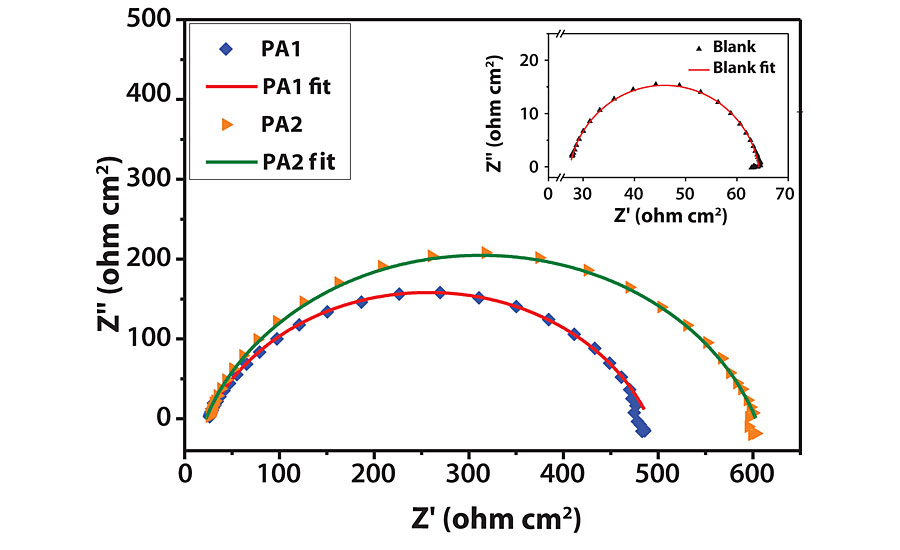
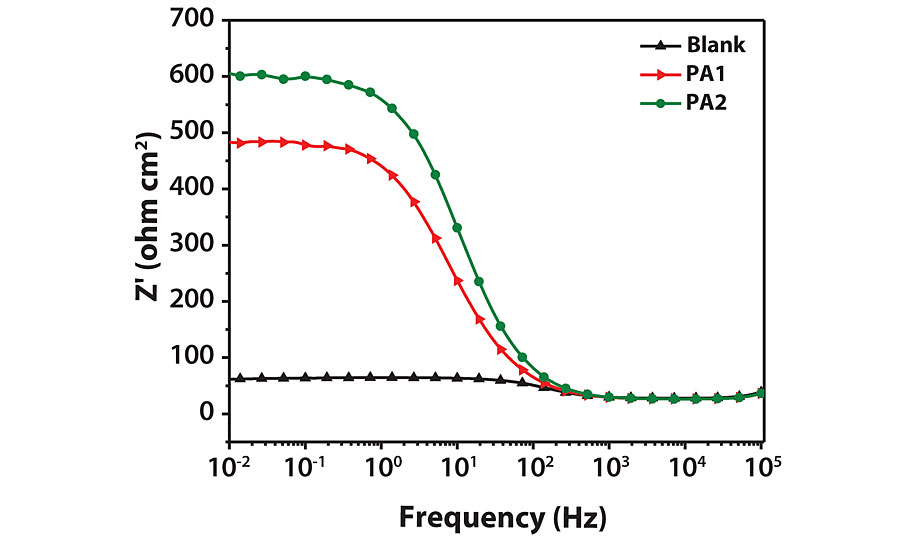

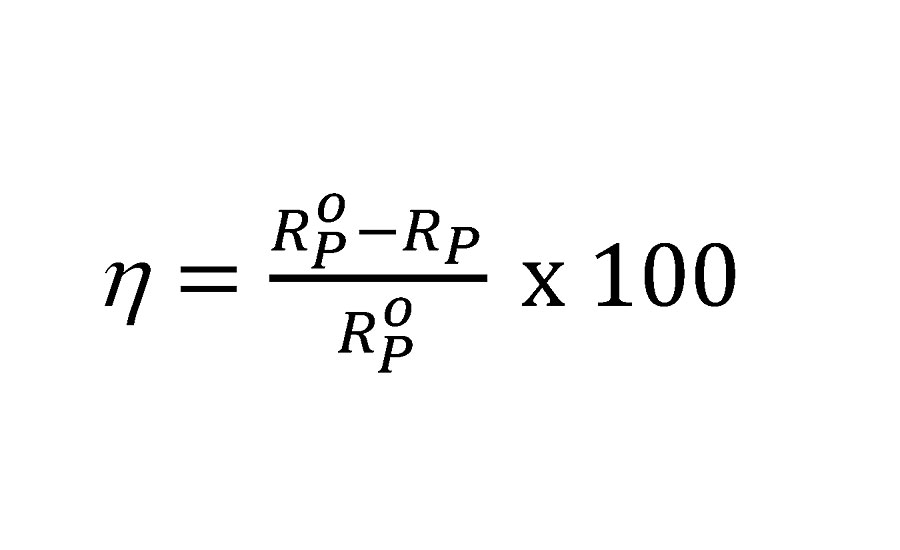
Where Rop and Rp are polarization resistance in the absence and presence of inhibitor respectively. The results are given in Table 5.
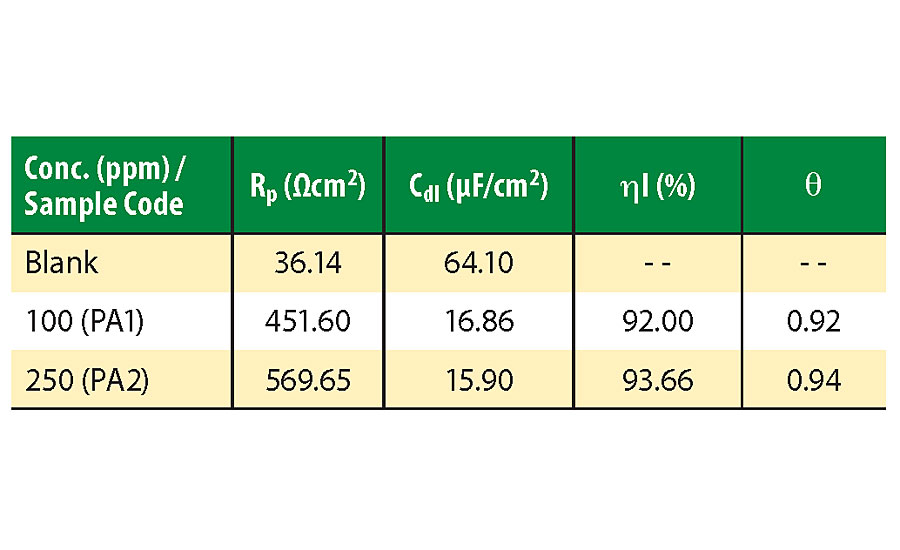
Corrosion resistance and inhibition efficiency increases with increasing RP and decreasing double layer capacitance (Cdl) values. Inhibition efficiency for PA1 is 92%, which increases with increasing concentration of inhibitor to 93.66% for PA2. Cdl decreases due to a decrease in dielectric constant caused by adsorption of inhibitor by displacement of water molecules from the metal surface. With an increase in inhibitor concentration, thickness of the electrical double layer increases, which causes decrease in Cdl value.34
Conclusions
A novel hyperbranched polyaspartic ester polyol with a high degree of branching was synthesized in an eco-friendly manner by melt polycondensation reaction. The reactions proceeded with high atom economy and yielded water as the only by product. Moisture-cured polyurethane-urea-polyurea and their soybean oil hybrid coatings were developed with H12MDI. Coatings exhibited excellent thermal stability, mechanical strength, abrasion resistance, gloss and anti-corrosion properties. Polyurethane-polyurea is useful as a cool coating due to excellent NIR-reflectance. Coating properties did not change much by addition of soybean oil to the main formulation, PUU. Soybean oil improved coating flexibility, reduced cost and added sustainability. Polyaspartic polymer exhibited excellent inhibition efficiency at very low concentration in 0.1N HCl. The inhibition property of polyaspartic would certainly aid in coatings’ anticorrosion ability. So, the developed polyaspartic material is sustainable, multifunctional and excellent anticorrosive coating technology. z
Acknowledgment
Rajnish Kumar thanks the Department of Science and Technology, Govt. of India, for the INSPIRE Fellowship.
References
1 De, S.; Jodie L. Lutkenhaus. Corrosion Behaviour of Eco-Friendly Airbrushed Reduced Graphene Oxide-Poly (Vinyl Alcohol) Coatings. Green Chemistry 20, no. 2 (2018): 506-514.
2 Schieweck, A.; Bock, M.C. Emissions from Low-VOC and Zero-VOC Paints– Valuable Alternatives to Conventional Formulations Also for Use in Sensitive Environments? Building and Environment 85 (2015): 243-252.
3 Huybrechts, J.; Dusek, K. Star Oligomers and Hyperbranched Polymers in Low-VOC Polyurethane Coatings: Part III. Surface Coatings International 81, no. 5 (1998): 234-239.
4 Chen, S.; Xu, Z.; Zhang, D. Synthesis and Application of Epoxy-Ended Hyperbranched Polymers.” Chemical Engineering Journal 343 (2018): 283-302.
5 Schubert, C.; Osterwinter, C.; Tonhauser, C.; Schömer, M.; Wilms, D.; Frey, H.; Friedrich, C. Can Hyperbranched Polymers Entangle? Effect of Hydrogen Bonding on Entanglement Transition and Thermorheological Properties of Hyperbranched Polyglycerol Melts. Macromolecules 49, no. 22 (2016): 8722-8737.
6 Sun, F.; Luo, X.; Kang, L.; Peng, X.; Lu, C. Synthesis of Hyperbranched Polymers and their Applications in Analytical Chemistry. Polymer Chemistry 6, no. 8 (2015): 1214- 1225.
7 Chen, H.; Kong, J. Hyperbranched Polymers from A2+ B3 Strategy: Recent Advances in Description and Control of Fine Topology. Polymer Chemistry 7, no. 22 (2016): 3643-3663.
8 Reisch, A.; Komber, H.; Voit. B. Kinetic Analysis of Two Hyperbranched A2+ B3 Polycondensation Reactions by NMR Spectroscopy. Macromolecules 40, no. 19 (2007): 6846-6858.
9 Kumar, R.; Narayan, R.; Aminabhavi, T.M.; Raju, K.V.S.N. Nitrogen-Rich Hyperbranched Polyol via A3+B3 Polycondensation: Thermal, Mechanical, Anti-Corrosive and Anti-Microbial Properties of Poly (Urethane-Urea), J. Polym. Res., Vol. 21, 547, 2014.
10 Chattopadhyay, D.K.; Raju, K.V.S.N. “Structural Engineering of Polyurethane Coatings for High-Performance Applications. Progress in Polymer Science 32, no. 3 (2007): 352-418.
11 Kumari, S.; Aswini, K.; Mishra, A.; Krishna, V.R.; Raju, K.V.S.N. Organically Modified Montmorillonite Hyperbranched Polyurethane–Urea Hybrid Composites.” Progress in Organic Coatings 60, no. 1 (2007): 54-62.
12 Pfister, D.P.; Xia, Y.; Larock, R.C. Recent Advances in Vegetable Oil-Based Polyurethanes.” ChemSusChem 4, no. 6 (2011): 703-717.
13 Kong, X.; Liu, G.; Qi, H.; Curtis, J.M. Preparation and Characterization of High-Solid Polyurethane Coating Systems Based on Vegetable Oil-Derived Polyols.” Progress in Organic Coatings 76, no. 9 (2013): 1151-1160.
14 Hojabri, L.; Kong, X.; Narine, S.S. Fatty Acid-Derived Diisocyanate and Biobased Polyurethane Produced from Vegetable Oil: Synthesis, Polymerization, and Characterization. Biomacromolecules 10, no. 4 (2009): 884-891.
15 Fragiadakis, D.; Gamache, R.; Bogoslovov, R.B.; Roland, C.M. Segmental Dynamics of Polyurea: Effect of Stoichiometry. Polymer 51, no. 1 (2010): 178-184.
16 Qiao, J.; Amirkhizi, A.V.; Schaaf, K.; Nemat-Nasser, S.; Wu, G. Dynamic Mechanical and Ultrasonic Properties of Polyurea. Mechanics of Materials 43, no. 10 (2011): 598-607.
17 Wicks, D.A.; Yeske, P.E. Polyurea Coating Compositions Having Improved Pot Lives. U.S. Patent 5,243,012, issued September 7, 1993.
18 Howarth, G.A. Polyurethanes, Polyurethane Dispersions and Polyureas: Past, Present and Future. Surface Coatings International Part B: Coatings Transactions 86, no. 2 (2003): 111-118.
19 Guan, S.W. 100% Solids Polyurethane and Polyurea Coatings Technology. Coatings World (2003): 49-58.
20 Balaskas, A.C.; Kartsonakis, I.A.; Snihirova, D.; Montemor, M.F.; Kordas. G. Improving the Corrosion Protection Properties of Organically Modified Silicate-Epoxy Coatings by Incorporation of Organic and Inorganic Inhibitors. Progress in Organic Coatings 72, no. 4 (2011): 653-662.
21 Tiu, B.D.B.; Advincula, R.C. Polymeric Corrosion Inhibitors for the Oil and Gas Industry: Design Principles and Mechanism. Reactive and Functional Polymers 95 (2015): 25-45.
22 Huang, H.; Yao, Q.; Liu, B.; Shan, N.; Chen, H. Synthesis and Characterization of Scale and Corrosion Inhibitors with Hyper-Branched Structure and the Mechanism. New Journal of Chemistry 41, no. 20 (2017): 12205-12217.
23 Pinoit, D.; Prud’homme, R.E. DSC and DMTA Characterization of Ternary Blends. Polymer 43, no. 8 (2002): 2321-2328.
24 Yang, J.; Han, C.R. Dynamics of Silica-Nanoparticle-Filled Hybrid Hydrogels: Nonlinear Viscoelastic Behavior and Chain Entanglement Network. The Journal of Physical Chemistry C 117, no. 39 (2013): 20236-20243.
25 Liao, H.; Normand, B.; Coddet, C. Influence of Coating Microstructure on the Abrasive Wear Resistance of WC/Co Cermet Coatings.” Surface and Coatings Technology 124, no. 2-3 (2000): 235-242.
26 Melchiors, M.; Sonntag, M.; Kobusch, C.; Jürgens, E. Recent Developments in Aqueous Two-Component Polyurethane (2K-PUR) Coatings. Progress in Organic Coatings 40, no. 1-4 (2000): 99-109.
27 Wazarkar, K.; Kathalewar, M.; Sabnis, A. High-Performance Polyurea Coatings Based on Cardanol. Progress in Organic Coatings 106 (2017): 96-110.
28 Levinson, R.; Akbari, H.; Reilly, J.C. Cooler Tile-Roofed Buildings with Near- Infrared-Reflective Non-White Coatings. Building and Environment 42, no. 7 (2007): 2591-2605.
29 Ostovari, A.; Hoseinieh, S.M.; Peikari, M.; Shadizadeh, S.R.; Hashemi, S.J. Corrosion Inhibition of Mild Steel in 1 M HCl Solution by Henna Extract: A Comparative Study of the Inhibition by Henna and its Constituents (Lawsone, Gallic acid, a-d-Glucose and Tannic acid).” Corrosion Science 51, no. 9 (2009): 1935-1949.
30 Lebrini, M.; Lagrenée, M.; Vezin, H.; Traisnel, M.; Bentiss, F. Experimental and Theoretical Study for Corrosion Inhibition of Mild Steel in Normal Hydrochloric Acid Solution by Some New Macrocyclic Polyether Compounds.” Corrosion Science 49, no. 5 (2007): 2254-2269.
31 Zhang, F.; Tang, Y.; Cao, Z.; Jing, W.; Wu, Z.; Chen, Y. “Performance and Theoretical Study on Corrosion Inhibition of 2-(4-Pyridyl)-Benzimidazole for Mild Steel in Hydrochloric Acid. Corrosion Science 61 (2012): 1-9.
32 Xu, B.; Liu, Y.; Yin, X.; Yang, W.; Chen, Y. Experimental and Theoretical Study of Corrosion Inhibition of 3-Pyridinecarbozalde Thiosemicarbazone for Mild Steel in Hydrochloric Acid.” Corrosion Science 74 (2013): 206-213.
33 Kissi, M.; Bouklah, M.; Hammouti, B.; Benkaddour, M. Establishment of Equivalent Circuits from Electrochemical Impedance Spectroscopy Study of Corrosion Inhibition of Steel by Pyrazine in Sulphuric Acidic Solution. Applied Surface Science 252, no. 12 (2006): 4190-4197.
34 Rbaa, M.; Benhiba, F.; Obot, I.B.; Oudda, H.; Warad, I.; Lakhrissi, B.; Zarrouk, A. Two New 8- Hydroxyquinoline Derivatives as Efficient Corrosion Inhibitors for Mild Steel in Hydrochloric Acid: Synthesis, Electrochemical, Surface Morphological, UV-Visible and Theoretical Studies. Journal of Molecular Liquids 276 (2019): 120-133.
This paper was originally presented at the 2019 Credit Polyurethane Technical Conference.
Looking for a reprint of this article?
From high-res PDFs to custom plaques, order your copy today!