A New Polyfunctional Aziridine Crosslinker

PolyAziridine LLC has developed a new difunctional water-based crosslinker. It is used to crosslink acid or carboxyl functional coatings, inks and adhesives to increase adhesion, physical and chemical properties. Test data, including MEK double rubs and chemical spot testing comparing the new crosslinker and typical trifunctional polyaziridine crosslinkers, showed similar results in clear coatings based on an acid functional polyurethane/acrylic blend and a polyurethane dispersion. This article will also show more properties comparing the new crosslinker to trifunctional polyfunctional aziridine crosslinkers. And, since the new crosslinker is an aqueous dispersion, it has the potential of formulating a one-part system of a polyurethane dispersion ink, adhesive or coating.
Chemical Molecule
The molecule of this new difunctional water-based crosslinker is based on the reaction of methylene diphenyl diisocyanate (MDI) and ethylene imine (EI), and is shown in Figure 1.
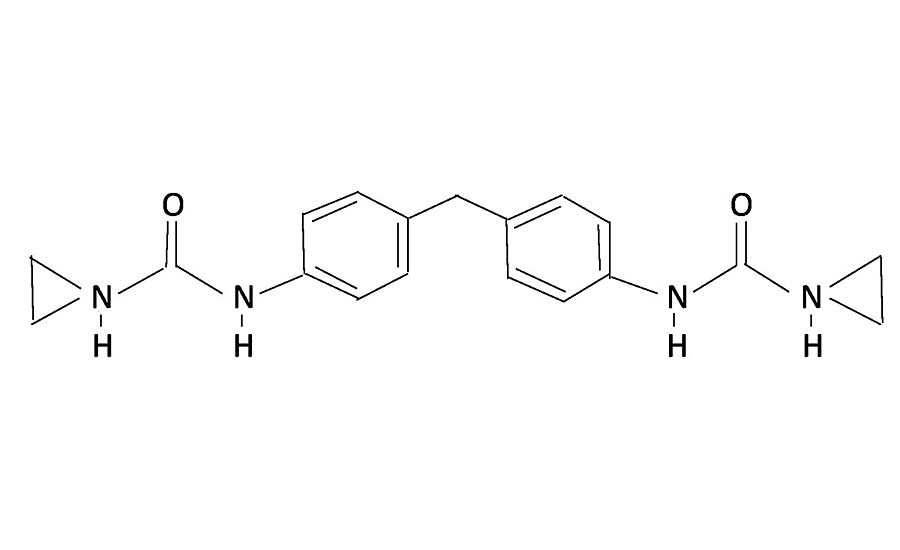
Reaction Mechanism
This new crosslinker is used to crosslink water-based, acid functional resins. The reaction mechanism is the result of the aziridine end groups reacting with active hydrogen as found on carboxyl groups of acrylic emulsions or polyurethane dispersions. The reaction mechanism is shown in Figure 2.
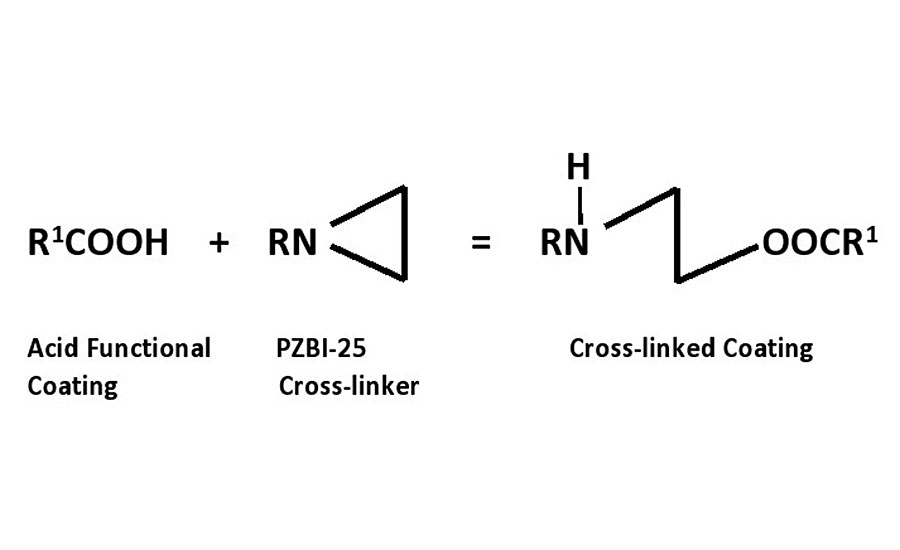
The hydrogen of the resin carboxyl group protonates the nitrogen group of the crosslinker, which causes the ring to open and react with remaining resin, yielding a crosslinked density since both ends of the difunctional crosslinker react with resin acid groups.
Crosslinker Properties
This crosslinker is a white aqueous dispersion with a solids level of 27 ± 1% and viscosity of <300 centipoise at 25 ºC. The CAS number is 7417-99-4 and has been evaluated and listed on the European REACH registration list. This product does need to be heat cured to activate crosslinking. The activation heat range is 200 ºF to 275 ºF (80 ºC to 120 ºC).
Addition Level and Technique
The aqueous crosslinker is added to the formulated system at 2-3% by weight. Through experimentation, it is best to determine the ideal level of the crosslinker to be used in each system to achieve the desired end results. It is added to the system slowly and under agitation. After adding all of the product, allow the mixture to continue to stir for 5 min.
Chemical Test Study
Two aqueous clear coatings were selected for this study: an 80/20 ratio of an acrylic emulsion and a polyurethane dispersion resin, and a pure polyurethane dispersion resin. Both coatings were carboxyl functional.
Three polyfunctional aziridine crosslinkers and a control without crosslinker were used for this study to evaluate chemical resistance. The three crosslinkers consisted of the new crosslinker, PZBI-25, and two conventional trifunctional polyfunctional aziridine crosslinkers referred to as Xlinker 1 and Xlinker 2 in the test data.
The chemical testing included methyl ethyl ketone (MEK) double rub per ASTM D4752, Standard Test Method for Measuring MEK Resistance of Ethyl Silicate (Inorganic) Zinc-Rich Primers by Solvent Rub, and Chemical Spot Testing per ASTM D-1308-02, Household Chemical Spot Test Method.
The panels used for the study were unprimed aluminum Q-Panels.
Preparation of Test Panels
The coated test panel preparation was the same for the MEK and Chemical Spot tests. 2% by weight of each crosslinker was added to each of the two coatings while stirring with a glass rod. After the addition, the mixture was stirred for an additional 3 min. Afterwards, each mixture sat for 10 min to relieve any bubbles that may have formed. Then, each mixture was drawn down on the aluminum panel. Four panels were prepared for each mixture so that duplicate testing could be performed. After each set of four panels was prepared, they were inserted into an oven maintained at 225 ºF (107 ºC) and baked for 1 min. Afterwards, they were removed from the oven and placed on a bench at ambient conditions for 1 week.
MEK Double Rubs and Chemical Spot Testing Results
MEK double rub testing was performed manually using cheesecloth over the index finger and saturating it in MEK. The finger was re-saturated every 50 rubs. The angle of rubs was 45 degrees. Each downward and upward motion was counted as a single rub. Figure 3 shows the MEK double rub results. Note that after 200 double rubs, the test was stopped.
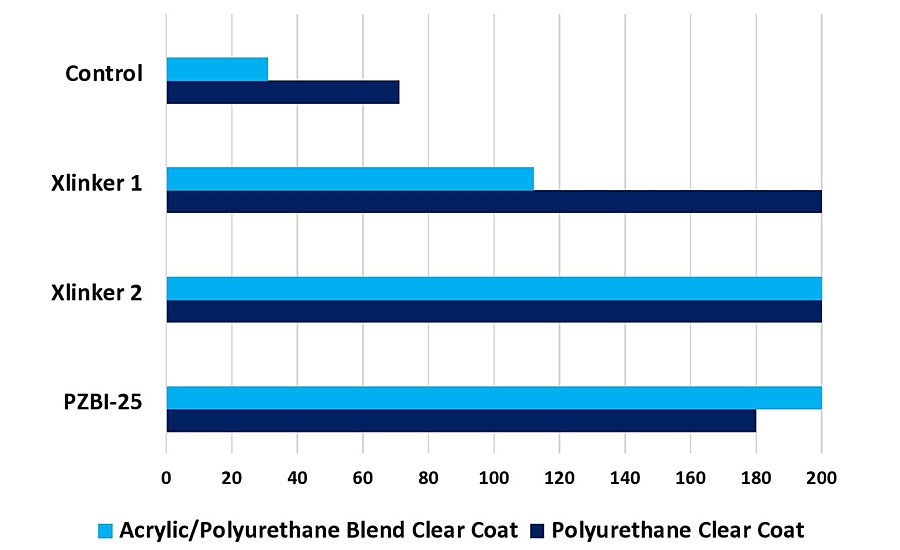
The MEK results first show that without any of the crosslinker, both clear coatings have significantly less performance versus the crosslinked coatings. Secondly, the PZBI-25 performed like the conventional trifunctional crosslinkers.
The chemical spot test reagents consisted of water, isopropyl alcohol and mustard. A 1-inch piece of filter paper was positioned on the surface of the test panels to keep the reagent positioned in a 1-inch-diameter circle. Then, reagent was applied slowly using a 1-mL syringe onto the filter paper, and each reagent was covered with a watch glass. Due to the viscosity of the mustard, no filter paper was needed. The reagent remained for 1 hr. After which, the watch glass was removed, and the reagent was removed softly with a paper towel. Each spot was evaluated for staining and surface attack. Table 1 shows the results.
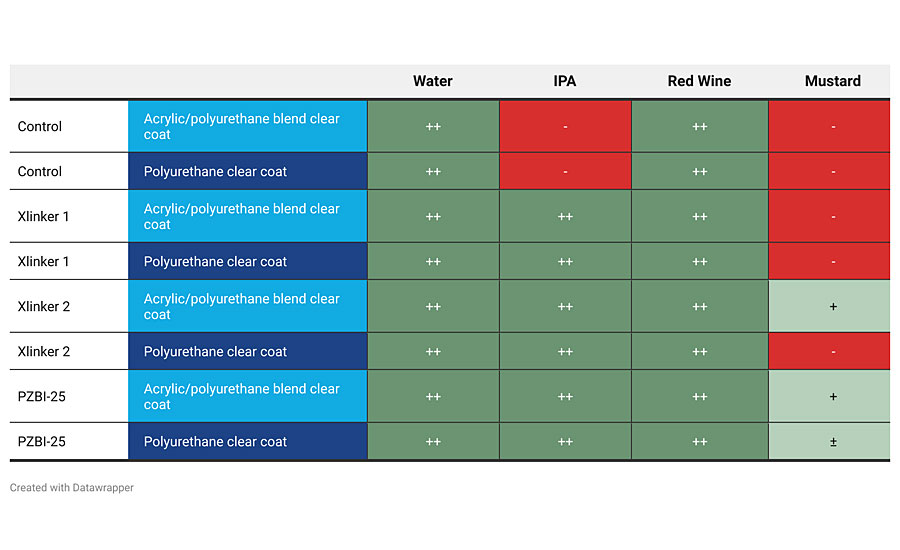
The test results showed that with and without crosslinker, the clear coatings performed well with water and red wine. It shows that there is no negative performance with the addition of the crosslinkers in the coatings. However, the control was attacked by the IPA and stained significantly with mustard. Whereas all the crosslinked samples had excellent resistance to attack from IPA. Mustard staining was present for the control and Xlinker 1, but Xlinker 2 had slight staining with the acrylic/polyurethane blended coating. The PZBI-25 had slight staining in the blended coating had very slight staining in the polyurethane coating.
Summary of the New Crosslinker versus Conventional Crosslinkers
Table 2 compares general properties of the new crosslinker versus conventional tri-functional polyfunctional aziridine crosslinkers. Since the new crosslinker is a dispersion, it mixes into a water-based coating very easily. Whereas more care must be given to the addition of the trifunctional crosslinkers to get a homogeneous mixture.
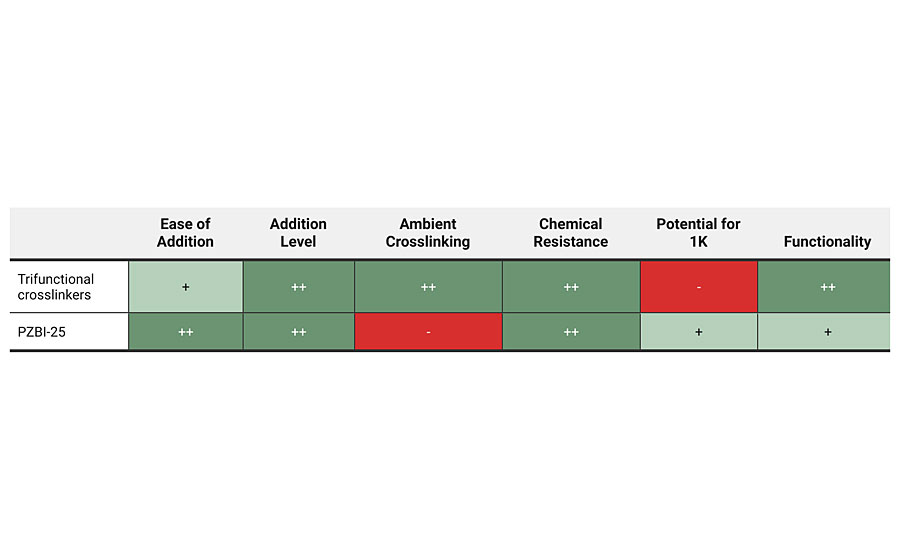
- The addition levels of both types of crosslinkers were the same low 2% by weight into the formulated coatings.
- The traditional tri-functional crosslinkers will react at room temperature. However, the new crosslinkers require a heat cure.
- The chemical resistance observed in this study yielded equivalent results for both types of crosslinkers.
- The new crosslinker has the potential of developing a one-part system since it is a dispersion, but the conventional tri-functional polyaziridine crosslinkers have a pot-life once they are added to the coating.
- Finally, the functionality of conventional aziridine crosslinkers is trifunctional versus the new crosslinker, which is difunctional.
For more information, visit www.polyaziridine.com.
Looking for a reprint of this article?
From high-res PDFs to custom plaques, order your copy today!