A pigment is any finely divided, insoluble material that is added to a coating system prior to application on a substrate. Typically, pigments are used to modify the optical properties of a cured film by introducing decorative color, enhancing opacity or controlling gloss. In addition to promoting visual effects, these materials are also commonly used as rheology modifiers, extenders and corrosion inhibitors. However, in all cases, the key to efficiently promoting the desired functionality rests with the ability to control both the distribution and particle size of the added pigment(s) within a coating formulation.
Achieving the desired pigment distribution within a coating system is not a straightforward process. Pigments are commonly supplied as powders or beads, which themselves are composed of large agglomerates of individual particles. For most purposes, these agglomerates need to be milled to obtain a consistent particle size, preferably as primary particles. The newly formed insoluble particles must then be evenly distributed in the media and prevented from reforming agglomerates. The process by which pigment milling, as well as particle separation and stabilization occurs is called dispersion.1
During the dispersion process, as the relatively large agglomerates become separated, a new interface forms between each particle and the surrounding liquid. For pigments that act as colorants, their use requires a dramatic reduction in particle size, with the resulting creation of a very large solid/liquid interface. The dispersion process is highlighted in Figure 1. These SEM images show raw yellow PY-74 agglomerates followed by their breakup and dispersal in the bulk media.
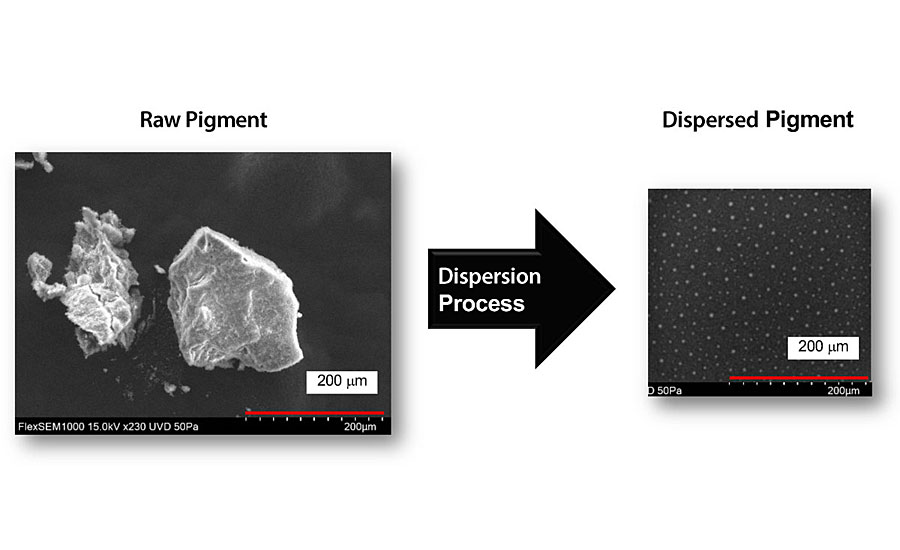
The process of pigment dispersion is facilitated through the addition of external mechanical force and the use of amphiphilic additives. Dispersants are one such additive that help to overcome key challenges encountered in the generation of dispersions. They can play multiple roles including wetting of the substrate, protection of the newly created pigment surface, control of viscosity and flow characteristics of the dispersion, sufficient and uniform reduction of particle size, and maintenance of the dispersion stability.2-3
Stepan Company has recently developed a new class of high-performance polymeric (HPP) dispersants that are very effective for creating pigment dispersions.4 In theory, these dispersants work by irreversibly adsorbing onto the pigment surface, while extending their long stabilizing segments into the continuous phase, providing steric and/or electro-steric stabilization. What makes HPP dispersants particularly useful is their potential to facilitate every stage of the dispersion process, offering excellent pigment wetting, easier and better separation of the particles, and long-term stabilization of the pigment dispersion.5-6
These attributes afford concrete benefits in application. During milling, the lower viscosity of the millbase allows for more pigment to be processed per batch. In let-down, compatibility of the pigment dispersion is improved, as a smaller amount of a less interacting dispersant is used. Further, the use of a smaller amount of pigment is possible because it is more effectively dispersed. Finally, better color development and gloss can be obtained on the resultant film as the pigment dispersion remains stable.
Experimental Details
Pigment dispersions were prepared by combining pigment, dispersant, defoamer, biocide and water together with grinding medium (0.8 – 1.0 mm glass or zirconium beads) in glass jars. During initial screenings, the jars were agitated on a shaker for 4 hrs; the time was varied from 1 to 10 hrs for milling efficiency studies. After milling, beads were removed by filtration, and the dispersions were evaluated.
Dispersion viscosity was measured using a rheometer (Anton Paar), at 25 °C with a 5-cm plate geometry. The viscosity at a shear rate of 10 s-1 was used for product comparison. Particle size was analyzed at 0.1% solids in water using a Zetasizer (Malvern). Stability was assessed by monitoring changes in dispersion appearance, viscosity and particle size while maintaining samples at 50 °C over a period of 4 weeks.
Tinting (dispersion let-down) was performed at a 1:9 volume ratio of pigment dispersion to basecoat. The paint was then drawn down with a 3-mil Bird bar on a glass slide and was allowed to dry at ambient conditions for 24 hrs before evaluation. Film jetness and undertone were calculated from measured values of X, Y and Z, which were measured with a spectrophotometer (X-Rite). Gloss was determined using a micro-tri-gloss meter (BYK).
Results and Discussion
Technology DevelopmentA generalized structure of Stepan’s HPP dispersants is shown in Figure 2. These HPP dispersants are composed of three discreet components:
- A linker, which can vary in length, functionality, flexibility and number of appendages;
- Affinity domains, which are designed to interact with the pigment surface, and can vary by the type, number and arrangement of anchoring groups;
- Stabilizing segments, which can differ by length, hydrophobicity and functionality.
This modular design of Stepan’s patent-pending technology enables the synthesis of a wide variety of dispersant concepts; each component of the generic structure can be varied independently. In addition, Stepan’s HPP dispersant technology is VOC free (ASTM Method D6886-14).
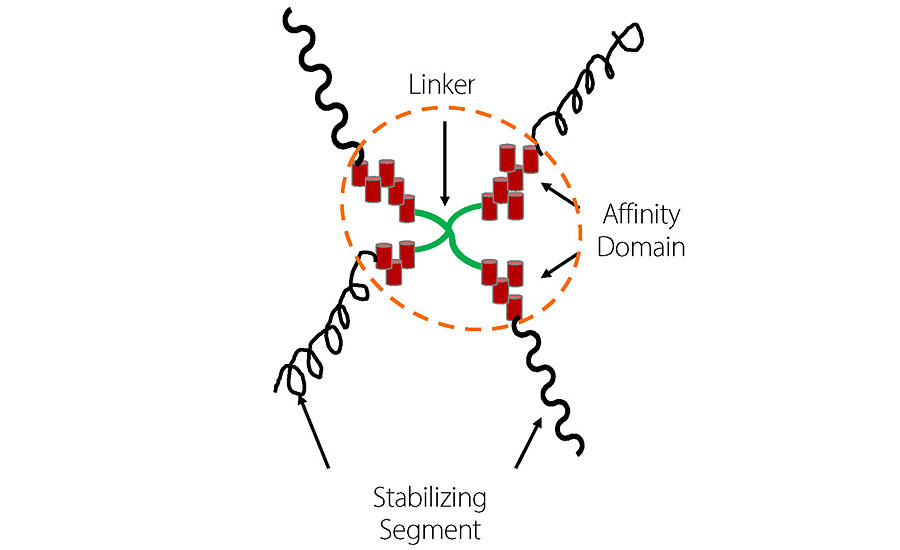
Throughout the process of evaluating the structural attributes of dispersants made with our chemistry, focus remained on identifying the most promising candidates.7 In addition to dispersion viscosity and paint compatibility, a number of additional criteria were examined, including dispersion stability, dispersant demand, milling efficiency, paint color development and product form. Dispersant 61 (commercially available as STEPSPERSE® 61) emerged as one of the best overall performers. A snapshot of the results obtained with Dispersant 61 is given in Figure 3. At optimum dispersant solids over pigment (SOP), each of the generated colorants has a viscosity at or below 110 cps at a shear rate of 10 s-1. Given the structural diversity of the nine pigments examined, these data underscore the broad utility of the technology.

Having demonstrated good efficiency, pigment versatility and resin compatibility of Dispersant 61, attention was directed to industrial-grade carbon blacks for industrial applications, which are of critical importance in the marketplace.
Industrial-Grade Carbon Black
Depending on the raw materials used and the method of manufacturing, carbon black can have a surprising range of different structures, physical forms and surface area values.8-9 In the case of carbon blacks that are used for industrial applications, they tend to have much higher surface areas compared to their architectural counterparts. The smaller particle sizes coupled with a higher degree of structure results in a pigment that is more difficult to wet and disperse. Furthermore, industrial carbon black is frequently used to tint coatings containing a wide variety of polymer resins, meaning that broad compatibility is essential to developing a successful product.
Industrial Black 1, which has a surface area of 583 m2/g (BET) and is acidic (pH = 3.0, at 2% pigment in water) was chosen for evaluation. Dispersions were formulated according to the method outlined in Table 1. In general, formulations were prepared with 15-20% PBK-7 at 60-100% dispersant solids over pigment.
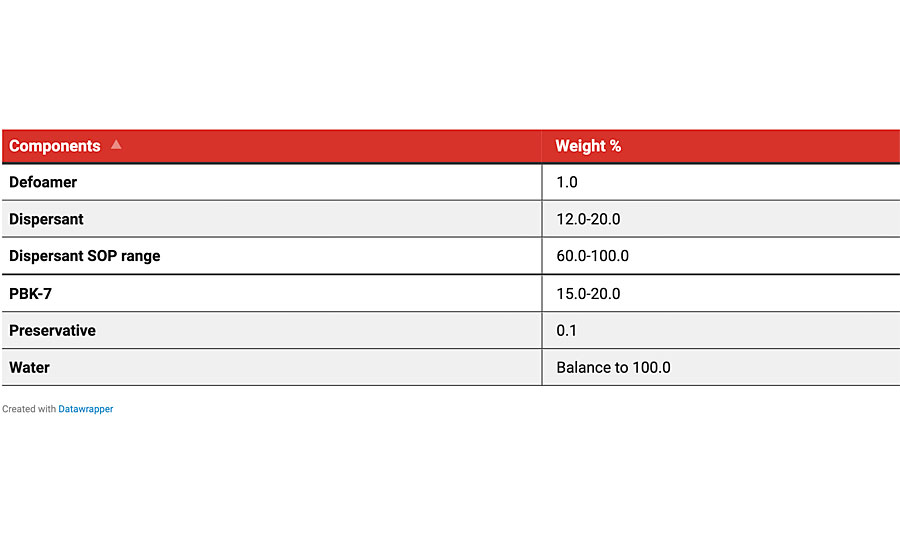
Four different commercial benchmarks, each known to be an excellent dispersant for carbon black, were chosen to compare with Dispersant 61. These five dispersants were subjected to a dispersant demand study with Industrial Black 1 at 20% pigment loading (Figure 4). The optimum SOP for Dispersant 61 was found to be very similar to three of the four standards; Control 3 was the poorest performer with this pigment. Dispersions that were generated using Dispersant 61, Control 1 and Control 2 (20% pigment loading with 60% dispersant SOP) were then subjected to a stability study. It was found that after only 1 week at ambient temperature, sedimentation had occurred in Control 1 and Control 2. In contrast, the dispersion prepared with Dispersant 61 remained stable under those conditions for more than 6 months.
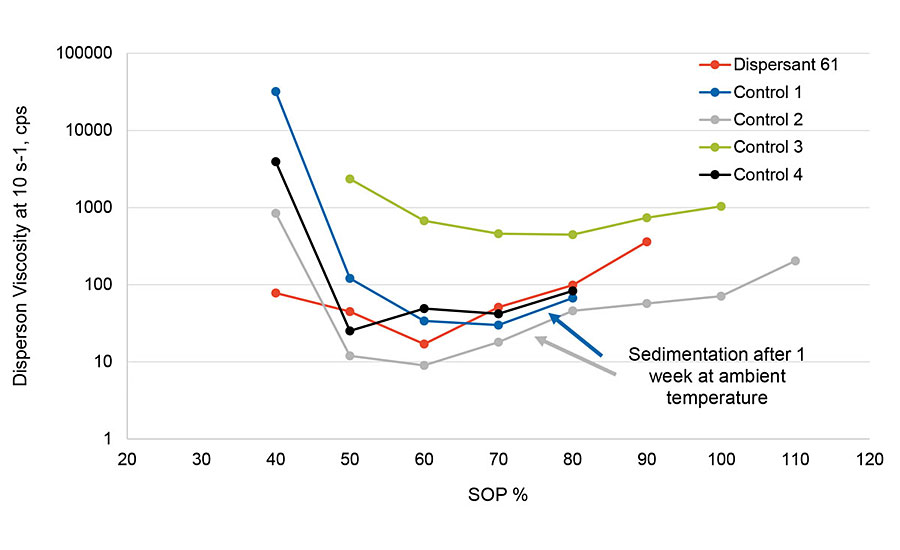
Using the same commercial standards, a milling efficiency study was conducted using Industrial Black 1 (Figure 5). This was done at 15% pigment loading and 100% dispersant SOP. Of the dispersants tested, Dispersant 61 demonstrated the best overall performance, both in terms of the speed in reduction of pigment particle size and the final particle size (less than 70 nm). These attributes offer a potential cost advantage over competitive products, as less time and energy are required to obtain the pigment particle size needed for a given application. Moreover, the rapid reduction in particle size suggests that Dispersant 61 is more effective at wetting than the controls tested.
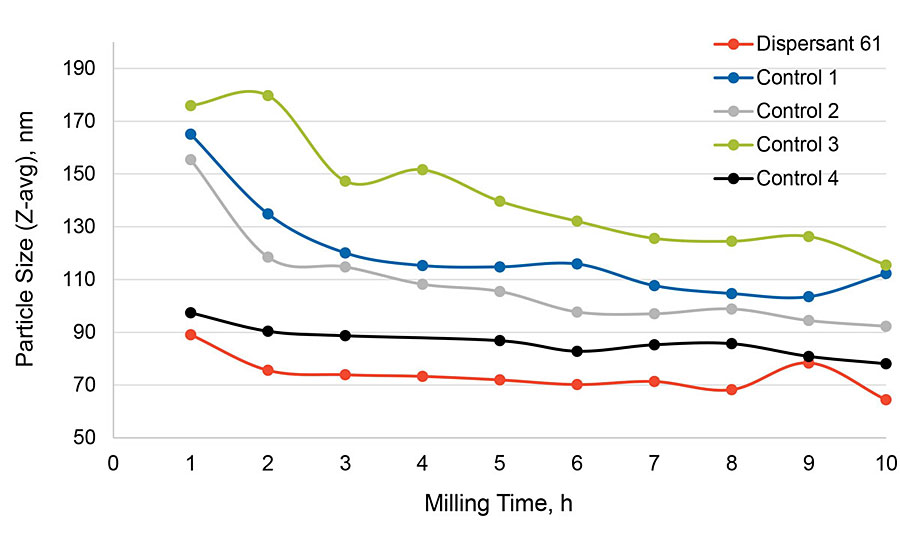
The dispersions produced in the milling analysis were further assessed through a high-temperature stability study (Figure 6). Dispersions made with Dispersant 61 exhibited better stability when compared with the controls, with essentially no change in viscosity over 4 weeks at 50 °C. Particle sizes were also measured during this time, and minimal changes were observed for Dispersant 61, whereas the dispersions made with the controls showed some changes.
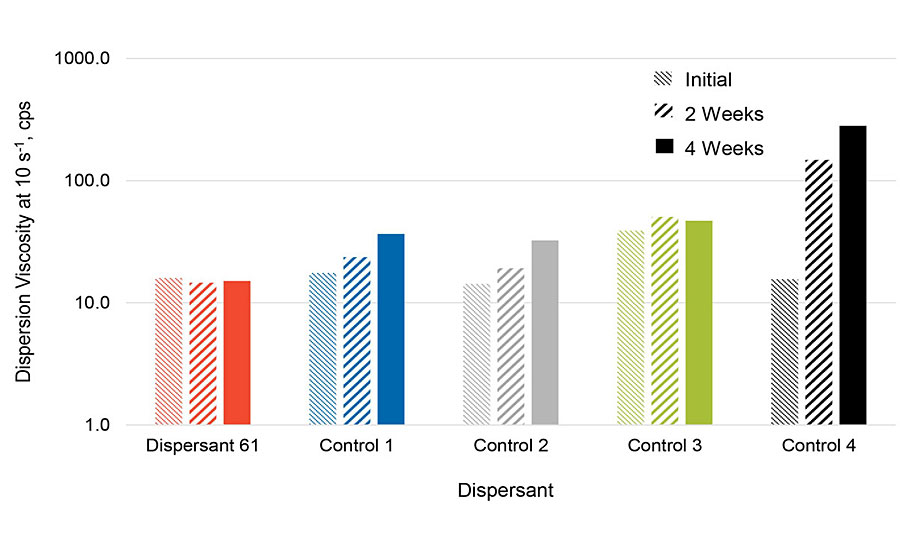
Taken together, these results show that Dispersant 61 offers clear advantages over commercial controls in the preparation of dispersions of Industrial Black 1. These benefits include faster particle size reduction, smaller final particle size and improved dispersion stability. Additionally, the optimum SOP for Dispersant 61 was determined to be equivalent to or lower than the tested commercial controls.
The dispersions containing 15% carbon black and 100% dispersant SOP were further evaluated to tint various base coatings (tinting was conducted as outlined in experimental section). A number of different resin types were utilized in the tinting studies. They included an acrylic, a vinyl acrylic, a polyurethane dispersion (PUD), a styrene acrylic, a cationic styrene acrylic, an alkyd, an acrylic/PUD blend, and a hydroxyl-functionalized acrylic. In the case of an acrylic coating system, let-down with a dispersion of Industrial Black 1 that had been prepared with Dispersant 61 afforded improved jetness and underdone (Figure 7) with similar 60° gloss when compared against the selected controls.
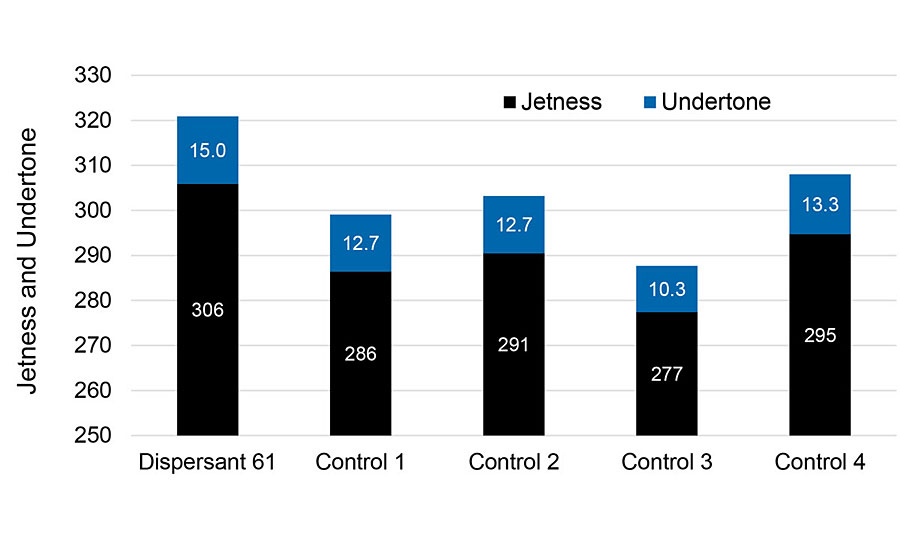
Let-down tinting of a vinyl acryl resin gave similar results. Superior jetness was again achieved with Dispersant 61. Notably, some of the commercial standards exhibited poor compatibility with this coating (Figure 8). In particular, let-down with dispersions made from Controls 1 and 2 resulted in the formation of a clumpy mixture, with significantly higher viscosity over that of the base paint. On the other hand, the use of dispersions made with either Dispersant 61 or Control 3 showed good compatibility and caused very little change in paint viscosity.
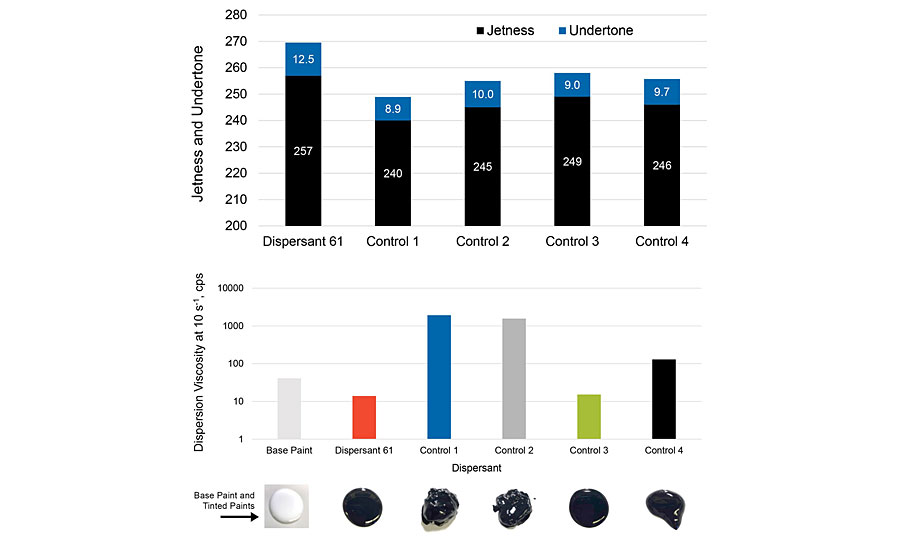
In addition to acrylic and vinyl acrylic paints, dispersions of Industrial Black 1 were let-down in several additional resins. These data are summarized in Figure 9. In six of the seven systems tested, let-down with dispersions prepared with Dispersant 61 afforded cured films with the best jetness. Likewise, dispersions prepared with the technology showed excellent compatibility with every paint evaluated.
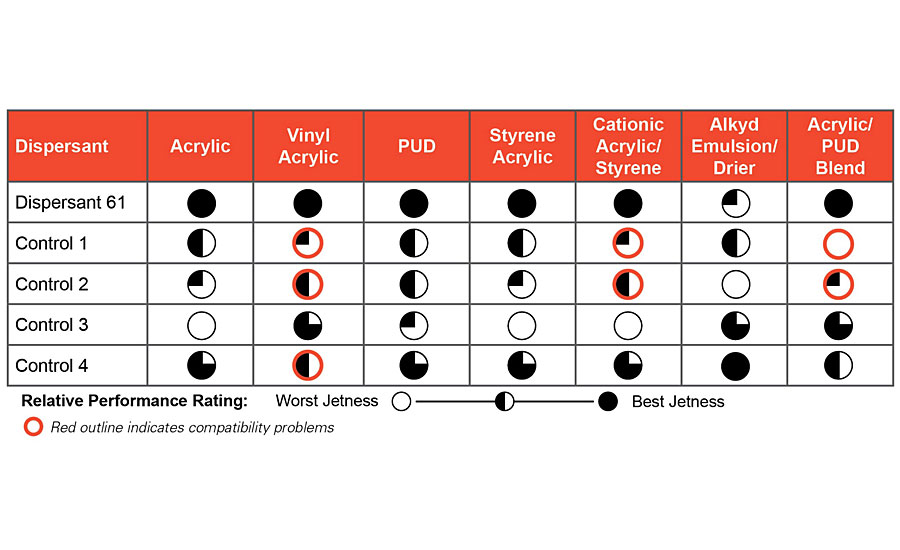
The performance attributes of Dispersant 61 were maintained when additional industrial carbon blacks were evaluated. As was observed with Industrial Black 1, dispersions made with this technology exhibited excellent compatibility and jetness development when used to tint different types of base paints.
Conclusion
Stepan has developed a proprietary modular chemistry platform that has been successfully leveraged to generate a new class of HPP pigment dispersants. Dispersant 61 (or STEPSPERSE 61) has demonstrated broad utility in preparing effective dispersions of several different pigment types. When used with architectural-grade carbon black, this novel technology affords significantly improved dispersion stability when compared with commercial benchmarks. STEPSPERSE 61 also exhibits excellent performance with industrial grade carbon blacks, offering superior milling efficiency, jetness, and resin compatibility.
References
¹ Mang, T.; Dresel, W. Lubricants and Lubrication, Wiley-VCH; Volume 1 (2017), p 862.
² van den Haak, H.J.W. Dispersant; Kirk-Othmer Encyclopedia of Chemical Technology, John Wiley & Sons; Vol 8 (2003), p 672-697.
³ van den Haak, H.J.W.; Krutzer, L.L.M. Design of Pigment Dispersants for High-Solids Paint Systems; Progress in Organic Coatings; Vol.43 (2001), p 56-63.
⁴ Vargas,C.; Dong, S.; Boebel, T. Novel High-Performance Polymeric Dispersants for VOC-Free Colorant; Pitture Vernici European Coatings Formulation; Vol 98 (2020), p14-17.
⁵ Hampton, J.S. A Review of Hyperdispersant Technology; Polymeric Materials Science and Engineering; Vol. 55 (1986), P 31-37.
⁶ Bauer, S.; Kleinsteinberg, F.; Reuter, E.; Glöckner, P. The Star Performer; European Coatings Journal; 5 (2010), p26-31.
⁷ Dong, S.; Vargas, C.; Boebel, T. High-Performance Polymeric Dispersant for Carbon Black in Waterborne Systems; American Coatings Show, 2020.
⁸ Danenberg, E.M.; Paqun, L.; Gwinnell, H. Carbon Black; Kirk Othmer Encyclopedia of Chemical Technology, John Wiley & Sons; Vol. 4 (1992), p1037-1074.
⁹ Carbon Black 101, https://www.birlacarbon.com/whats-trending/carbon-black/.
Report Abusive Comment