Although typically used only at amounts of 0.1% to 2% of the total formulation, pH neutralizers can have a dramatic impact on the overall performance of waterborne coatings. Depending on the formulation, manufacturers have several options for adjusting pH in their formulations.
The most commonly used inorganic neutralizers include ammonia and strong inorganic bases, such as potassium hydroxide (KOH) or sodium hydroxide (NaOH). While ammonia is an efficient neutralizer, it also has a strong odor, making it unsuitable for use in low-odor paint. Strong inorganic bases like KOH and NaOH are odorless, but result in coatings with poor scrub resistance and water resistance. The use of siliconates, which are less commonly used inorganic neutralizers, often result in loss of gloss and cause stability issues of the paint.
Organic amines, such as 2-amino-2-methyl-1-propanol, are widely accepted by the coatings industry for their multifunctional benefits beyond pH neutralization, such as pigment co-dispersancy, rheology stability, low odor, and in-can corrosion resistance. However, in certain industrial coatings applications with reactive chemistry, such as isocyanate curing or melamine formaldehyde curing, the active hydrogen of the amine neutralizer may interfere with the curing chemistry. As a result, there is continuing interest from industry for an organic amine neutralizer that could provide the multifunctional benefits of an organic amine without negatively affecting the application or dry-film properties of the coating.
Balanced Volatility and Base Strength
A new amine neutralizer, dimethylmethoxypropylamine (DMMOPA), was recently introduced for potential use in industrial and automotive coatings. DMMOPA was prepared by methylation of methoxypropylamine with formaldehyde, followed by a hydrogenation reduction and distillation/purification to obtain the target compound.
The key physical parameters of DMMOPA include a low-intermediate boiling point, forms an azeotrope with and is fully miscible with H20, and is nonreactive. The in-formulation functionality of DMMOPA was studied in waterborne melamine formaldehyde-cured coatings and latex-based air-drying paints.
Study
Formulation
In waterborne coatings, the binder resins, either in the form of water-reducible or dispersible polymer, are stabilized through the hydrated ionic pairs formed between the basic pH neutralizers and the acidic moiety on the polymer backbones. In this study, two water-reducible polyol resins were used:
- Acrylic polyol Paraloid™ WR-97 from The Dow Chemical Company;
- Polyester polyol Polymac™ WR 72-7203 from Polynt Group.
The physical parameters of these two binder polymers are listed in Table 1.
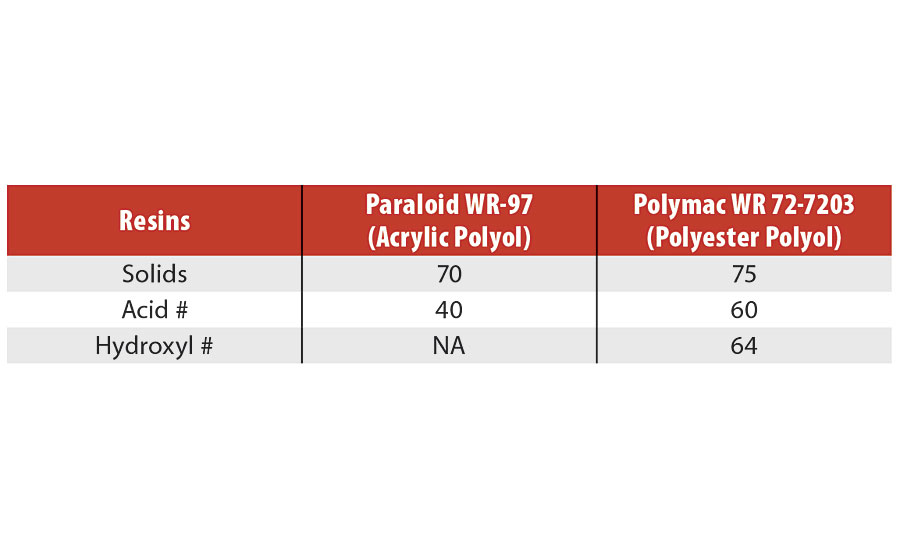
TABLE 1 » Resins used in polyol–melamine formaldehyde curing systems.
Two melamine formaldehyde resins from Allnex were evaluated:
- Cymel® 303, highly methylated;
- Cymel 325, high imino content.
The polyol-melamine formaldehyde curing formula used in this study is described in Table 2.
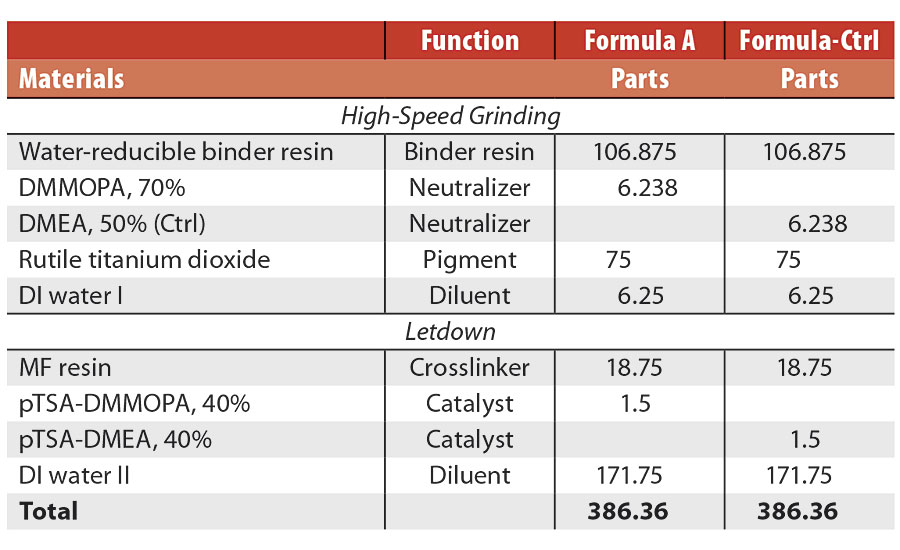
TABLE 2 » Formulas of water-reducible polyol–melamine formaldehyde curing system.
Waterborne Styrene Acrylic Paint Formulations
For the latex paint, RayKote™ 2010 styrene acrylic polymer from Specialty Polymers Inc. was used as the binder resin, which has a solids content of 50%, pH of 8.7 and Tg of 27 °C. The industrial coating formula (Table 3) used in this study was provided by Engineered Polymer Solutions.
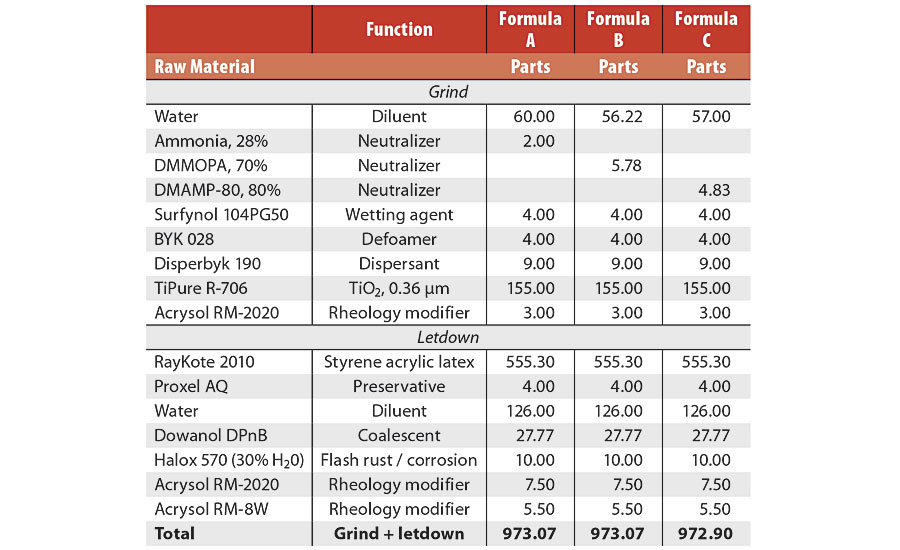
TABLE 3 » Formulas of waterborne styrene acrylic latex paint.
Results and Discussion
Waterborne polyol melamine formaldehyde curing chemistry has been used extensively in many industrial coating and automotive applications. One of the challenges facing the automotive coatings industry is the combination of reducing the curing temperature and shortening the baking cycle time to reduce energy costs, as well as reduce the curing temp to below 100 °C to coat onto thermal-sensitive substrates such as plastics, in a single process step.
It is generally accepted that the curing mechanism is due to the condensation reaction between alkoxyl or imino group of melamine resin and the hydroxyl group of the polymer to form the crosslinked structure and release methanol or water.1 The reaction is acid catalyzed, and typically the coating is baked at 120-170 °C for approximately 15-30 min to fully cure the coatings. Amine neutralizers provide the stabilization to the polyol polymer in aqueous phase through the ionic interaction with acidic functionalities on the polymers. However, the amine neutralizer can also hinder the curing reaction if it is not volatile enough and keeps the pH of the paint high for an extended period during the baking/curing process.
While dimethylethanolamine (DMEA) has been used for many years as the neutralizer for these coating systems, it has a relatively high boiling point at 135 °C and has an active hydrogen – both of which could negatively affect the curing performance, especially at low curing temperatures.
DMMOPA, on the other hand, has properties distinct from DMEA. In particular, DMMOPA does not have an active hydrogen, has a boiling point of 122 °C and can form an azeotrope with H2O at a 70:30 ratio at 93 °C, which is much lower than the 135 °C boiling point of DMEA. In the study, DMMOPA was evaluated for curing properties as the neutralizer against DMEA in the formulas described in Table 2 with five different combinations of polyol resins and melamine formaldehyde resins described in Table 4.
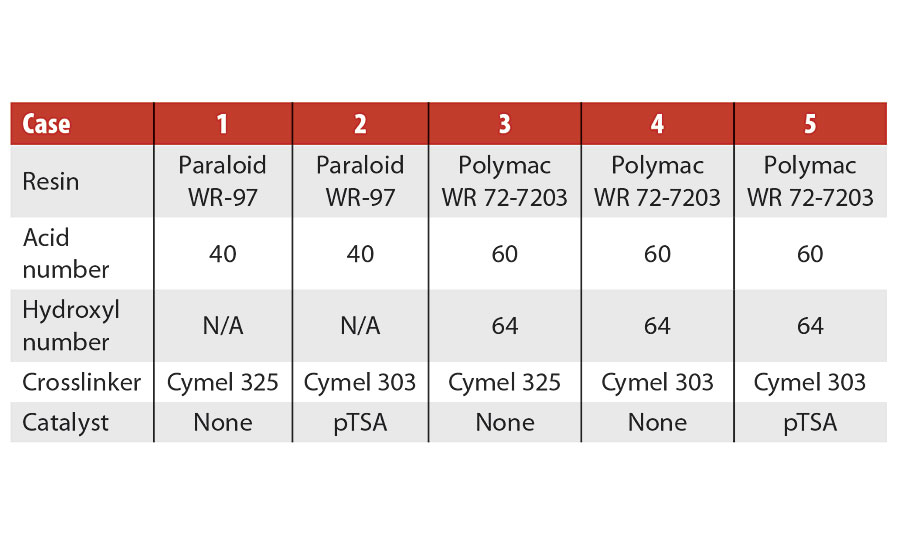
TABLE 4 » Curing case studies of polyol polymers and melamine formaldehydes.
Table 5 shows the curing conditions and cured film properties of Case Study 1 with acrylic polyol Paraloid WR-97 as the binder resin and Cymel 325 as the crosslinker. The formula of the solventborne control is similar to the formula described in Table 2, but uses DPnB as the solvent instead of water to represent the best-case scenario as far as the curing performance. The coating neutralized with DMMOPA demonstrated much-improved curing properties versus DMEA at the low temperature end (95-100 °C), as evidenced by the improved solvent resistance and pencil hardness comparison. With more than 200 MEK double rubs at 95 °C, DMMOPA shows the potential for the sub-100 °C curing. Compared with the solventborne control, the performance of DMMOPA is within a 5 °C difference.
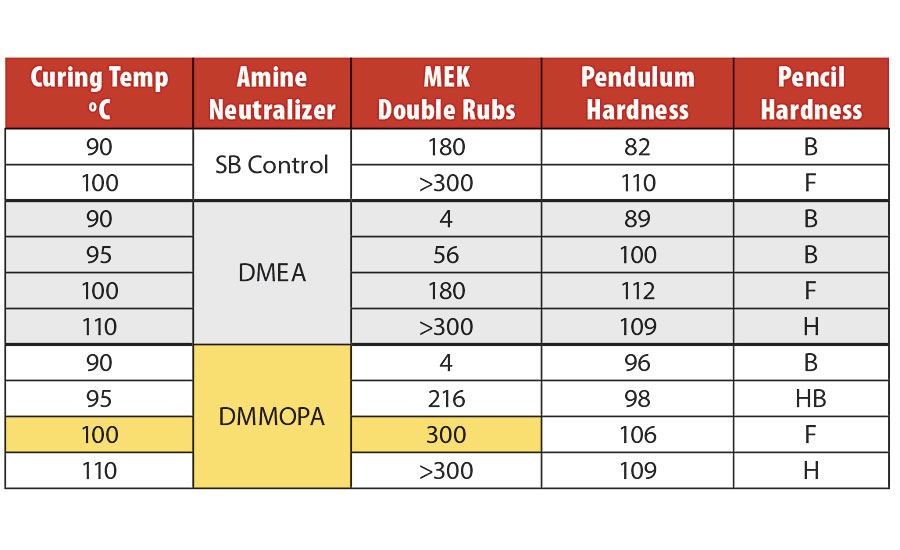
TABLE 5 » Polyol MF curing Case Study 1.
Case Study 2 (Table 6) with Paraloid WR-97 and highly methylated MF Cymel 303 (catalyzed by small amount of p-Toluenesulfonic acid), curing required a higher temperature than Case Study 1 due to the high reaction activation energy of methylated MF. Similar improvement in solvent resistance and pendulum hardness across the baking temperature range was observed for the formula neutralized with DMMOPA compared with DMEA.
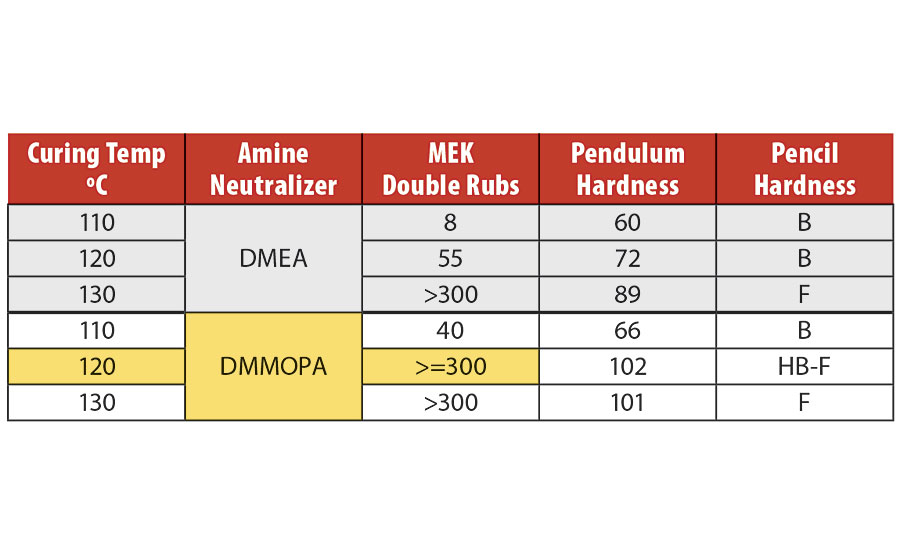
TABLE 6 » Polyol MF curing Case Study 2.
In addition to the acrylic polyol, a polyester polyol was used to evaluate the curing performance of the coating neutralized with DMMOPA and DMEA. The reason is that the acid monomer used in acrylic polyol synthesis is typically MAA or AA, which is an aliphatic acid and has a pKa around 4.75. Polyester polyol, on the other hand, typically uses aromatic acid monomer, and the pKa can be one magnitude higher than MAA and AA, and can potentially bind to amine neutralizers more strongly masking the difference of DMMOPA and DMEA. Case Studies 3-5 answer this question.
In Case Study 3 with polyester polyol and high imino MF (Table 7), DMMOPA maintained a clear advantage over DMEA as the neutralizer for the curing performance, such as solvent resistance and pencil hardness, which suggests that the positive properties of DMMOPA were not restricted by the type of counter acid on the polymer.
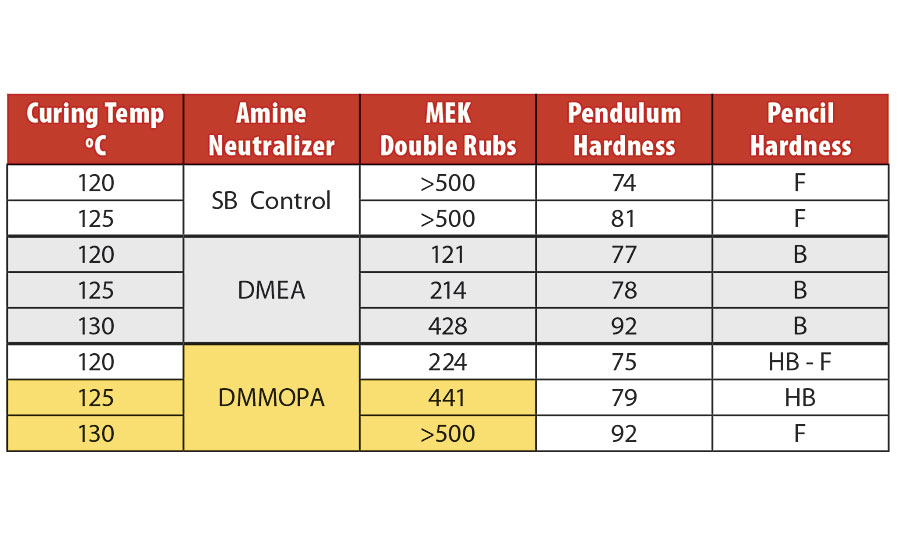
TABLE 7 » Polyol MF curing Case Study 3.
Case Study 4 (no catalyst) and Case Study 5 (with catalyst) compared the effect of p-Toluenesulfonic acid catalyst on the curing properties of paints neutralized with DMEA and DMMOPA. In Case Study 4 without catalyst (Table 8), clear improvement was observed for the performance of DMMOPA- versus DMEA-neutralized paints. This improvement was apparently widened across the range of curing temperatures studied when 0.4% p-Toluenesulfonic acid was used (Table 9). This indicates that DMMOPA is more responsive to catalytic effect and, therefore, could achieve better curing properties at even lower temperatures when catalyst is used.
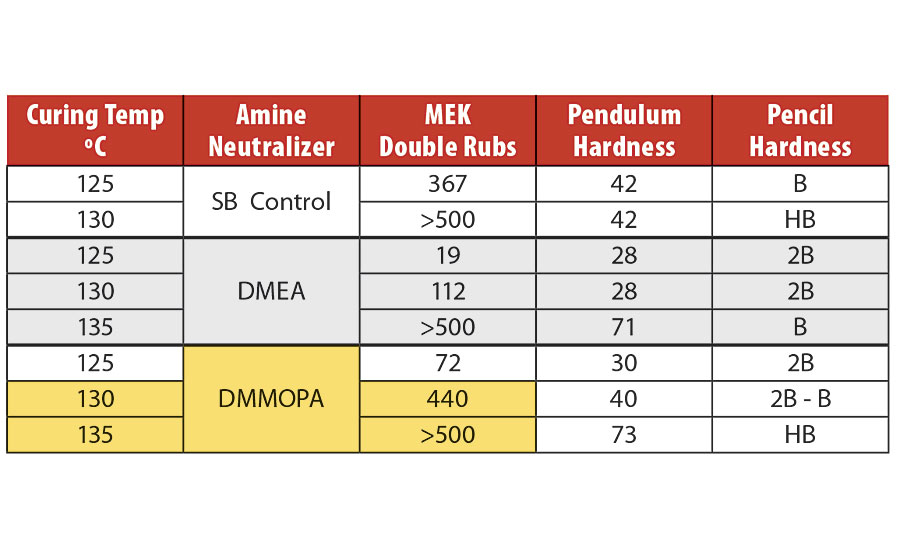
TABLE 8 » Polyol MF curing Case Study 4.
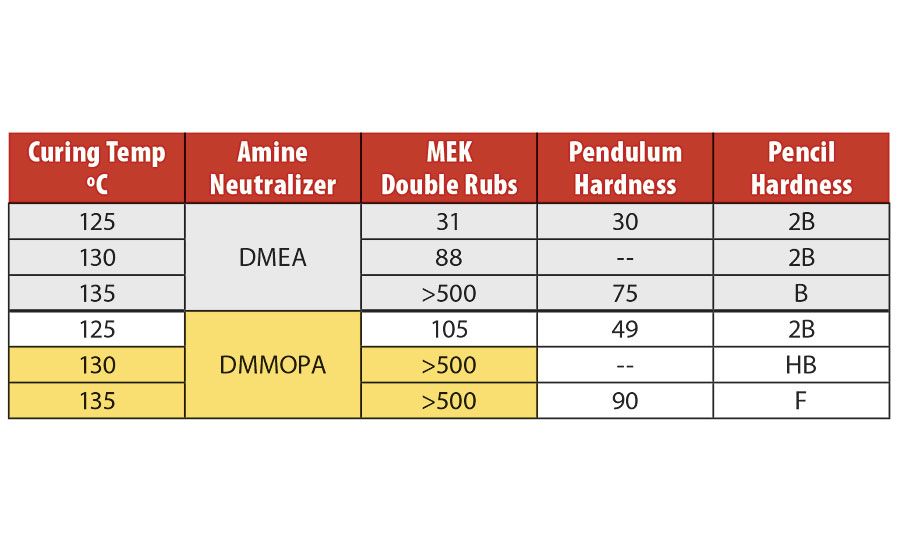
TABLE 9 » Polyol MF curing Case Study 5.
So far, these study results demonstrate that DMMOPA offers better curing properties against existing amine neutralizers in the polyol melamine formaldehyde curing chemistry and showed the potential for sub-100 °C curing for plastic substrates. The enhanced performance of DMMOPA could be related to its low boiling point, azeotrope capability, medium base strength and lack of active hydrogen. These properties allow DMMOPA to easily dissociate from the acid functionalities of the polymer and diffuse and volatilize out of the coating film to facilitate the acid-catalyzed curing reactions.
Table 10 compares the physical properties of DMEA, DMMOPA and other typical amine neutralizers used in the coatings industry. Other positive properties of DMMOPA observed in our study include full miscibility with water and resistance to thermal yellowing. Figure 1 is the residual of the respective salt formed between adipic acid and DMMOPA, DMEA and TEA and baked at 120 °C for 30 min. In the case of DMMOPA, the residual DMMOPA ammonium salt is colorless, while both DMEA and TEA ammonium salt showed yellowness. This result showed that DMMOPA has surprisingly excellent thermal yellowing resistance.
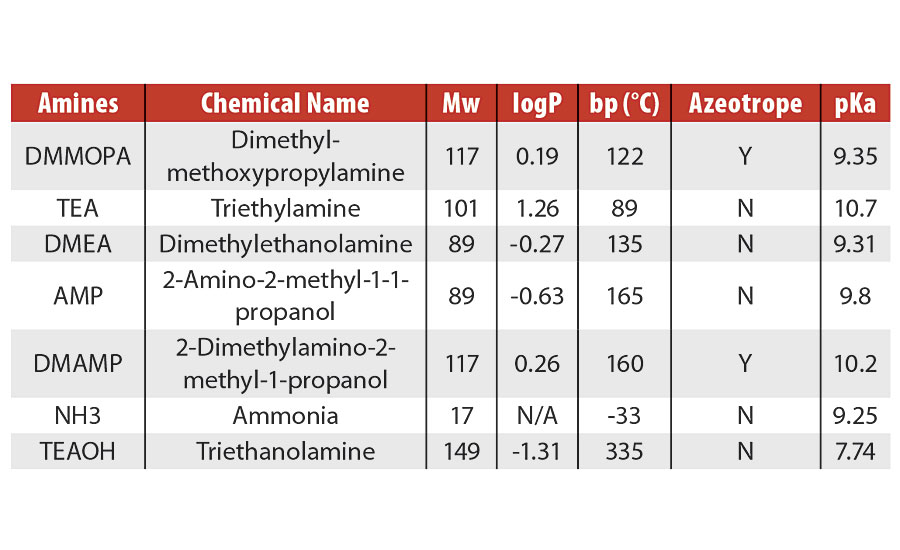
TABLE 10 » Physical properties of typical amine neutralizers used in the waterborne coatings industry.
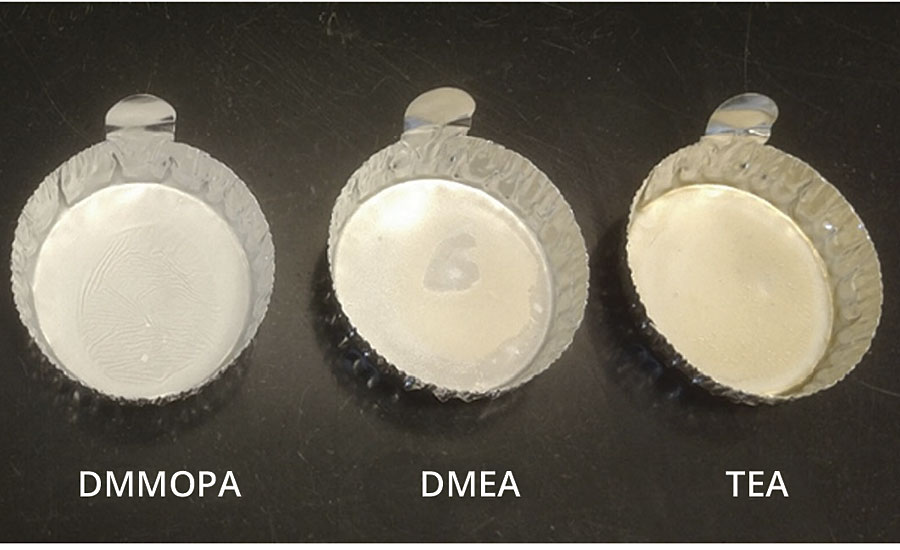
FIGURE 1 » Adipic acid-amine salt baked at 120 ºC for 30 min.
Latex Paint Applications
In industrial and exterior architectural coating applications, one key requirement is early water resistance. In waterborne coatings neutralized by amines, the amines exist as free molecules and bound organic ammonium salt on polymer or pigment surface. During the drying stage, both cases will soften the polymer and increase the coating’s water affinity. Amines with a high boiling point, high pKa and strong binding to the nonvolatile acidic species in the paint formula are retained in the paint film for an unnecessarily long period of time. This results in issues with early water resistance and blocking. This is not acceptable for outdoor and industrial applications.
Ammonia has been used extensively in these types of applications due to its gaseous and highly volatile nature, which gives the paint excellent early property development. However, paints neutralized with ammonia have a strong odor, as well as less-desirable performance with regards to aging pH and viscosity stability. On the other hand, typical organic amine neutralizers, while providing paints with many multifunctional benefits, have a high boiling point and tend to remain in the paint film for longer periods, causing water sensitivity issues. These neutralizers find little use in exterior and industrial applications.
Because of its balanced physical properties discussed earlier, DMMOPA may provide exterior or industrial latex paints with the positive attributes of a multifunctional organic amine and the excellent early water resistance of ammonia. In the study below, DMMOPA was evaluated in a styrene acrylic latex industrial coating formula with ammonia and DMAMP as the controls. DMAMP is an amine neutralizer known for its azeotrope capability with H2O at 98 °C and higher volatility compared with other typical organic amine neutralizers and found applications in certain industrial and exterior architecture coatings requiring decent early water resistance.
Table 11 is the water-soaking test of the paints neutralized with three amine neutralizers, coated on glass panels at 3 mil dry thickness and dried at room temperature (RT) for 17 hrs. After soaking in water for 2 hrs, DMMOPA shows comparable excellent early water resistance with ammonia, while DMAMP-80 started to show blistering and gloss reduction. With an even longer 4-hr water soaking, DMMOPA- and ammonia-neutralized paints maintained the film surface properties very well, and DMAMP showed more severe blistering and gloss loss issues. This result showed DMMOPA could indeed leave the paint film within the time window critical to industrial and exterior applications, resulting in an excellent water resistance.
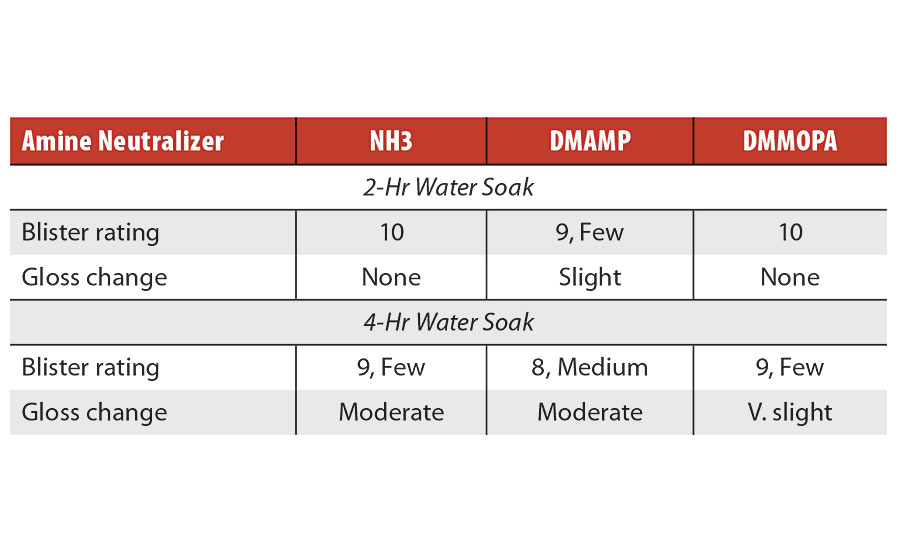
TABLE 11 » Water resistance of paints neutralized with various amine neutralizers.
Figure 2 is the cross-hatch adhesion test results of the three paints coated onto cold rolled steel (CRS) panel and dried for 7 days. With only 1-day dry, none of the amine-neutralized paints showed any adhesion to CRS and all were rated as 0B. After 7 days dry as shown in Figure 2, DMAMP-neutralized paint showed improved but still poor adhesion rated as 0B, while DMMOPA and ammonia showed much improved and comparable adhesion rated as 3B.
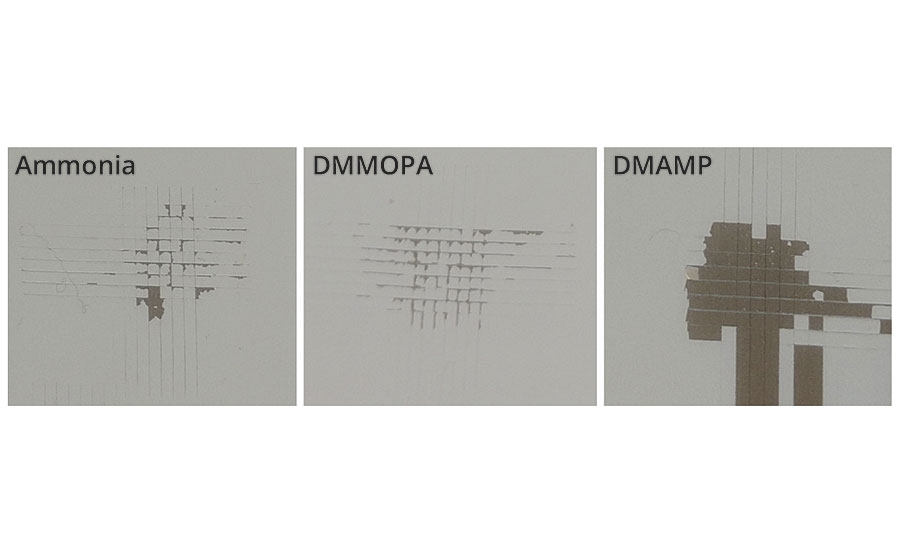
FIGURE 2 » Cross-hatch adhesion of paints neutralized with various amine neutralizers and dried for 7 days.
Figure 3 is the 20° gloss of the paints coated onto CRS panel. DMMOPA- and DMAMP-neutralized paint showed apparently better gloss development than ammonia. This is indicative of a better film forming likely due to the pigment co-dispersant effect and the slow evaporation nature of organic amines, which could result in a more ordering packing of particles during the paint drying stage.
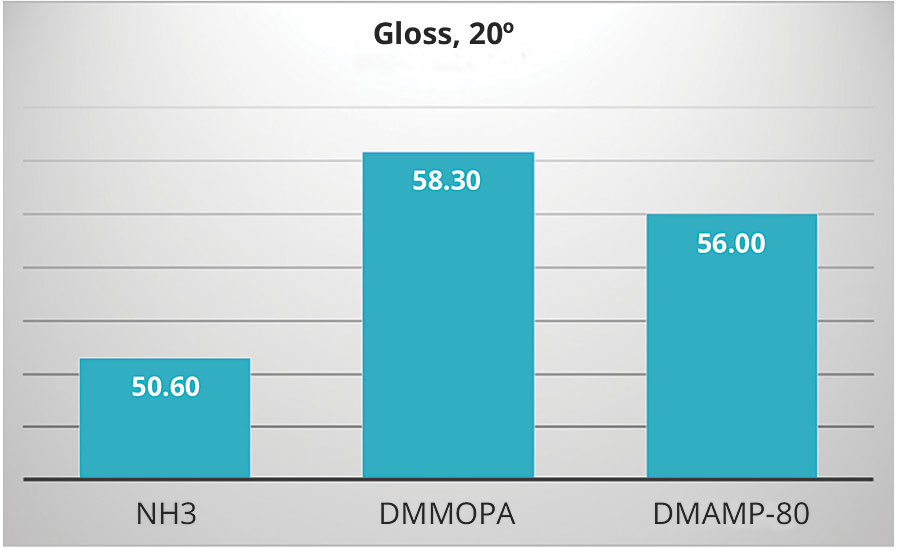
FIGURE 3 » 20º gloss of paints neutralized with various amine neutralizers.
Figure 4 is the TiO2 pigment dispersion study of TiO2 dispersed at 70% concentration with a polyacrylate dispersant and neutralized with ammonia, DMMOPA or without neutralization. The much lower dispersion viscosity of DMMOPA displayed in Figure 4 clearly indicated a significant benefit in using DMMOPA over ammonia as the neutralizer to better disperse TiO2 particles. Thus, DMMOPA could function as a useful co-dispersant, providing a beneficial synergistic effect with primary dispersants. Depending on the formulation, this may allow for formulation optimization, which could lead to a reduction of the primary dispersant, in turn reducing formulation costs while improving overall performance. The better film forming properties and balanced volatility of DMMOPA are also reflected in scrub resistance and corrosion resistance discussed below.

FIGURE 4 » Dispersant demand vs. viscosity of TiO2 neutralized with various amine neutralizers.
Figure 5 is the scrub resistance of the paints neutralized with the three amines and dried for 7 days. While DMAMP and ammonia have comparable scrub resistance, DMMOPA outperformed both DMAMP and ammonia by more than 40%.
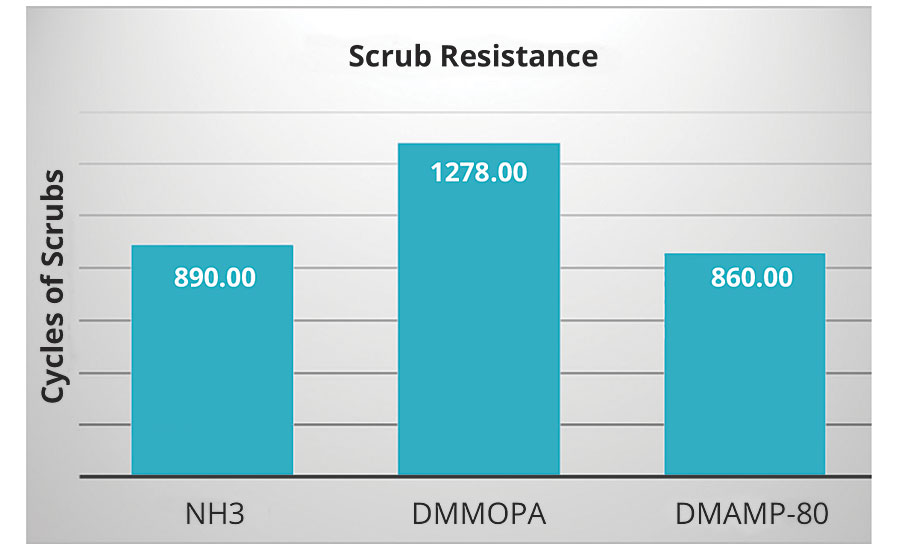
FIGURE 5 » Scrub resistance of paints neutralized with various amine neutralizers.
For waterborne industrial coatings, corrosion resistance is a critical performance parameter. While there are several reports studying the effect of resin, pigment dispersant, pigments and thickeners on corrosion resistance, there is no open literature work, to our knowledge, studying the effect of amine neutralizers on the corrosion resistance of a waterborne coating. In this study, we compared the preliminary corrosion resistance of paints neutralized with the three amines. For this quick screening corrosion study (Figure 6), the paints were coated onto a CRS at a thickness of 1.2 mil and dried at RT for 7 days, and then scribed and soaked in 5% salt water for 72 hrs. For both ammonia- and DMAMP-neutralized paints, corrosion propagation in the scribed area is much more severe than DMMOPA-neutralized paint.
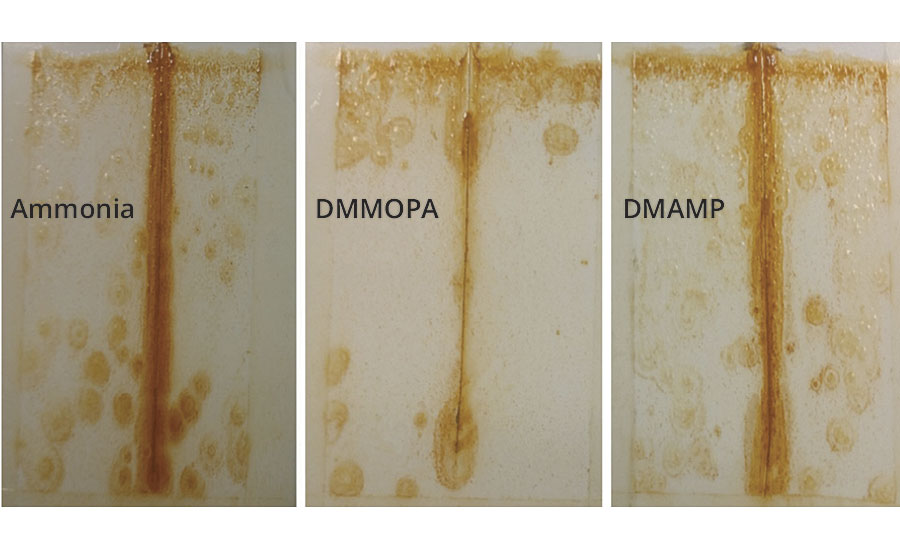
FIGURE 6 » Corrosion resistance of paints neutralized with various amine neutralizers.
It was also clear in areas of the DMMOPA-neutralized paint that were not scribed, the paint was more impermeable to saltwater penetration than ammonia- and DMAMP-neutralized paints, which resulted in fewer corrosion spots than both the ammonia and DMAMP systems. These results indicated that DMMOPA as a neutralizer could improve corrosion resistance of a latex paint, possibly due to the formation of a more cohesive film resulting from better pigment co-dispersing capability and lower volatility than ammonia. On the other hand, the higher volatility of DMMOPA compared to other less-fugitive organic amine neutralizers resulted in a much lower amount of residual amines (free or ammonium carboxylate) in the dried film and better dry-film properties.
It is widely accepted that the limiting factors for a coating’s corrosion resistance are barrier properties, adhesion properties and impedance. Although which of these is the main contributing factor is still a topic of debate, the most recent work by Engineered Polymer Solutions2 and Specialty Polymers Inc.3 seem to point that impedance is the dominating factor for corrosion resistance. While the study of the effect of DMMOPA on these three factors extends beyond the scope of this discussion, it appears that with its balanced physical properties, DMMOPA has the potential to positively contribute to the corrosion resistance of a latex paint.
Conclusions
This study has shown that DMMOPA has a unique combination of balanced physical properties such as water solubility, moderate pKa, low boiling point, azeotrope with water, nonreactive and yellowing resistance. These physical properties offered DMMOPA-neutralized paints a multitude of performance advantages in a variety of waterborne paint systems as discussed in this article, such as enhanced hardness and solvent resistance in polyol-MF baking coatings, as well as better gloss, scrub resistance, water resistance and corrosion resistance in latex paints. The results also demonstrated that amine neutralizers, although used in small quantities compared with other formulation ingredients, could have a major positive impact on the performance of the coatings if proper amine is selected and the overall paint formulation is optimized. n
Acknowledgements
Dick Henderson, Senior Customer Applications Specialist; John Quinn, Applications Technologist, ANGUS Chemical Company.
References
1 Wicks, Jr., Z.W.; Jones, F.N.; Pappas, S.P. Organic Coatings: Science and Technology, Volume 1: Film Formation, Components, and Appearance. John Wiley & Sons, N.Y., 1992.
2 Bulick, A.S.; LeFever, C.R.; Frazee, G.R.; Jin, K.; Mellott, M.L. The Impact of Film Properties on Corrosion Resistance in Waterborne Acrylics and Next-Generation Low-VOC Resin Development. Waterborne Symposium 2016.
3 Monaghan, G. Metal Adhesion and Corrosion Resistance of Coatings. Specialty Polymers Inc., Coatings Trends and Technologies 2017.
Report Abusive Comment