Colloidal MCC: An Effective Tool to Stabilize Pigment Dispersions

georgeclerk, iStock / Getty Images Plus, via Getty Images
Colloidal microcrystalline cellulose (colloidal MCC, offered by IFF with trade name Lattice® NTC) is an innovative line of co-processed microcrystalline cellulose and sodium carboxyl methylcellulose using IFF proprietary technology. Colloidal MCC forms a three-dimensional network when activated into water under high shear, entrapping solid particles and oil droplets. One of the key properties of colloidal MCC is its ability to stabilize water-based formulations without significant increase in formulation viscosity. Similar food-grade products sold under the trade name Avicel® have been used widely in food applications and proven to have excellent particle suspension and emulsion-stabilization properties.
The research1 at North Dakota State University (NDSU) showed that colloidal MCC was ineffective as a secondary thickener in increasing the viscosity of latex coatings. However, the addition of a small amount of colloidal MCC (0.1-0.2% wt) to paints having optimized Stormer viscosities can eliminate phase separation completely without affecting flow or leveling properties. It was also found that all-acrylic latex coatings thickened with colloidal MCC gave higher scrub resistance than those thickened with HASE.
We demonstrated in the previous publication2 that colloidal MCC is an excellent stabilizer and dispersing aid in waterborne acrylic gloss paint systems, due to its superior suspending functionality and emulsion stabilization properties. As a stabilizer and secondary rheology modifier, colloidal MCC provided minimum viscosity to waterborne coating systems at low use level while significantly improving in-can shelf stability and color-tinting ability. All these without significant viscosity changes. The ability to suspend solid materials at low viscosity also makes colloidal MCC especially suitable in viscosity-sensitive systems such as stain applications.
Lattice NTC cellulosic polymers originate from wood and have a natural content of around 91% using the ISO16128 method. Lattice NTC-61 was tested and confirmed to be readily biodegradable using the OECD301F method, and other NTC products are expecting similar biodegradability results due to similar compositions. This article reviews our recent research on stabilizing concentrated TiO2 slurry using the new colloidal MCCs.
Colloidal MCC Stabilizes Concentrated Tio2 Dispersions
The concentrated TiO2 dispersion was obtained from a US-based supplier. The product has a 76.5% TiO2 content. For this test, we prepared a 3% Lattice NTC-90 stocking dispersion. The proper amount was dispersed into DI water under low shear, followed by high-shear mixing to ensure full activation to form the stock dispersion. The NTC-90 stock dispersion was then added into the concentrated TiO2 dispersion using two target use levels of 0.15% and 0.3% of NTC-90. For the control (no Lattice NTC-90), DI water was added to ensure that all dispersions have equal TiO2 concentrations.
The Brookfield viscosity increased when using the new colloidal MCC, although the viscosity of the dispersion was still very low. It reached ~200 cps at 0.3% use level (Figure 1). This is slightly different to the NDSU results. In the NDSU studies2 the system was a full paint formulation and was optimized with other rheology modifiers to a much higher viscosity. In that finished paint product, the use of colloidal MCC did not increase the formulation viscosity.
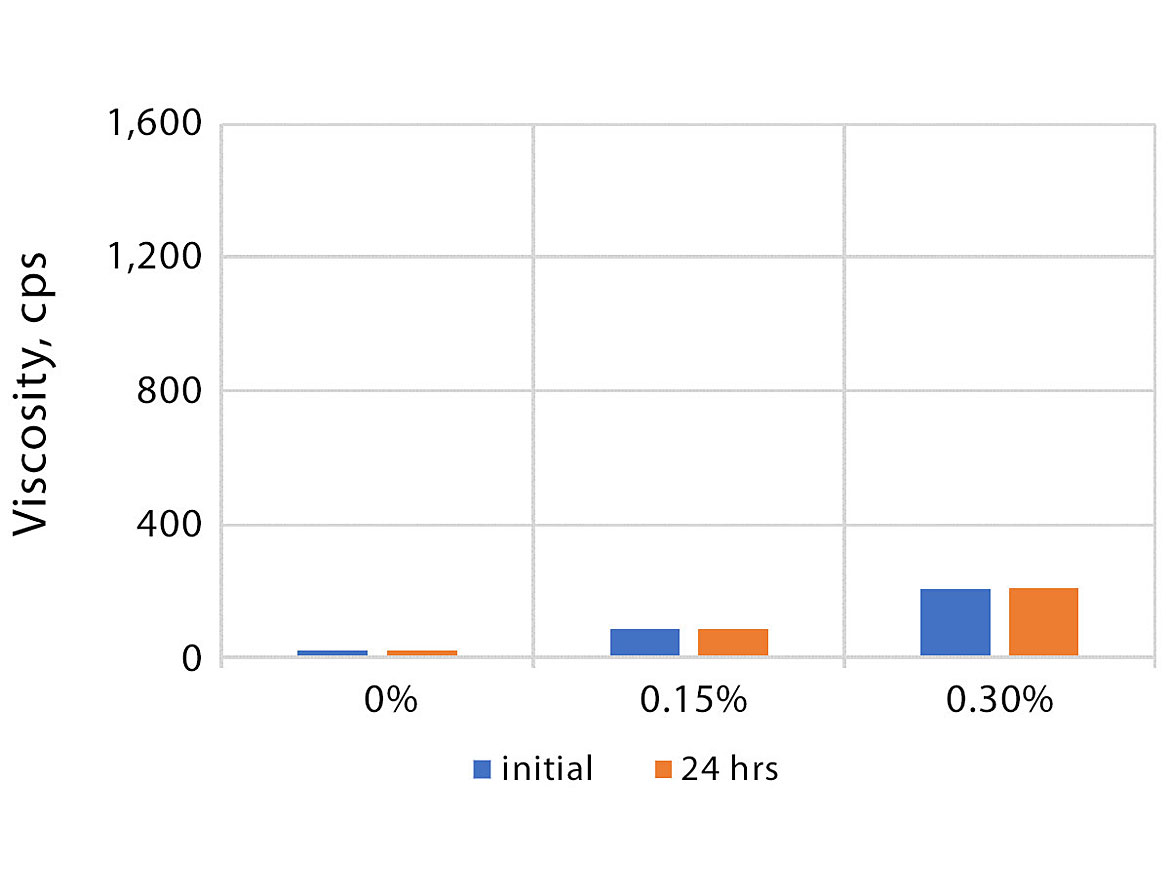
The TiO2 dispersion stability was analyzed using a TurbiscanLab Expert from Formulaction, a technology used to analyze destabilization mechanisms in concentrated dispersed media. It offers accelerated aging tests. The three TiO2 dispersion samples were tested at room temperature. The global TSI (Turbiscan Stability Index) was obtained over 7 days to compare the long-term stability of the dispersions. The higher the global TSI, the less stable the product is. Figure 2 shows significant improvement when Lattice NTC-90 use level increased. The higher the use level, the more stable the dispersion.
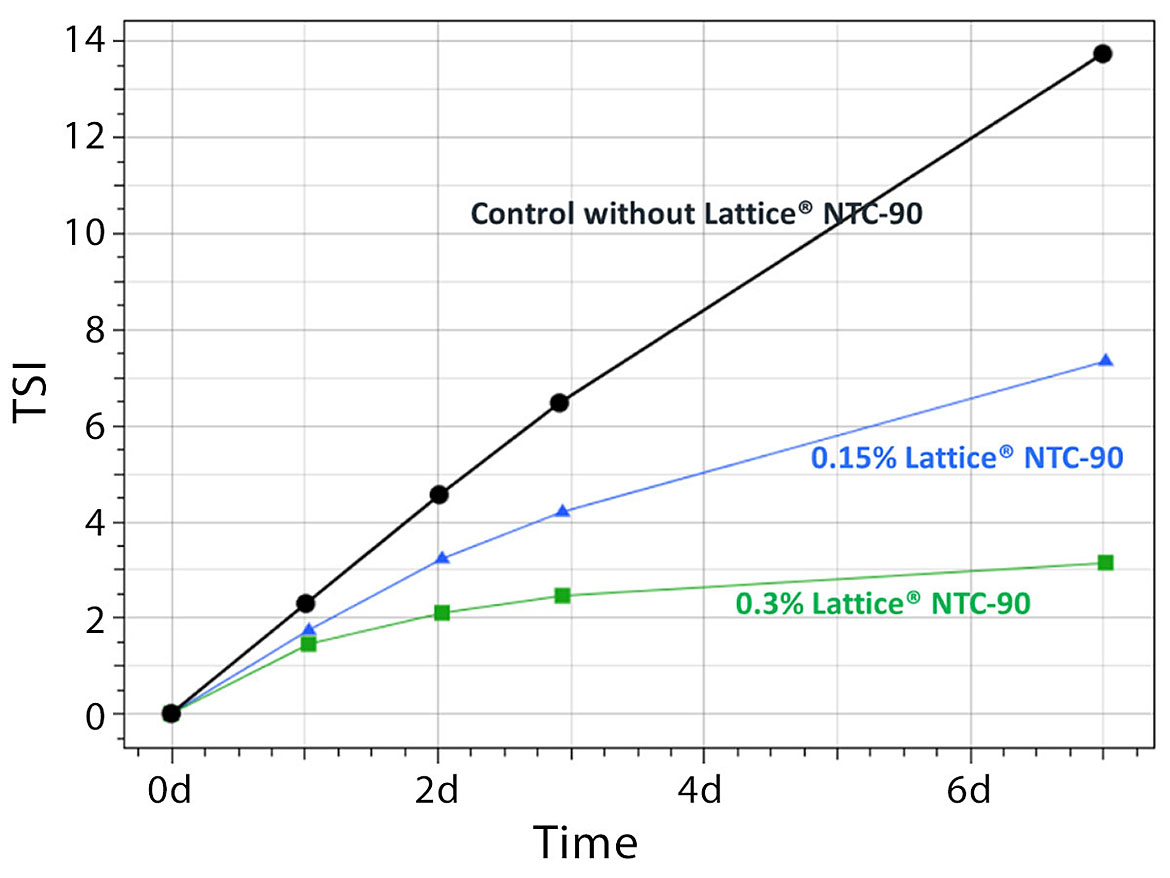
Similar results were found with visual observation in accelerated oven stability testing. In this test, the three samples were put in an oven at 54 °C for two weeks. Dispersions were then taken out for observation. Figure 3 shows flipped containers for visual observation. The sample without NTC-90 showed agglomeration and caked at the bottom of the container (TiO2 particles remained at the bottom of the container). Both samples with 0.15% and 0.3% NTC-90 remained stable, TiO2 particles were well suspended.
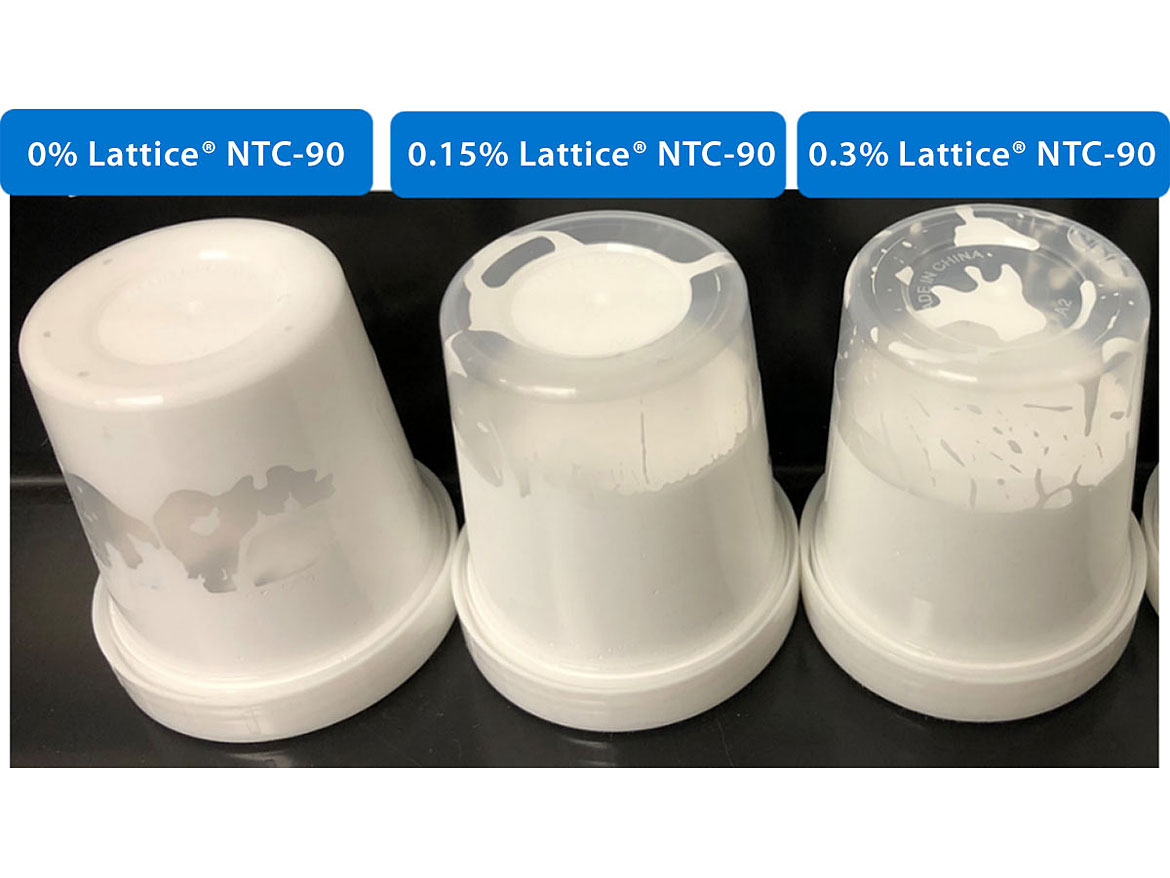
When sampling from the bottom of each container, the dispersion without Lattice NTC-90 showed severe hard caking (Figure 4). The other two samples were still homogeneous and fluid.
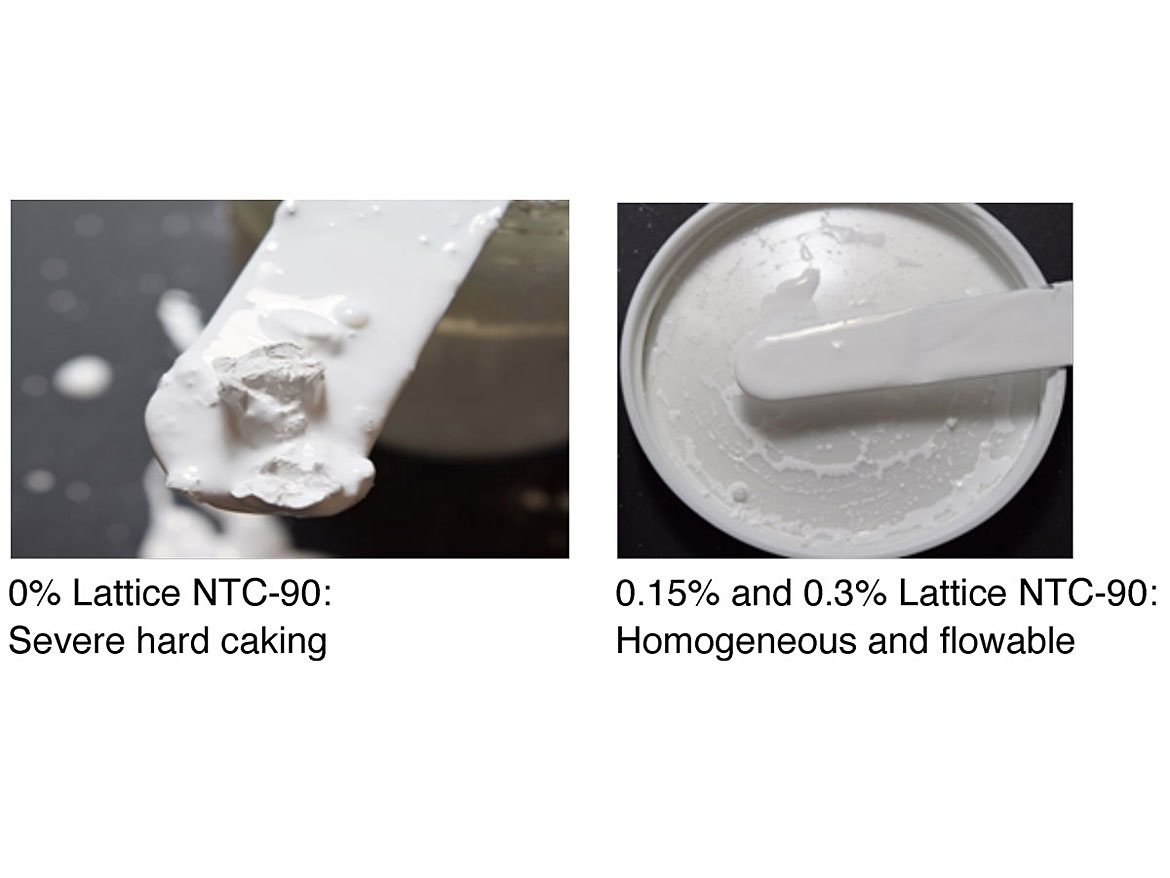
The results above showed that small amount of colloidal MCC can stabilize TiO2 particles with minimal viscosity increase.
Activation of Colloidal MCC
Colloidal MCC activation requires high shear. The higher the shear, the easier it is to reach complete activation. It is recommended to disperse Lattice NTC colloidal MCC into water first, then apply high shear until full activation is obtained. Depending on the grade chosen, the activation can be done by using a benchtop mixer, a Cowles disperser, an inline high-shear mixer or a homogenizer. The activation status can be confirmed using an optical microscope with polarized light. At 100x magnification, the fully activated colloidal MCC dispersion will show many luminous particles, well separated from one another (Figure 5b), while the undispersed state will show agglomerated particles that appeared as clusters/aggregates (Figure 5a). When fully activated, insoluble microcrystalline cellulose particles form a three-dimensional network with particles well separated from one another and kept apart by soluble carboxymethyl cellulose. This 3D network prevents particles from settling or agglomerating.
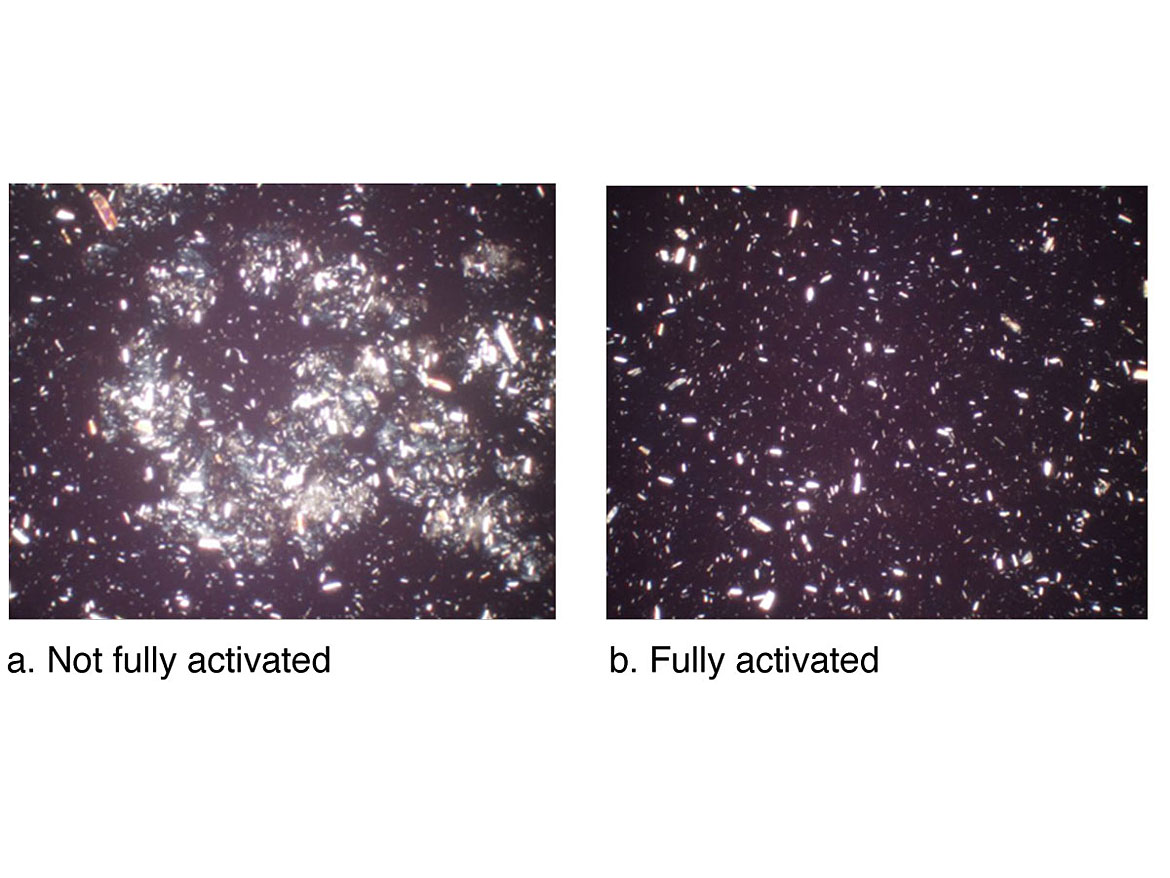
Proper activation is key for colloidal MCC functionality. Colloidal MCC will partially work at best (in some applications), or not at all, if it is not fully activated, . This can be observed with rheological measurements. Figure 6 shows rheology profiles of Lattice NTC-80 dispersion samples, activated using different equipment. High use level (1.2 wt%) was used in the study in order to show the rheology effect, since this is not in a formulation. The sample activated using an inline high-shear mixer had increased viscosity in the low shear rate region with clear thixotropic effect. The sample made with a low-shear benchtop mixer had very low viscosity with little or no thixotropic behavior. In this case, no network was formed, and the dispersion will not provide the required functionality.
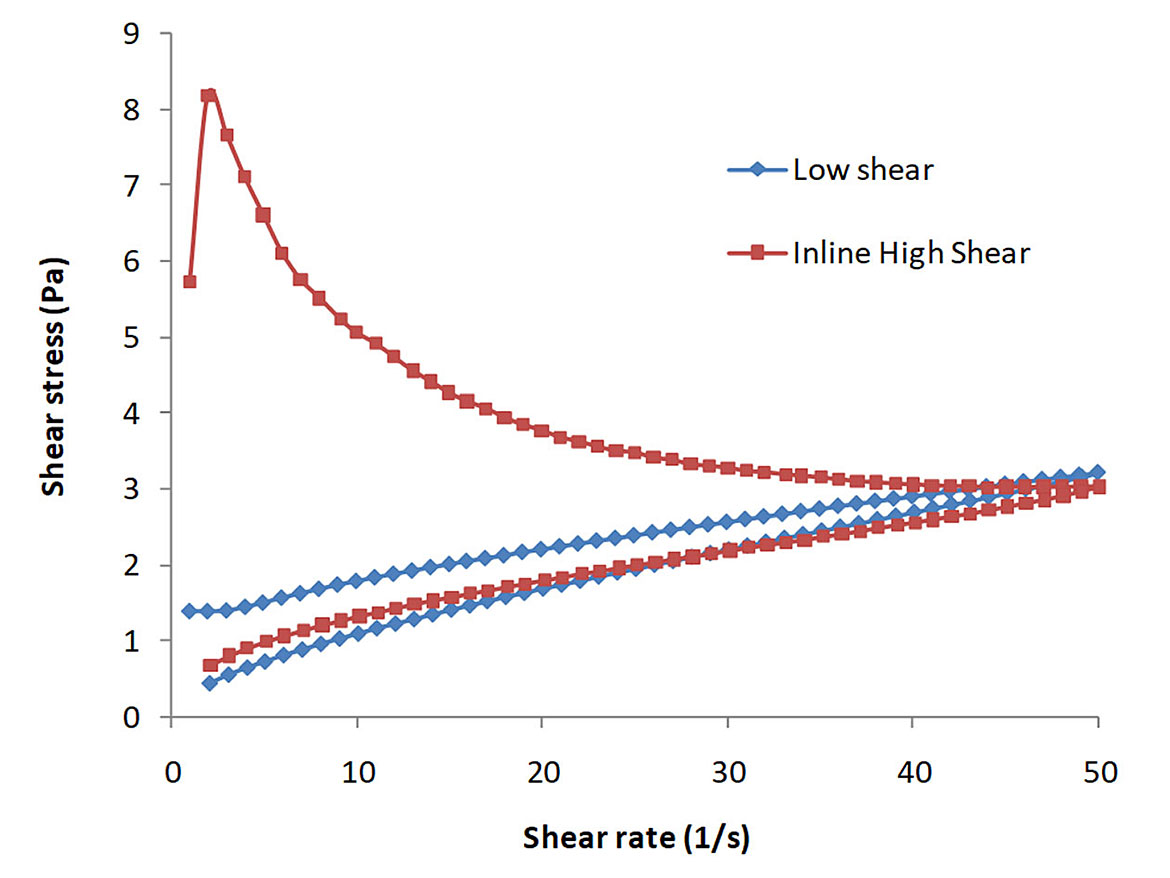
Summary
Lattice NTC colloidal MCC products are unique functional and biodegradable additives that can suspend solid particles and/or stabilize emulsions in various waterborne applications. They were reported to be able to solve issues such as color floating/color sinking, syneresis and settling in coating formulations without significant impact on formulation viscosity. They have shown to improve sagging and scrub resistance as well.
This work demonstrated that a small amount of NTC-90 (0.15%-0.3%) can be used to significantly improve the stability of concentrated TiO2 dispersions and minimize hard caking. This is a very interesting functionality since more homogeneously dispersed TiO2 particles can potentially reduce the TiO2 use level, reduce waste caused by hard caking, and save formulation cost.
The activation of colloidal MCC is key to obtain desirable functional benefits.
References
1 Ma, Z.; Lundberc, D.J.; Roberts, S.; Glass, J.E. Phase Behaviors and Film Properties of Dispersions and Coatings Containing Associative and Conventional Thickeners, Journal of Applied Polymer Science, 49(9),1509-1527 (1993).
2 Ayling,G.; Lynch, G.; Yang, H.S. Colloidal Microcrystalline Cellulose”, PCI Magazine, January 1, 2008.
Looking for a reprint of this article?
From high-res PDFs to custom plaques, order your copy today!