Epoxy Curing Agents

Davizro / iStock / Getty Images Plus, via Getty Images.
Continuing with the focus on resins, I will cover epoxy curing agents in this month’s column. When it comes to great adhesion, chemical resistance, and corrosion resistance, an epoxy is hard to beat. That is why it has been the mainstay of industrial primers for decades. An epoxy system is the thermoset reaction of an epoxide ring and a proton donor, most commonly from an amine or amide hardener. However, there are different epoxy curing agents, and each one provides different properties that can be suited for a wide variety of end-use applications. Epoxy resins can also react with other chemistries at high temperatures, such as carboxyl groups, but we will limit this article to common ambient cure systems. For this article, the epoxy part of the two-component system will be known as the resin, and the amine or amide curing agent will be known as the hardener.
Epoxy resins tend to have limited compatibility with some epoxy curing agents, so an induction time is needed. The induction time is the time between the mixing of the resin and hardener, and the application of the coating. This allows the chemical reaction between resin and curing agent to start. As the epoxy and curing agent reaction takes place, the compatibility of the system increases, and there will be fewer coating defects and better final film properties. If proper mixing does not occur, it is possible that the amine or amide component may rise to the surface of the applied coating, creating an uncured layer at the surface known as surface “blush,” which appears as a hazy finish.
Epoxy curing agents are often modified to improve certain properties. The modification may be to partially react the curing agent, to reduce induction time, and increase compatibility. Common additives are nonylphenol (accelerator and diluent) and benzyl alcohol (diluent and plasticizer). With increasing environmental regulations, bisphenol A, nonylphenol, and benzyl alcohol-free epoxy curing agents are becoming more common. It is also common to blend curing agents to adjust properties. For example, a small amount of a polyamine or polymercaptan added to a polyamide can reduce cure time.
Due to the health and safety concerns of amine curing agents, they are not recommended for the general public, and amide curing agents are the norm for the DIY market. Curing agents are generally used for high-solids coatings, masonry coatings, grouts, floor coatings, corrosion-resistant coatings, primers, patch compounds, sealants, general adhesives, and electrical encapsulation.
Due to the health and safety concerns of amine curing agents, they are not recommended for the general public, and amide curing agents are the norm for the DIY market. Curing agents are generally used for high-solids coatings, masonry coatings, grouts, floor coatings, corrosion-resistant coatings, primers, patch compounds, sealants, general adhesives, and electrical encapsulation.
The normal stoichiometry of epoxy systems is a 1:1 ratio of epoxy group to hardener group. Some systems allow for changing properties by moving off this ratio (amidoamine and amide), other hardeners have a dramatic drop off in properties when the ratio moves slightly off 1:1 (amine, and to a lesser extent mercaptans). The curing agent’s functionality also greatly influences crosslink ratio and final properties. They require a minimum functionality of 2 to allow polymerization. Therefore, while we refer to curing agents like amine or amide, they are really polyamine or polyamide.
Polyamide curing agents give longer potlife, slower reaction, better flexibility, and excellent corrosion resistance. They tend to be softer than other epoxy curing agents and can have very sluggish cure at lower temperatures. Stoichiometry is not critical, and under/over indexing the system is often used to modify final properties. Polyamides tend to have higher viscosities and are difficult to use in 100%-solids systems. They also tend to have low toxicity compared to other curing agents. Polyamides are not completely compatible with most epoxy resins, so an induction time is critical.
Polyamine curing agents have a shorter pot life and quick reaction speeds. They are harder and less flexible than polyamides. They also have lower corrosion resistance, and stoichiometry is critical. Polyamines have the lowest viscosity of the common epoxy curing agents and can be used at low temperatures due to their increased reactivity. There are many different types of amine curing agents, including aromatic, aliphatic, cycloaliphatic, Mannich bases, etc. Depending on the agent chemistry, they may have blushing issues, so use may be limited under high humidity/wet conditions. While they have lower corrosion resistance than other epoxy curing chemistries, they are still excellent compared to most non-epoxy systems. They can vary from simple molecules like DETA (diethylenetriamine) to complex polymeric materials. Epoxy-amine systems develop excellent chemical resistance compared to most other two-component epoxy systems.
Polyamidoamine curing agents fall somewhere between amine and amide curing agents in most areas, and have balanced properties. They usually have both amine and amide groups that are not a blend of an amine/amide.
Polymercaptans (sulfhydryl -SH functional) are known for very rapid and low-temperature cure, great bond strength, low toxicity, and little or no induction time. Polymercaptans are commonly seen in five-minute-type epoxy systems for adhesives, and are also used in coatings. They can be used as accelerators with other epoxy curing agents. They also provide increased flexibility in rigid epoxy systems.
With the move to coatings systems with a better environmental profile, epoxy systems are at the forefront. They are capable of being 100% solids, so not only is there no solvent released, they require less energy to transport the same amount of polymer. The high performance and long service life of the system means less recoating, which lowers their environmental footprint. The move to bio-based components also enhances their eco friendliness.
Table 1 briefly illustrates the differences between different epoxy curing agents.
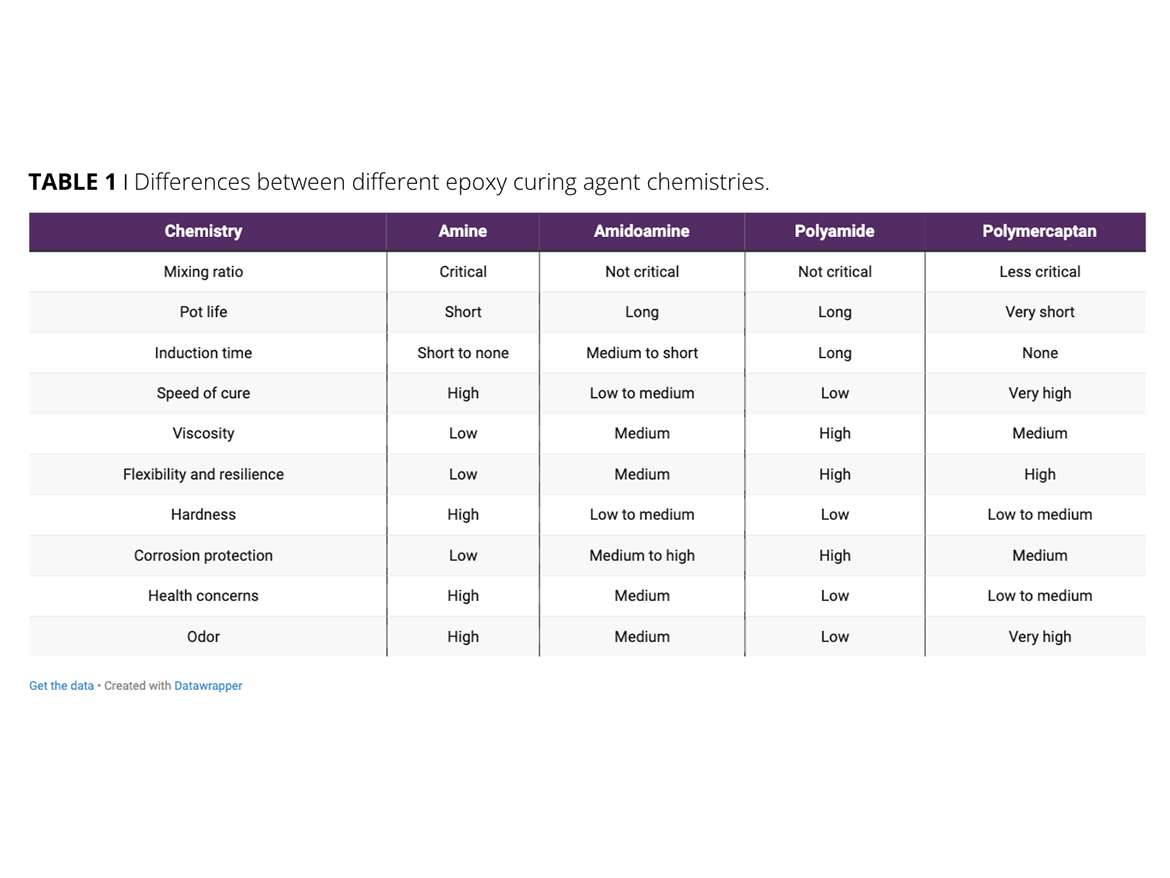
All information contained herein is provided "as is" without any warranties, express or implied, and under no circumstances shall the author or Indorama be liable for any damages of any nature whatsoever resulting from the use or reliance upon such information. Nothing contained in this publication should be construed as a license under any intellectual property right of any entity, or as a suggestion, recommendation, or authorization to take any action that would infringe any patent. The term "Indorama" is used herein for convenience only, and refers to Indorama Ventures Oxides LLC, its direct and indirect affiliates, and their employees, officers, and directors.
Looking for a reprint of this article?
From high-res PDFs to custom plaques, order your copy today!