Polyurethane Polymers, Part 2

Hamster3d, Vetta, via Getty Images.
In last month’s column we covered urethane chemistry. This month we will continue with urethanes and look at 100%-solids systems. Since these systems can be based on aromatic or aliphatic isocyanates, we will discuss aromatic systems. The main aromatic isocyanates are methylene diphenyl diisocyanate (MDI) and toluene diisocyanate (TDI), and their structures are shown in Figure 1.
So why would we want to make 100%-active aromatic urethane systems? There are numerous reasons. They have very good physical- and chemical-resistance properties. They contain nearly zero volatile organic compounds (VOCs) and they are low viscosity (well under 1,000 centipoise). Since the urethane system is 100% solids, you can build thick coatings (up to inches thick), with little shrinkage, something that cannot be done with solvent- or water-containing systems. This makes them very useful in self-leveling floor coatings and elastomeric roof coatings, amongst other applications.
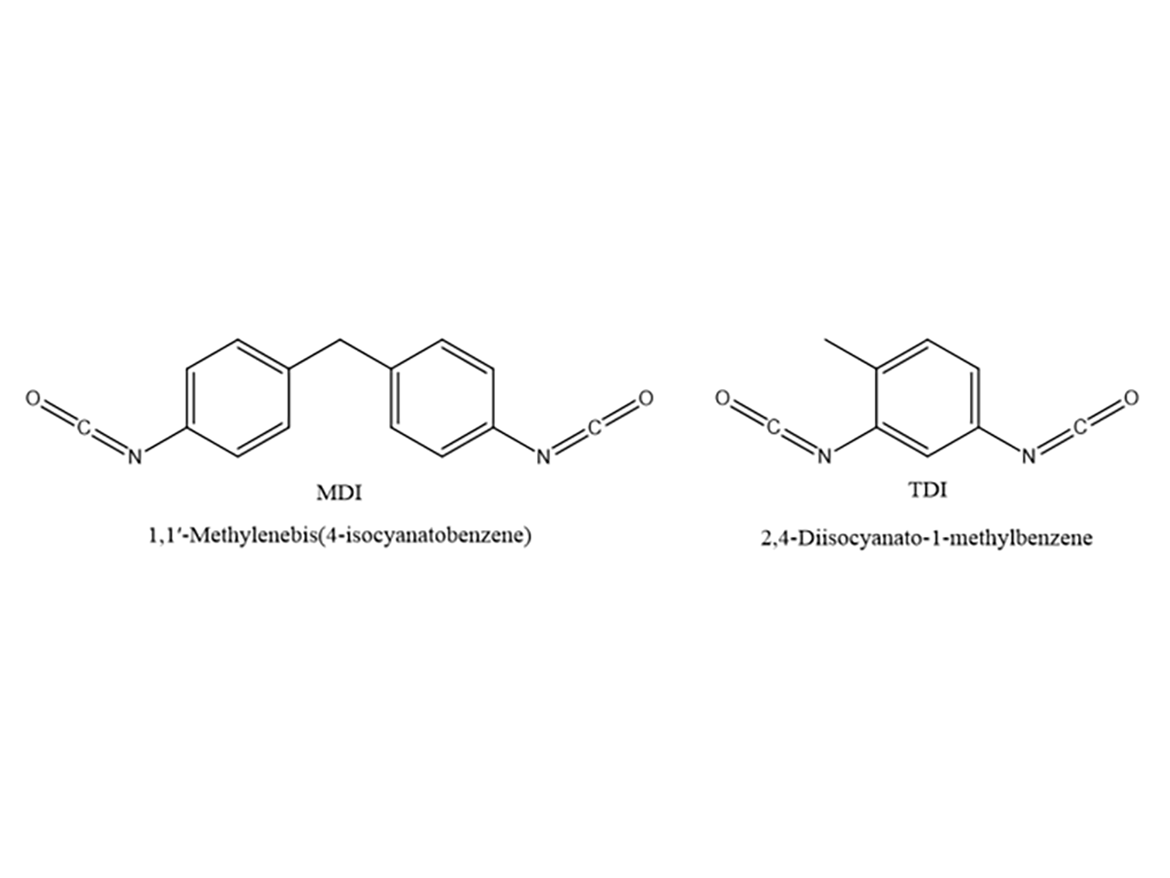
Due to environmental, health, and safety concerns, TDI cannot be used in two-component field-applied coatings, and is generally reserved for foam applications. MDI is a very versatile isocyanate.
MDI is unique because the monomeric and polymeric forms have extremely low vapor pressures, roughly 1.0 x 10-5 mmHg, at room temperature. So, unlike aliphatic isocyanates, which are only used in coatings in their polymeric form, MDI can be used in its monomeric or polymeric form (Figures 2 and 3).
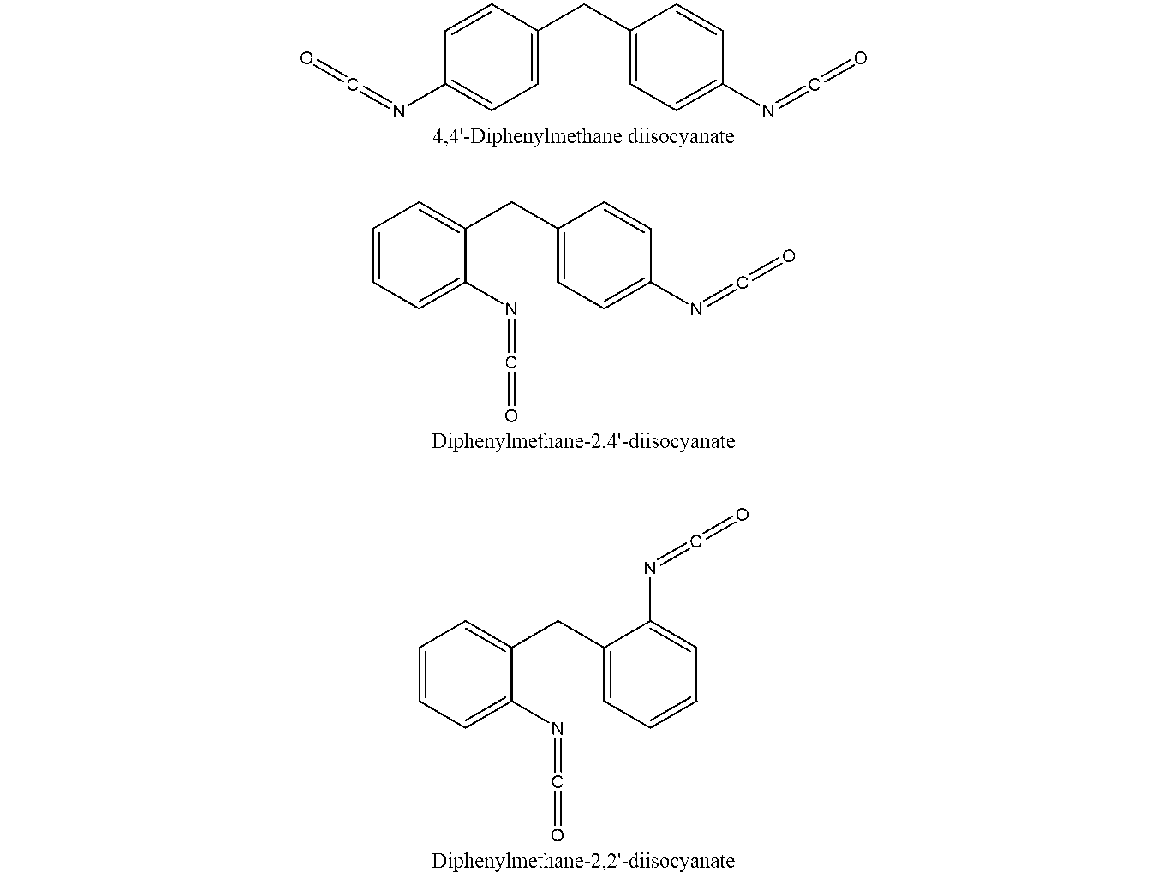
Monomeric forms are one of three isomer possibilities, 2,4; 4,4; and 2,2, which shows the location of the isocyanates (NCO groups) on the two aromatic rings (see Figure 2). The rough production breakdown of the three forms is: 75% of the 4-4 isomer, 20% of the 2-4 isomer, and <5% of the 2,2 isomer, however the manufacturing process can be adjusted to favor the yield of the 2,4 isomer. 4,4 MDI is a solid at room temperature and rapidly dimerizes. The dimer form is insoluble in MDI and will crystalize and settle out at very-low levels, well below 1%. This makes pure 4,4 MDI generally unusable in coatings, however it can be used to make polyurethane dispersions or pre-polymers by reacting them with diols.
To help make 4,4 MDI more stable, 2,4 MDI, polymeric pre-polymers or other modified MDIs are added. In fact, most commercial 2,4 MDI products are roughly 50:50 blends of 2,4 and 4,4 isomers. The most common MDI is the polymeric 200 centipoise version. This is about 60% polymeric and 40% monomeric (mostly 4,4 MDI). The increased functionality of the polymeric (roughly 3-7 functional), helps increase the crosslink density of the urethane systems.
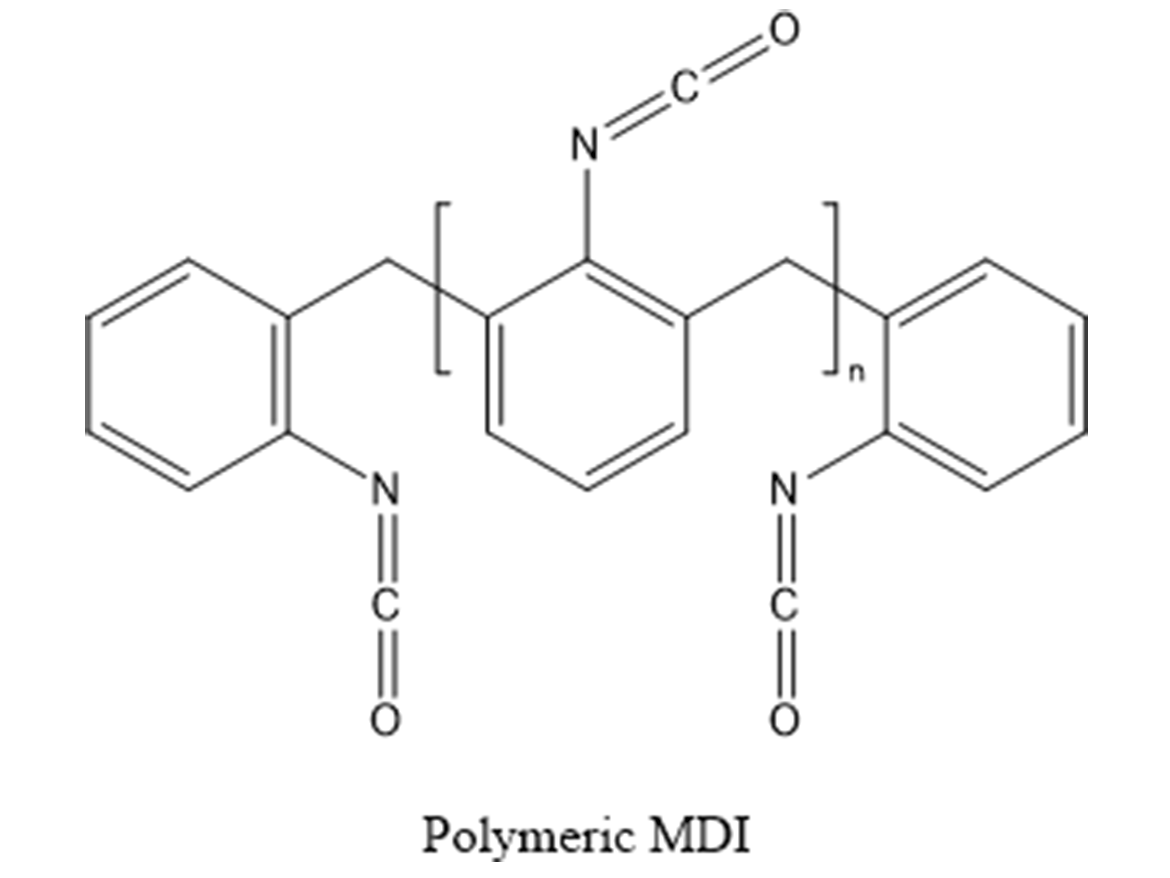
On the polyol side of low-viscosity two-component aromatic-urethane systems, the most common polyols are polypropylene oxide or castor oil. Both are economical and low viscosity. Polyesters and acrylics will normally have too high a viscosity to be used in 100%-solids systems. Polypropylene oxide diols are used when high elongation is required. Typical molecular weights are 400-4,000 Daltons for diols. Triols are made by pro-proxylating either glycerin (Figure 4) or trimethylol propane. Typical molecular weights are 400-6,000 Daltons, but for most coatings molecular weights are 400-3,000 Daltons. The higher molecular weights are predominately used in making flexible foam.
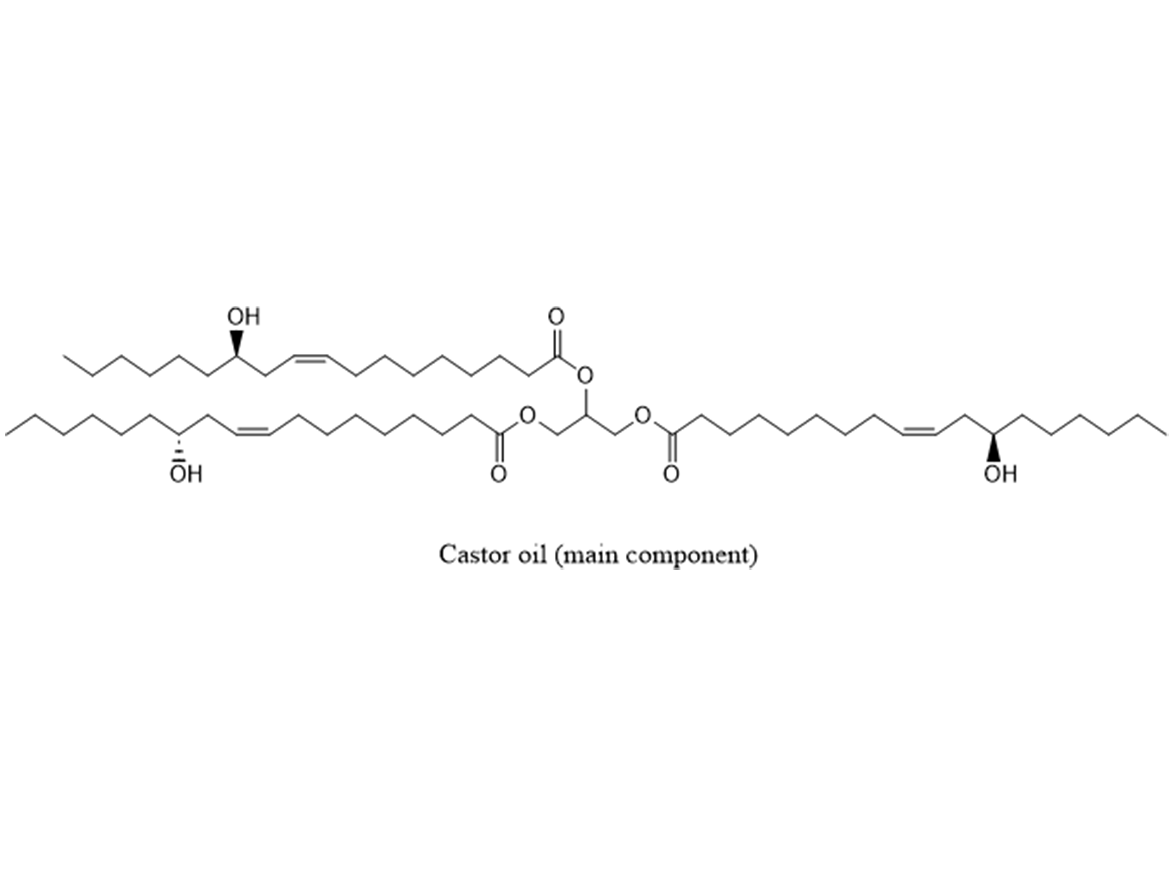
The biggest problem with polypropylene oxide polyols is when they are produced using an alkaline catalyst (mostly KOH). As the molecular weight increases, back biting causes the chain to break, leading to unsaturation. So, a polyol made with glycerin and 6 propylene oxide (PO), roughly 430 Daltons molecular weight will have an average functionality of about 2.95. Glycerin and 40 PO, roughly 2,400 Daltons molecular weight, will have a functionality about 2.8, having approximately 10% monol content. These monols will terminate the polymer growth and hurt properties. Using other catalysts, like DMC, (dimetal cyanide), will greatly minimize unsaturation.
Castor oil (Figure 5) is a unique oil, and is used in urethanes in large quantities. Most oils have a mix of fatty acids, and the same oil grown in different regions will have a different mix of fatty acids. Castor oil is 92% ricinoleic acid, and consistent in the two major growing regions (India and Brazil). The secondary hydroxyl functionality of ricinoleic acid makes it very useful in urethane systems.

Formulating MDI with castor oil or polypropylene oxide polyols is easy since the system will be ~100% solids, low viscosity and it has good physical properties (elongation, tensile strength, flexibility, abrasion resistance, etc). The two problems will be the competing reaction with water and the very-poor exterior durability. The water reactivity can be mitigated by using low-moisture raw materials and moisture scavengers. However, the substrate must be dry, and slightly over indexing the isocyanate by 3-5% will help maintain properties and prevent bubbles. The pot life of polyether polyols and polymeric MDI is about 20 minutes. The reactivity can be increased by using tertiary amines or metal catalysts. Organic acids can be used to decrease reactivity or increase pot life. Top coating the polyurethane with a light-stable coating will protect it from degradation.
Polymeric MDI has limited compatibility with higher-molecular-weight polypropylene oxide polyols. This will lead to incomplete mixing, independent domains, and poor performance. Using higher-monomeric-content MDI, adding some castor oil or polyols made by proproxylating ethylene diamine or toluene diamine will all increase the compatibility, mitigating this issue.
100%-active low-viscosity urethane coatings are not only possible, but have advantages over other coatings systems.
All information contained herein is provided "as is" without any warranties, express or implied, and under no circumstances shall the author or Indorama be liable for any damages of any nature whatsoever resulting from the use or reliance upon such information. Nothing contained in this publication should be construed as a license under any intellectual property right of any entity, or as a suggestion, recommendation, or authorization to take any action that would infringe any patent. The term "Indorama" is used herein for convenience only, and refers to Indorama Ventures Oxides LLC, its direct and indirect affiliates, and their employees, officers, and directors.
Looking for a reprint of this article?
From high-res PDFs to custom plaques, order your copy today!