Quality Assurance
Rheological Testing of the Sagging Behavior of Coatings
From a practical point of view, the following three criteria are important for coatings.
Specific terms that the coatings industry uses to describe these criteria are:
According to customers, there are few problems with the coatings resulting from the first two points. However, Ms. C. is still looking for a test method for QA that she can use to examine sagging behavior.
Tests with Flow Cups
When Ms. C. first started working for the company, viscosity was determined using flow cups. The Ford cup was used to determine the flow time as the "viscosity value" (see ASTM D 1200).4 It is now known that a single viscosity value cannot realistically describe a coating's flow behavior. The viscosity is not a material constant for most coatings because its value changes depending on the flow conditions. Therefore, flow cups were seldom used for laboratory testing except for oils or low-viscosity solutions. (The Ford cup was later replaced by the ISO cup, when ISO 2431 was introduced as the global standard in 1993).5 Thus, the problem of characterizing the sagging behavior of coatings could not be solved at all using the "flow viscosity value," as can be seen from comparative tests. The results of cup tests and application tests went well together only rarely within acceptable limits, and this agreement was likely accidental.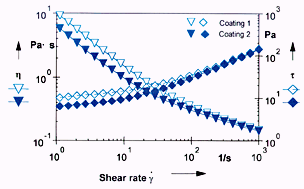
Flow and Viscosity Curves
Due to their complex structure, coatings have a complex flow behavior that cannot be described by one viscosity value. The viscosity depends greatly on the flow velocity. A few years ago, Ms. C. suggested that flow and viscosity curves should be carried out for the QA tests using a rotational viscometer. As the paint dispersions contain particles (metallic flakes), a parallel-plate measuring system with a gap width of 0.5 mm was used. This guarantees undisturbed flow during the shear test.Figure 1 shows typical measuring curves determined from two coatings in production:
Flow curves: This represents the shear stress t over the shear rate g.
Viscosity curves: These are determined from the flow curve data using a software program and represent the shear viscosity h over the shear rate g.6-7
The figure shows how the viscosity values of both coatings decrease in the shear rate range g = 1 to 1,000 1/s. The value falls from approximately 10 Pas to approximately 0.15 Pas. Both coatings display shear-thinning flow behavior (this behavior is also called "pseudoplastic"). Based on tests with the testing blade,8 Ms. C. knows that these two coatings display different sagging behavior. However, the viscosity curves for the two samples show no significant differences. This is especially true for the shear rate range between 100 and 1,000 1/s. Over time, it became clear that this test method was not suitable as a QA test to obtain information to characterize the sagging behavior.

Decomposition and Regeneration of the Coating Structure
Ms. C. then heard from a customer who uses a different test method for QA. He was satisfied with the method because the results matched those from application tests. He told her about oscillatory tests. At the time, the measuring principle seemed complicated, although it was clear to her that the test delivered exactly the results she needed. The test method realistically simulated the application process by the following three test intervals.Low-shearing: Determination of the structure at rest as the initial state before application
High-shearing: Reproduction of the behavior in the structural decomposition phase during application
Low-shearing: Determination of the structural regeneration over time after application
From the third interval, Ms. C. hopes to obtain the necessary information about the sagging behavior. She knows that a coating that runs off the substrate to a large extent is one that requires a long time for structural regeneration following application.

Oscillatory Tests
Ms. C. called a rheometer manufacturer to find out more about this test method. She made an appointment with a rheology consultant at their laboratory and brought along two coating samples. The consultant suggests measuring the viscoelastic properties of the dispersions in an oscillatory test, still using the parallel-plate system. In this type of test (in contrast to the flow curves of rotational tests), the upper plate of the measuring system performs a sinusoidal torsional oscillation at the set frequency and deflection amplitude.The rheometer measures two independent raw data values: the torque due to the sample's resistance to the forced deflection angle during shearing, and the phase shift between the set sine curve (as a time-dependent function of the deflection angle) and the resulting (time delayed) sine curve (as a time-dependent function of the measured torque).
Ms. C. takes in this detailed explanation but is more interested in the test result. The two independent raw data values are usually converted by a software program into G' and G'' values. The storage modulus G' represents the elastic behavior of the sample and the loss modulus G'' represents the viscous behavior. The curve functions of both parameters together describe the viscoelastic behavior.
Ms. C. quickly realizes that oscillatory tests have important advantages: this test characterizes the complete rheological behavior (both the viscous and the elastic, and therefore the viscoelastic behavior). Rotational tests only describe the viscous portion; however, in those tests the elastic behavior is ignored.

Step Test for Determining the Sagging Behavior
An amplitude test is performed as a preliminary test at the constant angular frequency of w = 10 rad/s. This test provides the permitted strain amplitude for the step test so that the limit of the linear viscoelastic range is not exceeded. Figure 2 shows that this limit is approximately g = 1 % for both coatings.For both coatings, the following settings were selected for the three intervals of the step test.
Oscillatory test with the shear strain g = 0.4 % and the angular frequency w = 10 rad/s. Both coatings show
G' G'', the elastic portion dominates over the viscous portion (see Figure 3). Under low-shear conditions, both coatings display a gel character and therefore have a certain amount of structure stability. The structural strength is usually given in the form of the G' value. Coating 1 has G' = 55 Pa and Coating 2 has G' = 28 Pa.
Rotational test with the shear rate g = 1,000 1/s. This interval is not presented in Figure 3.
The oscillatory test is performed under the same shear conditions as the first interval. Directly after the structural decomposition, both coatings in Figure 3 display G'' G'; the viscous portion dominates. Under this condition, a material flows. As long as G'' G', the sample has a liquid character and can run or sag unaided. The time-dependent regeneration of the structure can be seen in the increase in magnitude of G' and G". The G' value increases more steeply than G'' for both coatings. After a certain period of time, the G' and G'' curves of the two samples intersect. The coatings change from a liquid character back to a gel-like character. This intersection, with G' = G'', is usually taken as the criterion for the regeneration time of the structure.
This experiment showed the considerable differences that Ms. C. wanted to see: the intersection for Coating 1 occured after approximately 33 s, while Coating 2 had an intersection after approximately 54 s. Figure 4 shows a closeup of these intersections. The results match Ms. C's practical experience: users report problems with Coating 2 because it flows too long and therefore sags too much. With Coating 1, the tendency to sag remains within reasonable limits.
Measuring Instruments
The measurements shown were taken with the PHYSICA rheometer MCR 300 and the US 200 software.
Summary
A rheological test for determining the sagging behavior of spray coatings was presented using two waterborne coatings as an example. This step test consists of the following three intervals.Initial-state interval (oscillation under constant dynamic-mechanical conditions in the linear viscoelastic deformation range) for characterizing the structural strength under low-shear conditions in the form of the storage modulus G' and the loss modulus G''.
Load interval (rotation: high-shearing) to cause structural decomposition.
Recovery interval (oscillation under the same shear conditions as in interval 1) to analyze the time-dependent regeneration of the structure as G'(t) and G''(t), and the intersection of both function curves.
This article emphasizes the analysis of the third interval of the step test to characterize the structural regeneration. This process is often called "thixotropic behavior". The test result uses G' and G'' curves to show clearly how long a coating levels or sags after application.
Acknowledgment
The authors would like to thank Sarah Knights for the translation of this paper.
This paper originally appeared in the journal Welt der Farben.
For more information on rheology contact Eric F. Brown, Paar Physica USA, 10215 Timber Ridge Drive, Ashland, VA 23005; phone 804/550.1051; e-mail ebrown@paarphysica.com; or Circle Number 64.
References
1 Mezger, T.; Stellrecht, P.: The behavior at rest. Europ. Coat. J. (09/2000).2 Mezger, T.; Stellrecht, P; Wollny, K.: Thixotropic behavior / structure recovery of coatings (Congress Papers: European Coatings Show). PRA: Teddington, and Vincentz: Hannover, 2001.
3 Mezger, T.; Will, S.: Rheologische Pruefung des Ablaufverhaltens von Lacken. J. Welt der Farben (11/2001).
4 ASTM D1200 (1994 / 1999): Standard test method for viscosity by Ford Viscosity Cup.
5 ISO 2431 (1993, Corr. 2: 1999): Paints and varnishes - determination of flow time by use of Flow Cups.
6 Barnes, H.A., Hutton, J.F., Walters, K.: An Introduction to Rheology. Elsevier: Amsterdam, 1989.
7 Mezger, T.: The Rheology Handbook; for users of rotational and oscillatory rheometers. Vincentz: Hannover, 2002
8 Brock, T.; Groteklaes, M.; Mischke, P.: European Coatings Handbook. Vincentz: Hannover, 2000.
For further information
Contact Eric F. Brown, Paar Physica USA, 10215 Timber Ridge Drive, Ashland, VA 23005; phone 804/550-1051; e-mail ebrown@paarphysica.com; visit the link below or Circle Number 64.Links
Looking for a reprint of this article?
From high-res PDFs to custom plaques, order your copy today!