Pigment Blacks in Waterborne Coatings

This trend is being led by the automotive industry, which favors low-polluting coating systems. Aqueous-based paints are relatively quickly realizable alternatives. They are becoming well established not only in the field of OEM (original equipment manufacturers) but are also gaining in importance in the repair industry.
The increasingly strict environmental laws in Germany and the European Union require paint manufacturers to permanently allocate considerable adjustment expenditures. Not only is a decrease in emissions required, but applicability and the characteristics desired by the consumer must also be ensured. In this context, coloristic data demand special attention. Achieving the same jetness and hue in a new binder system is an essential development task.
This article will show a part of the experimental results obtained in the use of pigment blacks in various binders using approximately 10 additives. Although colloid chemistry experience in the field of waterborne paints is growing rapidly, a considerable part of what we know is still based on pure empirical knowledge. Work is exclusively focused on coloristic data. Other effects of additives on the paint must be studied separately.
The "Color" Black
In the true sense of the word, black is not a color that arises from the absorption of a specific wavelength of visible light and the reflection of the complementary color. A surface appears black whenever it reflects less than 1% of light. For the past 10 years, the popularity of black in the automobile industry has not diminished. Pigment blacks have proven their worth when it comes to jetness because they not only exceed the jetness of RAL 9005 (deep black), but they also achieve a blue-tinted blackness, which is perceived by the observer as particularly intense.It was a big problem in coloristic characteristics to quantify the jetness and hue of black paints.
It is readily apparent - for best results, in the sun or under a focused beam of light - whether a paint film surface is more jet black, blue-tinged or brown-tinged than another. However, it was impossible to express this difference in numbers.
With the development of colorimetric devices that distinguish well particularly in lower reflection areas, it is now possible to precisely quantify hues in the reflection area of <1%. The My value is derived from the standardized coordinate Yn for the green portion of the CIELAB system (see Figures 1-2). With the integration of Xn (red) and Zn (blue), the overall color impression is shown. Consequently, it is mathematically relatively simple to calculate the color ratio dM.1-2

Basic Characteristics
Production of Pigment Blacks
Pigment blacks are manufactured using three production processes: the gas black, furnace black and lamp black processes.4-5 Gas blacks have numerous "acidic" chemical groups on their particle surface while furnace blacks are weakly basic. Degussa gas blacks have an average primary particle size from 11 to 29 nm, and are characterized by their good dispersibility, as well as their solvent and binder compatibility. They have proven their worth worldwide in mass-tone coloration and as tinting pigments, and are preferred by numerous paint producers. Furnace and lamp blacks are used especially as tinting pigments.
Particle Size and Jetness
The smaller the particles, the bigger its light absorption or the smaller the light reflection. At the same time, the finer the pigment black, the greater the jetness (see Figure 3). Thus, the primary particle size of the pigment black with identical carbon black concentration is the deciding factor in a paint's jetness.
The size of actually existing agglomerates determines the hue. When viewed from the top, small agglomerates in mass tone demonstrate a blue tint, while larger agglomerates usually show the less desired red tint. It is, therefore, necessary to stabilize agglomerates after intensive dispersion in such a way that they do not flocculate.

Surface Modification
Oxidation of pigment blacks produces increased polar chemical groups on the particle surface area, which possess a higher affinity to the polar groups of paint binders. This especially applies to carboxyl groups. The treatment thus produces better dispersion and stabilization of the pigment black in the liquid phase and better distribution in a polymer matrix. In mass tone it yields a bluish tint.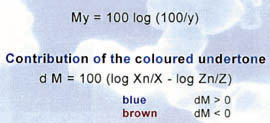
Pigment Black Dispersion Grinding Process
The dispersion of pigments and fillers takes place in several steps, some of which run parallel. Schematically one can distinguish the incorporation and the wetting of agglomerates present in the powder, their mechanical division and the wetting and the stabilization of freed boundary surfaces, thereby preventing the recombination of fragments. Agglomerates stabilize overall through adsorption of binders or wetting agents, which hamper undesired flocculation.
The smallest possible agglomerates of the pigment black and the narrowest possible agglomerate size distribution in the corresponding coating system are essential to produce optimal coloristic results. Dispersion is influenced by many parameters, which shall be discussed later on.
Grinding Media
The usual grinding media for pearl mills, attritors, Skandex, Red Devil, etc., consist of various materials that differ from each other primarily by their density and hardness. Special attention should be paid, in particular, to the following.- Glass -- approx. 1.5 g/cm3
Porcelain -- approx. 3.0 g/cm3
Steatite -- approx. 2.6 g/cm3
Al-oxide -- approx. 3.5 g/cm3
Zr-silicate -- approx. 3.9 g/cm3
Steel -- approx. 3.9 g/cm3
Grinding Media Size
Grinding media with a smaller diameter have a positive effect on the dispersion of pigment blacks, although their separation and cleansing are more difficult to achieve. In the experiments that will be described later, grinding media with diameters from 0.6-0.8 or 1.6-2.0 mm were used. These are the same media that are used in practice by paint manufacturers.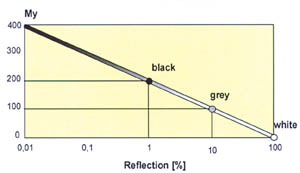
Dispersion Time
The longer the dispersion time, the better the degree of dispersion, which manifests itself in a low grindometer value, a high tinting strength or jetness and reduced haze. Good dispersion in pigment blacks leads to grindometer values of less than 10. In connection with this, pigment stability and to a certain extent the blue hue, in mass tone coloring especially, increase. However, only certain limit values are ultimately achieved and these values are dependent on the dispersion aggregate and of course the paint system.Wetting and Stabilization
As usual for fine pigments, the pigment black surface to be wetted and stabilized becomes larger with increasing dispersion. The developing reactive centers of the boundary surfaces must be saturated, i.e., stabilized and kept from re-agglomerating or flocculating. This requires adequate interaction of the dissolved or emusified paint constituents or the solvents with the pigment blacks. While in conventional systems this takes place through the adsorption of binder molecules and the resulting steric hindrance of the adsorbate, the electrostatic repulsion of the pigment particles or the corresponding adsorbates prevails in strongly polar systems such as waterborne paints. In general, the surface chemistry, the morphology and structure of the pigment black, the wetting capacity of the binder, the accompanying additives (wetting aids) as well as the solvents determine pigment black stabilization.As a rule of thumb, the following applies in the evaluation of the coloristic characteristics of a black paint in the first approximation:
- blue undertone = good stability
brown undertone = lacking in stability
In solventborne coatings it is possible to obtain good results without wetting agent, only by optimizing the grinding resins, the resin concentration and the solvents.
Waterborne Paints
Water as a solvent or emulsifying medium for paints differs fundamentally from organic solvents. Not only the inadequate wetting behavior or dissolving power for polymers, but also the high polarity and surface tension must be taken into account in the formulation of paints. Pigment blacks can be wetted with water but can hardly be stabilized. Therefore, polymers and wetting agents are of much greater importance here than in conventional systems.
For the dispersion of fine pigment blacks there are basically two ways to achieve success. First, carbon black is dispersed in water with the resin - if necessary - with small proportions of wetting and antifoam agents. Second, with no resin, pigment black is dispersed in a water/wetting agent mixture containing suitable antifoam agents and, if necessary, rheological additives.
Grinding with Dispersion Resins
Four different resins and three carbon blacks were evaluated.In order to determine the effect of the pure binder, no wetting agent was used. Results are shown in Table 2.Stability of Paints with FW 285 and FW 200
The stability of two paints was tested every four weeks during a storage time of six months at room temperature. Coloristic data, pH and degree of gloss were determined in the experiment.
The standard deviation showed that there was no there was no sign of flocculation that would have resulted in significantly worse coloristic characteristics.
Discussion of the Results
There is no significant difference with regard to the coloristic data achieved among the tested binders. The jetness levels reached are remarkably high and definitely can still be improved with the help of specially developed dispersion resins. One detects, however, the influence of the various pigment blacks on the jetness.Grinding with Dispersion Resins and Wetting Agents
Another experiment was conducted using the dispersion conditions described prior. Table 3 shows the raw materials and coloristic data of the mill base and the black coatings. As was clearly demonstrated, the black paints were only gradually improved by combining the binder and wetting agent in the mill base. An explanation for this could be a competitive situation between the binder and the wetting agent on the pigment black surface. Viscosity of the mill base diminished in all systems. This is of great importance in practice.Grinding with Wetting Agents
With the development of highly effective wetting and stabilizing agents for aqueous paints, it has become possible to wet and stabilize very fine pigments with a large specific surface area. Pigment blacks manufactured by the furnace black process have a hydrophobic nature, while pigment blacks produced by Degussa's gas black process are hydrophilic and thus differ in the amount of adsorbed wetting agent as well as the adsorption mechanism. By virtue of the surface chemistry, most carbon blacks are negatively charged. Therefore, cationic or neutral wetting agents are preferentially adsorbed by the carbon black.A low pH of a pigment black is not a reason for not using it in waterborne paints. One merely has to take into account that, due to the low pH, more neutralizing agent is required during the dispersion process. For this reason, the pH of the mill base must be raised by one-half to one point, as compared with what the desired pH should have been after the dispersion process.
Wetting Agent Proportions
One can find in the literature wetting agent proportions in relation to the pigment black surface area between 1-2 mg per m2. For the pigment black FW 285 with a BET surface area of around 350 m2/g, that would mean about 350 mg of wetting agent per g, which would correspond to 35% of wetting agent (active substance). Numerous tests, however, have shown that with fine pigment blacks in most cases1 50% of wetting agent -related to the pigment black - must be used. With pigment blacks having a smaller surface area, the aforementioned values apply.
The pigment blacks' typical morphology, which is dependent on the production process, could be an explanation for this.
Mill Base Formulation
In many experiments, the procedure shown in the above scheme proved favorable in the production of the mill base.Dispersing was made with a pearl mill. For most experiments, a Skandex disperser BS 20 was used. At the same time, several experiments were additionally carried out with the mini-zeta laboratory pearl mill (Netzsch), and the results were confirmed. These results cannot be generalized, because a pearl mill shows a higher efficiency in other formulations
With increasing dispersion time, the following occurs.
- Gloss at 20 deg increases
Haze decreases
Jetness My increases to a certain degree
Hue dM becomes bluer with better stabilization of fine pigment
Grindometer value decreases and shouldbe less than 10 microns
Wetting Agents
The wetting additives have been tested and were found to be particularly efficient in comparison to others. The wetting agent concentrations are between 50% and 100%, related to the pigment black. XPB FW 285, with an average primary particle size of 11 nm and a concentration of 10% - related to the binder - was used as the pigment black. Letting down was carried out with Alberdingk U 710 (see Figure 4).Figure 5 shows differently strong interactions of the dispersion additives with various pigment blacks, which can be seen especially with the hue - an obvious criterion for stability.
Discussion of the Results
As shown in Figures 4-5 in comparison to Table 3, the level of coloristic data is higher than that achieved with the pure grinding with dispersion resins. The described procedure is, however, not always possible since a lot of water is added to the finished paint through the milling formulation. One can try to increase the concentration of carbon black in the mill base or directly incorporate the pigment black.Influence of the Let-Down Resin
The tests carried out under identical conditions show the gradual difference in coloristic data depending on the let-down resin. The better the stabilization of the carbon black in the mill base, the less the tendency towards flocculation during the let-down process. The sequence of the addition of raw materials is just as important to the let-down process as it is to the preparation of the mill base (see Table 4).Following are a few rules of thumb for the let-down process.
- Ensure that the raw materials to be mixed have a good compatibility over the whole range of concentration.
- Adapt the pH of the mill base and the let-down resin.
- The temperature difference between the mill base and the let-down components should not be too large.
- If possible, the raw materials should be added while stirring constantly.
- If co-solvents must be employed, they should be grinded already with the mill base.
As expected, the jetness and, to a smaller extent, the bluish tint increase with an increasing concentration of the pigment black (see Figure 6). However, here again, we wish to refer to the logarithmic nature of the My value. If one takes reflection as the base, jetness tends to approach an asymptote with increasing pigment black concentration. Of course, the pigment black concentration in a mill base primarily is limited by the rheology.
For more information on pigment black, contact Maria Nargiello-Tetreault, Applications Manager, Degussa Corp., Akron Technical Center, 3500 Embassy Parkway, Suite 100, Akron, OH 44333; phone 888/SILICAS; e-mail maria.nargiello-tetreault@degussa.com; or Circle Number 96.
Brief Description of Pigment Blacks
Pigment Black XPB FW 285 has the deepest jetness among the carbon blacks manufactured by Degussa for waterborne paints. The well-known advantages of the Degussa gas blacks such as good dispersibility, high gloss and low haze in finishing paints are also especially strongly pronounced with FW 285. Due to its slightly acidic pH, the pH drop during dispersion is slight and pH stability is excellent.Pigment Black FW 1 falls under the same category, being likewise a gas black with all the positive characteristics mentioned earlier. In its coloristic data, it exhibits somewhat less jetness than XPB FW 285.
FW 200 and FW 2 belong to the group of additionally treated gas blacks.
The starting carbon black FW 1 is oxidized, with FW 200 being more oxidized than FW 2. Their strengths lie in the solvent-containing systems. With certain prerequisites followed, they can also be used in waterborne paints, exhibiting in them coloristic data much similar to those of FW 285. Due to the differing surface chemistry, other wetting agents and wetting agent concentrations could bring better results as against the non-oxidized carbon blacks. Since the pH is relatively low, higher amounts of neutralization agent are necessary in comparison to FW 285.
Colour Black S 170 is comparable to FW 1 in terms of surface chemistry but it is less fine and, therefore, exhibits somewhat less jetness. However, it is economically interesting.
Special Black 4 (ox.) and Printex U / Printex V are the so-called all-around carbon blacks, and are popular all over the world. They are used as much in waterborne paints as in conventional systems for black and gray coatings. Although they are relatively fine, they do not tend to a pronounced "rub-out" effect. They are especially preferred in one-coat paints since a high gloss and very good hiding power can be obtained with relatively good dispersibility.
Flame Black 101, Printex G and Special Black 100 have proven themselves well as pure tinting blacks. Printex 200, similar to tinting blacks, is relatively coarse for a pigment black and due to its relatively low conductivity in water it is predestined to be used in electrodeposition paints.
References
1 Mathias J., Lippok-Lohmer K., Welt der Farben 10/97, 28.2 Lippok-Lohmer K., farbe+lack 92 (11), 102h (1986).
3 Coatings Comet February 1999, 36-37 (IRFARB).
4 What is carbon black, Firmenschrift der Degussa AG, Frankfurt 1999.
5 Ferch H., Pigmentru?e, Vincentz Verlag, Hannover 1995.
Looking for a reprint of this article?
From high-res PDFs to custom plaques, order your copy today!