Staining Preventive UV Coatings
Hybrid organic-inorganic UV- or EB-cured coatings can be made from commercial easy-to-use low-viscosity acrylic monomers or pre-polymers containing a high content of pre-dispersed silica nanospheres. The use of such products has been described as fulfilling protection requirements for wood, metal, glass, plastic substrates and fiber optics, mainly against abrasion, scratch, chemical wear, tear, and barrier to gas.1-6 Three recent studies detailed the role played by silica particles in the enhancement of hardness, and resistance to scratch, abrasion and aggressive chemicals while maintaining transparency and gloss. The improvement was explained by the high surface covering by silica nanospheres and their homogeneous distribution in the bulk of the coatings.7-9 Another work described the increase of the photo-curing rates of colloidal silica acrylates compared to the unmodified monomers.10
In this study, we investigated some UV-cured hybrid coatings possessing hydrophobic or hydrophilic surface properties. The capacity of these coatings to resist staining is evaluated.
Architectural outdoor coatings require improvement in weathering resistance. Many paint manufacturers propose staining preventive and easy-to-clean coatings. Most of these products are traditional latex or solventborne coatings. UV-curable coatings were rarely proposed. The main objective is to keep the coating clean over time or to be able to clean it easily with an appropriate solution. Outdoor stains are generally mixtures of organic/lipophilic and inorganic/hydrophilic compounds originating from car exhausts and building works. These mixtures, once deposited onto the substrates, are very hard to remove. Factors that affect the resistance of coatings to staining and to dirt pick-up include the polymer chemical nature, glass transition temperature, viscoelastic properties, degree of crosslinking, surface morphology and hydrophilic/lipophilic behavior.12 Hydrophilic substrates are generally preferred to hydrophobic surfaces since stains are expected to be more easily removed from surfaces by rainfall or by light. Dirt and stain pick-up are usually measured with the change in total reflectance (DL*) and 60?gloss (DGl60) before and after exposure to rinsing cycles with a staining liquid and drying.13-14
Experimental Materials
Monomers:
Y Acrylic silica monomer: (Clariant) Highlink(r) OG103-53 (50% SiO2 - Dp=50 nm)
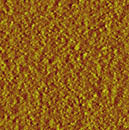
Tests
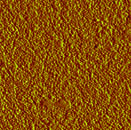
Formulation
Formulations were obtained by mixing all components by magnetic stirring. The following ratios, respectively, are: HDDA/PA = 90/10 (w/w), [SiO2] = 0-25%, [MLIPO] = 0-5%, [MHYDRO] = 0-20%, [Photoinitiator] = 6% of total monomers.Aspect of the Coating
All coatings prepared in this work are clear and transparent, showing good leveling onto Leneta charts and Polystyrene plates.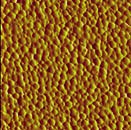
AFM Surface Characterization
Commercial colloidal acrylic silicas are available, sized from 10-100 nanometers. AFM observations of the coatings loaded with 25% silica of 13, 25 and 50 nm particles show a close-packed organization of monodisperse particles covering the whole surface (see Figure 1). The good particle dispersion indicates a good compatibility between the inorganic and organic phases.Surface Energy of the Lipophilic Hybrid Coatings
The reference coating (0% SiO2, 0% MLIPO) is moderately hydrophobic (qH2O = 68N). It shows a high surface energy with both apolar/dispersive and polar properties (gs= 55, gd= 41, gp= 14 mJ/m2). Figure 2a shows how the coatings become highly water-repellent when using small amounts of MLIPO at different SiO2 loadings. The highest contact angle with water (qH2O = 102N) is obtained when [MLIPO]= 0.5% and [SiO2] |12%. Surface energy is lowest then (see Figure 2b) and the coating gets a pronounced apolar characteristic (gs= 30, gd= 27.5, gp= 2.5 mJ/m2). This means that at low MLIPO level, the monomer has sufficient time to migrate to the air side of the coatings during polymerization. The diffusion process is surprisingly enhanced by 10% of nanoparticles. This result is backed by a recent study that shows that a concentration gradient is often found when using hydrophobic surface-active acrylic monomers in UV coatings.11Surface Energy of the Hydrophilic Hybrid Coatings
MHYDRO was chosen in our study for its hydrophilic property and for its good compatibility with the other components of the formulation. Perfectly clear coatings were obtained. Figure 3a shows that when [SiO2] = 0%, the water-coating contact angle qH2O drops with increased amount of the hydrophilic monomer to reach 52N when [MHYDRO] is 20%. Surface energy measurement (see Figure 3b) then showed an increase in total surface energy and a more hydrophilic character (gs=64, gd=44, gp=20 mJ/m2). These values remained unchanged up to [SiO2] = 10% but are strongly affected at higher loadings. Lowest values of water-substrate contact angle and highest surface energy with a hydrophilic character were obtained when [MHYDRO] = 20% and [SiO2]=25% (qH2O=37N and gs=73, gd=46, gp=27 mJ/m2). It is clear that MHYDRO monomer behaves very differently compared to MLIPO. At [SiO2]< 10%, little migration of MHYDRO was detected meaning that it is well copolymerized within the bulk. However, at higher SiO2 content, the monomer is more concentrated at the airside of the coating.
Staining Preventive and Easy-to-Clean Properties of Modified Hybrid Coatings
We also evaluated the ability of some hybrid coatings to resist staining. Resistance to Taber abrasion was also estimated. Used motor oil was chosen to simulate the staining. We then successively cleaned the coatings with a paper cloth, rinsed with water and finally with ethanol. In between, we measured (DGl60) which was found more discriminative than (DL*) measurements. Results are listed in the table.
Resistance to Staining
The hydrophobic oil sticks strongly to the hydrophobic coatings. {[SiO2] = 0/20;[MLIPO] = 1; (qH2O) = 94N/95N} and is not easily removed by hand cleaning or by water rinsing. This is due to their mutual hydrophobic affinity. The resulting stain is almost completely removed by a slight cleaning with ethanol, meaning that sticking is only superficial. Results in the table also show that surface hydrophobicity is enhanced by incorporating 20% SiO2 in the coatings. The stain is still not removed by hand cleaning and by water rinsing, it is however easily removed upon cleaning with ethanol. We can therefore consider these coatings as easy-to-clean materials.Hydrophilic coatings {[SiO2] = 0/20;[MHYDRO] = 20; (qH2O) = 53N/42N} resist much better to the staining. The coatings almost recover their original surface when cleaned with a paper cloth and rinsed with water. Cleaning with ethanol completely removes the stain. In effect, when cleaned with rainwater, the stronger affinity of the hydrophilic surface for water would facilitate the removal of the hydrophobic stain. One should, however, maintain a good hydrophilic/hydrophobic balance to minimize swelling or dissolution of the coating by water. We can consider these coatings as stain preventive and easy-to-clean coatings.

Abrasion Resistance
The effect of SiO2 loading is best seen with the severe abrasion test (CS17 wheels, 1kg load, 1,000 cycles). While the reference coatings suffered a weight loss of 17 mg and an optical density loss of 36%, the coatings loaded with 20% SiO2 resist 3 to 4 times better. Resistance to abrasion can be further improved on optimization of silica particle size, particle size distribution and loading.9Conclusion
Surface properties of thin UV-cured acrylic coatings containing hydrophilic and hydrophophic monomer additives and 50 nm size colloidal silica particles were compared in this study.Surface tension measurements have shown that the coatings become highly hydrophobic when 0.5% of hydrophobic additive was used. Hydrophobic stains are not easily removed on rinsing with water but these are completely removed on cleaning with an appropriate organic solvent.
Hydrophilic coatings can be obtained with 10-20% incorporation of a hydrophilic monomer. They offer very good resistance to staining. Stains are easily removed by water rinsing or by cleaning with solvents.
Colloidal silica even at high loading give clearcoats which resist very well to abrasion. Surface covering of the coating by silica nanoparticles also acts as a physical barrier.
Acknowledgements
The authors would like to thank Michael Kelly of Clariant Corp., and David Floc'hlay for his technical contribution to this study.
Copyright 2002, RadTech International North America Inc. Reprinted with permission from the RADTECH 2002 Conference Proceedings.
For more information on silica acrylates, contact in the U.S.: Maude Root, Clariant Corp., Charlotte, NC; e-mail maude.root@clariant.com; phone 704/331.7072; fax 704/331.7825; in Japan/Asia, contact Takeshi Nakamura at Clariant K.K., Osaka, Japan; e-mail takeshi.nakamura@clariant.com; phone: +(81)-66-262-8621; fax +(81)-66-262-8628; in Europe and ROW, contact Armand Eranian at Clariant France, e-mail armand.eranian@clariant.com; phone +(33)-1-46-96-98-75; fax +(33)-1-46-96-99-03.
References
1 Eranian, A.; Roux, C. Conference Comett/CTTM (Le Mans) (1995).
2 Lewis, L.N.; Katsemberis, D. J. Appl. Polym. Sci, 42,1561 (1991).
3 Misra, M.; Guest, A.; Tilley, M. Surf. Coat. Inter., 12, 594 (1998).
4 Etienne, P.; Coudray, P.; Moreau, Y.; Porque, J. SPIE Conference on Organic-Inorganic Hybrid Materials for Photonics, SIPE Vol. 3469, 8-13 (1998).
5 Etienne, P.; Coudray, P.; Piliez, J.N.; Moreau, Y.; Porque, J. SPIE 44th Annual Meeting, SIPE Vol. 3803, PP. 2-11 (1999).
6 A.R. Van Heeswijk, W.; Vriens. P.H.; Vrancken, J.J.; Van Engelen, G H.M.; Eranian, A.; Roux, C. Radtech Europe 95 Conference Proceedings, 430-436 (1995).
7 Vu, C.; Eranian, A.; Faurent., C.; Noireaux, P.; Deveau, J. Radtech Europe 99 Conference Proceedings (Berlin), 523-529 (1999).
8 Vu, C.; Faurent, C.; Elango, V.; Eranian, A. Radtech USA 2000 Conference Proceedings (Baltimore), 822-831 (2000).
9 Vu, C.; Lafert*, O.; Eranian, A. Radtech Europe 2001 Conference Proceedings (Basel), 822-831 (2001).
10 Decker, C. Chimia, 47, 378-382 (1993).
11 Zahouily, K.; Boukaftane, C.; Decker, C. Radtech Europe 1999 Conference Proceedings (Berlin), 803-808 (1999).
12 Smith, A.; Wagner, O. J. Coating Technol., 68, (862), 37-43 (1996).
13 Nakaya, T. 28th Annual International Conference on Organic Coatings Proceedings(Athens), 383-399 (1994).
14 Kaczynski, E.; Miroux, P. Eurocoat 94 V2 (Barcelona) (1994)
Looking for a reprint of this article?
From high-res PDFs to custom plaques, order your copy today!