Simple Coating Test Instruments
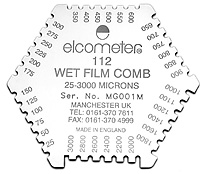
From the assessment of surface profile through climatic conditions to wet and dry film thickness, there are simple mechanical gauges to assess and monitor the application of a coating. These instruments represent testing methods that can be used particularly where conditions prevent the use of electronic gauges, such as where there are hazardous vapors, which could be ignited by a spark generated by a battery-powered gauge.
Surface Preparation
There are two issues to be considered when assessing the condition of a surface prior to the application of a coating: the profile and the cleanliness.The profile is a particularly relevant parameter where the substrate preparation includes grit or shot blasting.
The adhesion of an anti-corrosion coating is dependent on the profile height. More significantly, in terms of process control, the coverage rate for a paint is influenced by the profile height — the greater the peak-to-valley height, the greater the peak density and the greater the total surface area to be covered by the paint.
Analysis has shown that a coarse grit-blasted surface can have the effective area increased by a factor greater than three compared to a smooth surface.
The primary method to assess the profile after shot or grit blasting is to use the ISO Comparator. This is a four-segment replica of the different grades of surface finish described in ISO 8503. The difference between the shot and the grit comparator lies in the shape of the profile left after the blast process. A shot-blasted profile is rounded, whereas a grit profile is angular, matching the shape of the media used to clean the surface to be coated.
Assessing the cleanliness of the blasted surface starts with the simple evaluation of rust removal as described in ISO 8501. This book of colored photographs, often referred to as the Swedish Rust Standard, shows four grades of steel prior to cleaning. For each initial grade, illustrations of the finish that can be expected for a particular grade of cleaning are shown. For example, A Sa 2 represents A rust-grade steel cleaned to level 2, “thorough blast-cleaning,” and A Sa 3 represents A rust-grade steel cleaned to level 3, “visually clean steel.”
There is also a simple, low-cost method for assessing the contamination of a surface by soluble salts, such as magnesium and sodium chloride, that does not rely on electronics. Known as the CHLOR*TEST salt detection kit, this method uses an organic acid solution to break the salt/substrate chemical bonds and therefore dissolves a high proportion of the surface salt contamination. The level of contamination is assessed by collecting the sample and testing it with a chloride salt titration tube that measures the salt level in parts per million or µg/cm2.
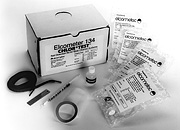
Climate Monitoring
When paint is applied, the relative humidity of the air, the air temperature and the surface temperature can individually and collectively influence the quality of the final coating. Painting a steel surface that has water vapor condensing onto it will lead to premature coating failure due to a corrosion cell being formed by the steel, the water and the trapped air (oxygen) underneath the coating that is intended to protect the surface.Simple mechanical gauges can be used to measure relative humidity and temperature and do not rely on battery power supplies. The traditional technique for measuring humidity using the wet and dry bulb hygrometer, often called the whirling hygrometer, is still widely used. Two glass thermometers, one with a moistened wick wrapped round the bulb, are whirled until the cooling caused by the evaporation of the moisture in the wick has cooled the “wet” bulb to a minimum temperature. The dry bulb temperature and the wet bulb temperature can then be used to determine first the dew point and then the relative humidity using a dew point calculator. The dew point is the temperature at which water vapor will start to condense out of the air at a particular humidity. To ensure that a surface is safe to coat, the surface temperature should be at least 3ºC above the dew point.
Bi-metallic dial thermometers with magnetic rings for attachment to steel can be used to establish the surface temperature while the relative humidity is being assessed. It should be noted, however, that the electronic Dewmeter provides the information more quickly than the traditional whirling hygrometer and magnetic thermometer.
Wet Film Thickness Measurement
For solventborne coatings, the measurement of the wet film provides information about the coating application and the coverage of the substrate. Such measurements are made with wet film combs or wet film wheels, and it is even possible to obtain a comb for the measurement of uncured powder paint.Wet film combs are very simple devices. Teeth are cut in to the edge of the comb. The depth of these teeth is controlled relative to the shoulders at the edge of the comb. For example, 25, 50, 75, 100, 125 and 150 µm is one side of a popular wet film comb. The shoulders of the comb are inserted into the paint layer to touch the substrate soon after the paint is applied and before the solvent can evaporate. Checking which teeth are coated and which are not can assess the depth of the wet film. The paint manufacturer’s technical data sheet can be consulted for the percentage solids or the wet-to-dry ratio. This information, together with the wet film thickness, can be used to predict the dry film thickness. The obvious advantage is that any correction to the process can be made instantly while the applicator is at hand.
These low-cost wet film combs are available in a variety of sizes and shapes, and there are even disposable wet film combs formed out of solvent resistant plastic that can be stored after use as a record of the wet film measurement.
Wet film wheels provide a continuous scale for the measurement of the wet film with an eccentric inner rim against two concentric outer rims. This form of wet film measurement is more difficult to manufacture and therefore is more expensive that the wet film combs, but is more precise.
Dry Film Thickness Measurement
Fifty years have passed since the first magnetic coating thickness gauge based on the magnetic reluctance principle was patented, and it is still available today. Also still available are the well-known “banana” gauges that are based on the magnetic pull-off principle. Neither of these gauges requires a battery, and both are calibrated on traceable coating thickness standards.The magnetic reluctance principle uses the effect of the non-magnetic coating on the strength of the magnetic field formed by a permanent magnet in the gauge and supported by the magnetic substrate under the coating. The thicker the coating the weaker the magnetic field passing through the substrate.
These gauges are capable of a measurement accuracy of ±10% and are applicable to all non-magnetic coatings applied to a magnetic substrate. The calibration of the gauge can be adjusted at a known point on the scale to account for the effects of different magnetic properties of different substrate materials, the shape of the coated object and its surface finish.
The banana gauge uses the magnetic force generated by a permanent magnet attracted by the magnetic substrate under the coating. The magnet is mounted on a balanced arm so the gauge can be used in any orientation — upright, horizontal or even upside down. The magnet is pushed into contact with the surface of the coating and a scale wheel, coupled to a helical spring, is used to exert a pull-off force on the magnet. The wheel is scaled in units of coating thickness — µm, mm or mil (thou) — rather than the force generated in the spring to pull the magnet off the surface. The position of the wheel when the magnet detaches from the surface is the thickness of the coating.
These gauges are capable of a measurement accuracy of ±5%. Gauges with ranges up to 6 mm are available.
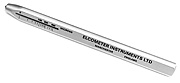
Conclusion
Although electronic gauges for the assessment of surface profile, salt contamination, humidity, temperature and coating thickness all have their benefits, the use of the low-cost mechanical coating gauges should not be overlooked. These gauges represent the origins for quality control methods used in the finishing industry and still have their place particularly on sites where the use of electronic gauges is hazardous or inconvenient, such as in remote locations where battery power may not be readily available.For more information on coatings testers, contact Elcometer Inc., 1893 Rochester Industrial Drive, Rochester Hills, MI 48309; phone 248/650.0500.
Looking for a reprint of this article?
From high-res PDFs to custom plaques, order your copy today!