Functional Silicate Fillers: Basic Principles
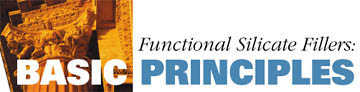
The industrial silicate minerals, wollastonite, talc, mica, kaolin, feldspar, and nepheline syenite are widely used in coatings as "extender pigments." Current formulation practice more appropriately uses these minerals as functional fillers. They are chosen to optimize coating stability, rheology and application properties, and to enhance dry film properties. Very fine particle size silicates, particularly certain kaolins and ultrafine talcs, are used as pigment extenders in a more literal sense. The pigment that is extended is TiO2. These extenders effectively separate the individual TiO2 particles and provide the optimum pigment spacing for maximum opacifying effect. Pigment extenders are used in this way to reduce the amount of relatively expensive TiO2 required for a given level of opacification and whiteness.
The effects of the silicates on coatings are a consequence of the following.
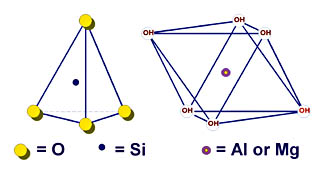
Structure and Mineralogy
The chemistry of the silicate minerals directs their lattice structures, which in turn determine their functional shapes. Chemistry and lattice structure also account for the chemical effects of these minerals in coatings. Although platy talc is insoluble in coatings, it will impart an alkaline pH because of the surface chemistry of its plate edges, which constitute a very small amount of its total surface area. Wollastonite imparts alkalinity and corrosion resistance because of the availability of soluble calcium on all surfaces.The structural lattice of the silicate minerals is built from two basic substructures: the tetrahedron and the octahedron, as illustrated in Figure 1. The silicates used by the coatings industry can be pictured as the configurations made by joining of such tetrahedra and octahedra to themselves and to each other in three dimensions. Kaolin, talc and mica are composed of one or two sheets of silica tetrahedra joined to a sheet of alumina or magnesia octahedra through shared oxygen atoms. This laminate structure accounts for their platy functional shape. Wollastonite is formed by chains of silica tetrahedra joined side by side with calcium, resulting in acicular, needle shaped crystals. Nepheline and feldspar crystals are not constrained to grow in any particular direction, so their particles have an irregular blocky shape.
Mineral purity is also a factor in filler selection and use. Commercially exploitable ore deposits are rarely composed of the single mineral of interest. A substantial component of the value-added cost of the silicates is often the expense incurred by the producer in reducing mineral impurities by screening, air classification, washing, flotation, centrifuging, magnetic separation, heavy media separation, electrostatic separation, or various combinations of these. Very minor amounts of residual accessory minerals can sometimes adversely effect utility and value. The presence of one percent of quartz in a kaolin, for example, may add abrasivity and health concerns. Conversely, some silicates such as nepheline syenite and tremolitic talc, which are natural mineral combinations, derive commercial value from their composite mineral properties.
Physical/Chemical Properties
The performance properties of the silicate fillers are determined by their physical and surface chemical properties. These involve particle shape and particle size, plus the filler's volume fraction in the coating matrix (PVC) and its adhesion to the binder.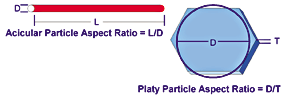
Particle Shape
The particles of the filler silicates can be described by three basic shapes: blocky, as with feldspar and nepheline syenite; platy, as with talc, mica and kaolin; and acicular, as with wollastonite. Platy and acicular particles are further characterized by aspect ratio. For platy particles, the aspect ratio is the ratio of the mean diameter of a circle of the same area as the face of the plate to the mean thickness of the plate. For acicular particles it is the ratio of mean length to mean diameter, as illustrated in Figure 2.If a mineral is to contribute to the mechanical properties of a coating film, stress, as from stretching or bending, must be transferred from the polymeric film to the strong and stiff mineral. The stress transfer is more efficient if the mineral particles are smaller, because for a given concentration greater mineral surface is exposed to intercept the stress. Effective stress transfer also requires a certain minimum aspect ratio. Once this ratio is exceeded, the efficiency of stress transfer increases with increasing aspect ratio. Platy and acicular particles are therefore preferred.
While small particle size and large surface area promote the durability of a coating film, they also promote high vehicle demand, which lowers critical pigment volume concentration (CPVC) and limits loading levels. The balance of film reinforcement and binder demand can be controlled by the choice of mineral, the particle size distribution of the mineral, and the use of combinations of minerals. For instance, wollastonite may be used as an alternative to the platy silicates because its acicular shape exposes relatively low surface area. This allows higher loadings, while still providing good mechanical film properties.
As shown in Figure 3, high aspect ratio particles in general tend to pack in such a way as to create larger interstices, which fill with binder, as opposed to low aspect ratio or blocky particles. Platy and acicular silicates, therefore, are generally produced with a broad distribution of particle sizes. The finer particles fit within the interstices of the larger ones, displacing binder and increasing CPVC, without compromising the mechanical properties of the coatings film. With narrow size distribution high aspect ratio fillers, this purpose may be served by the primary pigments and by low cost, fine ground nodular fillers such as calcium carbonate and silica.

Particle Size
There is probably no single property of fillers that is as misleading and misunderstood as particle size. A filler's technical description may contain a value, usually in micrometers, for median particle size or median diameter. This number is of limited practical value. The only three-dimensional geometric shape that can be unequivocally defined by a single number, such as diameter, is a sphere. The diameters of nodular and blocky particle are poorly related to that of a sphere. Platy and acicular minerals, particularly high aspect ratio types, cannot be defined in any literal sense solely by diameter, yet that is the way their particle sizes are routinely characterized.The equipment used for particle size analysis, whether based on principles of X-ray sedimentation, light scattering, light extinction or electrical resistance/volume displacement, interprets particle analysis data as if all particles are spheres, regardless of actual shape. Particle size is conventionally reported as diameter, but the values reported are actually in terms of equivalent spherical diameter (esd). A talc product, for example, may be offered with a median particle size of 3 micrometers. This value is actually 3 micrometers esd, meaning that the median particle size is equivalent to a sphere 3 micrometers in diameter.
For any given method of particle size analysis, particle size distribution data is somewhat useful for comparing the relative fineness of samples with similar particle shapes. However, particle size distribution, rather than the commonly reported median esd, must be compared. The median indicates only that half the particles have a larger esd and half a smaller one. It says nothing about the size of the largest or smallest particles, which can have a significant effect on the wet and dry properties of a coating. The median esd cannot provide truly comparable results for two minerals with distinctly different shapes, such as nepheline syenite and high aspect ratio wollastonite.
Particle size analysis is also complicated by different methodologies that base their calculations of esd on different physical properties. For the 3 micrometer median esd talc above, the equivalence may be to a 3 micrometer sphere having the same sedimentation rate, or the same volume, or the same mass, or the same surface area. Particle size analyzers designed on different principles of analysis should not be expected to necessarily provide comparable results even on the same sample.

Volume Fraction
The volume fraction of the filler, or its pigment volume concentration (PVC), is the volume it occupies divided by the volume of the dry coating film. Fillers usually exert their strongest overall influence on coatings properties when the volume fraction is sufficiently high to allow for the matrix to coat all particles and fill inter-particle voids. In coatings, this occurs at the critical pigment volume concentration (CPVC). As Figure 4 qualitatively illustrates, film properties change rapidly near the CPVC. Film density, tensile strength and adhesion tend to reach their maximum at the CPVC. At pigment volume concentrations above the CPVC, there is not enough binder to completely fill the voids between the pigment particles. As a result, the film becomes more permeable, with consequent reduction in scrub resistance, stain resistance, rust inhibition, enamel holdout and blistering. As the CPVC is approached and exceeded, the pigment particles progressively disrupt the smoothness of the film surface, causing light to be scattered and gloss to be reduced. The film surface becomes very rough with pigment particles, and the film has a very flat appearance.
Binder-to-Filler Adhesion
Intimate contact with the binder is essential to filler functionality. A filler may be dispersed throughout a coatings film, but any gaps at the filler-binder interface represent areas of zero tensile strength and locations for the transmission or collection of moisture and other liquids. This is analogous to exceeding the CPVC with the subsequent effects on permeability and tensile strength.Solventborne coatings present significantly different considerations than waterborne coatings regarding the intimacy of binder-to-filler contact and adhesion. In the case of the former, the mineral is already wetted by and dispersed throughout an organic medium. As volatiles are lost and the film contracts, the mineral particles become more closely packed and are ultimately encapsulated in the residual film of polymeric binder.
In a waterborne coating, such as a latex paint, the mineral particles are wetted by water that contains surfactants and dispersing agents designed to make the particles hydrophilic and resistant to agglomeration. The dispersed mineral particles share the aqueous medium with dispersed binder micelles. As volatiles are lost, the binder micelles coalesce into a continuous polymeric film. In so doing, they must deform around, displace water from, and coat the mineral surfaces. The greater the surface area of the mineral particles, the greater the challenge to effective encapsulation. This process is consequently less conducive to intimate matrix-mineral contact than that of solvent paints.
Surface treatments and surface modifications can optimize a filler's compatibility with and adhesion to the binder matrix. Although a mineral to which any type of organic chemical has been added is commonly called surface-treated, a surface treatment can be differentiated from a surface modification on the basis of functionality. A surface-treated filler is coated with a processing aid. A processing aid may not bond to the filler and does not bond to the matrix. It acts as a "wetting" agent to make the filler surface hydrophobic and more intimately coated by the organic medium. Surface treatments improve deagglomeration and dispersion in organic media and allow higher filler loadings.
A surface-modified filler has a coupling agent durably attached to its surface by covalent bonds. The coupling agent is in turn bound to the matrix through chemical reaction or chain entanglement. The coupling agents used as surface modifiers perform the same functions as surface treatments, and, in addition, improve substrate adhesion, film integrity, weathering and service life. The most commonly used modifiers are the organosilanes. The general chemical structure of organosilanes is RSiX3, where X is a hydrolyzable group, such as methoxy, ethoxy, acetoxy, or chloride, and R is a nonhydrolysable organofunctional group. The silanes most often used on fillers for coatings are alkoxy derivates, RSi(OR')3, with amino, epoxy, methacrylate or vinyl functionality.
Modification with organosilane depends on the ability to form a bond with silanol groups (-Si-OH) on the silicate mineral surface. Since the silicates that are successfully silane-modified generally lack structural silanols, these are a result of the reaction of silica surfaces and adsorbed atmospheric moisture.
The hydrolysis of an alkoxysilane forms silanetriol and alcohol:
RSi(OR')3 + 2H2O RSi(OH)3 + 3R'OH
The silanetriol slowly condenses to form oligomers and siloxane polymers. The -Si-OH groups of the hydrolyzed silane initially hydrogen bond with -OH groups on the mineral surface. As the reaction proceeds, water is lost and a covalent bond is formed. The reaction of hydrolyzed silane with mineral surface -OH can ultimately result in the condensation of siloxane polymer, encapsulating the mineral particle, if sufficient silane is used. Once the mineral is reacted with the silane it exposes an organophilic or organofunctional surface for interaction with the binder matrix, as illustrated in Figure 5. Silane treatment levels are typically 0.5-1.0% on mineral weight. Because the effectiveness of silane modification depends on the availability of silanol groups on the mineral surface, some of the silicate fillers are more amenable to silane modification than others. Wollastonite is very receptive to treatment and modification with silanes, and is the filler most commonly used in coatings in this form.

One Test for Many Properties
The oil absorption of a filler reflects the composite effect of all of the foregoing factors - particle shape, particle size distribution and surface area, effect of mineral PVC on CPVC, and mineral-matrix interaction. Oil absorption values are therefore a useful guide to the coatings formulator's selection of the optimum combination of pigments and extender pigments to meet formulating goals.The purpose of the spatula rub-out oil absorption test (ASTM D 281) is to indicate binder demand by determining the amount of linseed oil that is just sufficient to coat the mineral particles and fill the inter-particle interstices. The two components of oil absorption warrant separate consideration: The first is the amount of oil required to wet and coat the mineral particles. This depends on the particles' surface area, which is affected by their particle size distribution; their hydrophilicity, which can be adjusted by surface treatment or surface modification; and their porosity, which is a result of their lattice structure. Surface treatment or surface modification, for example, can reduce oil absorption and raise the CPVC of a filler that is otherwise an appropriate shape and size distribution. After the particles are coated with linseed oil, the second component of oil absorption is the additional oil that fills the interstices. In effect, this test measures the CPVC of the mineral-linseed oil composite and has some value in indicating the mineral's CPVC in a coating.
The following equation is often cited to relate oil absorption to CPVC (see Hare).
CPVC = 1 U [1 + (OA x r)/93.5]
where OA is the oil absorption and r is the specific gravity of the mineral. This is generally considered to be a good predictor of CPVC in solvent paints. This formula overstates somewhat the CPVC expected in latex films because of the different mechanism of filler integration. From this equation, nevertheless, comes an appreciation of the effect of a filler's specific gravity, or weight per gallon, on CPVC: for a given oil absorption, a higher specific gravity results in a lower CPVC. This relationship is easily overlooked, however, because the high specific gravity pigments and fillers, such as TiO2 and barite, are often lower in oil absorption than low specific gravity alternatives. Because paints are sold by volume, rather than by weight, specific gravity must be taken into account along with cost per pound when the overall economics of the coating formulation are considered.
The table provides an interesting comparison of the influence of particle shape and particle packing on the two components of oil absorption. The 6 Hegman high purity platy talc has a considerably lower surface area but higher oil absorption than the 6+ Hegman tremolitic talc. The surface adsorption by the platy talc is lower, and the inter-particle absorption is greater than with the tremolitic talc. This is understandable, since the high aspect ratio talc plates have relatively large interstitial volumes. The tremolitic talc is a natural mineral blend having a broad size distribution of platy, blocky and acicular particles. This combination exposes greater surface area, but allows the particles to more efficiently pack, leaving less interstitial volume.
The oil absorption values of individual pigments and fillers can provide a useful indication of the relative effects of these components on CPVC in a prospective formulation. Balancing the coating's PVC and CPVC to attain formulating goals, however, requires an appreciation of the aggregate surface areas, specific gravities and packing geometries of the particular combination of pigments and fillers used.
Conclusion
The basic principles presented form the foundation for an appreciation of the properties and functions of the silicate extender pigments in coatings. Subsequent articles will expand these principles to detail the use and effects of wollastonite, talc, mica, kaolin, feldspar and nepheline syenite in coatings.For more information on silicate fillers, contact RT Vanderbilt Co., phone 203/853.1400; fax 203/853.1452; visit www.rtvanderbilt.com; e-mail pciullo@rtvanderbilt.com or srobinson@rtvanderbilt.com; or Circle Number 122.
Bibliography
Braun, Jergen. H. Introduction to Pigments, FSCT, Blue Bell, PA, 1993.Ciullo, P.A., (Ed.) Industrial Minerals and Their Uses, Noyes Publications, Westwood, NJ, 1996.
Hare, Clive H. Protective Coatings, Technology Publishing Co., Pittsburgh, 1994.
Hurlbut, C.S., Klein, C. Manual of Mineralogy, 21st ed., Wiley, New York, 1993.
Patton, Temple C. Paint Flow and Pigment Dispersion, Wiley, New York, 1979.
Wicks, Zeno W. Film Formation, FSCT, Blue Bell, PA, 1986.
Links
Looking for a reprint of this article?
From high-res PDFs to custom plaques, order your copy today!