Reducing Rejects with Color Verification
First, here are a couple of definitions:
Color measurement has been used by manufacturers to ensure that the colors being produced are consistent and meet the customer's needs. This typically includes the use of a spectrophotometer and some associated software, and may include formulation and correction as well as quality control.
Color verification involves the use of a non-contact instrument to confirm the item being measured is the correct color. This typically is used when several parts are being assembled together, and a verification that the parts are of the same color is required. Verification is essential when similar colors are used in an assembly process, and the potential for selecting mismatched parts exists.
Prerequisites
The process of using color verification begins with several assumptions. First, it is assumed that the parts have been quality controlled for color and are known to be good, from a color perspective. This does not mean that every part has been measured, but simply that standard quality control procedures have been followed, and the parts are within tolerance.
Next, it is assumed that the parts being verified can be fixtured or presented in a uniform, repeatable manner to the instrument. It is common that all of the parts of the final product are loaded into an assembly fixture, and then verified for color, prior to the completion of the assembly.

The Problem
The issue of metameric colors is at the heart of the problem in these assembly processes. Metameric colors are different colors that appear to be the same under some set of conditions. This is a fairly common problem accentuated by the poor color quality of the lighting used in most production facilities. A human operator may struggle with being able to discern between two very close colors in this environment.
As an example of metamerism, Figure 1 shows the color swatches of two different colors as they would appear under typical production floor lighting.
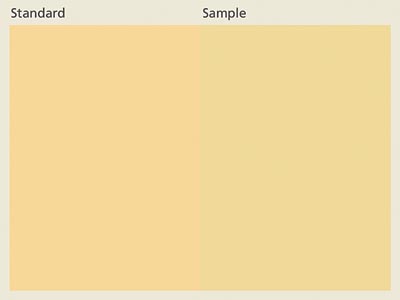
Looking at these two examples, it is easy to understand how a human operator might select parts of these two different colors as the same, leading to a product that might appear to be good, but will ultimately be rejected by the customer.
In addition to metamerism, a human operator's color vision can be affected by many things, including retinal fatigue. Retinal fatigue occurs when a person views the same color for extended periods of time. As the retinal fatigue becomes greater, the person's ability to distinguish between similar colors lessens, leading to more mismatched parts.
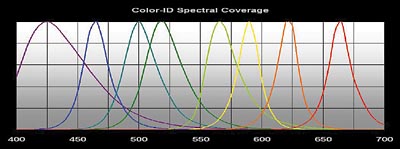
The Solution
The equipment used for color verification includes an instrument or measurement sensor head for each part that needs to be verified. Fixtures that hold the parts in place as well as holding the instruments in place also are required. Robots also can be used for this purpose. Typically, the instrument feeds information to a programmable logic controller (PLC). The PLC can then execute some action based on the instrument's input. The instrument also may communicate directly to a PC.Traditional instruments used for this purpose were quite limited. They could discern between three learned colors at a time, provided the colors were considerably different. These devices were simple RGB-based instruments and were susceptible to misidentifying metameric colors. They also were greatly affected by variation in sample positioning and ambient light.
New instruments used for this purpose are based on new technology and can discern between 50 learned colors at a time, greatly expanding usability. These instruments are nearly impervious to the effects of ambient light, and their positional sensitivity has been reduced. These new instruments also use advanced optics, which expand beyond the three-dimensional measurement of RGB, to eight different measurement points of color (Figure 3). This new technology provides an instrument capable of discerning the difference between metameric colors. In addition to verification of the parts, some rudimentary color tolerancing also is possible with these new systems.
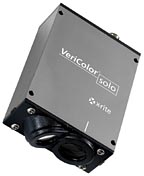
The Process
The process used to verify the color of a product follows several steps. At the end of the finishing stage, the operator can use a color verification system to perform a final quality check for any slight variances in color. It can also detect and report "pass" or "fail" based on the tolerances determined by the quality control professional. Again, its key advantage is its ability to check the color of every part, at each stage of the production process.For color verification once all the parts are at the assembly line, the parts for the product are loaded into the fixture. Then the instrument(s) measure each of the parts, and this measurement is used to determine if all measured parts are the same color, thereby verifying the product. The production can then continue to actually assemble the finished product. All of these actions can be done manually or may be automated and controlled by computers or PLCs.
As an example of the process, let's follow the assembly of a fictitious product that consists of three different painted parts and two plastic parts. The painted parts should all be the same color, while the two plastic parts are in an accent color, but should match one another.
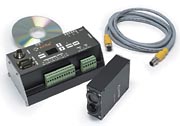
A color verification system can add significant value to the production process, especially when various parts of the same color must be correct at every stage of the process. This technology can reduce color errors, leading to less rejected product and improved efficiency. The latest instrumentation designed for this purpose greatly improves the ability to identify many more colors and to correctly detect the difference between metameric colors.
Looking for a reprint of this article?
From high-res PDFs to custom plaques, order your copy today!