Fluid Control
In the two decades plural-component coatings have been used in manufacturing, they have become the first choice for many manufacturers for their abrasion resistance, durability and color quality. However, like other high-performance coatings, achieving the optimal properties requires the right fluid handling equipment.
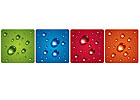
In the two decades plural-component coatings have been used in manufacturing, they have become the first choice for many manufacturers for their abrasion resistance, durability and color quality. Plural-component coatings, particularly those using epoxies and urethanes, are applicable to a wide range of products, from automotive interior and exterior components and off-highway and agricultural vehicles, to such consumer products as golf balls.
“Plural-component coatings offer a wide range of benefits to surface finishes, especially on products that will be used in extreme conditions,” says Larry Blum, account manager for ITW Ransburg.
Plural-component finishes possess a range of qualities:
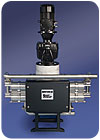
“Because of the variations in pot life among coatings, the location of the mix and metering equipment optimal to their application is critical to the success of the coating operation,” Blum says. “The advantage to mixing at the applicator is when the pot life of the mixed material is very short, or when color changes are not required,” he explains. “Mixing near the metering equipment reduces the effect of differing viscosities, hose length and volume, flow versus pressure drop, high ratios and pressure differential between the components.”
Blum recommends the use of coating systems that closely monitor the amount of material being mixed at any one time, and that can be used in low to high pressure operations.
“These systems provide high productivity, consistent quality and optimum fluid delivery. In addition, the systems produce much less waste for disposal, along with lower volatile organic compound (VOC) emissions and lower cure temperatures,” he says.
Coating equipment typically is divided into three categories, according to Blum: dosed metering systems, air-piloted servo-valve coating systems and gear pump systems. Dosed metering systems offer the lowest-cost solution for coating operations, but often don’t allow for precision control, and they typically result in more waste. Air-piloted servo-valve coating systems are effective in high-pressure applications, while precision gear pump systems can be used in most low-pressure applications.
“Look for control systems that optimize color change, flushing and load sequences. In addition, the color pump should be flushable for no color carryover,” says Blum.
Advanced fluid management systems are designed to optimize the efficiency of the materials and equipment, minimizing waste, downtime and changeover.
“We do a lot of work with epoxy and urethane coatings, and we recommend use of positive displacement gear pumps,” Blum says.
Golf balls, for example, require critical weight control over coating materials. This control is maximized through efficient fluid management equipment, including adaptability to rotary atomizers, bells, disks and electrostatic or non-electrostatic spray guns. Flow and ratio should be controllable for either manual or handgun application.
When considering plural-component coatings, don’t overlook the fluid handling equipment. The right equipment can make all the difference in achieving an efficient, high-quality finish.
ITW Ransburg, an Illinois Tool Works Company, develops custom electrostatic coating system configurations based on the coating selected and the need for color changeover. For more information, call 800.909.6886 or 419.470.2000, or visit www.itwransburg.com.
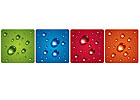
In the two decades plural-component coatings have been used in manufacturing, they have become the first choice for many manufacturers for their abrasion resistance, durability and color quality. Plural-component coatings, particularly those using epoxies and urethanes, are applicable to a wide range of products, from automotive interior and exterior components and off-highway and agricultural vehicles, to such consumer products as golf balls.
“Plural-component coatings offer a wide range of benefits to surface finishes, especially on products that will be used in extreme conditions,” says Larry Blum, account manager for ITW Ransburg.
Plural-component finishes possess a range of qualities:
- Excellent durability in varied weather conditions
- Critical gloss controls (ranging from low to high gloss finishes)
- Resistance to becoming brittle as it ages
- Adhesion to a wide range of substrates, including most plastics and metals
- Superior flexibility, along with impact and chip resistance
- Flexibility in curing temperature and time
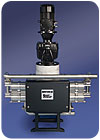
Advanced fluid management systems are designed to optimize the efficiency of the materials and equipment, minimizing waste, downtime and changeover. Shown is ITW’s Smart Pump.
Defining an "Efficient" System
Efficient plural-component coating operations use cutting-edge fluid handling systems that eliminate concerns of pot life while simultaneously reducing the amount of waste produced.“Because of the variations in pot life among coatings, the location of the mix and metering equipment optimal to their application is critical to the success of the coating operation,” Blum says. “The advantage to mixing at the applicator is when the pot life of the mixed material is very short, or when color changes are not required,” he explains. “Mixing near the metering equipment reduces the effect of differing viscosities, hose length and volume, flow versus pressure drop, high ratios and pressure differential between the components.”
Blum recommends the use of coating systems that closely monitor the amount of material being mixed at any one time, and that can be used in low to high pressure operations.
“These systems provide high productivity, consistent quality and optimum fluid delivery. In addition, the systems produce much less waste for disposal, along with lower volatile organic compound (VOC) emissions and lower cure temperatures,” he says.
Coating equipment typically is divided into three categories, according to Blum: dosed metering systems, air-piloted servo-valve coating systems and gear pump systems. Dosed metering systems offer the lowest-cost solution for coating operations, but often don’t allow for precision control, and they typically result in more waste. Air-piloted servo-valve coating systems are effective in high-pressure applications, while precision gear pump systems can be used in most low-pressure applications.
“Look for control systems that optimize color change, flushing and load sequences. In addition, the color pump should be flushable for no color carryover,” says Blum.
Advanced fluid management systems are designed to optimize the efficiency of the materials and equipment, minimizing waste, downtime and changeover.
“We do a lot of work with epoxy and urethane coatings, and we recommend use of positive displacement gear pumps,” Blum says.
Golf balls, for example, require critical weight control over coating materials. This control is maximized through efficient fluid management equipment, including adaptability to rotary atomizers, bells, disks and electrostatic or non-electrostatic spray guns. Flow and ratio should be controllable for either manual or handgun application.
Improving Control
An effective fluid management system can help a coating line minimize energy consumption, solvent use, equipment wear and maintenance. It also can help reduce paint waste and shear, thereby improving process control.When considering plural-component coatings, don’t overlook the fluid handling equipment. The right equipment can make all the difference in achieving an efficient, high-quality finish.
ITW Ransburg, an Illinois Tool Works Company, develops custom electrostatic coating system configurations based on the coating selected and the need for color changeover. For more information, call 800.909.6886 or 419.470.2000, or visit www.itwransburg.com.
Looking for a reprint of this article?
From high-res PDFs to custom plaques, order your copy today!