Structured Nano-Acrylic Polymers


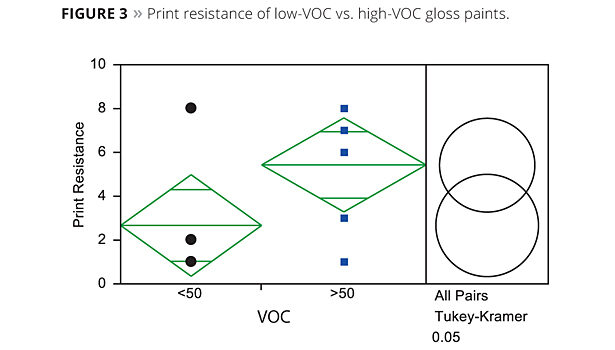
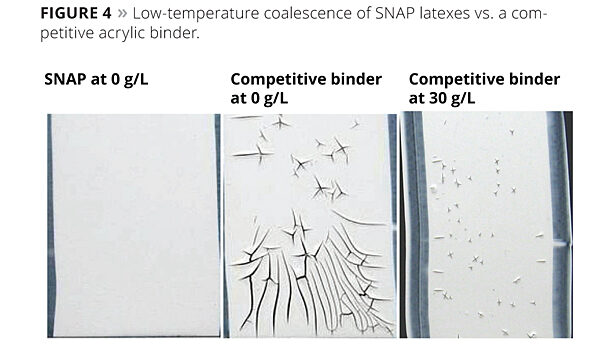
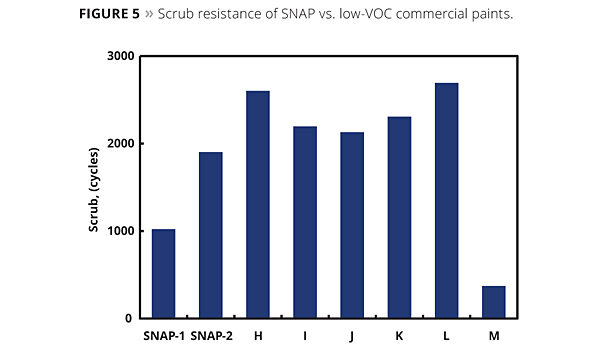
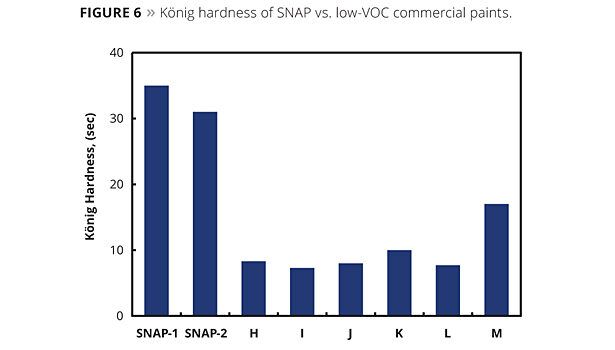
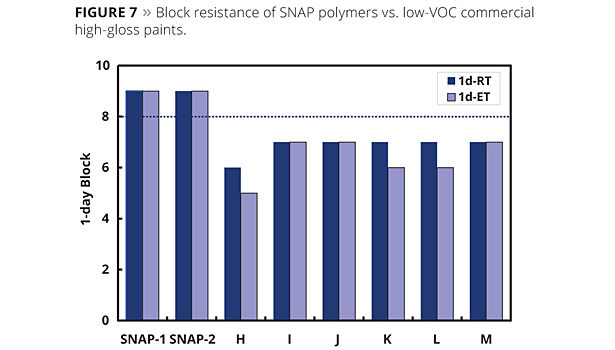

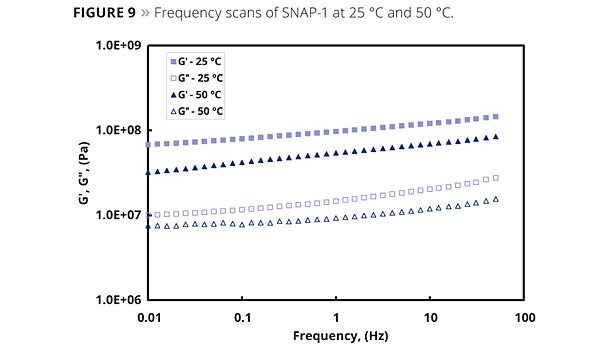
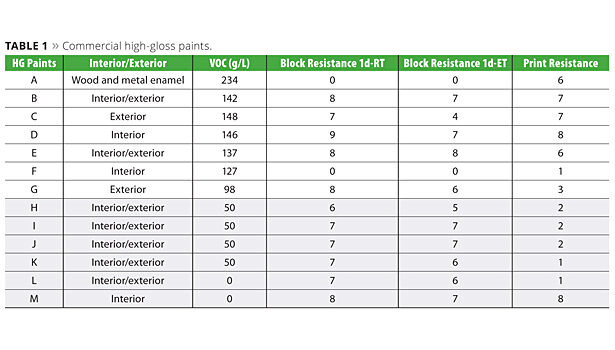
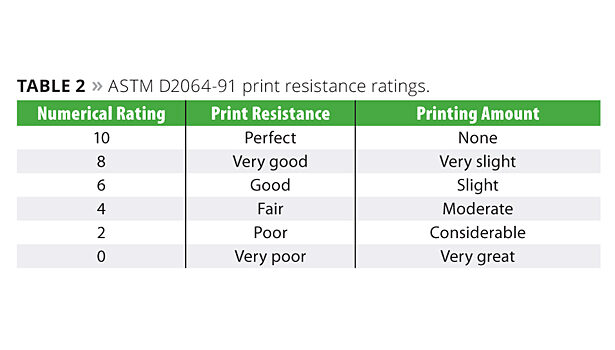











Driven by low-VOC requirements, softer polymers with low minimum film formation temperature (MFFT) are being utilized in waterborne architectural coatings. An obvious drawback of such soft binders is poor film hardness, which impacts many important resistance properties, such as block, print, scratch, abrasion and dirt pickup. Poor antiblocking characteristics cause the two contacting surfaces (for example, newly painted doors and windows) to stick, resulting in tearing or peeling of the paints upon separation. Print resistance measures the resistance of coating films to deformation from objects (for example, picture frames) placed on top of the coating.
The coatings industry has made great strides in enhancing the performance of low-VOC waterborne coatings. Blending a soft, film-forming latex with a small-particle-size, high-Tg modifier has been a common practice to enhance block resistance and wet adhesion properties.1-8 However, inherent incompatibility between most polymer pairs in general hinders the development of cohesive strength as reflected in decrease of scrub resistance.9 A more elegant approach to fulfilling the contradictory requirements of film formation and hardness is to design structured emulsion polymers with internal hard and soft domains inside the latex particle.10-15 Yet, antiblocking and print resistance are still found to be deficient because most self-filming binders have limited potential to develop adequate bulk modulus and surface hardness. Additionally, such multiphase particles often compromise scrub durability, attributable to inherent incompatible compositions of different polymer phases.
This article introduces a novel acrylic latex technology based on structured nano-acrylic polymers (SNAP™). Since high-gloss applications demand the highest polymer performance due to higher binder usages and the requirement of defect-free film formation for gloss development, the benefits of SNAP technology are highlighted in a high-gloss formulation. Their key performance properties are compared to the state-of-the-art, low-VOC high-gloss products. This innovative acrylic technology enables coatings formulators to develop zero- or low-VOC, high-performance paints for non-flat finishes on trim, wood and walls.
Experimental
High-Gloss Paints
Two example SNAP latexes (SNAP-1 and SNAP-2) were evaluated in a solvent-free, high-gloss formulation with 17% pigment volume concentration (PVC) and 38% volume solids. The formulated paints based on this new technology were compared to commercial products labeled as high-gloss paints. Thirteen commercial high-gloss paints were purchased for the benchmarking study. Table 1 summarizes their recommended application areas (interior vs. exterior), VOC levels, 1-day block resistance at room and elevated temperatures, and print resistance.
Low-Temperature Coalescence (LTC)
Film formation and mud cracking at a low temperature (40 ºF) indicate the degree of coalescence of latex paints. Drawdown films were prepared on Leneta 1B opacity charts using a 10-mil bird applicator for LTC and a 25-mil square bar for mud cracking tests, respectively. The paint films were placed in a 40 ºF refrigerator immediately after the films were drawn down and dried for 24 h. The dried films were examined for continuity; degree of cracking on the sealed and unsealed portions was rated on a 1 to 5 scale (1 = severe cracking; 2 = moderate cracking; 3 = some cracking; 4 = slight cracking; 5 = no cracking).
Scrub Resistance
Relative scrub resistance was evaluated on the Garner Straight Line Washability and Wear Abrasion Machine. Coatings were applied at a wet film thickness of 7 mils over Leneta black plastic charts and dried for 7 days at controlled temperature and humidity (CT/CH: 77 °F and 50% relative humidity). The nylon bristle brushes were conditioned by running 400 cycles before the test began. A standardized abrasive scrub media (#SC-2 from the Leneta Company) was used. The test included the additions of 7 mL of scrub media and 5 mL of water at the beginning and after every 400 cycles. Testing was done in triplicate and the number of cycles to failure was recorded. A semigloss acrylic paint was employed as the scrub control on each test panel.
Block Resistance
Test paints were prepared on Leneta 1B opacity charts using a 3-mil bird drawdown bar. Films for room temperature (RT) block were dried in the CT/CH chamber for 1 day. Two square strips of 2.54 cm x 2.54 cm were placed together with paint film against paint film under a 454-gram weight. After 24 h, the strips were separated and evaluated. For the elevated temperature (ET) block test, the paint strips after 1 day drying at CT/CH were placed in a 120 ºF oven for 30 min. The weight load of 1000 gram was transferred to the paint films via a 2.54-cm diameter rubber stopper. The films were cooled for 30 min before the block ratings were given. Room and elevated temperature block were rated on the ASTM D-4946 scale from 0 to 10. The test was run in triplicate and the average value reported.
Print Resistance
Print resistance measures the amount of imprint left by objects placed on top of the coating due to deformation of the coating films under weight. Paints were drawn down on Leneta 3B charts using a 6-mil bird bar and dried for 7 days in the CT/CH chamber. A piece of cheesecloth was placed on the drawdown film and a 500-gram weight transferred to the film via a No. 8 rubber stopper, creating a pressure of about 0.9 psi (or 6.2 kPa). This assembly was conditioned in a 120 °F oven for 1 h and then allowed to cool. The rating of an impression resulting from the paint film being in contact with the cheesecloth was given. The numerical scale of 0 to 10 corresponds to the scoring system specified in the ASTM D2064-91 method (Table 2).
König Pendulum Hardness
König pendulum was employed to measure hardness of coating films following ASTM 4366. Paint films were prepared on 3-inch by 12-inch glass plates using a 10-mil drawdown bar and dried for 7 days. The dry film thickness was approximately 4 mils. The König pendulum resting on the coating surface was set into oscillation (rocking), and the time in seconds for the swing amplitude of the pendulum to decrease from 6° to 3º was recorded.
Dynamic Mechanical Analysis (DMA)
An AR-1000 rheometer (TA Instruments) was utilized for dynamic mechanical analysis. Frequency sweeps from 0.01 to 628 rad/sec were performed on solid rectangular samples of SNAP latex films. The storage modulus (G’), loss modulus (G”) and tan δ were measured.
Results and Discussion
Benchmarking Commercial High-Gloss Paints
Among the 13 commercial paints examined, six were formulated at VOC less than 50 g/L. In fact, two out of the six low-VOC paints were advertised to be VOC-free. Seven of the high-gloss paints were classified for both interior and exterior applications. The low-VOC products, for the most part, performed similar to, or better than, the conventional high-gloss paints. The greatest improvement areas were scrub resistance and elevated temperature block.
Figure 1 compares scrub resistance of low-VOC vs. high-VOC commercial high-gloss paints. All but one low-VOC paint scrubbed 2000 or more cycles, whereas the high-VOC paints averaged around 567 scrub cycles. This data suggests that a strong emphasis has been given to improve durability of low-VOC paints since scrub resistance is one important aspect of durability, especially for interior applications.
Block resistance is a key performance requirement for gloss and semigloss paints. The block resistance data compiled in Table 1 indicates that even high-VOC conventional formulations do not possess perfect block resistance. The 1-day room temperature block resistance ranks from 0 to 8, with an average value of 5. The elevated temperature block in general is poorer than the room temperature ratings. Paints A and F, two higher-VOC-containing products, received the lowest antiblocking ratings of zero at both room and elevated temperatures. The six lower-VOC products fall in a narrow range of 5 to 7 (Figure 2). Comparatively, the block ratings of higher VOC products displayed a substantially wider spread.
Both interfacial energy and polymer cohesive strength affect block resistance. For example, harder binders with higher modulus have better antiblocking properties because polymer cohesive strength increases with increasing polymer Tg. The degree of interdiffusion also decreases due to less free volume and more restricted chain mobility. Both of these factors improve antiblocking properties. For the same reasons, the low-VOC-capable polymers inherently block or adhere more easily. Plastic deformation causes the soft polymers to have intimate contact, thereby increasing contact area and promoting interdiffusion, especially in high temperature and pressure situations. Furthermore, the polymers have good compatibility and, therefore, good adhesion because the two contacting surfaces are chemically identical. Consequently, film surface characteristics such as surface energy and morphology of the contacting surface areas can play more important roles in block resistance of low-VOC coatings.
Print resistance is more directly related to the modulus of the paint films. Not surprisingly, lower-VOC products are generally inferior to the higher-VOC paints, as shown in Figure 3. High-VOC paints usually employ higher Tg binders that can offer greater film hardness and thus higher print resistance. However, paint M, a zero-VOC product, scored an encouraging 8, suggesting that it is possible for low-VOC binders to match the performance of high-VOC products, including print resistance.
SNAP Technology
The biggest challenge for low-VOC binders and paints is to simultaneously satisfy the demands of excellent film formation, film hardness and durability. The structured nano-acrylic polymer (SNAP) technology represents an innovative solution that promises to raise the performance standards of low-VOC paints. Synthesis of structured latex particles has been explored previously to balance film formation and hardness.10-15 However, the results from the benchmarking study of commercial paints indicated that antiblocking and especially print resistance are still hard-to-attain film properties of low-VOC waterborne coatings.
The SNAP technology involves a sophisticated multi-stage emulsion polymerization process that allows the production of nano-sized acrylic particles at low viscosity (<500 cPs) and practical solids content (49%). Unique hard and soft polymer phases created by unconventional compositional designs are responsible for unparalleled film hardness and good low-temperature coalescence (LTC). Two of the example latexes designated as SNAP-1 and SNAP-2 are discussed below.
Film Formation
The SNAP technology enables zero-VOC paints to form continuous and smooth films, even at low temperatures. The pictures in Figure 4 illustrate its low-temperature coalescence ability compared to a competitive acrylic binder in the same high-gloss formulation. Smoothness of the paint film surface is essential for high-gloss development. When compared to low-VOC commercial paints, SNAP-2 indeed produced the highest 20° gloss.
Scrub Durability
Scrub resistance is an indication of mechanical integrity and energy absorbing capacity of the paint films. Scrub durability is thus related to toughness and elasticity of the coating film. Typically, it increases with decreasing PVC or increasing binder usage. Good scrub resistance allows the painted surfaces to be cleaned without being damaged. Figure 5 shows that SNAP latexes offer similar scrub performance to current commercial low-VOC paints. The low-VOC paints, except M, all exhibit very good scrub durability.
König Hardness of Paint Films
Exceptional film hardness is the most remarkable feature of the SNAP technology. The pendulum damping test has been found to have good sensitivity in detecting differences in coating hardness, where hardness is defined as resistance to deformation. Figure 6 displays the oscillation times the König pendulum registered on the SNAP and commercial paint films. The pendulum hardness test is based on the principle that the amplitude of the pendulum’s oscillation decreases more quickly on a softer surface. For five of the commercial paints, the oscillation time is less than 10 seconds at ~4 mil dry film thickness. The König hardness of two SNAP-based paints is three times the average value and doubles the readings of the best low-VOC paint, M.
Block Resistance
Figure 7 plots the ratings of 1-day block resistance at room and elevated temperatures. The commercial products exhibit similar block resistance within a small range from 5 to 7. No direct correlation can be made between the hardness data (Figure 6) and block resistance (Figure 7). It is apparent that bulk property is not the only factor affecting block resistance, and the contribution of the surface component should not be overlooked. Nevertheless, the two example SNAP latexes display outstanding pendulum hardness and block resistance, exceeding the commercial high-gloss products we tested in the North American marketplace.
Print Resistance
Interior gloss and semigloss paint systems on window sills and other horizontal surfaces often have objects such as flower pots or picture frames placed on them that may leave a permanent impression. Relative to block resistance, print resistance appears to be a greater challenge for high-gloss paints. The performance gap is more profound for low-VOC paints (Table 1).
The average print resistance score of the lower-VOC paints is only 2.7 on the scale from 0 to 10. Paint M scored the highest print resistance rating of 8. Unfortunately, this paint has the lowest scrub resistance among the lower-VOC products (Figure 5). As shown in Figure 8, the SNAP polymers produced perfect scores in the print resistance test without compromising scrub resistance. This is a significant improvement over the current low-VOC high-gloss products. In fact, they outperform even the conventional, high-VOC binders in block and print resistance. Both block and print resistance results clearly demonstrate the advantages of SNAP technology over the low-VOC commercial high-gloss paints.
Compared to block resistance, print resistance is more closely related to bulk hardness, whereas block resistance can be enhanced through modifications of paint surface properties. Print resistance, like pendulum hardness, also depends on viscoelastic properties of the coating film.
Dynamic Mechanical Analysis
Exceptional hardness of the SNAP technology can be attributed to unique viscoelastic properties of the multiphase polymer. DMA is widely used to characterize the viscoelastic behavior of materials. The response of materials as a function of oscillation frequency reflects the contributions from different mechanisms at the molecular and microscopic levels. In an oscillatory frequency sweep, the crossover frequency at which the elastic modulus (G’) equals viscous modulus (G”) usually marks the onset of the flow region. The frequency scans of SNAP-1 polymer at 25 °C and 50 °C display no crossover points in the entire frequency range from 0.01 to 100 Hz (Figure 9). In addition to the absence of a crossover frequency, the storage modulus is almost an order of magnitude higher than the loss modulus. When tan δ (G”/G’) is low, the elastic behavior dominates and the material is less likely to deform permanently. A large separation between G’ and G” remains even at 50 °C; the elastic modulus is consistently higher than the viscous modulus. Also, 50 ºC is close to the testing temperatures for hot block and print resistance. These two sets of data in Figure 9 demonstrate that SNAP technology produces stiff polymer films which, in turn, result in outstanding block and print resistance performance.
Conclusion
SNAP is an exciting technology innovation that fills the unmet needs of low-VOC waterborne coatings. Through creative designs of polymer composition and particle morphology, the resulting polymers are able to form smooth, coherent films in the absence of coalescing solvents or plasticizers, and at the same time deliver exceptional film hardness. The benchmarking results presented in this article clearly demonstrate the performance advantages of SNAP technology over the low-VOC commercial products tested.
While designed for architectural coatings, SNAP technology also offers the same performance benefits for other applications where film hardness and/or high gloss are desired properties, such as floor, wood and concrete coatings.
References
1. Boyce, C.A.; Farwaha, R,; Licht, B.H.; Menard, M. US 5,208,285.
2. Feng, J.R.; Winnik, M.A. Polymer blend latex films: morphology and transparency, Macromolecules 28,7671-7682 (1995).
3. Winnik, M.A.; Feng, J.R. Latex blends: An approach to zero-VOC coatings, J. Coatings Technology 1996, 68(852), 39-50.
4. Eckersley, S.R.; Helmer, B.J. Mechanistic consideration of particle size effects on film properties of hard/soft latex blends, J. Coatings Technology 1997, 69(864), 97-107.
5. Friel, J.M. EP 466409A1,
6. Robeson, L.M.; Vratsanos, L.A.; Miller, S.A. US 6,656,998.
7. Satgurunathan, R.; Bouman, J.; and Gould, A.J. WO 03/031526A1.
8. Gebhart, M.S.; Fradkin, E.G.; Baker, B.E.; Friel, J.M.; Edwards, S.S.; Puschal. A.A.; Eckert, C.; Even, R.C. US 6,930,141 B2.
9. Wu, W.; Olesen, K.R.; Miner II, A.R.; and Schneider, J.A. Blending Vinyl Acetate-Ethylene and Acrylic Latexes to Achieve Targeted Performance Properties, JCT -CoatingsTech. 2008, 5(5), 44-52.
10. Holub, P.; McEntire, E.E. US 2005/107527A1.
11. Enelie, B.; Hiff, T.; Gopsill, C.; Schuster, U. WO 9833831.
12. Farwaha, R.; Phan, L.; Currie, W.; Tinamissan, J.M. EP 609756A2
13. Bardman, J.K.; Even, R.G.; Frazza, M.S.; Guo, Y.; Krasnansky, R.; EP 1008635B1.
14. Sakaguchi, S.; Takamatsu, A.; Sasaki, H.; Tsuneta, K. EP 11167477B1.
15. Schuler, B.; Baumstark, R.; Kirsch, S.; Pfau, A.; Sanfor, M.; Zosel, A. Structure and properties of multiphase particles and their impact on the performance of architectural coatings, Progress in Org. Coatings 2000, 40, 139-150.
Looking for a reprint of this article?
From high-res PDFs to custom plaques, order your copy today!