Exploring the Chemistry Behind Silicone-Based Release Additives

The need for certain release properties can be found in numerous everyday applications, as well as in industrial applications.1 Depending on the nature of these applications, different levels of the release effect are desired, and demands regarding durability of the release effect vary substantially. Therefore, it makes sense to take a closer look at the specialty additives that create this effect.
In the first section of this article, the chemical background of this additive class is explained. The second section explains the mode of action in typical release additive applications and the basic effects of different types of silicone-based release additives. Finally, the basic formulation principles are explained.
Chemical Background
The most simple route to a silicone-based release additive is to obtain polydimethylsiloxane (PDMS) from dichlorodimethylsilane (Figure 1), which is readily available via the Müller-Rochow synthesis2 on industrial scale, via a hydrolysis-condensation reaction (Figure 2).3
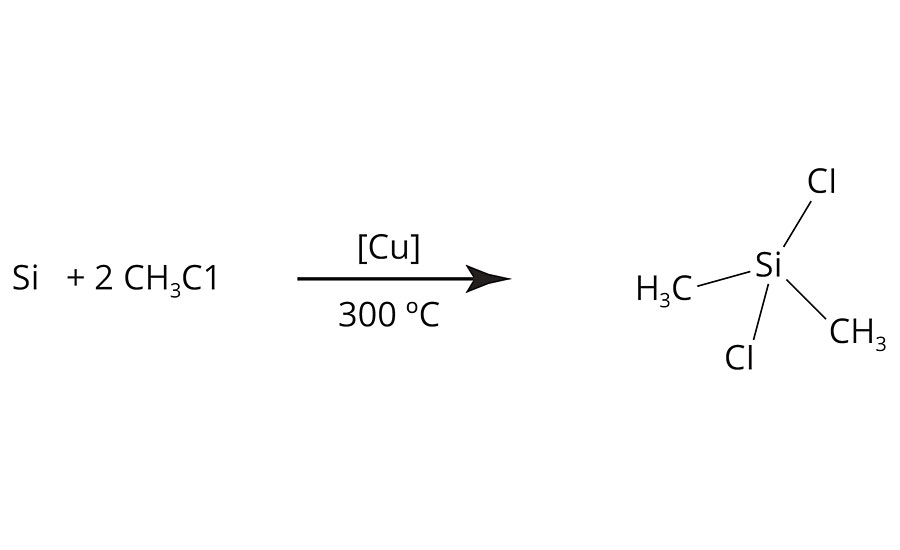
FIGURE 1 » Synthesis of dichlorodimethylsilane via the Müller-Rochow synthesis.
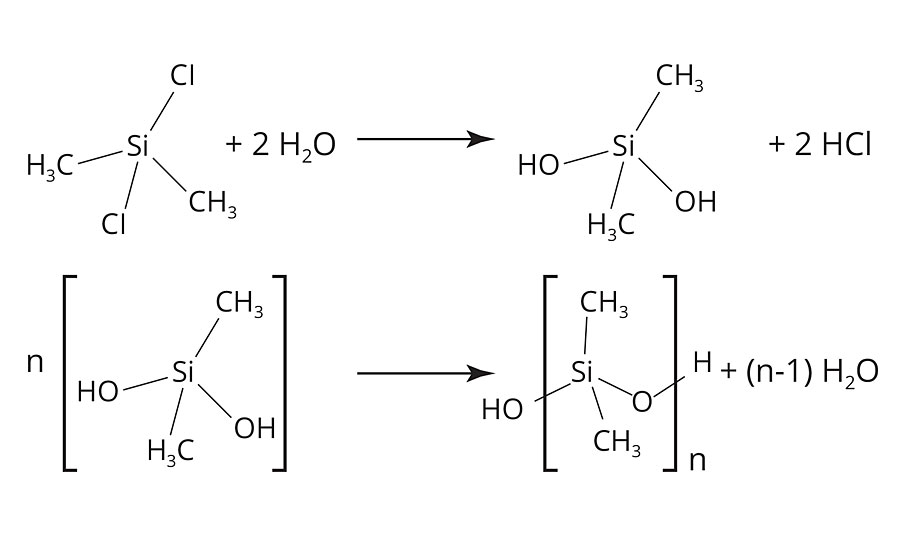
FIGURE 2 » Synthesis of polydimethylsiloxane via a hydrolysis-condensation reaction.
The obtained PDMS typically consists of 30-50 repeating units. For further fine-tuning of the polymer, equilibration processes are utilized. Under the influence of catalysts, the PDMS polymers are forced into a condensation (water removal) reaction; this yields a PDMS polymer with a higher number of repeating units (Figure 3).4
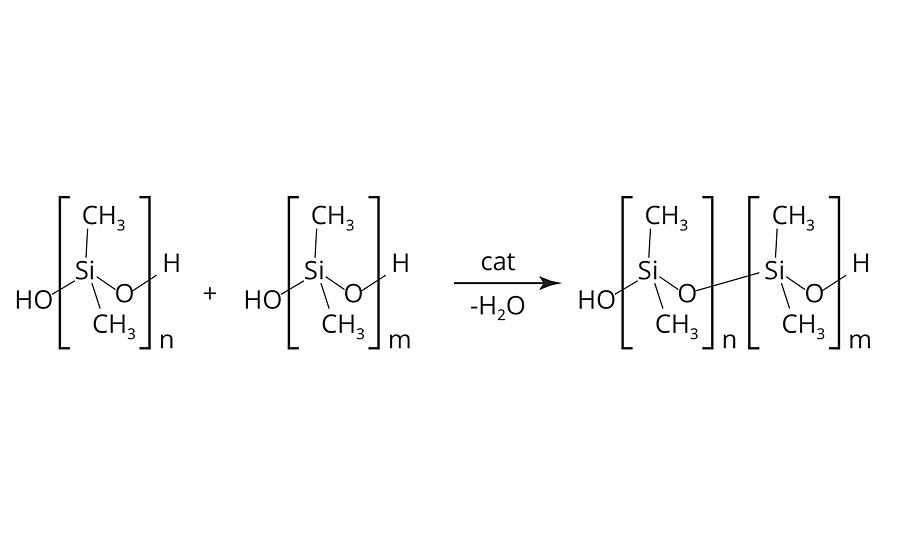
FIGURE 3 » Condensation reaction of polydimethylsiloxanes
The condensation reaction is terminated by the addition of “end cappers,” such as (H3C)3Si-O-Si(CH3)3. Thus, the number of repeating units and the molecular weight of the PDMS are controlled (Figure 4). Alternatively, the termination of the condensation may also be established with mono-functional chloroalkylsilanes (Figure 5).5
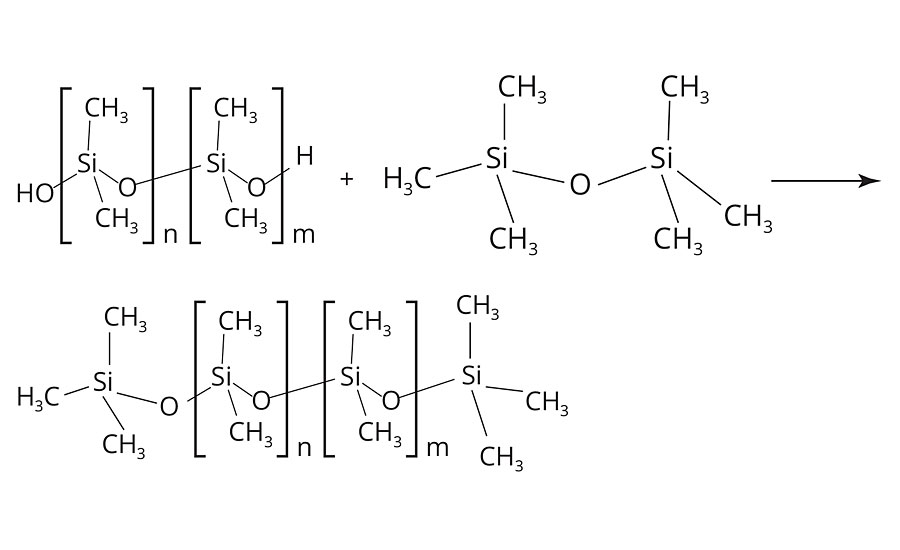
FIGURE 4 » Termination of the condensation reaction of polydimethylsiloxanes via “end cappers”.
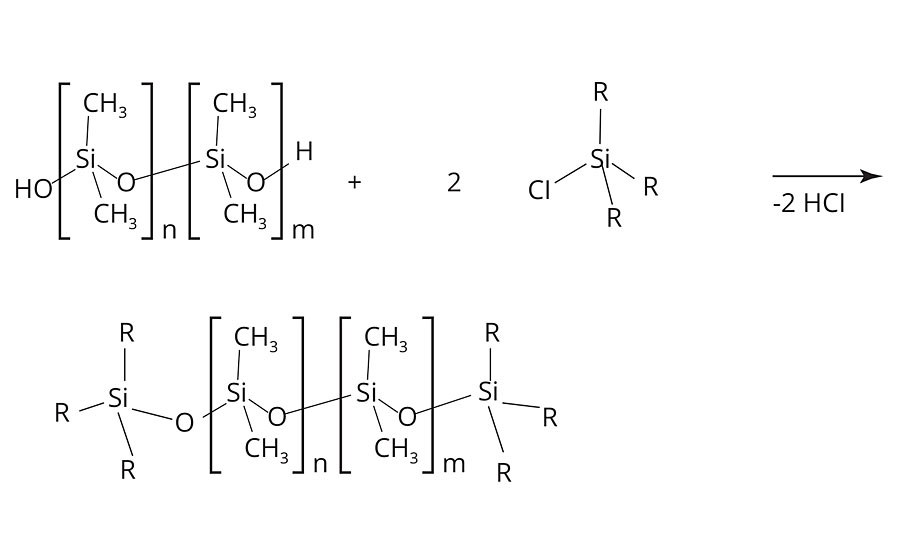
FIGURE 5 » Termination of the condensation reaction of polydimethylsiloxanes via mono-functional chloroalkylsilanes.
The PDMS obtained via these synthesis routes are noncrosslinkable. This results in a migration tendency mainly influenced by the molecular weight of the molecule, the compatibility of the PDMS with the coating formulation and the coating formulation itself. The most basic way to modify the molecular weight was described in the previous section. The compatibility of silicone release additives can be modified by changing two parameters: the length of the siloxane chain and the degree of organic modification. Regarding the former, the release effect increases as the length of the siloxane chain increases. At the same time, the compatibility decreases. Regarding the latter, the compatibility increases as the degree of organic modification increases. Furthermore, the better the polarity of the organic modification matches the polarity of the coating formulation, the higher the compatibility.
To obtain crosslinkable siloxanes, acrylate functionalities are introduced into the polymer.6 In principle, two main options for the modification are possible:
- modification at the backbone of the polymer chain, which yields comb-like structures
- modification at the ends of the polymer chain, which leads to a a,w-modification (Figure 6)
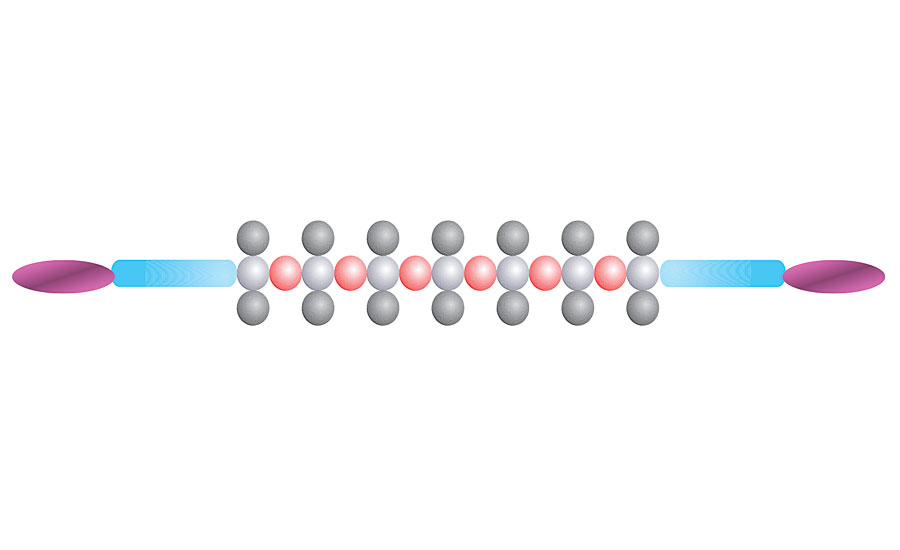
FIGURE 6 » Polydimethylsiloxane with α,ω-modification (organic modification in blue, acrylate groups in purple).
The influence of adequate organic modification on the compatibility is quite apparent when comparing mixtures of modified PDMS/water and pure PDMS/water. The mixture of water with pure PDMS looks turbid, while mixtures of water with adequately modified PDMS remain clear. Figure 7 illustrates this effect.
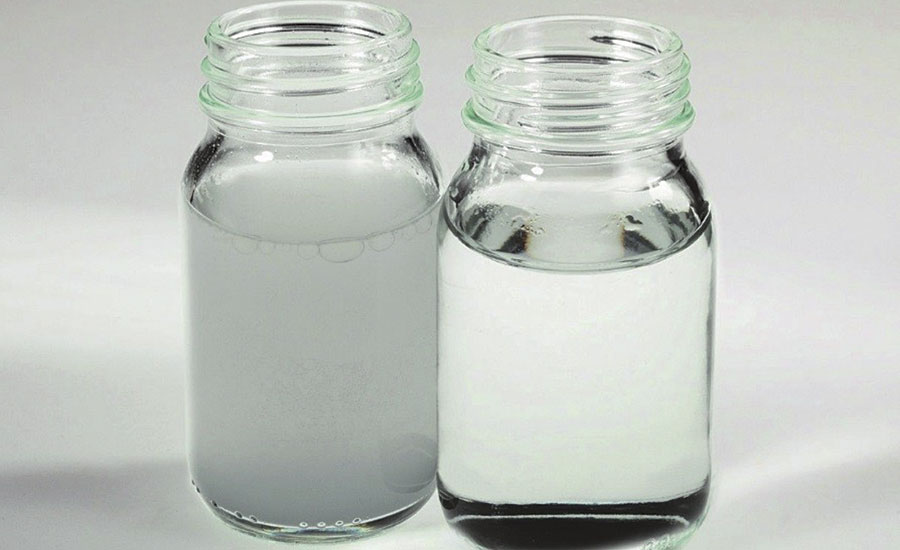
FIGURE 7 » Mixtures of water with pure PDMS (left) and adequately modified PDMS (right).
Mode of Action
As explained in the first section, silicone release additives can be separated into two groups: noncrosslinkable and crosslinkable release additives. In a standard release coating, the noncrosslinkable release additive is partially at the top of the coating surface (Figure 8). When, for example, a label is placed on this coating, the noncrosslinkable release additive migrates (over time) into the glue layer; thus, the release effect is influenced negatively (Figure 9).
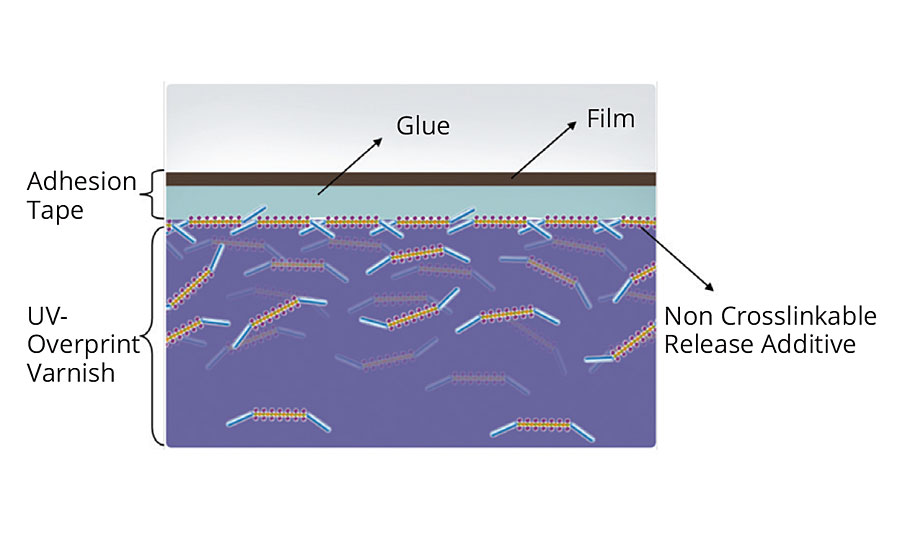
FIGURE 8 » Coating film with noncrosslinkable release additive, covered by adhesive tape.
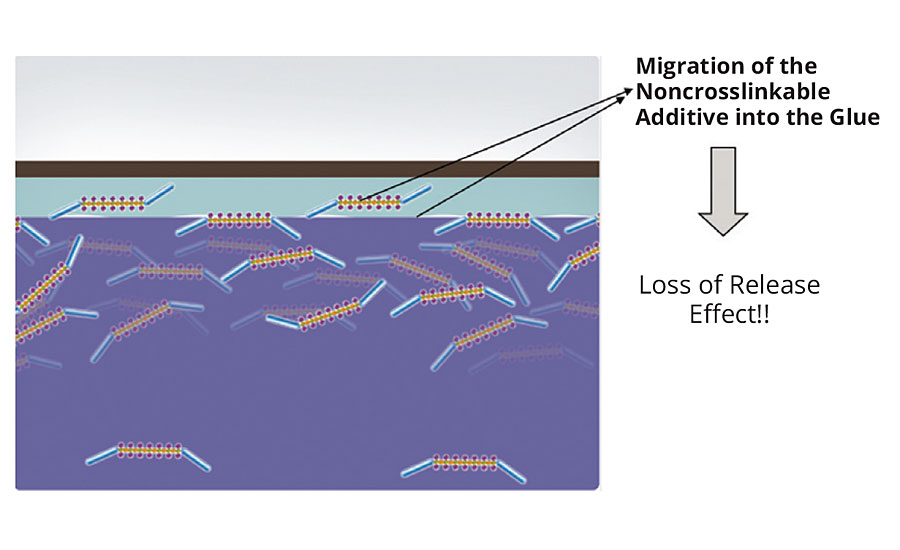
FIGURE 9 » Coating film with noncrosslinkable release additive, covered by adhesive tape; migration of release additive into the glue layer.
If a crosslinkable release additive is used, most of the additive molecules will be permanently anchored due to the crosslinking of the double bonds of the attached acrylate groups. When, for example, a label is placed on this coating, the crosslinked release additive molecules remain in place and do not migrate into the glue layer; thus, the release effect maintains a high level of performance for a prolonged time (Figure 10).
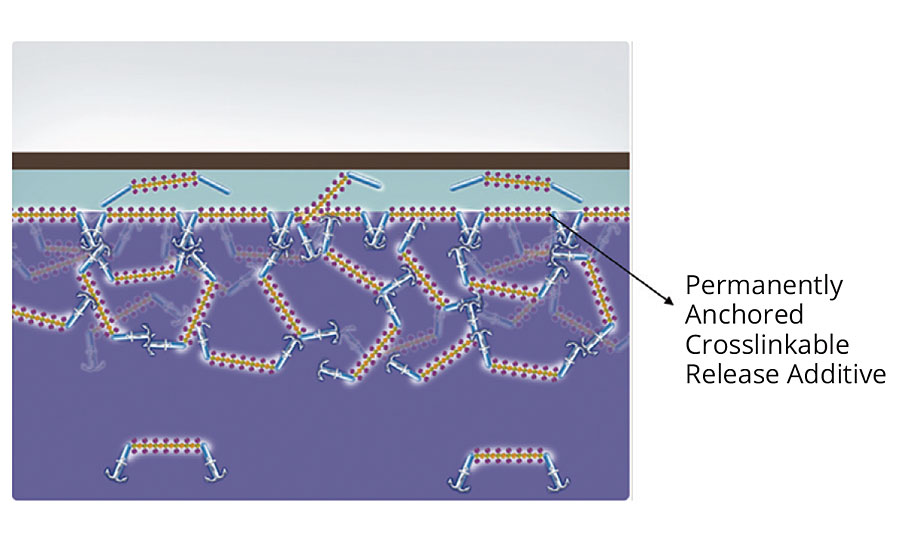
FIGURE 10 » Coating film with anchored crosslinkable release additive, covered by adhesive tape.
Formulation Approach
Crosslinkable release additives are important when long-lasting release effects are required in printing applications. As explained in the previous section, the ability to incorporate the release additive permanently into the coating or ink layer via the crosslinkable acrylate groups offers a major benefit when durability is desired. The acrylate groups form a network with the binder upon radiation curing, thus minimizing the tendency of the additive to migrate. In this way, longer-lasting surface effects can be achieved.
Typical applications for crosslinkable release additives include:
- Wipe-off applications (such as the scratch-off section of a lottery ticket);
- Peel-off application (such as label release or easy-opening packaging);
- Anti-blocking applications (such as blocking prevention in stacked packaging).
In a formulation, the main goal is to level out release properties and maintain a smooth surface. A common approach includes using a combination of radiation-curing additives. Typically, additives that yield good leveling properties are combined with additives that yield excellent release properties. Depending on the formulation and on the polarity of the system, different combinations and ratios of the radiation-curing additives are necessary. The most common approach is to first choose the appropriate release additive, then choose the appropriate combination partner to achieve the desired leveling. Figure 11 illustrates the release effect of various additives. Therefore, if maximal release is desired, Rad 2800 is the product of choice.
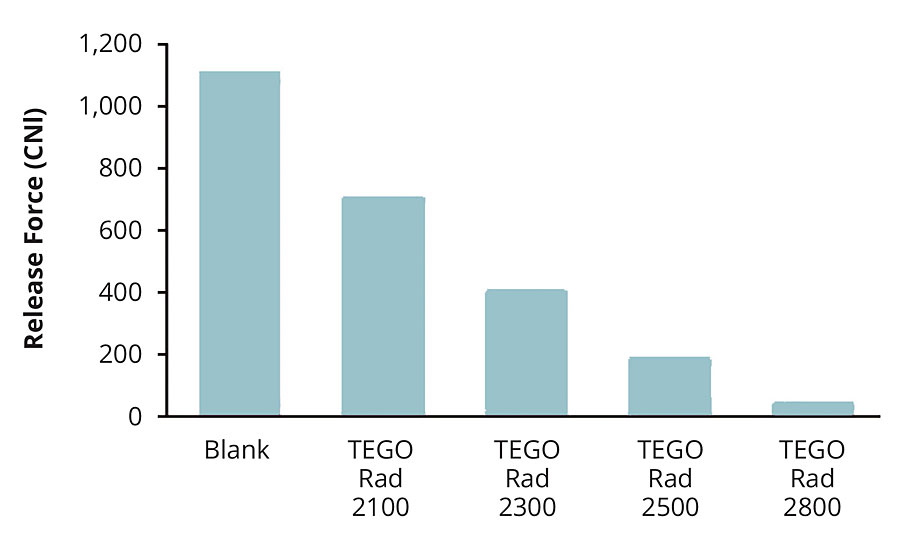
FIGURE 11 » Comparison of the release effect of different TEGO Rad additives.
About Radiation-Curing Additives
Radiation-curing additives are a range of modified silicone-based additives with organic modification. They bear acrylate groups, thus they are crosslinkable, which equips them with unique properties. Depending on the silicone character and on the degree of organic modification, they improve slip, substrate wetting and anti-cratering, scratch resistance, and leveling. Furthermore, some of them have release and defoaming properties.
Summary
The radiation-curing additives are unique because they can be crosslinked into the coating; the resulting glide and release effects are particularly durable. With conventional additives, the release effect is markedly weaker and less permanent because the additives are not crosslinked into the coating.
Rad 2800 is a desirable release additive for printing inks and varnishes. This product displays the highest release effect. It has pronounced silicone character, combining strong hydrophobing properties with optimal system compatibility.
The use of Rad 2200 N, 2250 and 2300 allows formulators to achieve good slip and flow in print varnishes, resulting in defined surface smoothness and good haptic qualities. Because of their outstanding compatibility, their use does not impair transparency. Rad 2500, Rad 2650 and Rad 2800 distinguish themselves particularly by their good release effect, so adhesive strips can be easily detached without leaving residue.
References
1 Glöckner et. Al. Radiation Curing Coatings and Printing Inks; Hannover: Vincentz Network, 2008 (1), p 142ff.
2 Koerner et. al. Silicones; Essen: Vulkan Verlag, 1991 (1) p. 9-15.
3 Brook. Silicon in Organic, Organometallic and Polymer Chemistry; New York: Wiley & Sons, 2000 (1), p. 258ff.
4 Brook. Silicon in Organic, Organometallic and Polymer Chemistry; New York: Wiley & Sons, 2000 (1), p. 261ff.
5 Klotzenburg; et al. Polymere; Berlin: Springer, 2014 (1), p. 204f.
6 Glöckner et. Al.: Radiation Curing Coatings and Printing Inks; Hannover: Vincentz Network, 2008 (1), p 98f.
This article has also appeared in PPCJ and Boytürk magazines.
Looking for a reprint of this article?
From high-res PDFs to custom plaques, order your copy today!