A New Tool for PUD Design

Over the past decades, polyurethane dispersions (PUDs) have increasingly gained attention in the world of material science, leading to a number of developments in several coatings and adhesives applications. This interest for PUDs is supported by the need for eco-friendly products and the trend towards waterborne systems, as well as the constant quest for superior performance. The end-use properties of a PUD are essentially defined by the structure of the polymer, and more specifically by the nature of the building blocks constituting the backbone of the macromolecules, namely diols and diisocyanates. Due to process constraints and application requirements, the choice of diisocyanates entering into the structure of PUDs is often limited to a handful of substances chosen among (cyclo)aliphatic isocyanates.
A few years ago, Vencorex Chemicals launched a new difunctional isocyanate polymer, Tolonate™ X FLO 100, which is generally used as a crosslinker (reactive diluent) in 2K polyurethane systems. In this article we aim to investigate the potential use of its structure in PUD synthesis and the benefits in final material performance.
Introduction
PUDs are flowable, two-phase systems consisting of water and polymer, mainly made from diisocyanates and polyols (macrodiols), as well as other components such as ionizers, neutralizers and chain extenders. The most common diisocyanates used in PUD production are (cyclo)aliphatic isocyanates such as isophorone diisocyanate (IPDI) and methylene bis(cyclohexyl isocyanate) (H12MDI), mostly because of their low reactivity with water, thus enabling PUD production with limited side reaction during the aqueous dispersion phase. In addition, (cyclo)aliphatic isocyanates enable the design of light-stable resins suitable for various applications in the coatings field.
Tolonate X FLO 100 is a partially bio-based, solvent-free and low-viscosity aliphatic difunctional isocyanate (Figure 1). It is particularly designed for producing solvent-free polyurethane and polyurea materials and/or for reducing volatile organic compound (VOC) emissions of polyurethane solvent-based formulations.
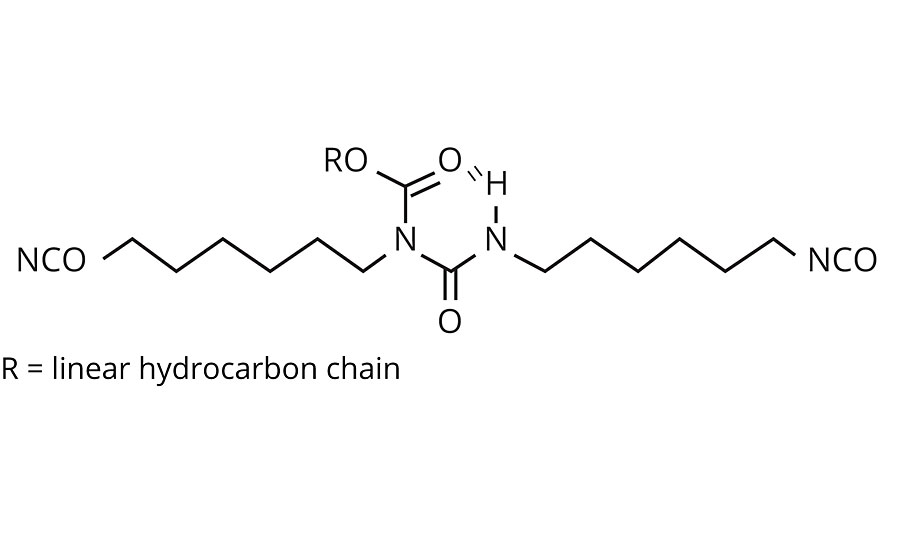
Due to its atypical structure, more specifically the presence of a linear apolar side chain, Tolonate X FLO 100 is often applied for improving flexibility and hydrolytic resistance of the coating when used in the hardener system of conventional 2K polyurethanes. The objective of the present study is to investigate the impact of the Tolonate X FLO 100 structure when used as a building block of a PUD system.
Recently, there has been consistent research to enhance PUD film properties, including flexibility as well as hydrolysis and chemical resistance. The patent of Nakamura et al. (US20110136976) has described PUDs made from H12MDI and polycarbonate polyols, of which elongation at break can be increased up to 47% from a standard recipe. Another patent of Pedain et al. (US 6,248,451/ 2001) has described PUDs produced from 4,4’ diphenylmethane diisocyanate and polyester polyols, with >5% of substances with functional groups similar to that present in the structure of Tolonate X FLO 100. It shows better chemical (ethanol 48%) and hydrolysis resistance of modified PUDs in comparison with conventional PUD recipes. Suitable applications are wood and parquet.
Experimental
The PUD experiment was set up according to the prepolymer mixing process (PMP), which comprises four theoretical steps: (1) polyaddition or prepolymerization in organic phase; (2) neutralization; (3) dispersion of prepolymer in aqueous phase; and (4) chain extension to obtain the final PUDs. The lab equipment for conducting these four steps used in our study included a jacketed stirred-tank reactor with 500-mL operating capacity, bottom outlet and reactor cap with multiple inlets. This reactor was equipped with a heating and cooling bath with an operating temperature range of 10 °C - 120 °C. The anchor-type agitator was applied in order to reduce the rod climbing or so-called “Weissenberg effect” from highly viscous liquids, especially during the chain extension step. Chemicals used in this study are described in Table 1.
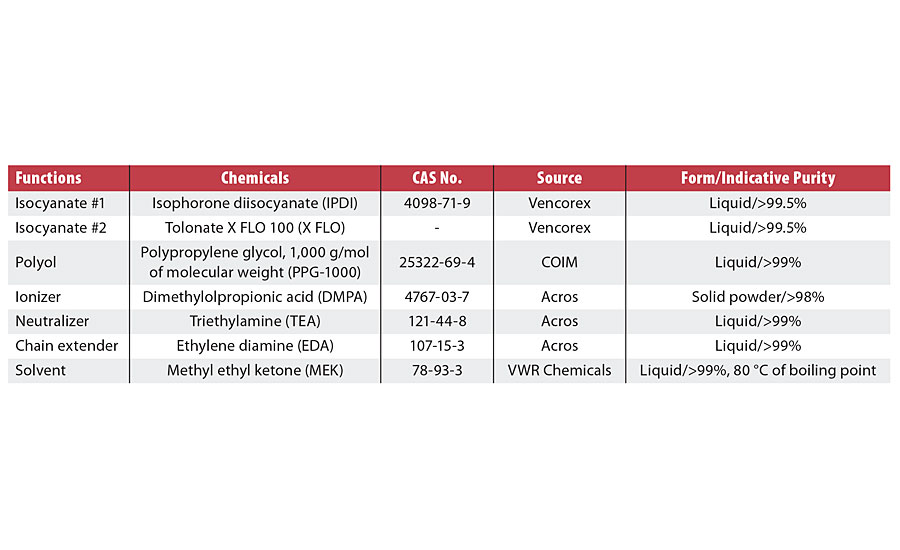
In each set of experiments, 50 g of PPG-1000 were used. The PPG-1000, DMPA and small amount of MEK were introduced into the jacketed stirred-tank reactor and preheated to 60 °C. Then, the isocyanate part was mixed and prepolymerized with the hydroxyl part, PPG-1000 and DMPA, at 80 °C for 4.5 hrs. After that, the prepolymer was cooled down, and made-up MEK was input to reduce prepolymer viscosity. The prepolymer was then neutralized with TEA at 60 °C and further cooled down to below 40 °C before dispersion into water. Water was input from the top of the reactor at the rate of 30-50 mL/min at a high agitation rate at approximately 500 rpm. After the prepolymer and water were visually homogenized in the reactor, diluted EDA was injected for chain extension of the dispersed prepolymer.
The syntheses were carried out using the following parameters: isocyanate:hydroxyl (NCO:OH) ratio = 1.8, DMPA:polyol ratio = 1, neutralization degree (i.e. ratio of amine:carboxylic groups) of 70%. The polymerization in the dispersion phase was conducted until a chain extension degree (i.e. % of NCO groups available after prepolymerization phase that are reacted with EDA during chain extension) of 80% was reached. The final solid content was 35%, with co-solvent content below 4%. The molar ratios of X FLO per total NCO, in the isocyanate part, varied from 0% to approximately 20%. Table 2 summarizes the compositions of the isocyanate parts in the study.
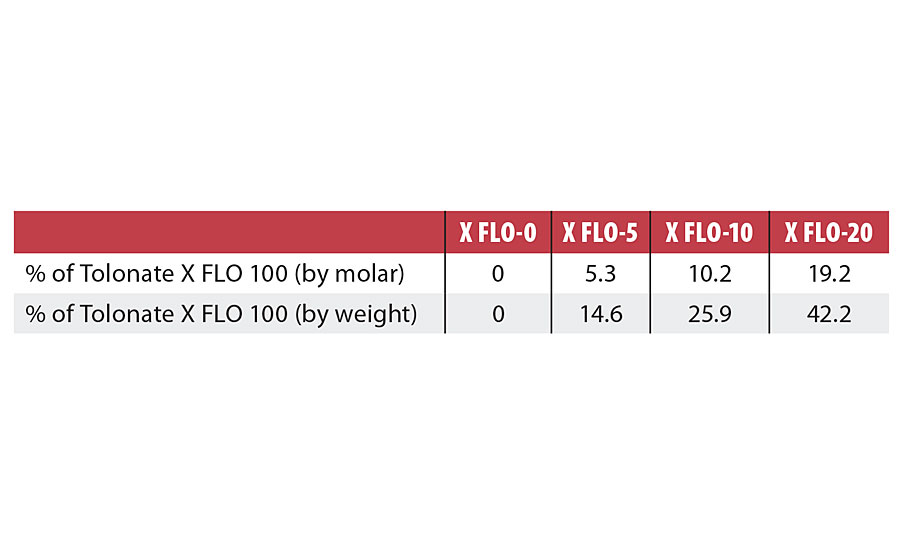
The reaction kinetics during PUD synthesis were studied using Fourier Transform Infrared Spectroscopy in attenuation mode (FTIR-ATR, Tensor 27 from BRUKER). Isocyanate (NCO) groups along the synthesis were followed using the peak at 2,270 cm-1 by FTIR. The data were normalized using the surface of the alkyl functions at 2,800-3,000 cm-1. The measurements made for PUDs in the water phase were subtracted with the standard profile of water. Seven specimens at different times along the PUD synthesis were collected in each experiment to construct a kinetic profile.
The mean particle size and particle size distribution of the final dispersion was measured using a laser diffraction granulometer (Mastersizer 2000 from MALVERN).
The final PUDs were tested after application and drying. Dry films with thicknesses of approximately 60 microns were made by manual applicator on glass substrates, passed through flash-drying, and put in an oven at 80 °C overnight to ensure total drying. The following properties were measured: pendulum (König) hardness, scratch resistance using Taber scratch tester, hydrolysis and chemical resistance (overnight) by water and isopropanol, as well as film gloss (at 20°) and haze using a BYK Gardner 4630. Another set of thick films with estimated thickness of 1 mm was made on flat plates and left in a controlling chamber at 25 °C for at least 5 days to minimize trapped bubbles and to ensure total drying. With these thick films, ultimate tensile strength and elongation at break were measured by Uniaxial tensile testing machine MTS Insight 30kN (MTS Systems).
Finally, glass transition temperature (Tg) was analyzed by Dynamic Mechanical Analysis (DMA, PerkinElmer DMA Q800).
Results and Discussion
Synthesis and Basic Properties of Liquid PUDs
Table 3 presents the characteristics of the PUDs made from the experiments X FLO-0 to X FLO-20. As seen in this table, the incorporation of 5% and 10% of Tolonate X FLO 100 did not impact the properties of PUDs in terms of particle size distribution, pH and viscosity. When the X FLO ratio was increased to around 20%, the particle size and viscosity of the final PUDs started to increase. This behavior could be attributed to side reactions with water during the dispersion of prepolymers, leading to different behaviors in the chain extension step. These side reactions with water could indeed be enhanced with increasing the amount of X FLO, as the reactivity of the NCO group is known to be higher compared to the ones of the IPDI structure.
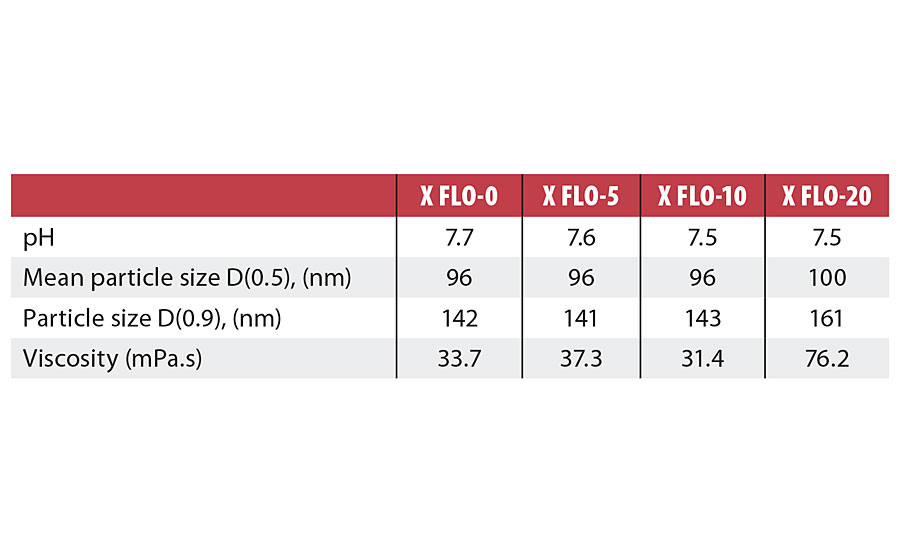
Kinetic Profiles of Isocyanate Reactions
The kinetic results in ATR-FTIR are summarized in Figure 2. The kinetic profiles were tracked in each experiment, and the results show that all experiments follow the same trends, in which amount of free NCO drops to around 45% from initial during the prepolymerization step. Then, 2-4% of NCO reacts with water in dispersion, and the majority of this further reacts with amine during the chain extension step.
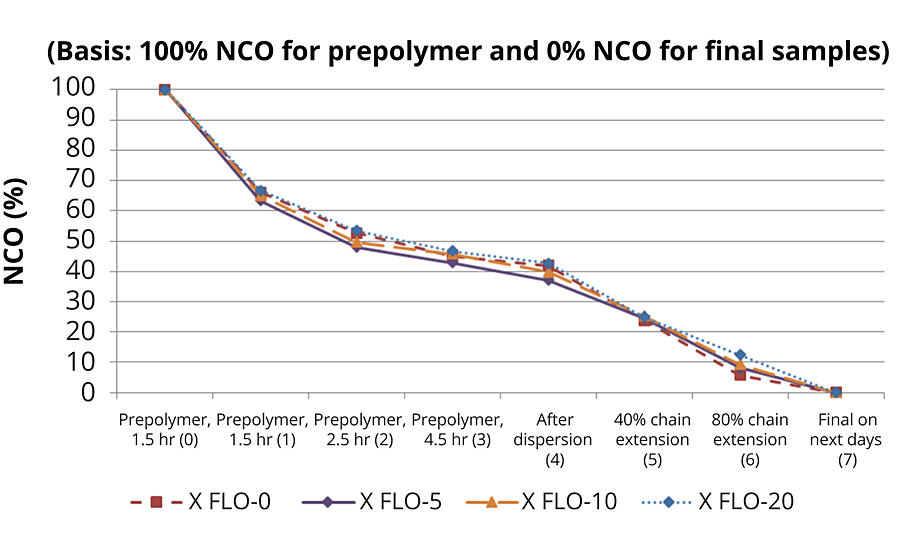
As described in the Experimental section, the reaction in the dispersion phase was stopped after 80% chain extension was reached, as some of the remaining NCO groups were entrapped inside polymer particles, these NCO groups will be more difficult to reach by EDA molecules during PUD synthesis. However, and with a longer period of time, all of the rest of the NCO functions will finally react, eventually with surrounding water, eventually to urea functions (see particle model proposed by Jhon et Al. (2001) in Figure 3).
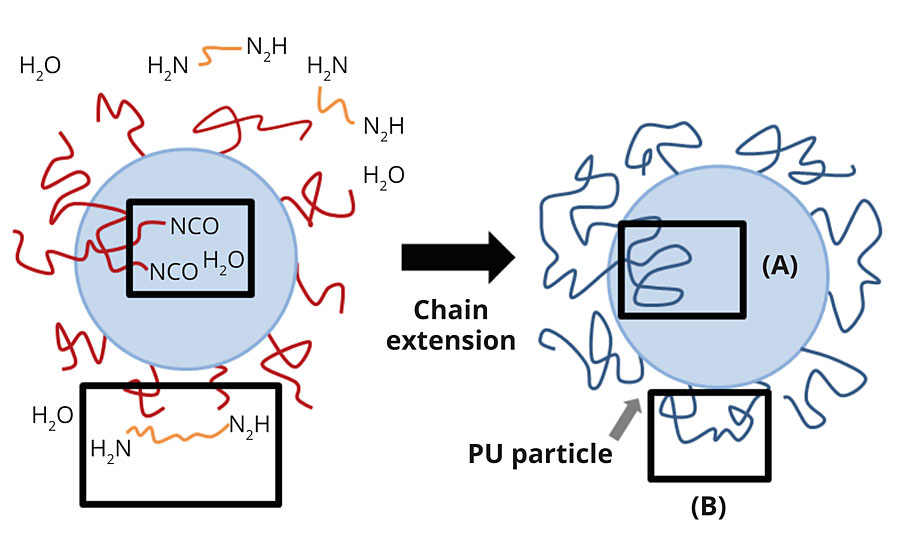
Physical Properties of PUD Films
Next, films from each liquid PUD experiment were analyzed with regards to their physical properties (aspects), mechanical properties, and chemical and hydrolysis resistances. In order to assess the benefit of X FLO when incorporated in the backbone of the PUD structure, two additional films were prepared (X FLO-10x and X FLO-20x). Those two systems were made by mixing the PUDs without X FLO (X FLO-0) with Tolonate X FLO 100 directly (ratio of 4.2 % and 7.6% by weight on wet PUDs, equivalent amount to X FLO-10 and X FLO 20 respectively) before applying the films. Composition details as well as test results are summarized in Table 4.
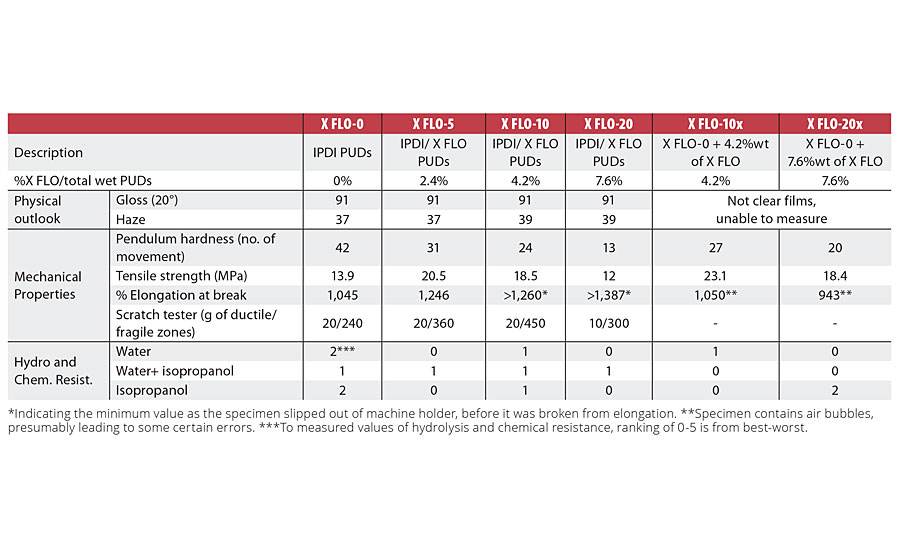
At the same weight ratio of crosslinking Tolonate X FLO in the structure, represented by comparisons of X FLO-10 vs X FLO-10x, and X FLO-20 vs X FLO-20x, the crosslinked PUDs did not show the same properties as the ones with X FLO in the backbone, simply observed from physical aspects. The hazy films indicate a phase separation from blending high-polar aqueous phases with low-polar X FLO. The consequence on mechanical properties is lower strength as well as lower elongation at break (Figure 4).

Conclusions
Tolonate X FLO 100 can be advantageously used in the design of polyurethane dispersions. The results obtained in this study show that, by adding Tolonate X FLO 100 to conventional diisocyanate monomers like IPDI, up to 20% by mol (40% by weight) in the diisocyanate composition, Tolonate X FLO 100 does not impact the polymerization process nor the characteristics of the dispersion. The most remarkable impact is the drastic increase in flexibility and elongation at break of the final material. A direct consequence is the improvement of the scratch resistance (brittleness) of the film. Furthermore, Tolonate X FLO 100 can improve hydrophobicity of the film and chemical resistance of the coating. Additionally, being a polymer, it offers safer handling during the preparation of the PUDs compared to classic diisocyanate monomers.
These benefits can be of great help when designing PUDs for applications requiring superior flexibility performance, such as coatings for textiles and leather finishing, and adhesives and sealants.
Acknowledgements
The authors would like to sincerely thank all colleagues at Vencorex Chemicals for their contributions on this work, especially Philippe Olier and Remi Martinez for technical advice and expertise. Jean-Yves Martin, Muriel Ducomet and Marie-Laure Bonnefoy are also acknowledged for their kind support in technical testing and analysis.
References
1. Jhon et al., Chain Extension Study of Polyurethane Dispersions, Colloids and Surfaces, Vol. 179 (2001).
2. Mulonda Hercule et al., Preparation & Characterization of PUDs crosslinked by Urea Bridges, International Journal of Chemistry, Vol.3, No.2 (2011).
3. Nakamura et al., Aqueous Polyurethane Dispersion and Process for Preparing the Same, Publication number: US 20110136976 (2011) .
4. Negim et al., The Effect of Diamine Extender on the Properties of Polyurethane Dispersions, Middle-East Journal of Scientific Research, Vol. 16 issue 7 (2013).
5. Pedain et al., Aqueous Polyurethane Dispersions Having Improved Water and Solvent Resistance, Publication number: US 6248415 (2001).
Looking for a reprint of this article?
From high-res PDFs to custom plaques, order your copy today!