An Epoxy Curing Agent with Superior Carbamate Stability

Epoxy systems (resins) offer good adhesion, high mechanical and thermal properties, and good chemical resistance as industrial maintenance coatings.1,2 These properties protect different surfaces, such as concrete, from decomposing in challenging environments. Amines, phenols, thiols and carboxylic acids are well suited co-reactants for hardening epoxy resins. Therefore, there is a wide portfolio of resins with different applications. In flooring applications,3 cycloaliphatic diamine hardeners often are the reactant of choice because they harden at low temperatures and bond readily to wet concrete.4 Additional advantages are simple handling, low viscosity and toxicity, good adhesion, outstanding color stability and a fast cure.
Amine adducts are often used in flooring applications. Blushing occurs when primary amines react with atmospheric carbon dioxide and water to form carbamate salts. In adduct form, the relative primary amine content has been reduced in the molecule, resulting in reduced hygroscopicity in the adduct and therefore reduced blushing.2-4 Amine adducts are also less corrosive and less volatile. On the downside, adduction leads to a significant increase in viscosity. The formulation with solvents or plasticizers such as benzyl alcohol (BnOH) lowers the viscosity of amine adducts and also accelerates the epoxy-amine reaction at ambient or sub-ambient temperatures.3,4
In this article, we explore the differences between adducts of two cycloaliphatic diamines, isophorone diamine (IPDA)3 and methylcyclohexyl diamine (MCDA), and between adducts of MCDA and aryl diamines, m-xylylene diamine (MXDA), shown in Figure 1. All three amines vary in terms of their curing profile, thermal profile and appearance. Both IPDA and MCDA are well suited to flooring applications and readily react with epoxy resins under ambient or sub-ambient temperatures. MCDA is a cycloaliphatic diamine epoxy hardener and consists of two regioisomers, 2,4 and 2,6-MCDA, with four and three stereoisomers, respectively (Figure 1).6 MCDA’s viscosity is below the already low viscosity of IPDA,5 which opens a wide spectrum in formulation and/or extended working pot-life.
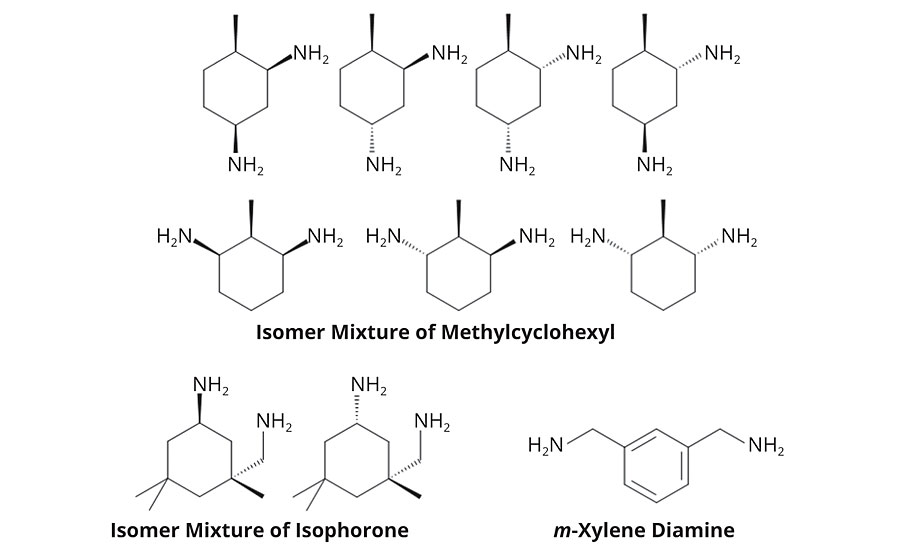
Experimental
Materials
Diglycidyl ether of bisphenol-A (DGEBA) was obtained from Leuna-Harze GmbH (Epilox® A 19-03, epoxy equivalent weight 184 g/mol). Isophorone diamine (Baxxodur® EC 201, amine hardener equivalent weight 42.6 g/mol) and methylcyclohexyl diamine (Baxxodur EC 210, amine hardener equivalent weight 32 g/mol) were obtained from BASF SE. m-Xylene diamine (amine hardener equivalent weight 34 g/mol) was purchased from Mitsubishi Gas Chemical. Benzyl alcohol was purchased from Honeywell. All chemicals were used as received.
Adduct Synthesis
Amine functional adducts (Figure 2) were synthesized with excess amine. The molar ratio of DGEBA to diamine was either 1:16, 1:8, or 1:2.5. For adducts with a molar ratio of 1:2.5, BnOH was added to keep viscosity within a workable range. For these adducts, BnOH and diamine were employed in equivalent amounts (wt%). The synthesis of 1:2.5 (DGEBA/MCDA) adduct is shown as an example. MCDA (175 g, 1.37 mol) and BnOH (175 g) were combined in a 1 L round bottom flask under a nitrogen atmosphere. DGEBA (200 g, 0.55 mol) was added dropwise and the mixture was stirred to facilitate complete reaction. No active heating was employed, although the temperature of the reacting mass was kept below 100 °C.
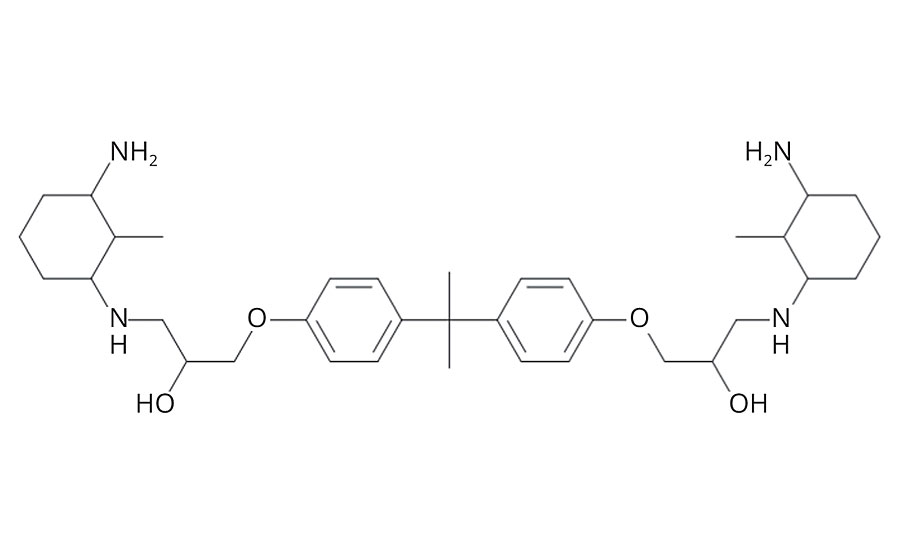
Preparation of Reactive DEGBA-Adduct Mixtures
To harden DGEBA with the prepared adducts or adduct-BnOH mixtures, reactive mixtures were formulated using a 1:1 stoichiometric ratio of epoxy groups to active NH functionality. The epoxy adduct or epoxy adduct-BnOH mixtures were stirred via a propeller mixer at 2,000 rpm for 1 min. Immediately following preparation, differential scanning calorimetry (DSC) and rheological experiments were conducted, and samples for Shore D and spectral gloss measurements were prepared.
Methods
DSC (204 F1 Pheonix, Netzsch) was used to determine the reaction and thermal profile [onset temperature (To), peak temperature (Tp), glass transition temperature (Tg)] according to ASTM D3418 using a heating rate of 20 °C/min starting with ambient temperature (23 °C).
The rheological profiles (pot-life and gel time) at 23 °C and 75 °C were determined using a conventional shear stress controlled plate-plate rheometer (MCR 301, Anton Paar) with a plate diameter of 15 mm and a gap distance of 0.25 mm, using rotational mode (pot-life) or oscillatory forces (gel time). Pot-life was measured as the time at a given temperature needed to attain a viscosity of 10,000 mPas. Gel point was defined as the crossover point of the storage and loss moduli, and gel time was defined as the time taken from addition of the hardener to the reaction mixture, to reach the gel point.
Shore D measurements were conducted by pouring 3 g of a reactive mixture into an aluminum pan with an inner diameter of 30 mm. The systems were cured under two different atmospheric conditions, either 10 °C (65% relative humidity) or 23 °C (ambient atmosphere). Shore D hardness measurements were conducted every hour according to DIN ISO 76191 on test specimens with a thickness of 35-36 mm.
Ease of carbamate formation was visually monitored by placing 3 g of adduct, or adduct-BnOH mixtures, in 35 mm diameter wells of a 2 x 3 well plate. The adducts and adduct-BnOH mixtures were then stored at 23 °C and 50% relative humidity for 48 hrs, and photographs were taken after 2, 4, 6, 8, 16, 24, and 48 hrs. Carbamates were detected through the visual observation of white precipitate or surface irregularities.
Gloss tests were conducted by applying the reactive epoxy adduct-BnOH mixtures to a matte black surface with a 500 µm doctor blade. Curing the coatings at 8 °C for 69 hrs yielded hardened films. Specular gloss was measured with a micro-TRI (20°, 60°, 85°) gloss meter from BYK Gardner with a 20° geometry according to ASTM D523.
Results and Discussion
Adduct Production
A total of nine adducts were synthesized by slowly adding DGEBA to excess amine (Table 1). The adducts were not isolated or purified following synthesis; all systems synthesized are mixtures of DEGBA-diamine adducts and residual diamine. The use of BnOH allowed epoxy-diamine mixing ratios as low as 1:2.5 for all three diamines. Without the use of solvent the lowest mixing ratio achievable was 1:8.
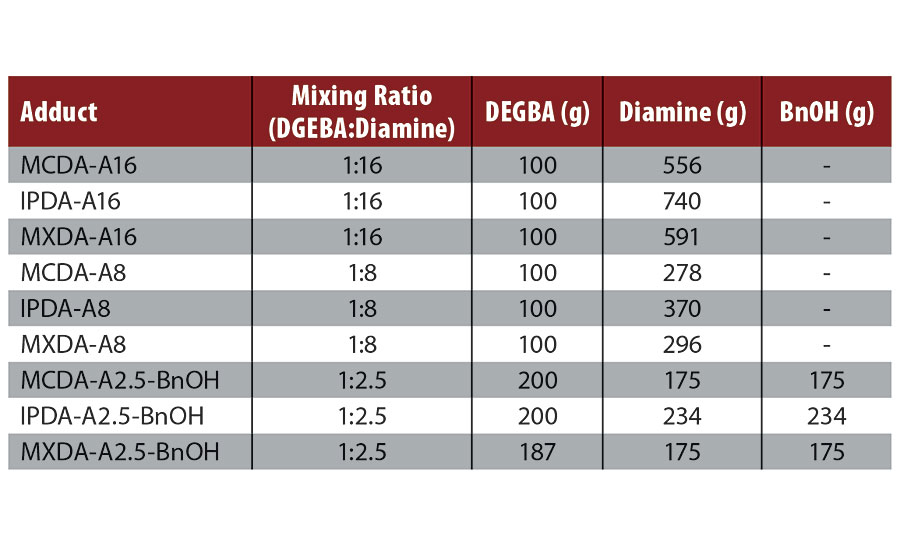
Thermal Properties
When employing a stoichiometric mixing ratio in the absence of BnOH, adduction of MCDA, IPDA and MXDA led to a slight decrease in the onset and peak exotherm temperature, and a slight increase in Tg, as compared to the pure diamines. Both MCDA and IPDA are cycloaliphatic amines containing two primary amines, resulting in similar polymeric backbone structures and Tgs. Compared to MXDA, a methyl group separates the amine groups from the aromatic core, leading to more backbone flexibility and a lower Tg. As expected, the adducts employing BnOH saw a reduction in Tg by 40-70 °C. The DSC results are summarized in Table 2. All DSC values reported here for the pure diamines are in good agreement with those previously reported.5-8
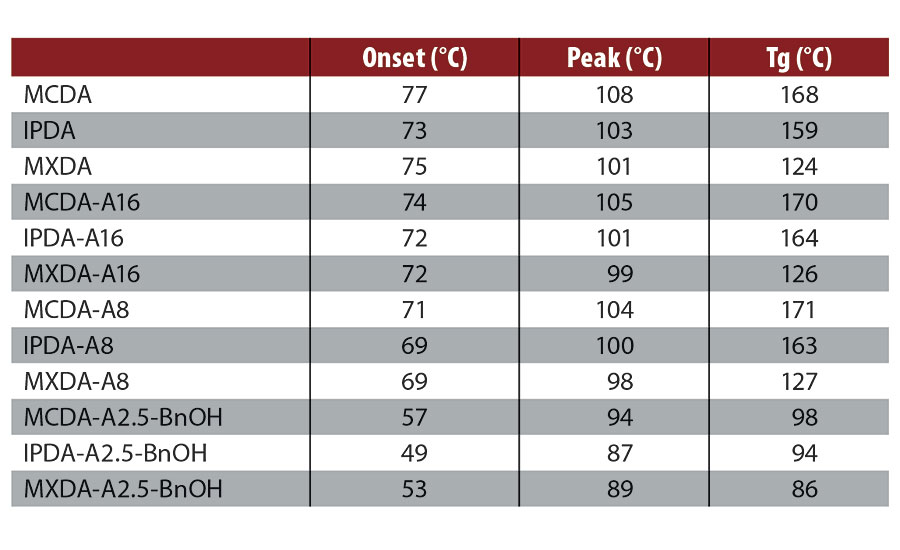
Rheological Properties
Greater differences were observed when comparing the rheological profile of DGEBA cured with MCDA-adducts versus IPDA-adducts or MXDA-adducts. For example, MXDA-A16 formulated with DGEBA had the lowest viscosity, followed by MCDA-A16, and then IPDA-A16, at room temperature (Table 3). At an elevated temperature of 75 °C, MCDA-A16 formulated with DGEBA displayed the lowest viscosity, while the viscosities of formulated MXDA-A16 and IPDA-A16 adducts were very similar to one another. Additionally, the viscosity behavior of DGEBA formulations with the various adducts was found to differ. For example, as shown in Figure 3, although formulations employing MCDA-A16 had a higher initial viscosity than those with MXDA-A16, the formulated viscosity of the MCDA-A16 progressed more slowly, yielding a longer pot-life. Pot-life is influenced by a combination of two factors, the starting viscosity and the rate of reaction, and even though MXDA-A16 has a lower starting viscosity, it reacts more quickly than MCDA-A16. This trend is also visible in the time to gel, where formulated MXDA-A16 was found to reach the gel point in the shortest amount of time, followed by IPDA-A16 and then MCDA-A16. As all A16 adducts theoretically have the same functionality, therefore MXDA’s fast gel time is indicative of its faster reaction rate.
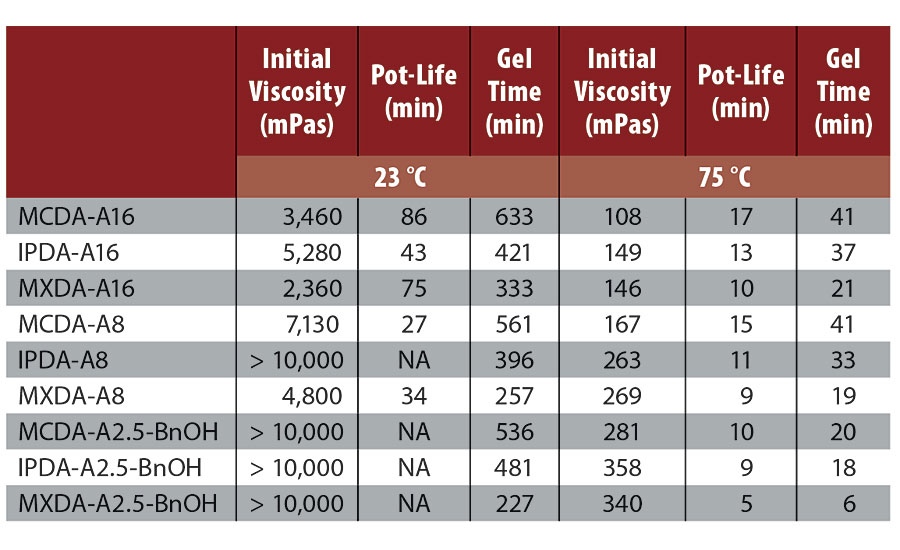
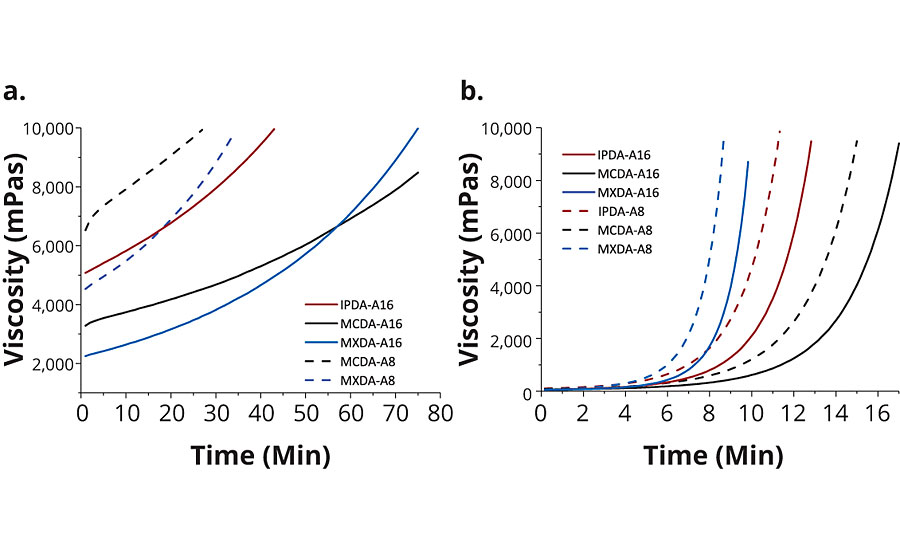
Shore D Development
The progression of Shore D hardness over time was determined for the synthesized adducts in combination with DGEBA, under two different atmospheric conditions, either 10 °C (65% relative humidity) or 23 °C (ambient atmosphere). Shore D development is also dependent on two factors: rate of network density build-up and polymeric backbone stiffness. Here, we are comparing diamines with similar rigidity and functionality, so differences in Shore D development will be dependent primarily on the reaction rate. Unsurprisingly, adducts based on MXDA were found to reach a Shore D over 80 significantly earlier than adducts based either on IPDA or MCDA (Table 4, Figure 4). IPDA was found to have a slightly better performance than MCDA at 10 °C, both in terms of hardness development and tack-free time, but IPDA- and MCDA-adducts displayed equivalent behavior when the temperature was raised to 23 °C.
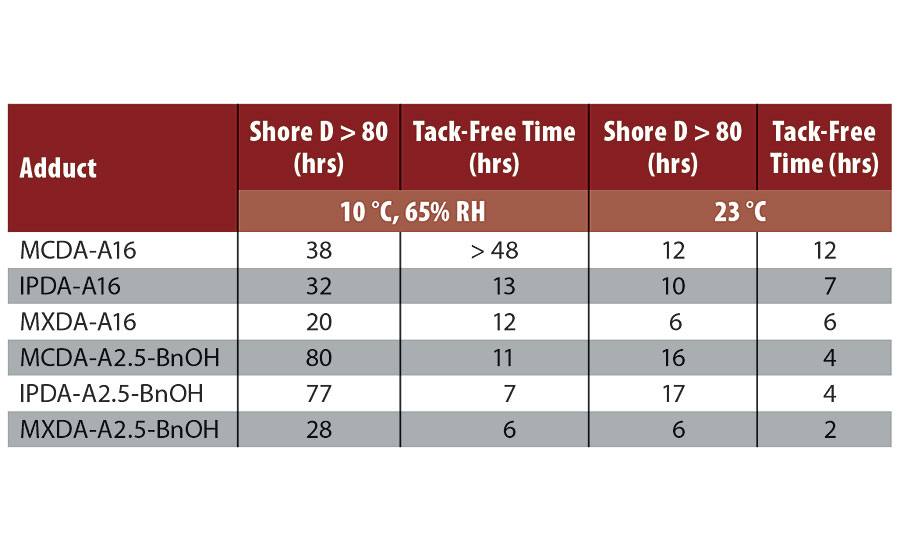
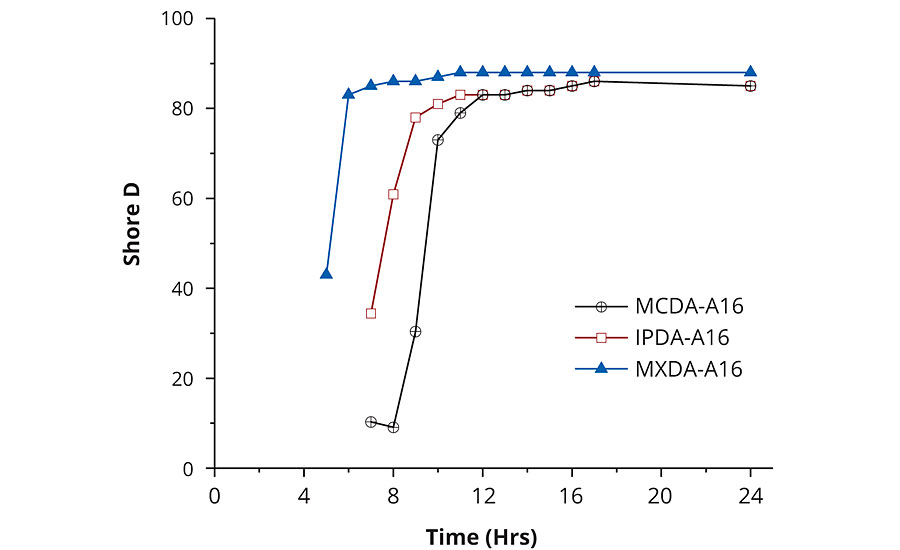
Carbamate Stability
Primary amines react readily with atmospheric carbon dioxide and water vapor to form carbamate salts. These salts tend to accumulate on the surface of the reacting mass, which leads to blushing. Blushing can have detrimental effects on gloss, color and intercoat adhesion.3,4 Stability against carbamate formation of the various adducts was determined using two different approaches. First, pure adducts or adduct-BnOH mixtures in the absence of DGEBA, were aged in a climate chamber at 23 °C and 50% RH. Formation of carbamate salts was then detected visually, through the observation of white precipitate or surface irregularities (Figure 5).
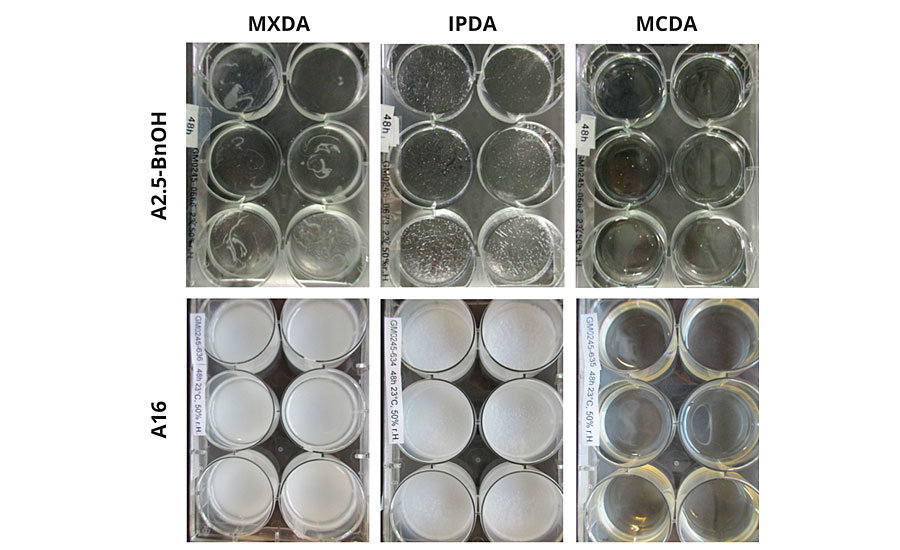
A significant amount of carbamate salt was visually present in MXDA-A16 after only 2 hrs and in IPDA-A16 after 16 hrs. Comparatively, although MCDA-A16 turned slightly turbid after 16 hrs, no carbamate precipitate was visible in MCDA-A16 even after 48 hrs. Adducts containing BnOH were also tested. Again, carbamates were first detected in MXDA-A2.5-BnOH after 8 hrs, then in IPDA-A2.5-BnOH after 24 hrs, and no turbidity or carbamates were visible in MCDA-A2.5-BnOH after 48 hrs. However, it is important to note that the A2.5-BnOH adducts had significantly less visible carbamate salts than their A16 counterparts. This is due to the decreased primary amine content of the A2.5-BnOH adducts, as well as the presence of BnOH, which serves to further dilute the primary amine concentration. As noted earlier, carbamate formation can be particularly detrimental to gloss. Therefore, our second approach to carbamate detection was to measure spectral gloss after complete curing at 8 °C and 70% RH. These low temperatures and high humidity conditions serve to accelerate carbamate formation. Reactive formulations employing the 2.5-BnOH adducts were coated onto a matte black surface, and gloss readings were determined at 20° following cure. A similar carbamate stability trend was observed; MCDA-A2.5-BnOH had the highest gloss reading of 89, indicating the lowest level of carbamate formation on the coating surface, followed by IPDA-A2.5-BnOH with 85, and then MXDA-A2.5-BnOH with 78. This trend clearly demonstrates that qualitative detection of carbamate salt formation can manifest itself in more quantitative application testing, such as spectral gloss readings (Figure 6).
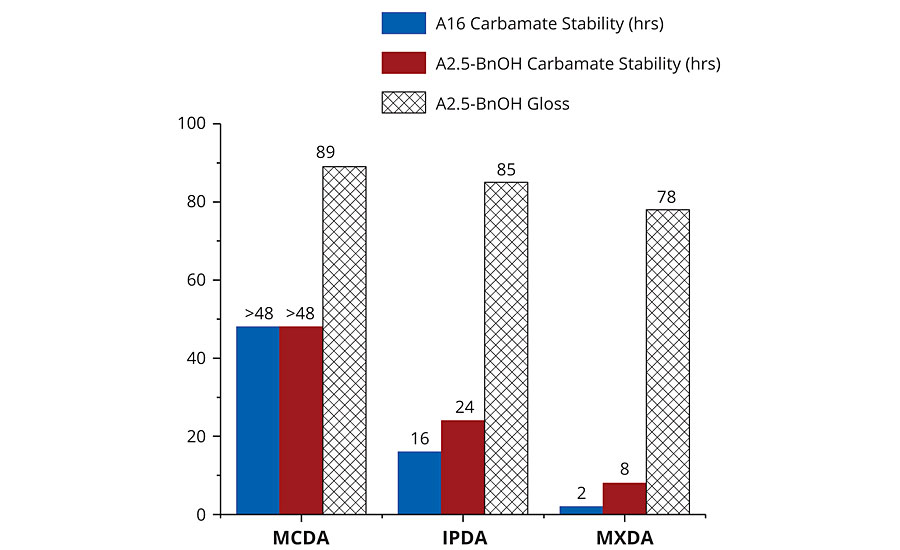
Conclusions
Epoxy-amine adducts based on MCDA (Baxxodur EC 210) were readily synthesized, with DGEBA-diamine adduct ratios ranging from 1:16 to 1:2.5. For the 1:2.5 adducts, BnOH was used as a solvent to help mediate the resulting high viscosities. MCDA-based adducts were found to react significantly slower than MXDA-based adducts, but the reactivity of MCDA-based adducts were comparable to IPDA-based adducts. The reactive formulations tested were very simple, and did not include co-hardeners or accelerators. Proper selection of co-hardener(s), accelerators, plasticizers and solvents can be used to further fine tune the reaction kinetics to match desired applications. Additionally, although MCDA-based adducts had higher initial formulation viscosities than the MXDA-based adducts, the viscosity of MCDA-based adducts progressed more slowly, leading to a longer pot-life. A long pot-life, where prolonged low viscosity allows for easy handling, is crucial to the production of defect-free, high-quality coatings. Lower formulated viscosity also allows for greater formulation freedom; for example, solvent content can be reduced and other high-viscosity or solid components can be more easily incorporated. Most importantly, MCDA-based adducts were found to have greater stability against carbamate formation relative to the MXDA- and IPDA-based adducts. This behavior was further validated in coating tests, where a formulation employing MCDA-based adducts resulted in a coating with the highest spectral gloss; carbamate formation is detrimental not only to spectral gloss, but also to yellowing and intercoat adhesion. Overall, MCDA is an attractive building block for epoxy-diamine systems and is particularly well suited to industrial coatings applications. n
References
1 Maslow, P. Plastic Mortars, Sealants and Caulking Compounds. ACS Symposium Series, Ed. R.B. Seymour, American Chemical Society, Washington DC, 1979, 113, 39-60.
2 Chen, X.M.; Ellis, B. Coatings and Other Applications of Epoxy Resins. Chemistry and Technology of Epoxy Resins, Ed. B. Ellis, Springer, 1993, 303-325.
3 Pham, H.Q.; Marks, M.J. Epoxy Resins. Ullmann’s Encyclopedia of Industrial Chemistry, 2005.
4 Wicks, W.Z.; Jones, F.N.; Pappas, S.P.; Wicks, D.A. Epoxy and Phenolic Resins. Organic Coatings Science and Technology Third Edition, Wiley, Hoboken, 2007, 271-293.
5 De Nograro, F.F.; Guerrero, P.; Corcuera, M.A.; Mondragon, I. Effect of Chemical Structure of Hardener on Curing Evolution and on the Dynamic Mechanical Behavior of Epoxy Resins, J. Appl. Poly. Sci., 1995, 56, 177-192.
6 Pfeffinger, J.; Malkowsky, D.; Geottke, S. Use of a Stereoisomer Mixture of Diaminomethylcyclohexane as a Hardener for Epoxy Resins, US Patent Application 20120226017, 2012.
7 Galy, J.; Sabra, A.; Pascault, J.P. Characterization of Epoxy Thermosetting Systems by Differential Scanning Calorimetry, Poly. Eng. Sci., 1986, 26, 1514-1523.
8 Sabra. A.; Pascault, J.P. Epoxy Thermosetting Systems Based on Cycloaliphatic Diamines, J. Appl. Poly. Sci., 1986, 32, 5147-5160.
This article originally appeared in Coatings World Magazine, May 2018.
Looking for a reprint of this article?
From high-res PDFs to custom plaques, order your copy today!