A Study of Icephobic Coatings, Part 1






In snowfall regions, ice accretion/accumulation is a potential hazard in various industries including transportation, aircraft/aerospace, marine, power transmission (ground wires, phase conductors and insulators), power production (wind turbines, buildings, electrical distribution, telecommunications and agriculture), automotive, outdoor sports facilities, solar cells, etc.
Due to extreme weather conditions in cold climate regions, utmost care is needed while driving on roads during winter months. Icefall and snow accumulation disrupt day-to-day activities and effectively curtail road transportation. There is a tremendous amount of research work being conducted in cold regions, such as the northern U.S. and Canada, as well as the rest of the cold countries around the globe.1,2 Ice accumulation can cause hazardous road conditions and stall road transportation. For normal traffic flow and safer mobility, measures are needed for de-icing or anti-icing of accumulated ice on roads.
The term de-icing implies the removal of ice or clearing of ice after ice storms occur. On the other hand, anti-icing systems are activated before ice storms occur, thus preventing significant ice deposition overloads (static or dynamic) due to ice weight and wind, particularly on power lines. Both de-icing and anti-icing operations are performed using mechanical means (e.g., brooms, brushes, plows) and as well as through the application of chemical agents. To clear off the ice and snow on roads, a large amount of solid and liquid chemicals, as well as abrasives (e.g., sand) are used for de-icing or anti-icing, collectively known as “de-icers”.3
The aviation industry is also significantly affected. Aircraft engines are stalled, and their fuel efficiency and lift diagnostic performance are dramatically reduced. During the period between 1998 and 2007, there were catastrophic socio-economical losses due to the damage from ice storms in Eastern Canada and Oklahoma. In the United States, between the years 1959 and 1994, other icing events caused the collapse of 140 communication towers (40-2000 ft tall).4 And in the United States, ice accumulation during the winter season caused 135 planes to crash between 1993 and 2004, resulting in 171 casualties.5, 6
In cold climate regions, ice and snow that adhere to structures cause numerous problems. Mechanical failures or insulator flashover can happen due to accumulated ice on power transmission and electrical distribution equipment. Power outages inhibit life normalcy, leading to significant socio-economic consequences. Crops are damaged, electric power lines go down, and wind turbines and HVAC systems are also severely affected. Serious problems are also encountered when ice and snow build-up on the high-voltage overhead power transmission lines and conductors. During this time, even the electrical transportation and telecommunication networks are interrupted.
In the case of power production through wind turbines, ice accretion affects energy production performance, and both electrical and mechanical failures can occur. Usually, about 20% of wind turbines are located at sites where icing events are likely to occur in winter. The reason for building wind turbines in this region is because the wind power is 10% higher than the standard areas due to enhanced air density at lower temperatures.7, 8 High altitudes are the best sites for installing wind turbines for energy production. At high altitudes, wind speed is generally increasing by 0.1 m/s per 100 m of altitude for the first 1,000 m.7, 8 In Switzerland, these wind turbine sites are installed at approximately 800 m above the sea level, and these sites often face incredibly harsh conditions.8
Compelling methods are demanded to keep wind turbines ice-free for efficient energy production. Among others, Markus examined various coating methods claiming icephobic properties for wind turbines.8 These methods include hydrophilic and hydrophobic coatings, sol-gel coatings containing fluorinated compounds, and viscoelastic rubbers, as well as commercially available icephobic products. Investigations on icephobic properties of different coatings and ice adhesion measurements are commonly performed with a 0° cone test to determine ice adhesion strengths between coating and ice.8 At present, conventional anti-icing and de-icing methods are in use for the wind turbine industry that utilizes an anti-icing method based on ice-accretion. Also, de-icing methods are applied when ice already has built-up on the surfaces of wind turbine rotor blades.7, 8
The passive method, which is also popularly known as the surface coating method or permanent surface coating method (also termed as "icephobic" coating), is useful for ice adhesion prevention. Icephobic coatings can protect the exposed surfaces and can significantly reduce or eliminate ice adhesion strength. The passive protection method does not require an external power or energy source, such as heating. It utilizes the advantage of inherited physical surface properties such as low water contact angles and reduced friction coefficients to repel ice by its weight. Icephobic coatings are inexpensive, durable and easy to apply on various surfaces.
The low adhesion strength between ice and a solid surface defines the “icephobicity” of a coating material.9, 10 It is worth mentioning that no material can completely prevent ice or snow accumulation on surfaces. The most common assumption is that any product having reduced chemical affinity with water should also have weak ice adhesion strength. However, this theory is not entirely accepted among the researchers.10-14 Saito et al.14 have shown that an increase in substrate surface roughness increases ice adhesion. Although snow/ice build-up on various surfaces is unavoidable, few preventive efforts have been utilized on hydrophilic, hydrophobic and super-hydrophobic surfaces for reducing ice adhesion over the past decades. Ideally, preventing ice accumulation rather than de-icing is a favorable solution, which can be achieved through icephobic coatings. For practical applications, the structural and chemical integrity of icephobic surfaces must withstand erosion, wear, UV radiation and other weathering conditions. Whereas, for commercial adoption of icephobic materials, the engineered surfaces of these materials must be cost-effective, environmentally friendly and manufacturing scalable.7
This article summarizes the materials used in surface coatings or icephobic coatings for preventing ice accretion on substrate, and the effect of salts and chemicals used for de-icing and anti-icing, along with their implications on snow-affected industries. Additionally, it discusses the best practice employed in aviation industry de-icing operations. It also mentions the impact of de-icing agents on contaminated waste-water and the cost involved in the recovery process.
Icephobic Surface Coatings and Materials of Choice
There has been a long history of research work on ice adhesion testing, dating back to the 1930s. The National Advisory Committee for Aeronautics (NACA) Langley made qualitative comparisons in an open-plenum icing tunnel in 1930.15, 16 Various test methods were utilized to measure the adhesion of ice before 1940 in the earlier research.17 The first coating materials included greases, oils, soluble compounds, paints and several others. In early 1918, Lewis, in his U.S. patent, suggested an anti-freezing mixture for the radiator system of internal combustion engines to prevent water freezing in cold climates.18 He proposed a solution of calcium chloride dissolved in water along with caramel, glucose and borax. The purpose of glucose and caramel solutions in this mixture was to prevent the crystallization of calcium chloride when the compound turns super-saturated on the evaporation of water. It was suggested that such technology could be useful for various applications and not confined to the radiator system.
Later in 1956, Rolle et al. explored de-icing lacquer formulations as a permanent coating material that was based on nitrocellulose, ethylcellulose, cellulose acetate and polybutylene in combination with resins, such as alkyds and vinyls, and/or plasticizers for the aviation sector.19 The ice adhesion to various solids was also studied by Rarty et al. In his findings, a significant factor of adhesion was drastically reduced by surface contaminants on the metals, and this reduction was stronger over the areas at the metal coating interface.20 The detailed studies on shear stresses developed near the interface of ice and substrate demonstrated that adhesion properties vary based on polymer materials and metals in contact. This team conducted critical investigations on adhesion of ice to various surfaces and established a direct relationship between adhesion and frictional properties of the ice sliding on similar surfaces. Some other studies suggested that adhesion strength of ice to various surfaces varied significantly, and if left untouched, bare concrete, wood, steel and aluminum have high ice adhesion strength.21-25 Parameswaran21,22 determined through pile push-through tests that the order of adhesion from highest to lowest followed a pattern such as wood > concrete > steel, and that the effect is due to anchoring effect on highly porous surfaces.23
Wei et al.24 from fracture tests found that ice adhesion was weaker on steel compared to aluminum due to the lower surface energy of steel relative to aluminum.24,25 A comprehensive literature survey on adhesive materials and few strategies for reducing ice adhesion were outlined by Sayward.26 He suggested utilizing low-surface-energy coating materials to achieve an optimal degree of roughness to reduce ice adhesion.26 The presence of air was discovered as an important contaminant in adhesion. The surface roughness and texture played an important but secondary role. However, on hydrophobic surfaces, enhanced roughness could lead to air entrapment that will impair wetting and adhesion.26
To reduce the adhesion of ice (an adhesive whose liquid form is water), substrate wettability should be reduced by making it more hydrophobic26 - implying reduction in surface reactivity and surface forces, making it inert and incompatible with water. The resulting higher water contact angle makes it occlude air at the interface. Various polymeric materials showing variation in ice adhesion characteristics have been studied both at the laboratory scale and large-scale for their ice-withstanding capability. Several classes of epoxies, polyurethanes, silicones, etc., are few noted materials.26-28
The ice adhesion in rubbery materials with controlled surface properties was examined by Andersson et al.29 They developed several compositions of rubber materials using tertiary butyl-cumyl peroxide as a cross-linking agent and pure polymer. The trifolium pretense, a leaf from red clover, was also tested for ice adhesion strength. On comparing to natural products, leaf-based surfaces shed water easily. It was also noticed that reinforcing a rubber material with carbon black significantly enhanced the power of ice adhesion, revealing a correlation between wetability and interfacial shear strengths between polymer materials and ice. Also, an increment in polymer surface-free energy with an increase in bond strength was noticed.
The water contact angle measurements on different types of leaves such as aspen, birch, sallow, raspberry, lady's mantle, timothy, white clover and couch, on 30 different surfaces have shown low ice adhesion for materials with hydrophilicity numbers, “k” values, smaller than approximately 0.2, which correspond to water contact angles of roughly 90° or higher.29 Few scattered studies30-32 have reported that ice adhesion decreases with increasing water contact angle, whereas others have found little relation between the two parameters.33-37 The theoretical calculations and experimental observations from the literature have suggested that low ice adhesion is related to low permeability, absorption capacity and high surface hydrophobicity (an elevated water contact angle).
The ice adhesion strength on synthetic polymer coatings was found an order less than on uncoated surfaces. Few commercial polymer coatings displaying adequate properties have been proven to be effective in reducing ice adhesive strength over coated surfaces. Coating materials like Teflon-4, organosilicone epoxy ‘G’ and vinyl polymer sheets with perfluorinated films were few superior coating materials.38 Apart from low surface energy, high linear thermal coefficient of the polymer surface has a profound effect on ice adhesion strength.
Polycarbonate-based ice-releasing block-copolymer films were made of poly(dimethyl-siloxane)-bisphenol, as coatings for ice adhesion were studied by Le Grand et al.39 and H.H.G. Jellinek et al.40 They mentioned that in addition to the hydrophobic ice adhesion properties of the materials, their mechanical and physical properties are also significant. Hydrophobic surfaces are essential for superior ablation properties. However, experimental observations28, 9 revealed that good adhesion surface itself is not sufficient, and that low glass transition temperature, Tg, which is a measure of segment mobility, is also important. The dimethyl siloxane content must lie in a specific range of weight percent and chain length. Adhesion strength varies based on the siloxane content and its block-chain lengths, and as well as on glass transition temperature. If the weight content, Tg and block-chain length are outside the favorable range, then the rheological-mechanical properties of the films become similar to that of ice, and adhesion is reduced.28,39 However, the rheological properties of ice and polymers must be different for better results. Polysiloxane(amide-ureide) is an alternative material of choice for long-lasting anti-ice coatings. The bonding between the substrate and the polysiloxane(amide-ureide) coating disrupts the hydrogen bonding between the accumulated ice and the coated substrate. The ability of adhesion of polymer coating to the substrate and its capacity of the coating to inhibit the formation of ice on a coated surface make it a suitable material for inhibiting ice formation on aircraft or other vehicles.40
Poly(tetrafluoroethylene) (PTFE), an extremely adherent coating on under layer Al2O3 substrates produced by anodizing in an oxalic acid electrolyte, drastically improved both hydrophobic and icephobic properties.41,42 To avoid PTFE degradation, its impregnation could be carried out at low temperature (320 °C), which ultimately minimizes the Al alloy structural modification.41, 42 The PTFE impregnation within anodic films prepared in phosphoric acid can also yield good results. These highly hydrophobic coatings are 1.15 times better than flat Teflon, and they reduced ice adhesion by almost 2.5 times and remained active for several-ice shedding events.41, 42 Caroline Laforte et al.13 suggested two different categories (commercial and industry) of surface protective coatings. Commercially available protective surface coating products are easy to apply, which are readily available in the market for purchase at an average price of around $65/L. These commercial products include a few with a rigid finish somewhat like paint, others that have a finish with visco-elastic properties like rubber and highly compacted dried powder on the aluminum surface. Industrial category protective coatings are comprised of a protective wax for metals, lithium grease and a Teflon coating applied to aluminum surfaces. These coatings were also useful for protection against corrosion. However, studies confirmed that any such two categories studied do not hold the exact icephobic material properties: high effect of reducing ice adhesion and long-lasting life. Such icephobic coatings are not a permanent solution because of the gradual degradation of the surface caused by successive de-icing operations. The use of icephobic coatings, however, could help in reducing the shear forces needed to remove ice build-up. In such processes, a small amount of ice is pre-formed on the surface and later removed through the use of external forces such as gravity or aerodynamics, which overcome adhesion forces.43
Several coatings formulations along with different combinations of binders such as Braycoote and Rain-X, together with fillers, such as MP-55 and UF-8TA, with varying filler/binder proportions, were tested to evaluate the ice adhesion in the SILC (Shuttle Ice Liberation Coating) coatings by Ferrick et al.44 They have also noted that the measured contact angles ranged from 81° to 143° for the tested surfaces. Coatings made of a mixture of Rain-X and MP-55 resulted in low ice adhesion when compared to bare metals with static ice-shear tests. A mixture of urethane and PTFE (polytetrafluoroethylene) particles called advanced icephobic surface (AIS) coatings were tested for the prevention of icing on airfoils in an icing wind tunnel.45 These test substrates were made on two different airfoils; one airfoil was coated with AIS and the other airfoil with polyurethane. The tested AIS coatings were transparent, water repellent with a contact angle of 150°, and characterized by hardness 2H (pencil hardness). An electrical heater was inserted in the airfoils to simulate an anti-icing system. It was noticed that on entering an electrical heater in the airfoils, relatively less ice was accumulated on AIS-coated airfoil compared to the polyurethane-coated airfoil. The effect of the AIS coating was even more in glaze icing conditions, as ice accretion on the polyurethane-coated airfoil was not observed on the AIS coated airfoil.45 C. Antonini et al.46 on the other hand, proposed an alternative approach based on superhydrophobic coatings. Likewise, it was observed that the isolated ice accreted surfaces form on the superhydrophobic surface was different from that of compact ice accretion on the hydrophilic surface. These characteristic approaches facilitate ice braking and enhance ice removal from the substrate surface effectively and safely.46
The Environmental and Economic Impact of De-Icing Salts and Chemicals
Good surface layer friction can be achieved with the application of the chemicals for safer road conditions. For the snow melting process on roads, rock salt (sodium chloride-NaCl) was first introduced in the 1930s. However, the use of salts for de-icing becomes a regular practice for highway maintenance after the 1960s.1-3 Typically, rock salt is spread over ice/snow surface to melt that acts as an abrasive for the motion. The lower cost, abundance, effectiveness and easy spread on surfaces makes rock salt a suitable ingredient for the de-icing process.1 Rock salt works effectively up to -9 °C (16 °F). Salt can quickly soften the ice, and melts about 10% of the total water content of the snow and ice layer of the treated surface.2 De-icing using rock salt is a slow process. The basic properties of de-icers must be readily soluble in water and lower its freezing point. Some de-icers give off their heat as they dissolve, which facilitates for faster melting of snow and ice. Hence there are ongoing research efforts for more alternate materials for a speedy recovery from ice and snow. To clear the pavements and roads, large quantities of de-icing chemicals are applied for safer normal traffic flow. Concurrent research and development on the new de-icing materials for efficient road conditions, and to address the growing concerns over the economic and environmental impacts on various chemicals used is required.47-51
In addition to the rock salt, some other popular salts include calcium chloride (CaCl2) and magnesium chloride (MgCl2), which was also tested for de-icing, and small quantities were also used as dust suppressants. However, NaCl is by far the most widely used salt for de-icing. De-icers are not limited to different salts; it ranges from rock salt to urea.52 For better efficiencies, anti-caking agents such as Prussian blue, sodium ferrocyanide (Yellow prussiate of soda), chromates, and phosphates were also added to sodium chloride and calcium chloride.53 According to Field et al.54, 55 research, it is approximated that 9 to 10 million tons of NaCl, 0.3 million tons of CaCl2 abrasives are used annually. Highway salting rates vary from 400 to 800 pounds of salts per mile. When salt is spread on the accumulated snow/ice, it may choose different pathways. It may dissolve in the melting snow and runoff.
As snow melts, moving traffic on roads may splash the slat or salt solution into the adjacent roadside environment, where it may seep into the soil and become available for roadside vegetation or the underlying water table. In the splashing process, some other higher concentrations of pollutants are also accompanied by salt.1 Surface waters are complex ecosystems; the effect of salt on surface waters was researched by numerous different studies (short term and long term) to understand the impact of the pollutant from a de-icing operation. Demers and Sage carried out a two-year study/survey on the effect of chloride salt, and determined the impact of de-icing on four tributaries to Rich Lake located in the central Adirondack Mountains of New York’s 28 N highway. The total amount of salt applied in their study was 44 tons in 1986-87 and 41 tons in 1987-1988.56 They observed chloride levels were increased in the downstream section of their four streams study. However, there is no significant difference in the case of downstream 50 m and downstream 100 m samples. The highest chloride concentration found in Rich Lake was 3.69 mg/L, well below the average value for fresh waters of 8.3 mg/L.57 They have also noticed from their studies that the saline water (salt-based chloride after melting snow) entering into the lake was accumulated in the deeper portions of the lake below the lower-density freshwater, indicating that the chlorides are more concentrated at the lower depths than on top layers. Similar results were observed by Judd et al.56 when large amounts of snowfall happened during the winter season of 1964-1965 in Ann Arbor, Michigan. During that time, heaver salt was applied than the usual quantity, and much of the saltwater from de-icing entered into the First Sister Lake. Chloride levels reached as high as 177 mg/L and conductivity 754 ohms in the lower meter of water during these periods.57
A three-fold increase in average chloride content from 7 mg/L in 1910 to about 23 mg/L in 1964 was witnessed in long-term studies of Lake Erie.58 So far, there was no deleterious impact as the concentration of chloride is not very high. However, the continuous rate of increase of chlorides due to road salt application during the snow season can cause serious health issues. Annually, 11 percent input of chlorides into Lake Erie waters was estimated.58 High chloride levels are also observed in the summer season, which is due to the cationic exchange that traps the sodium with humus in the soil, leaving the chloride at the bottom of the groundwater.58 Because of dilution, smaller lakes are at significant risk when compared to much larger lakes.59
The study found that sodium, calcium and chloride ions have a definite impact on soil properties, but the disadvantages of road salt pollution on roads were temporary, and the percentages of chloride concentrations were not sufficient to warrant the complete discontinuation of the use of salt on roads. Salt spreading is an essential step in reducing the risks posed by snow accumulation on roads. Bowers et al.,60 in a study on US highway 41, near Marquette, Michigan, revealed that the sodium levels were high along the highway immediately following the snowmelt. However, calcium levels did not increase sufficiently, and its levels in the soil were increased with the progress in winter months. Sodium acetate is readily biodegradable even at low temperatures, and sodium formate is also highly biodegradable, but it is highly dependent on the temperature. Research results of Transport Canada and ADI Nolan Davis, Inc., concluded that sodium formate, a potassium acetate-based chemical de-icer, is more benign to that of urea and glycols. Even though sand is not degradable, it can clog storm drains and contaminate surface waters through increased erosion and sediment formation.1
Field studies have shown that calcium magnesium acetate (CMA), an organic compound and a powdered mixture of dolomite limestone and acetic acid, is equally capable as salts for ice melting for lower application rates. Based on laboratory results, CAM is one of the best alternatives to de-icing, but these results are not enough for field investigations.58 And it works very well and adheres when mixed with sand when compared to salt and sand mixture. Sand can improve the adhesion of the chemicals to the road surface until the ice melting action begins when compared to salt and ice. CMA is less effective and slower in freezing rain, drier snowstorms and light-traffic conditions.58 CMA is also one of the readily biodegradable de-icers, which makes it a favorable alternative runway anti-icer. However, one drawback with CAM is depletion of oxygen, and degradation of acetates appears to be a potential impact related to the use of this de-icing compound.61, 62 When compared to salts, CMA affects the soil differently, since its components are different from salts. Acetate ion in CMA is less mobile in soils than chloride ion in salt. And it is readily degraded by soil microorganisms, and is not conserved.58 Even though CMA is thought to be an alternative material of choice for de-icing for road salts, it does not work in the vicinity of surface waters. No other significant work on ground waters has been reported in the literature on the impact of ground waters by road salt application.
Aircraft de-icers are categorized into four classes: Type I-Type IV. The most commonly used de-icing fluid for aircraft is Type I, which contains either ethylene glycol or propylene glycol, water and additives, and remove accumulated ice and snow from aircraft surfaces.63-65 Types II, III, and IV were developed for anti-icing, and they form a protective anti-icing film on aircraft surfaces to prevent the accumulation of ice and snow. They also contain either ethylene glycol or propylene glycol, a small amount of thickener, water and additives.63-66 Additives contain corrosion inhibitors, flame retardants, wetting agents, identifying dyes and foam suppressors. In the aviation industry, ethylene or propylene glycol-based materials were adopted for anti-icing and de-icing chemicals. Glycol mixtures contain 10-20% of additives. These additives contain corrosion inhibitors, thickening agents and surfactants. Particularly propylene glycols can reduce the melting point of ice to -59 °C (-74 °F). Glycols alone are not too toxic. However, they are chronically toxic when combined with different additives both for de-icing and anti-icing. Urea, in combination with glycols, is also used in the aviation industry for runways. Urea is also used occasionally in highway de-icing applications. Airplane de-icing is essential for safe travel, but using this combination can release de-icing fluids to the environment, which are harmful.63, 64 Turnbull and Bevan's studies confirmed the damaging effect of urea for airport de-icing applications.65 They concluded that the application of urea has an adverse impact on the mainstream water quality and ecology. In addition to the aforementioned glycol-based de-icers, diethylene glycol is also approved as a depressant. However, currently, diethylene glycol-based de-icing fluids are not used in the U.S.66
The Federal Aviation Administration (FAA) imposed specific passenger safety regulations on the aviation industry/air transportation for their smoother operations. De-icing and anti-icing are mandatory for both passenger and commercial aviation operations with proper discharge controls in place to ensure the safety of passengers. Without adequate discharge controls in use, airport de-icing and anti-icing can result in environmental impacts on both aquatic life and human health. Quality of surface waters/groundwaters (i.e., lakes, rivers) is significantly impacted in the case of biodegradation of propylene or ethylene glycol (i.e., the base chemical of de-icing fluid) used for de-icing and anti-icing operations. Here, in this case, a significant reduction in dissolved oxygen levels can ultimately lead to fish kills. However, it is less likely to happen during the de-icing season, but may happen as the atmospheric temperatures rise and airports are still conducting de-icing operations. During this time, snow dump piles melt and release the chemicals into streams.
In this regard, the US Environmental Protection Agency (EPA) released a primary data summary that provides information about the air transportation industry and the best practices being employed for aircraft and airfield de-icing operations. EPA conducted this study on approximately 200 U.S. airports with a minimum annual snowfall of one inch, on average with potentially significant de-icing/anti-icing operations which meet the obligations of the EPA under the Section 304(m) of the Clean Water Act in accordance with consent decree in Natural Resources Defense Council and Public Citizen, Inc. v. Browner (DDC 89-2980, as modified February 4, 1997).66 They hope that this study will serve as a source of objective information to airport authorities, airlines, state and local city regulators and citizen groups. Individual airlines and fixed-base operators (i.e., contract service providers) are responsible for aircraft de-icing/anti-icing operations. Airport authorities are responsible for de-icing/anti-icing of airfield pavement and all other common areas. Either party is needed to follow the FAA regulations. Airport authorities are ultimately responsible for waste-water management. Even though EPA set regulations, local state or community officials will look after local water quality and environmental issues, etc. Due to this, there is a large disparity in regulations/permits from airport to airport. De-icing/anti-icing is an important aspect for smoother and safer operation of daily activities in the aviation industry.
Another challenging aspect is taking care of the waste-water collection, containments and recycling/treatment programs after de-icing/ anti-icing. Even after imposing stringent regulations, most airports have achieved 70% collection efficiency of the aircraft de-icing/anti-icing fluids applied. EPA also spent $20 million to finance the necessary equipment and infrastructure changes. Few severe environmental incidents were reported, even after imposing EPA's Storm Water Discharge Permit regulations with best management practices. EPA estimates approximately 28 million gallons (50% concentration) of aircraft de-icing fluid (ADF) annually are introduced into surface waters. This is almost equal to 14 million gallons of ADF concentration before dilution with water and 12.6 million gallons of pure glycols, or about 100 million pounds of biochemical oxygen demand.66 As stated earlier, airports and airlines have different sets of operations during de-icing/anti-icing operations. Their financial accounting practices also vary widely. Due to different ownership structures of airports and complexity in financial management, airport authorities may impose the cost of capital improvements as higher fees to airlines or the passengers in the form of user or passenger facility charges.66
In the process of identifying potential environmental hazardous, toxicity of ADF's and economic impacts etc., EPA conducted an extensive literature survey. It collected data from various sources such as the U.S. Air Force, the Permit Compliance System and Toxics Release Inventory databases, local and other federal agencies, United States Geological Survey (USGS), the US Fish and Wildlife Service, Environment Canada, and the Canadian federal agency. During the de-icing process, ADFs sticks to the aircraft surface to remove or prevent snow and ice accumulation. As mentioned earlier, other than nonchemical methods, mechanical methods or thermal forces were used to clear off snow, which can avoid chemical contamination of surface waters. As chemicals were widely used in the de-icing and anti-icing process, at most, care needed in choosing materials for highway road and transportation and as well as aviation applications. In general, airlines do not track de-icing costs at the corporate level; however, they are tracked by airlines at individual airports, and all costs are directly attributed to de-icing operations. Airport landing fees and other charges are attributed to both direct operating costs (e.g., vacuum trucks, waste-water treatment operations) and capital costs (e.g., de-icing pads, drains, retention ponds) of ADF collection and disposal.66 There is certainly much more impact of using chemical-based de-icing/anti-icing agents. Impacts include: human health problems (worker and population exposure - headaches, nausea), aquatic life and wildlife, birds, and cattle are equally affected as human beings. Groundwater is contaminated by releasing toxic organic chemicals, oil and grease, and metals form airport de-icing and anti-icing operations.66 However, EPA suggests that not all the fluids sprayed in the de-icing and anti-icing operations have a potential impact on U.S. surface waters since there is a chance of losing the fluids during spray time. And the potential impact only comes from the fluids that were sprayed on paved areas. Economic impact and cost to manage waste-water from de-icing and anti-icing operations from a few snow-affected airports in the U.S. are listed in Table 1 from the EPA report.66
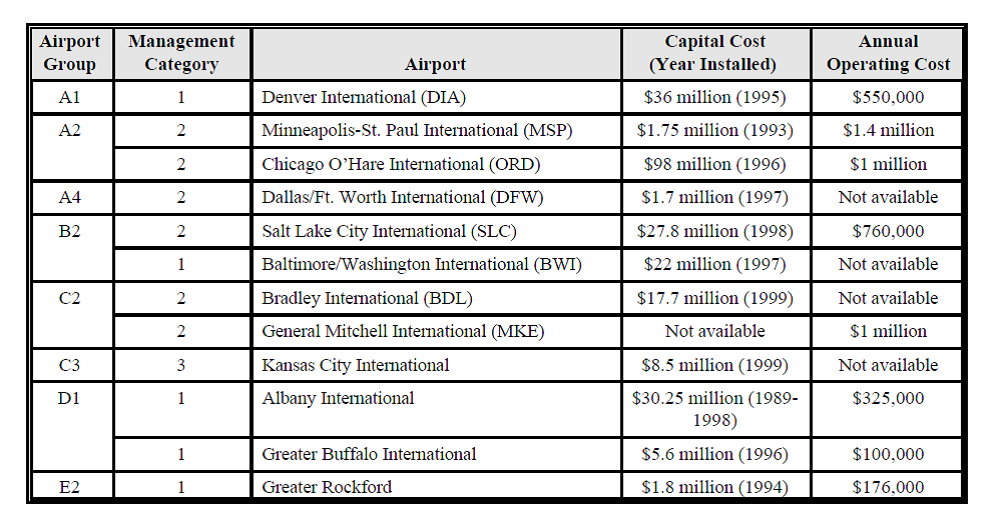
Ultimately, all aforementioned issues make the projects economically more burdensome going further. Increased concerns on environmental safety and the detrimental effect of various chemicals used in previous studies must be taken into consideration for further research.
Acknowledgement
Flora Coating would like to thank Dr. Venkata Sreenivas and Dr. Natarajan Ganesan for their help in preparing this article.
References
1 Salt Institute (1999) Highway Deicing for Safety and Mobility, (http:// www.saltinstitute.org/30.html (accessed June 18, 1999).
2 Paschka, M. G.; Ghosh, R. S.; Dzombak, D. A. Potential Water-Quality Effects from Iron Cyanide Anti-Caking Agents in Road Salt, Water Environment Research, 71(6), 1999, 1235-1239.
3 Fay, L.; Shi, X. Environmental Impacts of Chemicals for Snow and Ice Control: State of the Knowledge, Water, Air and Soil Pollution (2012) 223:2751-2770.
4 Mulherin, N.D. Proc. of the International Workshop on Atmospheric Icing of Structures, IWAIS’96, Chicoutimi (QC) Canada, June 3-6 (1996).
5 Imse, A. The Denver (CO) Rocky Mountain News, January, 24 (2005).
6 Menini, R.; Farzaneh, M. Advanced Icephobic Coatings, Journal of Adhesion Science and Technology 25 (2011), 971-992.
7 Parent, P.; Ilinca, A. Anti-icing and De-icing Techniques for Wind Turbines: Critical Review, Cold Regions Science and Technology 65 (1) (2011) 88-96.
8 Susoff, M.; Siegmann, K.; Pfaffenroth, C.; Hirayama, M. Evaluation of Icephobic Coatings - Screening of Different Coatings and Influence of Roughness, Applied Surface Science 282 (2013) 870- 879.
9 Sojoudi, H.; Wang, M.; Boscher, N.D.; McKinley, G.H.; Gleason, K.K. Durable and Scalable Icephobic Surfaces: Similarities and Distinctions from Superhydrophobic Surfaces. Soft Matter 12, (2016) 1938-1963.
10 Mobarakeh, L.F.; Jafari⁎, R.; Farzaneh, M. Robust Icephobic, and Anticorrosive Plasma Polymer Coating, Cold Regions Science and Technology 151 (2018) 89-93.
11 Lliboutry, L. Traité de Glaciologie. Tome I, Masson & Cie, Paris, 1964, pp. 228-229.
12 Landy, M.; Freiberger, A. Study of Ice Adhesion. Journal of Colloid Interface Science, vol. 25, 1967, pp. 231-244.
13 Laforte, C.; Laforte, J.L.; Carriere, J.C. How a Solid Coating can Reduce the Adhesion of Ice on a Structure, IWAIS (2009).
14 Saito, H.; Takai, K.; Yamauchi, G. Water and Ice-repellent Coatings. Surface Coatings International, vol. 80, no. 4, 1997, pp.168-171.
15 Knight, M.; Clay, W.C. Refrigerated Wind Tunnel Tests on Surface Coatings for Preventing Ice Formation, 1930. NACA-TN-339.
16 Geer, W.C.; Scott, M. The Prevention of the Ice Hazard on Airplanes, 1930. NACATN-345.
17 Rothrick, A.; Selden, R. Adhesion of Ice in its Relation to the De-icing of Airplanes, 1939. NACA-TN-723.
18 Lewis, C.A. Antifreezing Compound. U.S. Patent 1,282,249; 1918.
19 Rolle, C.J.; Barnes, W.D. Cellulose De-icing Lacquer for Stationary Aircraft, Ind.Eng. Chem. 48 (1956) 1326-1327.
20 Raraty, L.E.; Tabor, D. The Adhesion and Strength Properties of Ice, Proc. R. Soc. Lond. A, 245, (1958).
21 Parameswaran, V. Adfreeze Strength of Model Piles in Ice. Can. Geotech. J., 18, (1981) 8-16.
22 Parameswaran, V. Adfreezing Strength of Ice to Model Piles. Can. Geotech. J., 24, (1987) 446-452.
23 Yoshida, M.; Ohichi, T.; Konno, K.; Gocho, M. Adhesion of Ice to Various Materials. Proc., 7th Cold Regions Technology Conf. (1991).
24 Wei, Y.; Adamson, M.; Dempsey, J. Fracture Energy of Ice/Metal Interfaces. Proc., Int. Society for Optical Engineering, SPIE, Bellingham, Wash., (1999) 126-135.
25 Oksanen, P. Adhesion Strength of Ice. Research Rep. 123, Technical Research Centre of Finland, VTT, Espoo, Finland, (1982).
26 JSayward, J.M. Report 79-11, US Army Corps of Engineers, Cold Regions Research and Engineering Laboratory, CRREL, Hanover, NH (1979).
27 Landy, M.; Freiberger, A. Studies of Ice Adhesion: I. Adhesion of Ice to Plastics, Journal of Colloid and Interface Science Volume 25, Issue 2, (1967), pages 231-244.
28 Jellinek, H.H. G.; Kachi, H.; Kittasaga, S.; Lee, M.; Yokoto, R. Journal of Colloid and Interface Science, 256, 544-551 (1978).
29 Lars-Olof Andersson, L.O.; Golander, C.G.; Persson, S. Ice Adhesion to Rubber Materials, Journal of Adhesion Science and Technology,8:2, 117-132, (1994).
30 Croutch, V.K.; Hartley, R.A. J. Coatings Technol. 1992, 64, 41-53.
31 Petrenko, V.F.; Peng, S. Can. J. Phys. 2003, 81, 387-393.
32 Petrenko, V.F.; Whitworth, R.W. Physics of Ice. Oxford University Press, New York. 1999. pp. 243-251.
33 Bascom, W.D.; Cottington, R.L.; Singleterry, C.R. The Adhesion of Ice to Hydrophobic Surfaces, Lab. Report 6350, Naval Research Laboratory: Arlington, VA, 1966.
34 Landy, M.; Freiberger, A. J. Colloid Interface Sci. 1967, 25, 231-244.
35 Bascom,W.D.; Cottington, R.L.; Singleterry, C.R. J. Adhes. 1969, 246-263.
36 Murase, H.; Nanishi, K.; Kogure, H.; Fujibayashi, T.; Tamura, K.; Haruta, N. J. Appl. Polym. Sci. 1994, 54, 2051-2062.
37 Kulinich, S.A.; Farzaneh, M. Langmuir 2009, 25, 8854-8856.
38 Tkachev, A.G.; Malyshev, V.P. Kholodilnaya Tekhnika 8, 15-18 (1976).
39 Le Grand, D.G.; Gaines, G.L. Surface Activity of Block Copolymers of Dimethylsiloxane and Bisphenol-A Carbonate in Polycarbonate, Jr., Polymer Preprints 11, 442, (1970).
40 Byrd, N.R. Polysiloxane(Amide-Ureide) Anti-Ice Coating, US patent No: US 6,797,795 B2 (2004).
41 Menini, R.; Farzaneh, M. Elaboration of Al2O3/PTFE Coatings for Protecting Aluminium Surfaces. Surface Coating Technology 203, 1941-1946, (2009).
42 Menini, R.; Ghalmi, Z. Farzaneh, M. Highly Resistant Icephobic Coatings on Aluminum Alloys, Cold Regions Science and Technology 65 (2011) 65-69.
43 Antonini, C.; Innocenti, M.; Horn, T.; Marengo, M.; Amirfazli, A. Understanding the Effect of Superhydrophobic Coatings on Energy Reduction in Anti-icing Systems, Cold Regions Science and Technology 67 (2011) 58-67.
44 Ferrick, M.G.; Mulherin, N.D.; Haehnel, R.B.; Coutermarsh, B.A.; Durell, G.D.; Tantillo, T.J.; Curtis, L.A.; St. Clair, T.L.; Weiser, E.S.; Cano, R.J.; Smith, T.M.; Martinez, E.C. Evaluation of Ice Release Coatings at Cryogenic Temperature for the Space Shuttle, Cold Regions Science and Technology 52 (2), 224-243, (2008).
45 Kimura, S.; Yamagishi, Y.; Sakabe, A.; Adachi, T.; Shimanuki, M. A New Surface Coating for Prevention of Icing on Airfoils. Proceedings of SAE Aircraft and Engine Icing International Conference, Sep. Seville, Spain, 2007.
46 Antonini, C.; Innocenti, M.; Horn, T.; Marengo, M.; Amirfazli, A. Understanding the Effect of Superhydrophobic Coatings on Energy Reduction in Anti-icing Systems, Cold Regions Science and Technology 67 (2011) 58-67.
47 Menzies, T.R. National Cost of Motor Vehicle Corrosion from Deicing Salt. In R. Baboian (Ed.), Proceedings of the CORROSION/91 Symposium “Automotive Corrosion and Protection” (pp. 1111). Houston: NACE International, (1992).
48 Buckler, D.R.; Granato, G.E. Assessing Biological Effects from Highway Runoff Constituents. U.S. Department of Interior and U.S. Geological Survey Open-File Report 99-240, (1999).
49 D'Itri, F.M. Chemical Deicers and the Environment. Boca Raton: Lewis Publishers, (1992).
50 Levelton Consultants Limited. Guidelines for the Selection of Snow and Ice Control Materials to Mitigate Environmental Impacts. NCHRP Report 577. National Research Council, Washington, DC. (2007).
51 Shi, X.; Fay, L.; Gallaway, C.; Volkening, K.; Peterson, M.M.; Pan, T.; Creighton, A.; Lawlor, C.; Mumma, S.; Liu, Y.; Nguyen, T.A. Evaluation of Alternate Anti-icing and Deicing Compounds Using Sodium Chloride and Magnesium Chloride as Baseline Deicers. Final Report for the Colorado Department of Transportation. Denver, CO. Report No.CDOT-2009-01. 2009.
52 Schraufnagel, F.G. Pollution Aspects Associated with Chemical Deicing, Highway Research Record 193, 1967, 22-33.
53 Environmental Protection Agency Water quality Research: 1971, Environmental Impact of Highway Deicing, Water Pollution Control Research Series, 11040 GKK 06/71.
54 Field, R.; O’Shea, M.L. The USEPA Research Program on the Environmental Impacts and Control of Highway Deicing Salt Pollution, in F. M. D’Itrie (ed.), Chemical Deicers and the Environment Boca Raton, Florida: Lewis Publishing, 1992, pp. 117-133.
55 Field, R.; Struzeski, J.E.; Masters, E.H.; Tafuri, N.A. Water Pollution and Associated Effects from Street Salting, Water Pollution Control in Low-Density Areas: Proceedings of a rural environment engineering conference, 1975, 317-340.
56 Demers, C.L.; Sage, W.R. Effects of Road Deicing Salt on Chloride Levels in Four Adirondack Streams, Water, Air and Soil Pollution 49, 1990, 369-373.
57 Judd, J.H. Lake Stratification Caused by Runoff from Street Deicing, Water Research 4, 1970, 521-532.
58 Ramakrishna, D.M.; Viraraghavan, T. Environmental Impact of Chemical Deicers – A Review, Water, Air & Soil Pollution (2005) 166: 49.
59 Jones, P.H.; Jeffrey, B.A. Environmental Impact of Road Salting, in F. M. D’Itrie (ed), Chemical Deicers and the Environment, Boca Raton, Florida: Lewis Publishing, 1992, pp. 1-97.
60 Bowers, M.C.; Hesterberg, J.H. Environmental Implications of Highway Agents on White Pine in Marquette County, Michigan, Michigan Botanist 15(2), 1976, pp. 75-89.
61 Defourny, C. Environmental Risk Assessment of Deicing Salts, World Salt Symposium, 8th The Hague, Netherlands 2, 767-770, 2000.
62 Brenner, M.V.; Horner, R.R. Effects of Calcium Magnesium Acetate (CMA) on DO in Natural Waters, Resources, Conservation and Recycling 7, 1992, 239-265.
63 Cornell, J.S.; Pillard, D.A.; Hernandez, M.J. Comparative Measures of the Toxicity of Component Chemicals in Aircraft Deicing Fluid, Environmental Toxicology and Chemistry 19(6), 2000, 1465-1472.
64 Corsi, S.R.; Booth, N.L.; Hall, D.W. Aircraft and Runway Deicers at General Mitchell International Airport, Milwaukee, Wisconsin, USA. 1.Biochemical Oxygen Demand and Dissolved Oxygen in Receiving Streams, Environmental Toxicology and Chemistry 20(7), 2001, 1474-1482.
65 Turnbull, D.A.; Bevan, J.R. The Impact of Airport Deicing on a River, The Case of the Ouseburn, New Castle Upon Tyne’, Environmental Pollution 88(3), 1995, 321-332.
66 Preliminary data summary-Airport Deicing Operations, Environment Protection Agency Report, EPA-821-R-00-016, August 2000.
Looking for a reprint of this article?
From high-res PDFs to custom plaques, order your copy today!