A New Approach to Ceramic Matrix Composites

Ann Arbor, Michigan, is considered a hot spot of new technologies, spurred by the local colleges and universities, with the University of Michigan in the heart of it all. Covaron Advanced Materials is a small company amongst this talent and is developing some of the most interesting advancements to the field of ceramic coatings. Covaron’s technology is a new approach to ceramic matrix composites (CMC), introducing advanced-ceramic engineered feedstocks to the world of geopolymers. These new families of materials have high formulation versatility with properties comparable to traditional ceramics. The technology utilizes a unique proprietary chemistry to combine alumino-silicate inorganic network with carefully selected technical-ceramic additives to create a new class of high-temperature-resistant materials, currently being developed under the name PetraForge®.
PetraForge consists of a two-component system that is easily mixed in conventional equipment. Once mixed, PetraForge formulations can form an intermediate gel state at room temperature or remain as a slurry, depending on exact formulation. Once heated to 300 °C, both slurry and gel state materials convert to a ceramic matrix composite. The proprietary chemistry allows mechanical, thermal, electrical, and chemical properties to be customized through modification of the inorganic network on a microstructural level as well as through the use of functional additives. PetraForge is stable up to use temperatures of 1100 °C (current limitations due only to testing equipment).
PetraForge bonds to substrates (e.g. metals, ceramics, glasses, and select polymers) as either a ceramic matrix composite coating or an adhesive, without the process complexity associated with typical ceramics. PetraForge can also be formed either as a high-strength/high-temperature, low-density material through self-foaming ("foam-in-place"), or as complex shapes ceramic matrix composite monoliths due to virtually no shrinkage (< 0.5%) from slurry to final state.
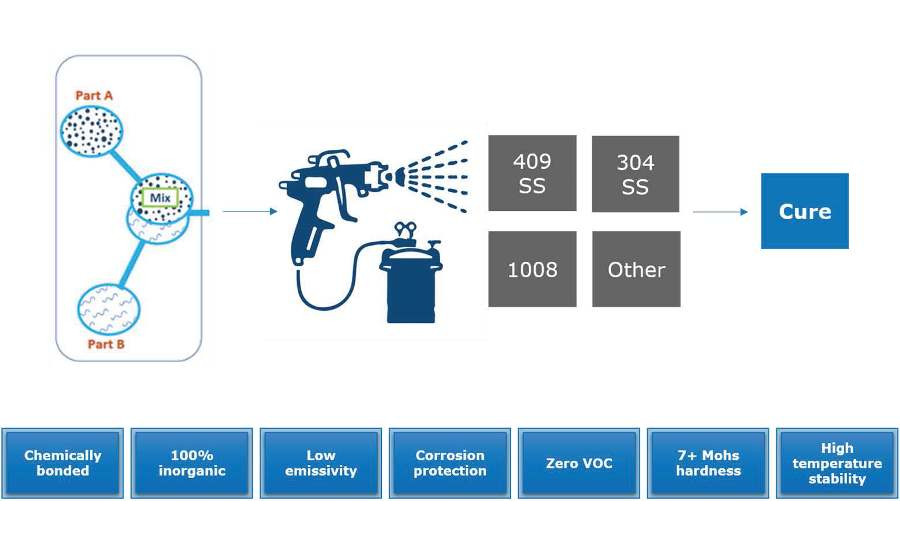
Geopolymers are versatile and useful materials but suffer from very high batch-to-batch variability that is absent in PetraForge. Compared to traditional geopolymers, PetraForge also has higher flexibility and strength, showing remarkable physical properties with substantial levels of performance simply off the comparison charts to regular Geopolymers: A PetraForge thick coating (up to 200 microns) adheres to metal substrates without failure while bending the metal plate over 40 degrees on a 10-mm mandrel, which is generally only possible with very thin geopolymer or ceramic coatings.
Unique combination of properties of PetraForge include:
- Zero VOCs.
- Mohs hardness as high as 7, higher than stainless steel, much higher than competitors’ coatings.
- Can be created with reflectivity as high as 80% (Figure 2), which can result in heat loss reduction of 25-40% in applications such as steel exhaust pipes (Figure 3).
- Flexibility, high enough to bend a thick coating up to 40 degrees on steel substrates (Figure 4).
- Thermal conductivity tunable between 0.5 to 3 W/mK.
- Excellent adhesion to numerous substrates of steels, glasses and bricks.
- Excellent corrosion protection.
- Resistance to most acid and base solutions.
- High electrical resistance.
- Curing temperature of 300 °C.
- Depending on substrates and properties desired, can be sprayed, dipped, or doctor-bladed.
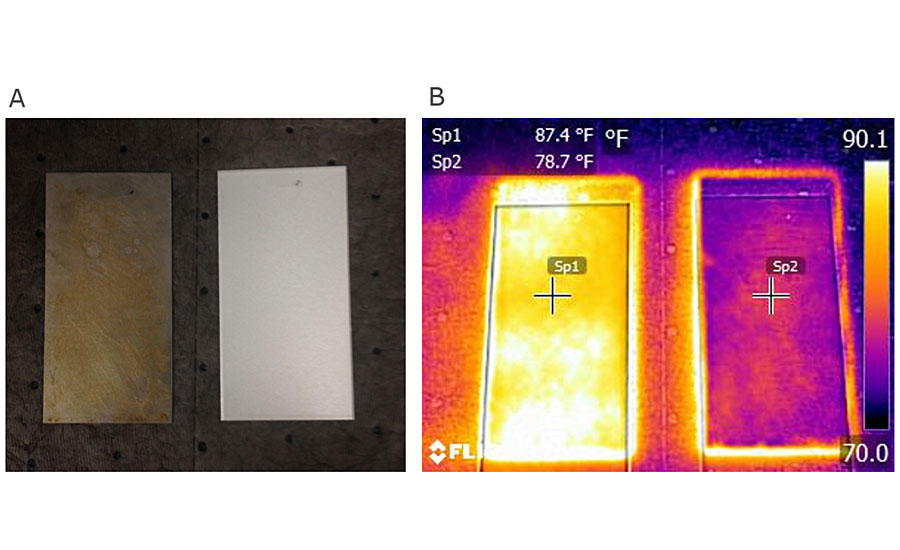
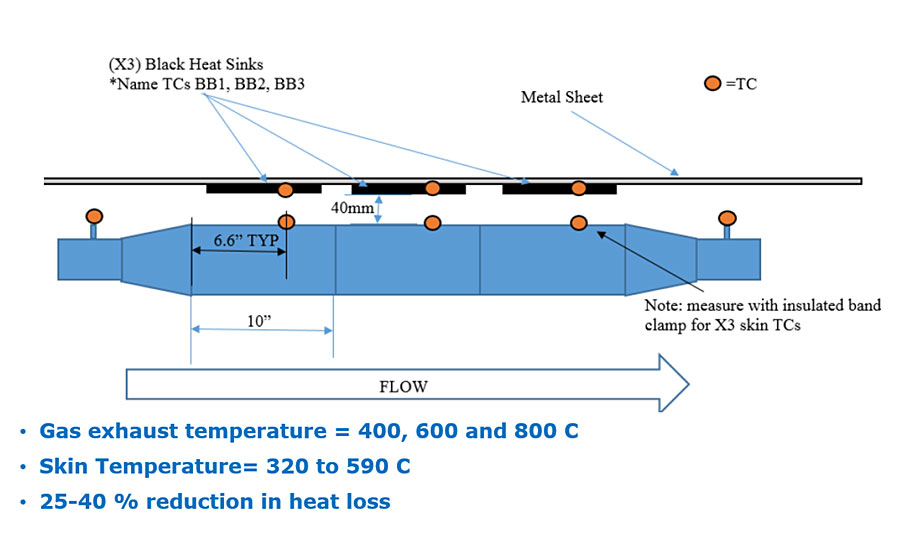
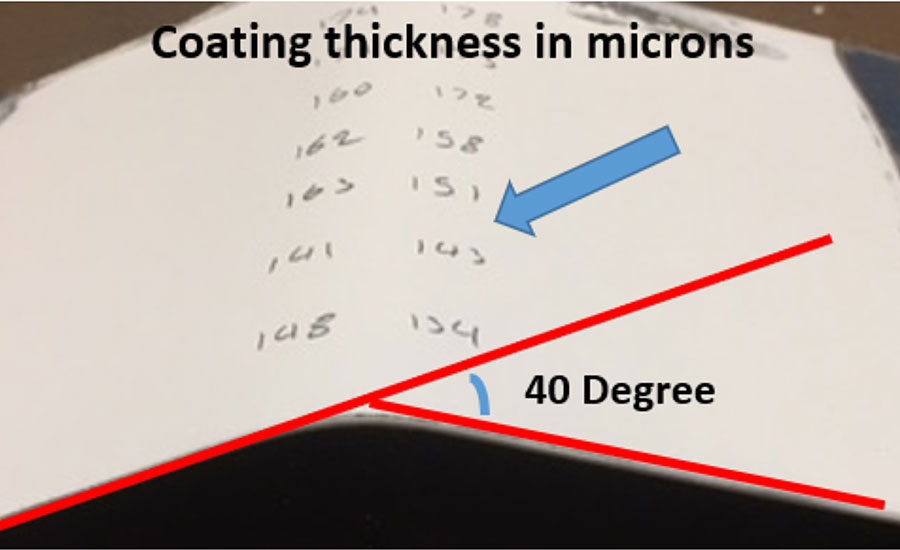
Several adaptations have been done to PetraForge to tune in specific properties based on the application needs. Applications for which PetraForge has been tailored for to meet specific range of properties include:
- Automotive,
- Batteries,
- Furnaces,
- Industrial exhausts,
- Solar cells.
Working on numerous applications has given Covaron the chance to improve PetraForge to withstand the harshest of environmental parameters including temperature weathering from -40 °C to plus 200 °C, operating temperature as high as 1100 °C, and harsh chemical exposure to NaCl, Na2CO3, FeCl3, ZnCl2, acid rain, and various herbicides.
PetraForge adds the advantage of significantly higher hardness and environmental stability to typical high temperature thermal barrier coatings. It is light weight, and can reduce weight and cost of products by reducing/eliminating thermal shields. The resulted 25-40% reduction in heat transfer can increase energy saving by increasing thermal efficiency.
The properties of PetraForge can be tailored to overcome various industrial problems depending on the application needs. Covaron has only started to uncover the possibilities of this material, and PetraForge can be adjusted to unique situations which makes it the ultimate benefit of working with Covaron’s highly talented team.
By Covaron Advance Materials, Ann Arbor, MI
Looking for a reprint of this article?
From high-res PDFs to custom plaques, order your copy today!