Novel Epoxy Systems for Greener Construction

The “Green Building Movement” promotes sustainable construction practices. Hexion supports the underlying goals of this effort by taking an integrated approach to sustainability with the goal of creating long-term stakeholder value through environmental and product stewardship, safety and compliance. This sustainability initiative guides product development within existing green building initiatives. The specialty epoxy resins and amine curing agents in this article offer performance improvements, as well as, the benefits of lower VOC content and lower indoor emissions.
Infrastructure Refurbishment versus Replacement
After years of deferring maintenance, owners and municipalities are recognizing the benefits of well-maintained infrastructure components such as flooring, roofing, decking, pavement, supportive structures and the reinforcing elements in high-profile applications. The preferred approach to achieving quality and aesthetic requirements in today’s cost-sensitive environment is to refurbish versus replace. In most cases, the less-costly option is to maintain and repair for extending the service life of infrastructure.
Higher Performance Waterborne Epoxy Systems
Growing government and public sector preference for sustainable development is driving lower VOC regulations on a global basis. This “green wave” is inspiring change across the construction industry. Higher performance waterborne epoxy systems address the growing market need for longer service life, lower VOC content and higher performance. Leveraging the key drivers of better performance and lower cost at lower VOCs are important as waterborne systems continue to replace traditional solventborne epoxy/polyamide coatings on a global basis. 1
Ultra-low VOC content (less than 50 g/L) and higher performance can be achieved by using a cosolvent-free epoxy dispersion, EPI-REZ™ Resin 7720-W-50 and a hydrophobic amine adduct emulsion, EPIKURE™ Curing Agent 6870-W-53. Both epoxy resin and curing agent components utilize proprietary, non-ionic surfactants that are pre-reacted into the resin backbone. Properties of the resin and curing agent are summarized in Table 1.
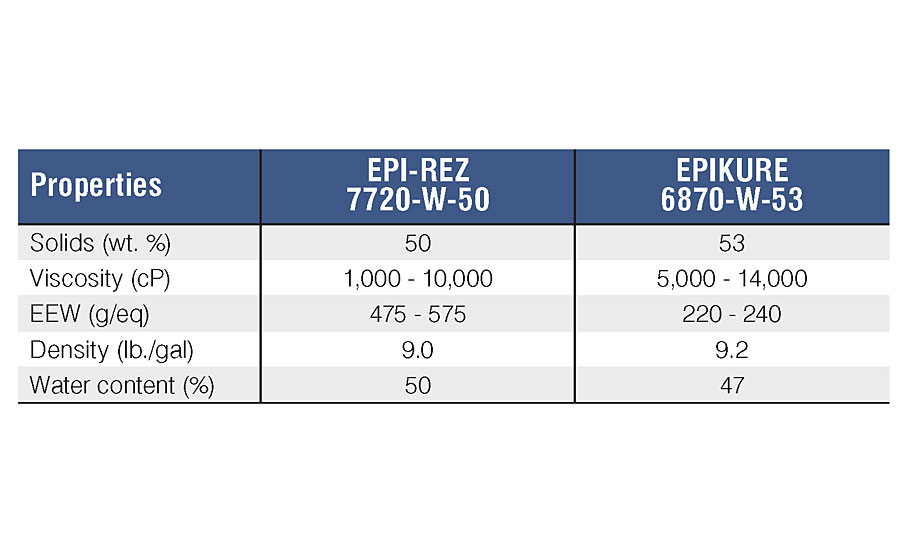
Figure 1 shows examples of starting formulations for an ultra-low-VOC, high-gloss white enamel and high-gloss clear sealer.
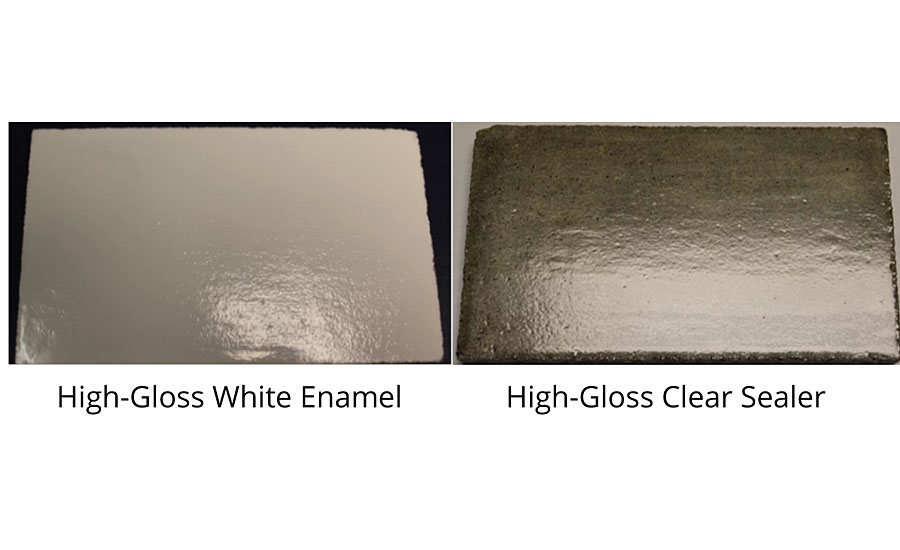
In a white primer at less than 50 g/L VOC, this high-performance waterborne epoxy system can be formulated to provide superior water resistance, improved corrosion resistance and long pot life. Table 2 compiles the data for two coatings systems applied over concrete and metal.
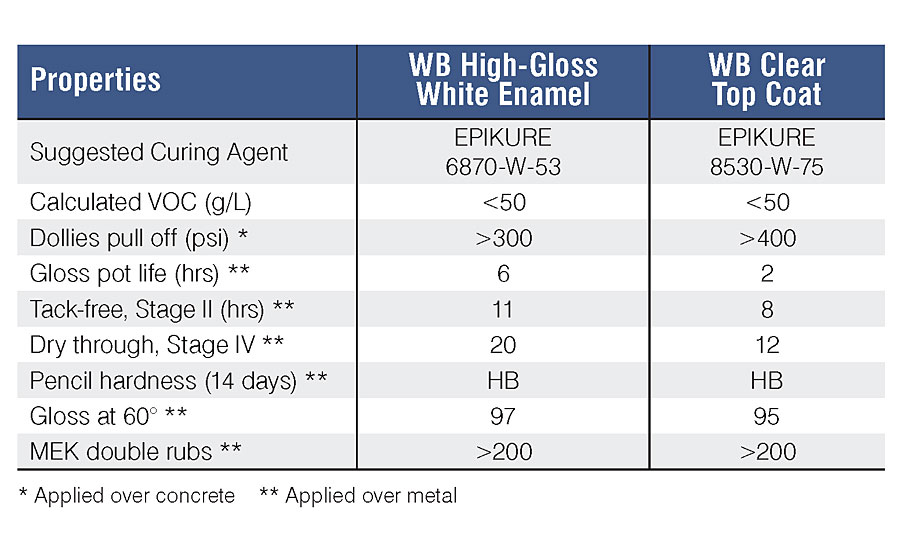
Figure 2 compares 1,000 hrs salt spray performance of an ultra-low-VOC primer formulation with the new epoxy resin dispersion to a commercial solventborne, solid epoxy resin/polyamide curing agent. Both coatings were applied to cold rolled steel at 3 mils dry film thickness and then cured for seven days at ambient conditions (77 °F, 55% R.H.). The waterborne epoxy coating outperforms the solventborne control in terms of corrosion resistance (field blisters and scribe creep).
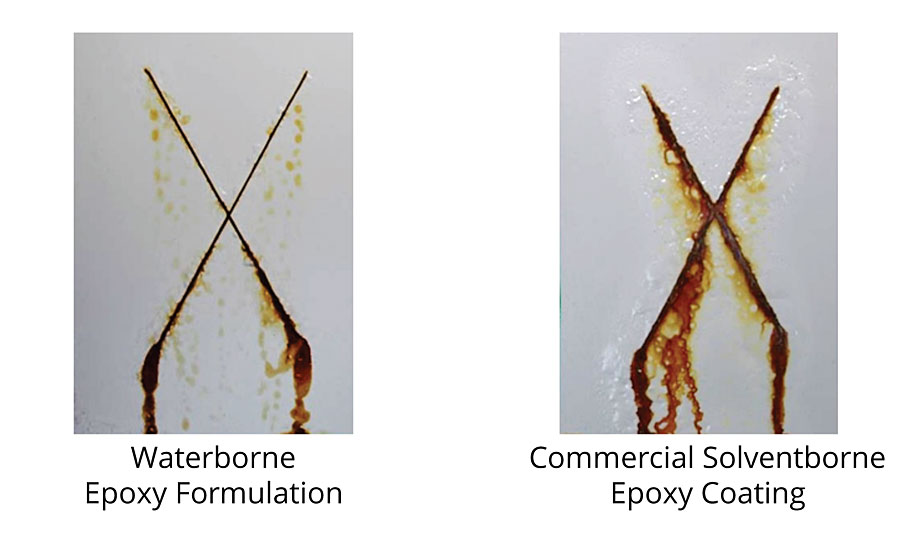
Higher Solids, Solventborne Epoxy System
In June 2018, the U.S. EPA designated 51 areas of the country as non-attainment zones. These areas can be expected to adopt lower VOC limits in the future. 2 So as a result, the use of solventborne, Type-1 solid epoxy resin will continue to be challenged. The simplest way to meet these lower VOC requirements is to switch to an intermediate molecular weight, higher solids resin. As shown in Table 3, the viscosity of EPIKOTE™ Resin 874L-X-90 is significantly lower than the solution viscosity of a Type-1 solventborne resin such as EPON™ Resin 1001-X-75. Changing to a higher solids epoxy resin enables formulation of coatings that meet a 250 g/L VOC maximum requirement while maintaining excellent performance.
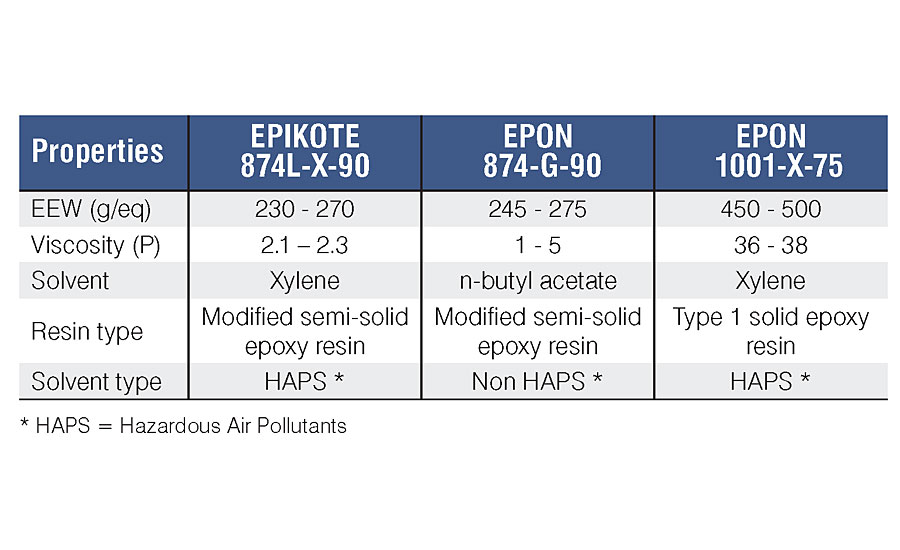
These higher solids epoxy resins provide lower viscosity and equivalent corrosion resistance when compared to the Type-1 epoxy resin. This cost-effective epoxy resin can be combined with a benzyl alcohol-free curing agent, EPIKURE Curing Agent 3175, for either metal or concrete protection. This high-solids system features faster dry times, better corrosion resistance and longer pot life than standard liquid epoxy resins.
Solvent-Free Amine Curing Agents
Amine Curing Agent for Lower Indoor Air Emissions
It is well-known in the construction industry that properly cured epoxy resin and amine curing agent systems can be formulated into special purpose coatings with high mechanical strength and superior chemical resistance. A unique amine curing agent, EPIKURE Curing Agent 580, when combined with a modified epoxy resin, EPIKOTE Resin 240, yields the same high performance versus a commercial cycloaliphatic curing agent, as shown in Table 4.
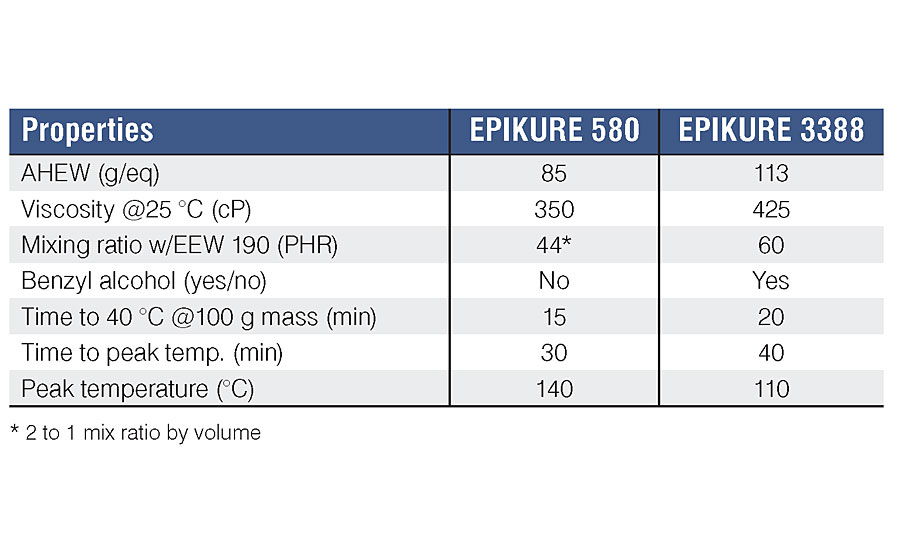
This amine curing agent does not contain benzyl alcohol or any other component with a boiling point of less than 250 °C. Furthermore, the amine curing agent does not contain nonylphenol and it offers ultra-low BPA content. Formulations based on this curing agent provide superior workability, good surface quality, higher reactivity and excellent hardness development in self-leveling flooring applications.
DIN EN 13419-2 Test Method measures the emission of volatile organic compounds in a formulation using a specific test cell. This method determines an area-specific emission rate of VOCs from building products under defined conditions. The emission data obtained can be used to calculate volatile concentrations in a model room.
Chamber tests were performed on the lower emission curing agent according to the European AgBB Scheme. In this AgBB evaluation, samples of the neat epoxy system, without any added fillers or solvents, were cured at ambient temperature and stored in a closed test chamber for 28 days at 23 °C. Figure 3 shows VOC emissions as determined by gas chromatography after 3 and 28 days per DIN 13419. The test results confirm a much lower emission level for EPIKURE 580 versus a standard cycloaliphatic amine curing agent, EPIKURE 541.
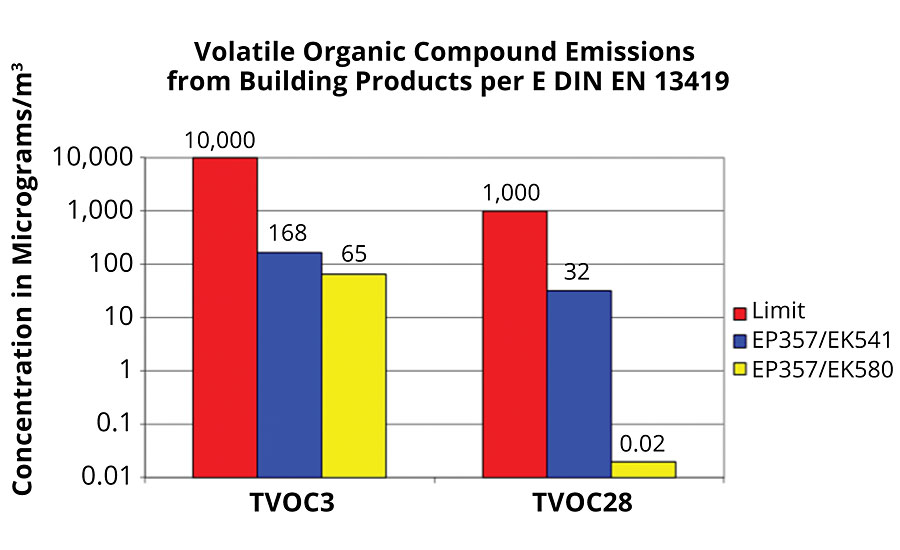
Flexible Amine Curing Agent
A flexible amine curing agent, EPIKURE Curing Agent 3204, offers a unique combination of lower viscosity, low equivalent weight, lighter color and improved curing profile. This flexible curing agent does not contain any benzyl alcohol or any nonyl phenol. Combinations with liquid epoxy resins provide very good adhesion to metal and concrete in applications where a high degree of substrate movement is expected. Table 5 summarizes the physical and cured state properties.
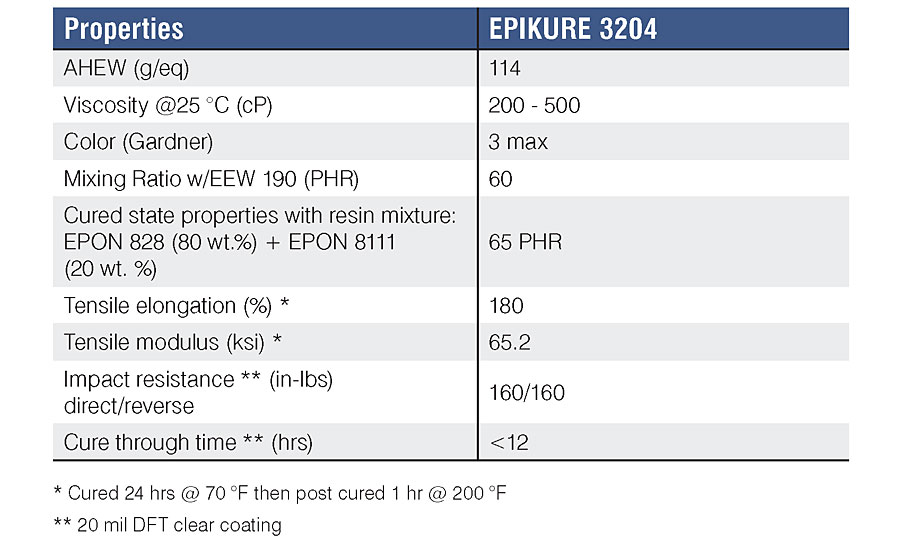
Moisture Vapor Barriers
A solvent-free epoxy system has been specially designed for formulating moisture vapor barrier coatings. This moisture vapor suppression system (MVSS), EPIKURE Curing Agent 3393 and EPON Resin 233, has been confirmed by third-party testing to provide perm ratings of <0.10 perms. With this low perm rating, when properly formulated and applied to well-prepared concrete surfaces, the resulting formulation may be considered a Class 1 Vapor Diffusion Retarder. These Class 1 coating formulations are potentially suitable for use under a variety of finish floor coverings such as vinyl tiles and sheeting, rubber-backed carpet, hardwood and solvent-free epoxy floor coatings.
In Figure 4, the highlighted area in green represents where the testing model predicts Class 1 Vapor Diffusion Retarder capability. Minimum coating film thickness for obtaining the Class 1 rating depends on concrete cure time. 3
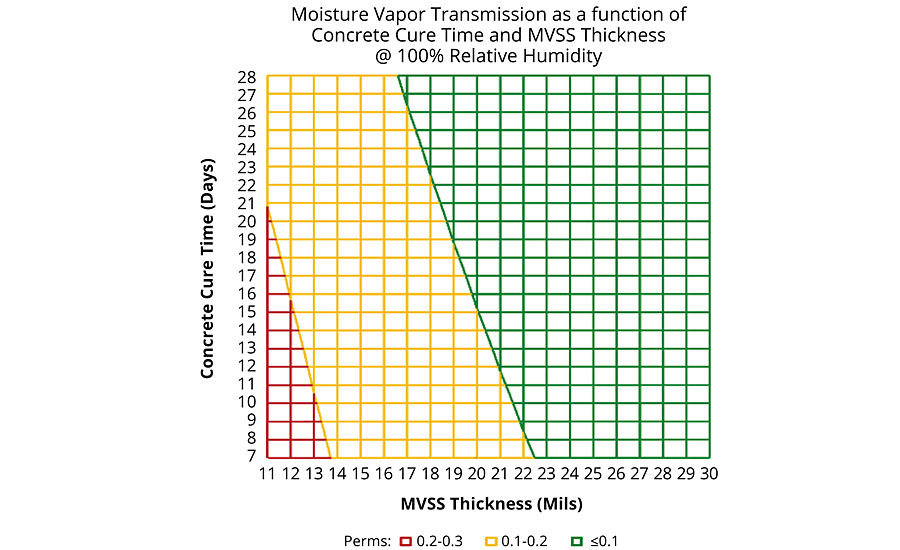
Lower Yellowing Epoxy Systems
Modified Cycloaliphatic Amine Curing Agents
One of the first options to improve weathering performance is to use a lower yellowing cycloaliphatic amine curing agent. This class of curing agents provides superior chemical resistance, high gloss, low viscosity and are widely used in coatings and flooring, machinery bases, tank linings, secondary containment, and low-temperature-cure applications.
Hydrogenated Epoxy Resin
The lower yellowing, improved chalk resistance and excellent gloss retention of systems based on a hydrogenated epoxy resin, EPONEX™ Resin 1510, are suitable for use in a wide range of end-use applications including gel coats, decorative aggregates and castings. The combination of a cycloaliphatic resin with a modified cycloaliphatic amine curing agent provides improved UV resistance.
Figure 5 compares the yellowing resistance of several epoxy systems after 7 days QUV-A exposure. The top row of panels illustrates performance of a standard cycloaliphatic curing agent with a diluent-modified, BPA-based epoxy resin. The second row shows performance of EPIKURE 196 with the same epoxy resin. The last row combines the hydrogenated epoxy resin EPONEX 1510 with the lower yellowing, cycloaliphatic amine curing agent EPIKURE 196.
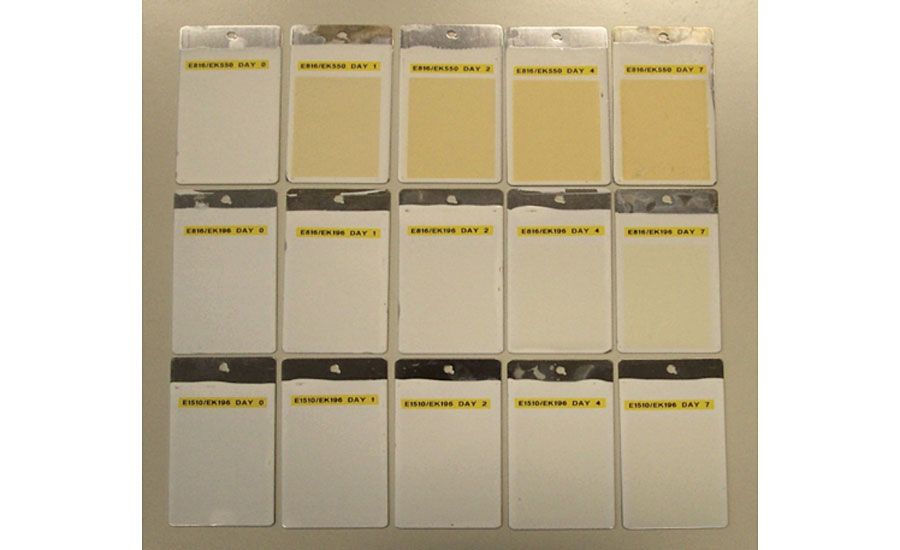
Epoxy Polysiloxane Hybrid Resin
Combining an epoxy polysiloxane hybrid resin, EPOSIL™ Resin 5550, with an amino-functional silane curing agent yields significantly improved coating performance. The properties of the epoxy polysiloxane resin are summarized in Table 6.

Table 7 compares a white pigmented enamel based on the epoxy polysiloxane hybrid system with two commercial offerings, one in a standard white enamel (Commercial A) and one (Commercial B) in a clear formulation. Notable benefits of the hybrid epoxy enamel compared to the commercial systems include superior hardness, lower mix viscosity and longer pot life.
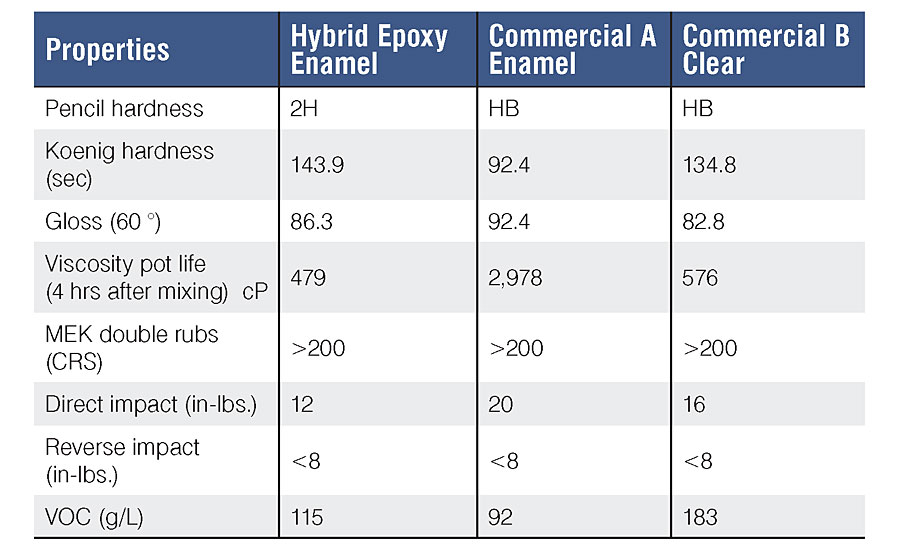
The viscosity pot life of all three systems, hybrid epoxy, Commercial A and B, are shown in Figure 6. The commercial coatings (A and B) are known to contain hybrid epoxy/polysiloxane resins, so this represents a fair benchmark comparison test. The pot life study shows that the hybrid epoxy formulation using EPOSIL 5550 has much lower mix viscosity across the entire 4 hrs of pot life.
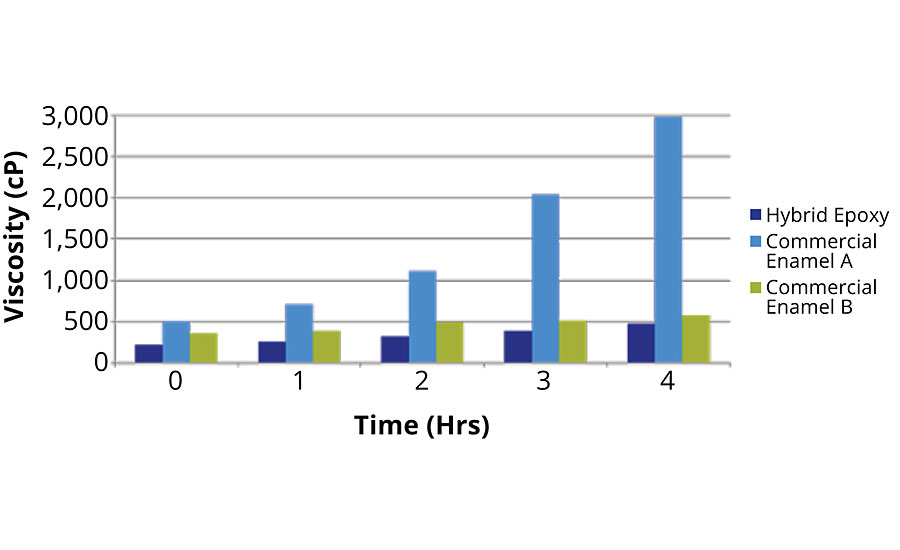
Figure 7 summarizes Delta E data for all three systems, Hybrid Epoxy, Commercial A and Commercial B. After 1,000 hrs QUV-A exposure, the white enamel formulation has comparable Delta E (yellowing change) of less than 2.
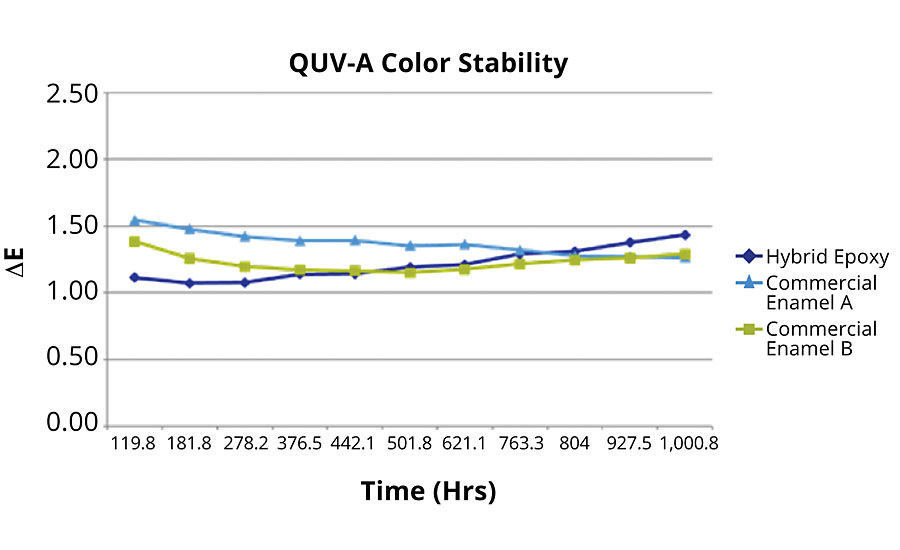
Epoxy/polysiloxane hybrid resins can be formulated into non-isocyanate cure coatings with lower yellowing, lower mix viscosity and higher temperature resistance. Another benefit of epoxy polysiloxane technology is the potential to remove a coating layer from the application process. This provides tremendous value to the end-use customer.
Epoxy systems are known for their excellent corrosion resistance and now with significantly improved gloss retention, it may be possible to convert a three-layer coating system to a two-layer coating system (Figure 8). This reduces labor costs and enables faster turn-around times.
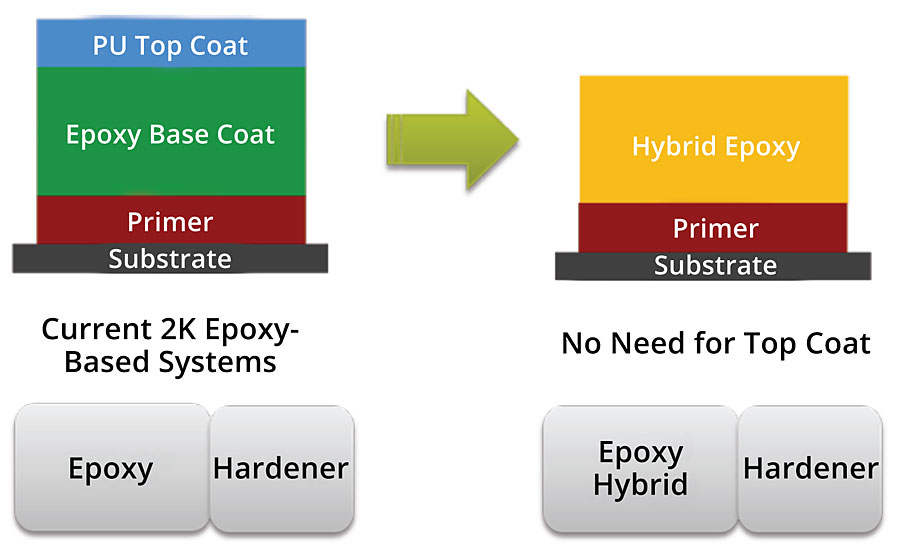
When crosslinked with amino silane curatives, polysiloxane epoxy hybrid resins yield an interpenetrating network that provides improved weathering resistance, higher temperature resistance and reduced dirt pick-up in outdoor environments. These epoxy polysiloxane hybrid topcoats can be formulated into clear and pigmented coatings with the potential for graffiti resistance due to complete removal of permanent marker inks after 24 hrs (Figure 9).
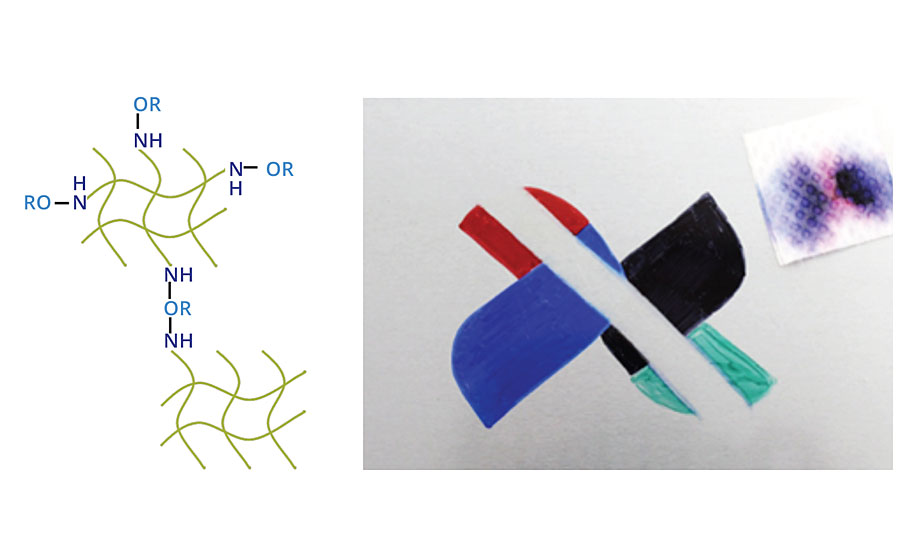
Standard epoxy coatings are generally limited to operating service temperatures below about 400 °F. Hybrid epoxy polysiloxane resins such as EPOSIL 5550 have a higher heat resistance (lower weight loss) at sustained elevated temperatures (up to ~600 °F) as shown in Table 8.
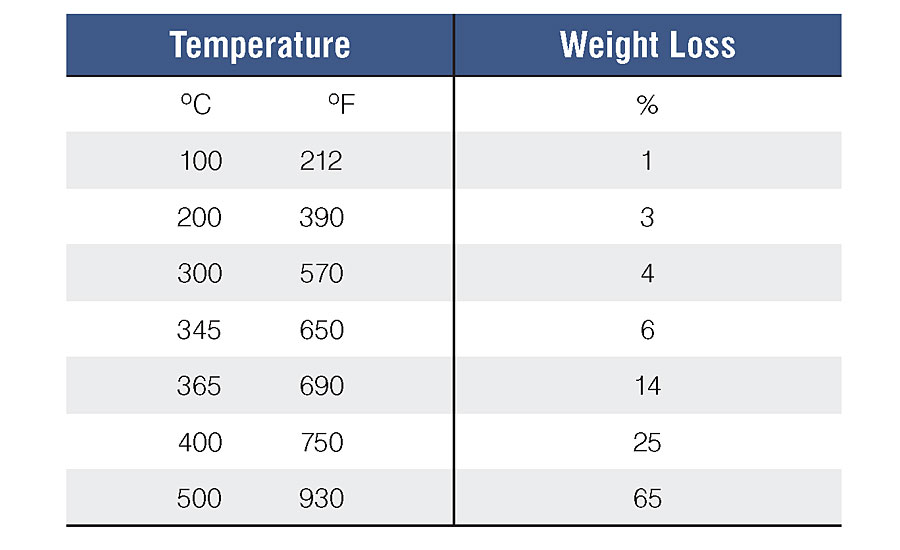
Conclusions
Public and private sector entities are embracing sustainability initiatives, and the construction industry is no exception. Greener product offerings with lower solvent emissions (VOCs), lower indoor air emissions and higher performance enable formulators to develop more sustainable (greener) options for their customers (i.e., contractors, engineers, architects and owners).
For example, ultra-low VOC formulations based on cosolvent-free waterborne epoxy dispersions or higher solids epoxy resin solutions address the market’s desire for VOC compliance and higher performance. Solvent-free amine curing agents provide options for either lower indoor air emissions or urethane-like flexibility. A specially designed epoxy system can deliver a moisture vapor suppression rating of <0.1 perms (Class 1 moisture barrier). And finally, there are options to achieve improved yellowing resistance and longer service life with aliphatic epoxy resins. The epoxy systems in this article can be formulated into cementitious coatings, underlayment, joint fillers, adhesives, anti-corrosive primers and topcoats that perform in the most challenging conditions.
References
1 Vogt, H. et. al. Global Waves of Change, Paint & Coatings Industry, Aug. 2019, p. 27-31.
2 https://www.paint.org/colorado-aim/”Colorado to Develop Architectural and Maintenance AIM and Consumer Products Rules”, July 17, 2018.
3 “Superior Moisture Vapor Control using EPON™ Resin 233 with EPIKURE™ Curing Agent 3393 Epoxy System”, publication number HXN-707 from Hexion Inc.
Looking for a reprint of this article?
From high-res PDFs to custom plaques, order your copy today!