FEVE fluoropolymer-based coatings have been used in architectural and industrial coatings for nearly 40 years. Coatings formulated with fluoroethylene vinyl ether (FEVE) resins exhibit excellent corrosion resistance and weatherability, providing protection against UV rays, wind, precipitation, dirt and chemicals. This coating technology also provides long-term gloss and color retention for 30 years or more. Because of their long life, FEVE-based coating systems reduce lifecycle coating costs, improve asset utilization and eliminate the need for multiple painting cycles.
As the coatings industry looks to adopt greener technologies, while maintaining performance properties and cost control, interest in FEVE powder resins is gaining interest. They can provide exceptional weatherability, corrosion resistance and environmental benefits when used in exterior architectural coatings applications. These resins do not require a solvent (zero VOC), and have high recyclability and reclaimability. FEVE powder resins can be used in formulations to meet the American Architectural Manufacturers Association (AAMA) 2605 specification (FGIA), the highest standard for organic coatings on architectural aluminum extrusions and panels.
The new research presented in this article examines weathering performance and corrosion resistance using electrochemical impedance spectroscopy testing of FEVE powder-based topcoats on aluminum substrates.
FEVE Chemistry
FEVE resins are amorphous A-B type copolymers with repeating units of fluoroethylene and substituted vinyl ether (Figure 1). Unlike pure fluoropolymers, FEVE resins are soluble in solvent due to the vinyl ether groups. Solvent solubility transforms FEVE resins from high-performance polymers into high-performance resins for coatings.
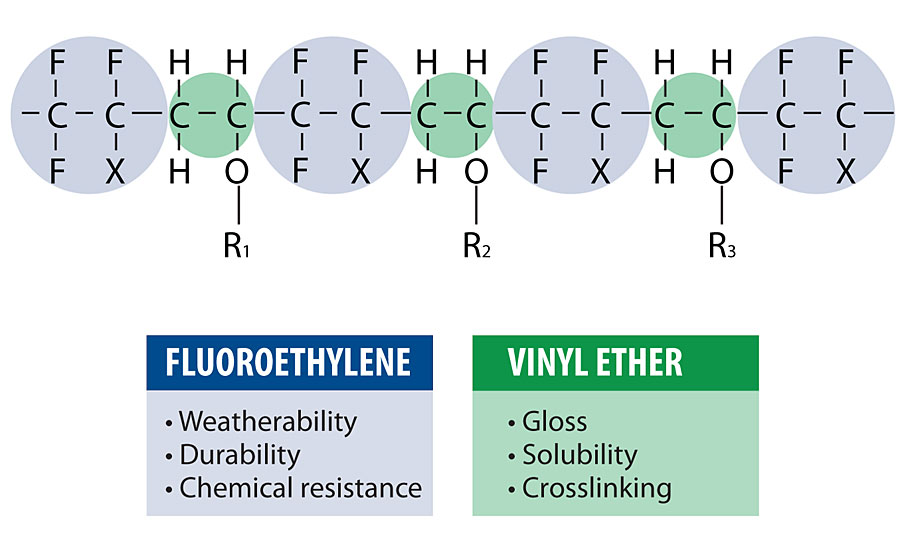
FEVE resins have characteristics of both fluoropolymers and hydrocarbons. The fluoroethylene groups are the strength of the FEVE resin. These groups are what make this class of polymers so resistant to UV degradation. The C-F bond is strong. The energy of this bond is ~486 kJ/mol, 1 while the energy of UV radiation at 300 nm is ~399 kJ/mol. The alternating pattern is critical for the extreme UV resistance properties. The chemically stable and UV-resistant fluoroethylene unit sterically and chemically protects the neighboring vinyl ether unit.
The vinyl ether groups make FEVE polymers usable as resins for paint. Without the vinyl ether groups, FEVE resins would not be soluble in solvents. This solubility is what allows FEVE resins to be used in a wide array of coating formulations that can be applied in factory or field settings. The vinyl ether groups also contribute to high gloss and allow for functional groups, like hydroxyl groups, to be incorporated into the structure.
FEVE resins are an excellent choice for coating formulations as they are offered in a range of grades with varying properties like molecular weight, hydroxyl value and Tg (Table 1). FEVE resins tend to be glassier in nature but are easily blended with other resins when more flexibility is needed.
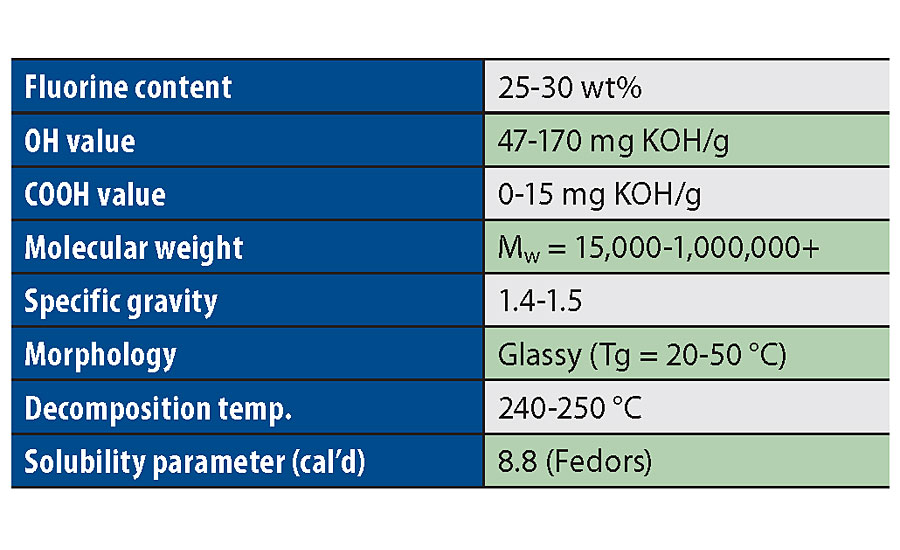
Historical FEVE Testing
Years of weathering testing has shown the superior performance of coatings based on FEVE resins. This data has been discussed extensively in earlier research. 1 A 15-year exterior exposure study of two white 2K polyurethane coatings was performed in Japan (Figure 2). One system was based on a conventional acrylic polyol polyurethane system, and the other was based on an FEVE-based polyol polyurethane system. A red, light-sealed tape was used to cover a portion of each panel. This area was considered the unexposed area. The results of the following tests showed that after 15 years, the panel protected with the FEVE-based system demonstrated significant protection from corrosion and weathering.

Highlights from weathering testing research are found in Fig 3-8.
Visible Light Photomicrographs
Figure 3 shows significantly less erosion with the FEVE-based white coating compared with the polyurethane-based white coating.
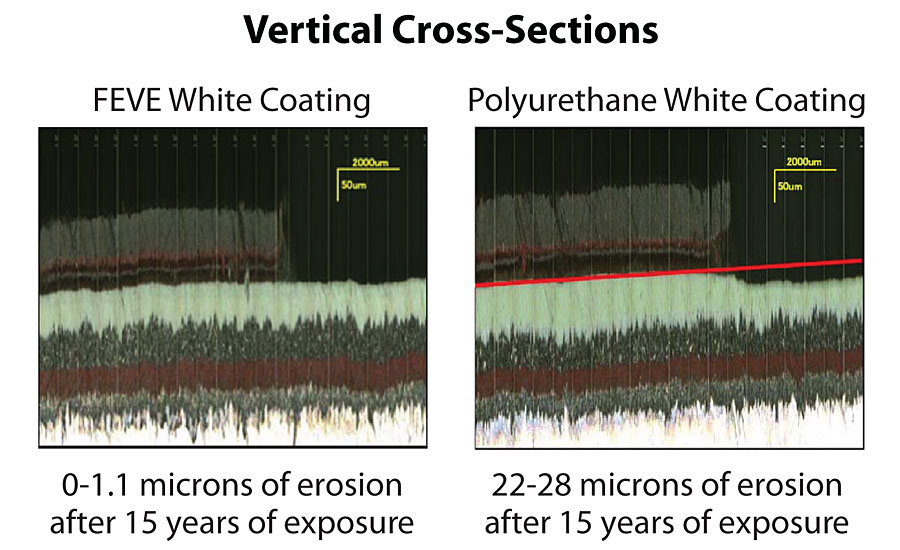
QUV-A Weathering
The QUV® accelerated weathering test shows that FEVE-based coating significantly outperforms polyurethane and acrylic urethane coatings in gloss retention over time (Figure 4).
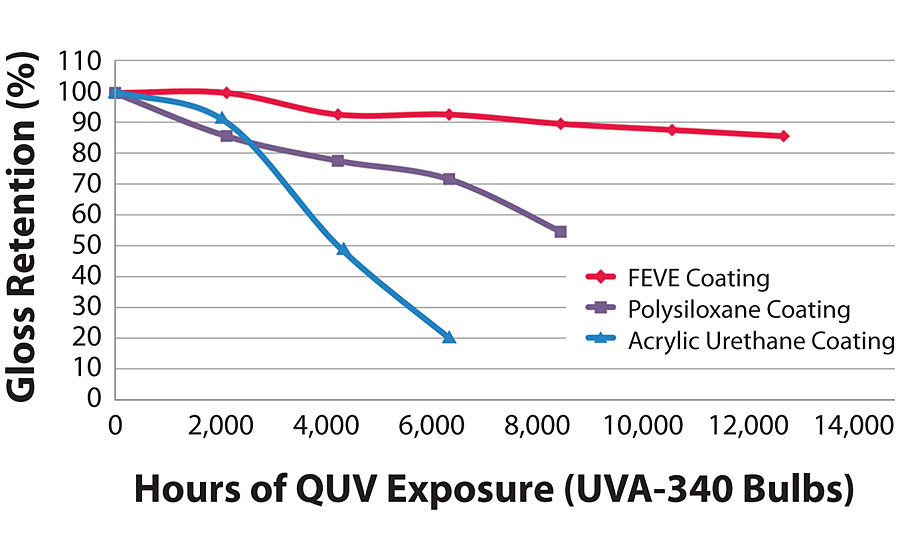
EMMAQUA ® Testing
EMMAQUA (Equatorial Mount with Mirrors for Acceleration with Water) testing shows the gloss retention of the FEVE-based coating is similar to that of a PVDF coating and significantly better than an acrylic urethane coating (Figure 5).

Florida Weathering
A Florida weathering test shows that the FEVE-based coating performed better after 10 years of exposure than high-performance polyester after only three years (Figure 6). After 10 years, an FEVE-based coating and PVDF coating performed similarly, and both retained color and gloss much better than the polyester coating.
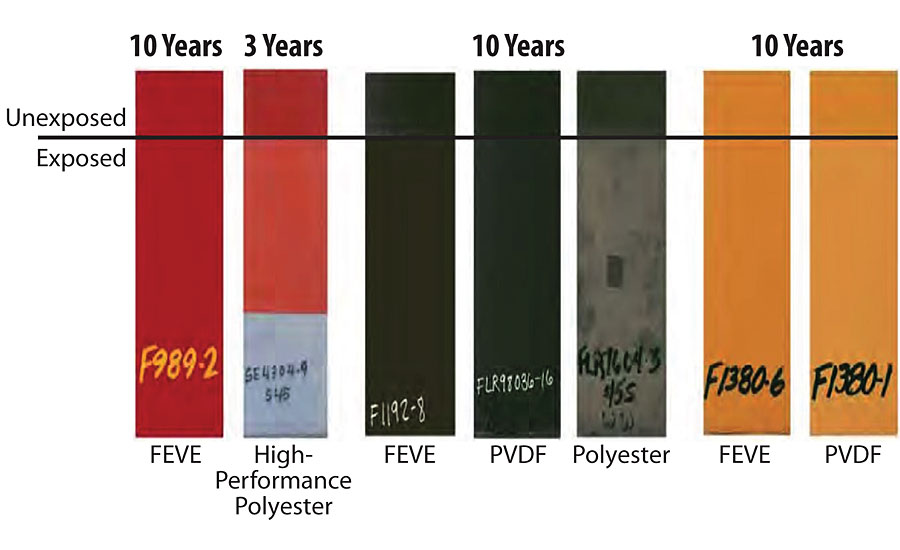
A 10-year Florida weathering test compared the gloss retention of FEVE yellow coating and FEVE clear coat (Figure 7). At four years, the FEVE yellow coating still retained 100% of its gloss and retained 70% at 10 years. The FEVE clear coating retained over 80% of its gloss at three years and 70% at 10 years.
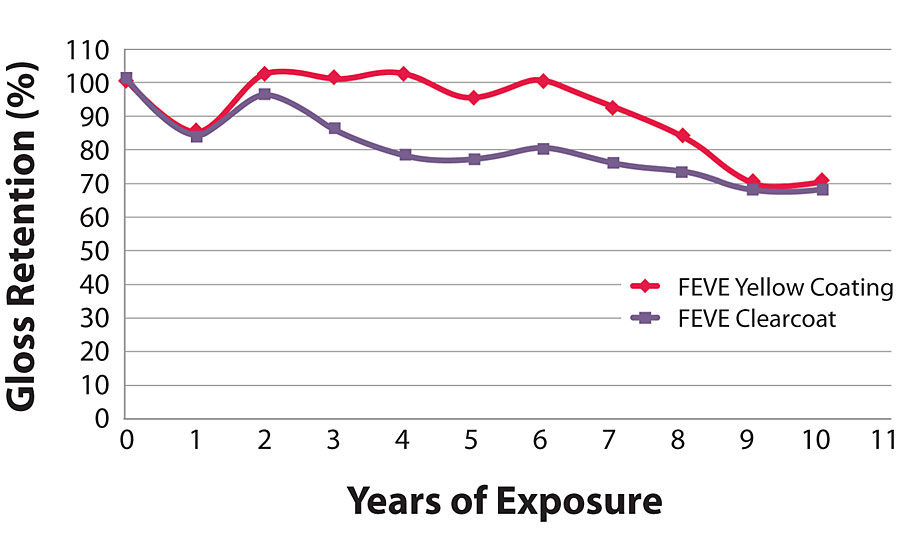
Real-Time Weathering on Offshore Platform
An FEVE-based fluorourethane topcoat was tested alongside an acrylic urethane topcoat at an offshore platform test station (Figure 8). Each coating system consisted of a 3-mil zinc-rich primer, 6 mils of a middle coat and a 25-micron (1-mil) topcoat. After 13 years, the acrylic urethane topcoat had completely deteriorated. At 16 years, the FEVE topcoat still measured a thickness of 21 microns.
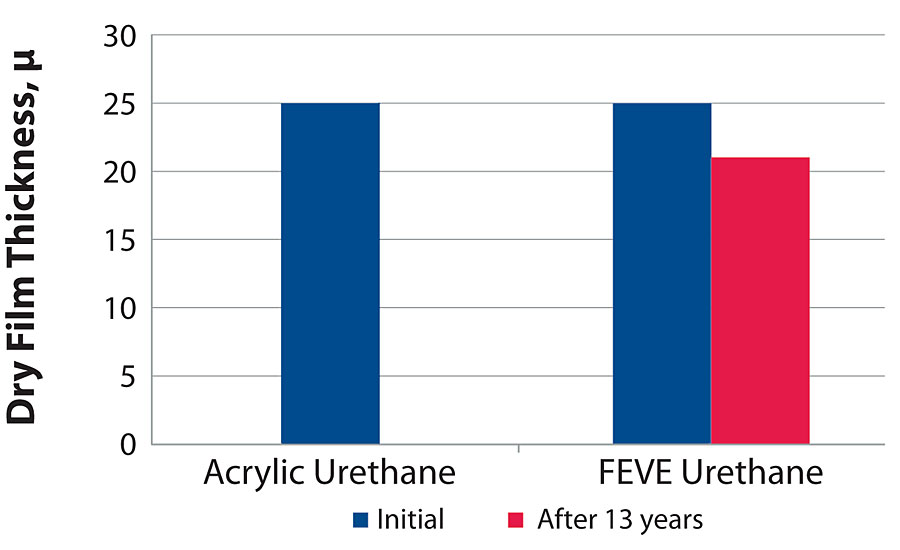
FEVE Resins for Powder Coatings
Much of the research on the performance of FEVE-based coatings has been conducted with solvent-based coatings. This data is useful as a reference and an indication of the general performance properties of FEVE-based coatings. However, as the coatings industry is shifting away from solvents, we conducted the following research to gather performance data on FEVE-based powder coatings.
FEVE powder resins are used in crosslinked thermoset powder coatings and are applied via electrostatic spray, as is typical for conventional powder coatings. Powder coatings based on FEVE powder resins are used for long-life coatings that meet the requirements of the AAMA 2605 standard. Figure 9 shows FEVE powder resin properties.
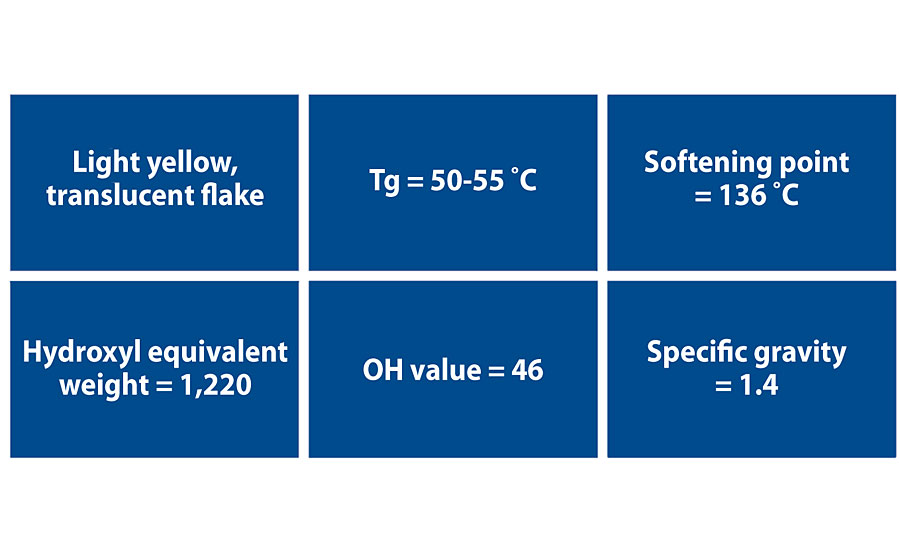
Accelerated weathering testing was conducted with a powder formulation of FEVE flake resin, B-1530, benzoin, leveling agent and pigment (Figure 10). A QUV-B test demonstrated sustained gloss retention from 100% to 90% over 10,000 hrs. The results of an EMMAQUA test showed gloss retention of 80% at 3,000 mega Joules per meter squared. For reference, 3,000 MJ/m 2 of irradiance is similar to the output of the sun over the course of 10 years.
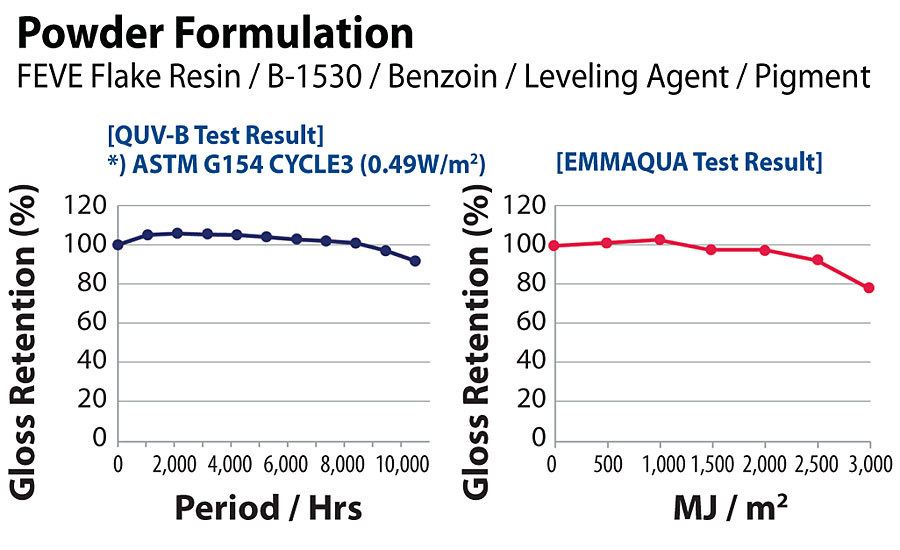
Ten-year natural exposure tests were conducted on a brown FEVE powder-based coating (Figure 11). The Florida exposure test demonstrated gloss retention of 79% at 10 years, while the Okinawa test showed 60% gloss retention at the same duration.
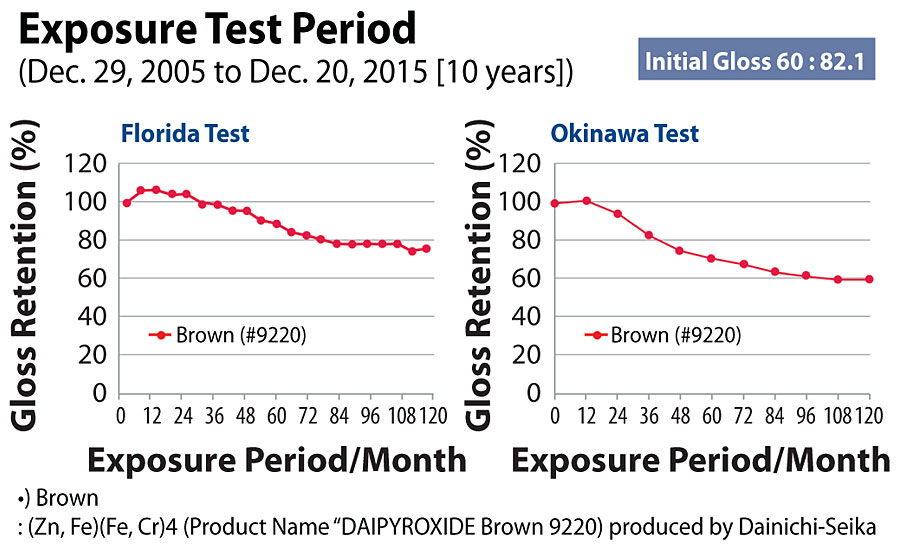
A South Florida weather test showed over 90% gloss retention of both a clear FEVE powder coating and a white specialty pigment FEVE powder coating at nine years (Figure 12).
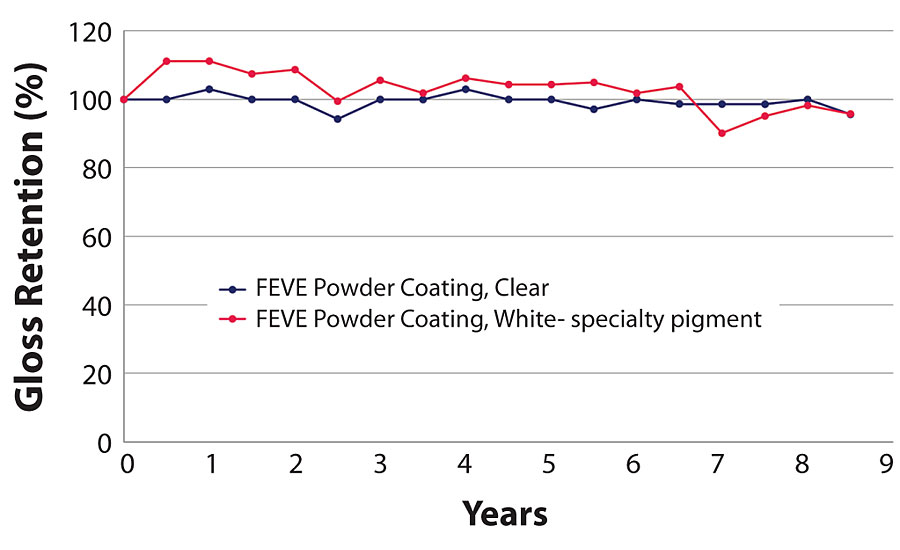
FEVE in Corrosive Environments
Corrosion impacts both steel and aluminum substrates, causing damage and adding to lifecycle costs. Especially impacted by corrosion are structures like steel bridges over brackish or salt water, aluminum extrusions near the seacoast and aluminum curtain walls in northern metropolitan climates exacerbated by road salts. Liquid coatings over steel often use a two- or three-coat system utilizing zinc-rich primers. Because aluminum corrodes differently than steel, it is often pretreated with chromium, although chromium-free treatments are being studied now.
FEVE-based coatings resist degradation by UV light and corrosives, and serve as a barrier to prevent or slow moisture and salt intrusion. Liquid FEVE coatings have been used on bridges over seawater for 35 years. Analytical and accelerated tests show FEVE resins offer excellent barrier properties that last over decades.
Figure 13 shows a comparison that we conducted of liquid FEVE-based topcoats with other common topcoat chemistries currently used on steel structures in the standard ASTM B117 salt fog test. The results show that FEVE topcoats provide similar or better barrier protection compared to the industry standard technology.
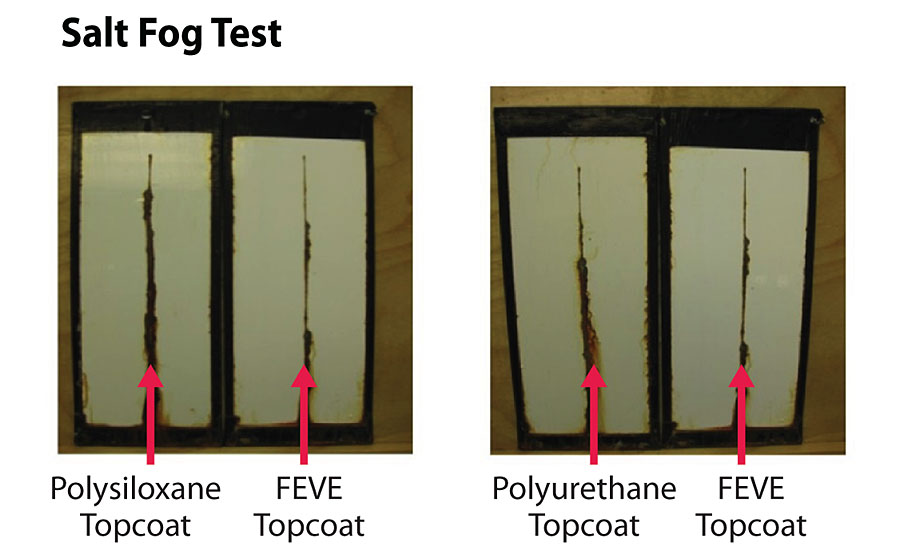
Electrochemical Impedance Spectroscopy Testing
In electrochemical impedance spectroscopy (EIS) testing, alternating current (AC) voltage is applied at different frequencies to the sample, and the current is measured. Evaluation involves fitting raw data to electrical circuit models. This can determine the contribution of various frequency-dependent components such as capacitors, constant phase elements (CPE) and Warburg diffusion elements.
Early EIS studies of FEVE coatings showed that while the initial impedance of FEVE chemistry is similar to other coating chemistries, FEVE coatings maintain a much higher percentage of the original impedance after aging and exposure to the elements. FEVE coatings are able to maintain strong barrier protection with aging compared to conventional coatings due to the superior weatherability that FEVE resins exhibit (Figure 14).

EIS testing was used to compare several coating types. EIS enables detection of small changes in coating behavior in a short time period and allows quantitative determination of coating properties without affecting the coating. Organic coatings initially have a high electrical resistance through the coating. As coatings age, UV light causes microcracking and erosion of the coating. This porosity in the coating then becomes saturated with water, chloride, oxygen and other initiators, which ultimately exposes the metal surface to corrosion.
EIS testing of an FEVE liquid coating was compared to both a polysiloxane and a polyurethane using the conditions shown in Table 2.
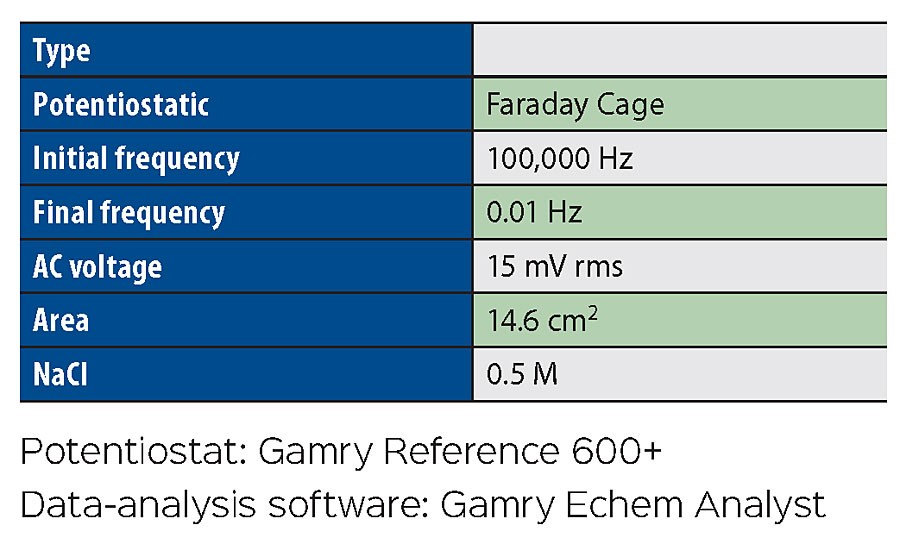
As shown in previous testing, the initial impedance is generally similar between the three coating types. Upon aging, 350 hrs of QUV-A followed by a salt soak, the FEVE coating maintains 80% of its impedance, while the polysiloxane maintains only 35%. The notably lower initial impedance of the polyurethane is maintained better than the polysiloxane at 67%, but still not at the level of the FEVE coating. Overall the absolute impedance of the FEVE coating after aging is higher than both the polysiloxane and the polyurethane coatings (Table 3 and Figure 15).

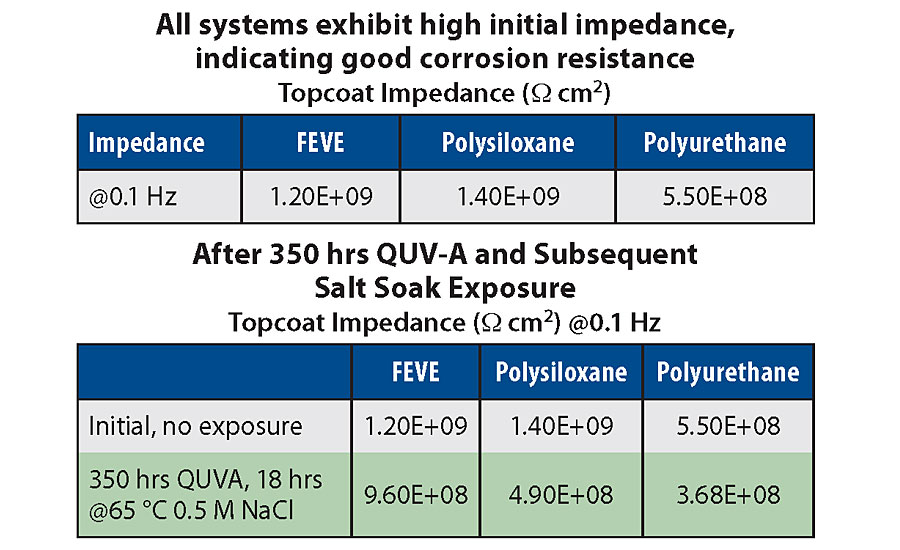
FEVE Powder Resins for Corrosion
Much of the corrosion data has been focused on the more traditional liquid FEVE coatings. New studies of FEVE powder coatings and how they specifically perform in corrosion testing are ongoing. Results to date show that FEVE powder coatings display good salt fog corrosion resistance without primer. It should be noted that in most seacoast environments, primers are preferred due to concerns with damage and filiform corrosion.
Figure 16 shows one-coat, FEVE powder-coated aluminum panels after 4,000 hrs of salt fog. In both of the acid-etched and alkali-etched panels, no significant corrosion is observed.
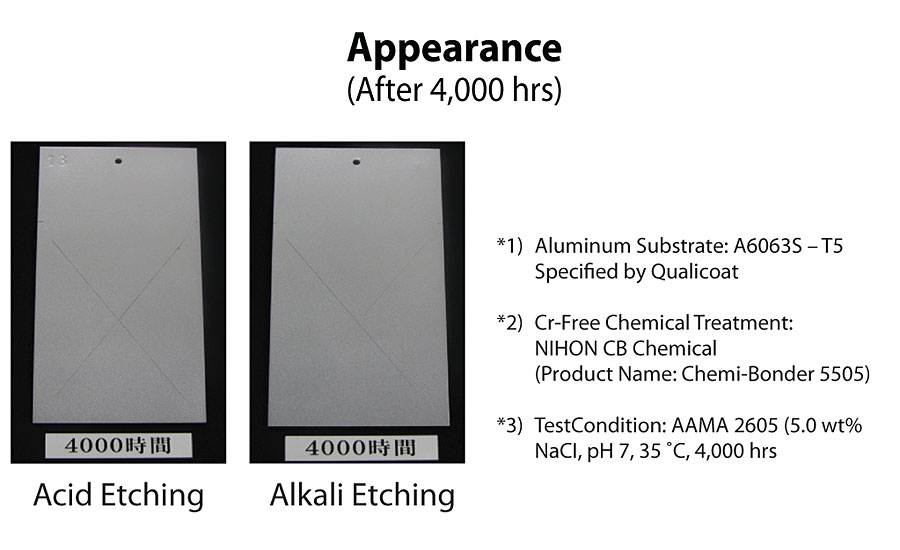
Initial EIS testing of an FEVE powder coating shows 75% retention of impedance after 2,400 hrs of QUV-A exposure, followed by a 36-hour salt soak (Figure 17).
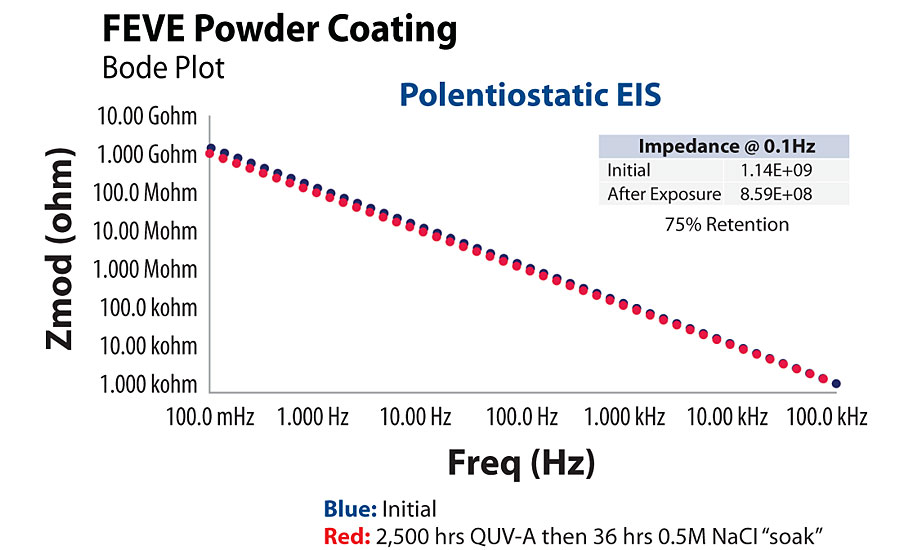
Current and Future Testing
Based on the information gained through this research, the next steps are to continue with testing various pigmented FEVE powder formulations according to ASTM D5894 Cyclic Prohesion. Future testing will study these formulations over primers in both prohesion and EIS spectroscopy.
Applications of FEVE Powder-Based Coatings
Architectural applications of FEVE powder-based coatings include aluminum windows (AAMA 2605), curtain walls (AAMA 2605), light poles, railings, flag poles and stadium seating. The slide show in Figure 18 shows some current examples.
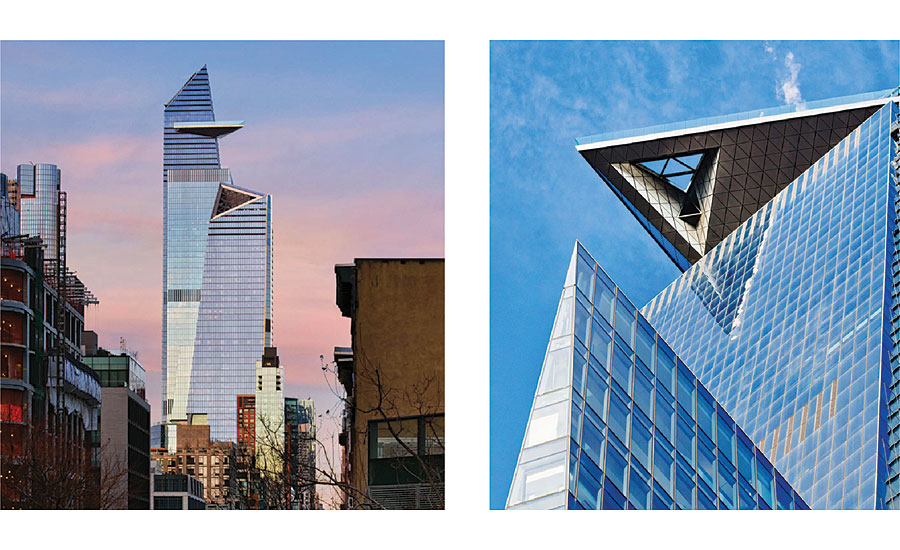
Conclusion
Historical research and real-world applications demonstrate that FEVE resin-based coatings provide superior resistance to UV degradation, weathering and corrosion. For years, however, testing primarily focused on FEVE solvent-based coatings. With the rapid shift toward more environmentally friendly coatings, testing of FEVE powder-based coatings is needed. As the research in this article demonstrates, FEVE powder-based topcoats can provide weatherability, corrosion resistance and environmental benefits when used in exterior architectural coatings applications.
References
1 Munekata, S.; Miyazaki, N.; Kaya, S.; Takayanagi, T. Characteristic Properties of LUMIFLON ® as a Coating Material. Reports Res. Lab. Asahi Glass Co. Ltd. 1984, 34, 207.
The author thanks her AGC colleagues Donald Lawson (Don.Lawson@us.agc.com) and Connie Przeslawski (Connie.Przeslawski@us.agc.com) for their contributions to this article.
Report Abusive Comment