Amine-cured epoxy has a long history of success as a chemically resistant coating in a wide variety of applications, including industrial and marine markets. These formulations tend to be epoxy with filler and other additives on the A side, and amine curative on the B side, that when mixed together give a sprayable coating with a very workable pot life and good adhesion to a wide variety of substrates. The ultimate chemical resistance of the cured epoxy coating will depend on several factors, including the chemical structure of both the epoxy and the amine curative, the crosslink density, the stoichiometry of the epoxy to amine curative, the types of fillers and additives used, and the cure temperature and time. Figure 1 shows a representation of the crosslink density of a traditional epoxy compared to a polymer-modified epoxy that is extremely chemical resistant, such as ChemLine ® 784/32 from Advanced Polymer Coatings. By utilizing polymer technology with very high functionality, the coating can achieve up to 784 crosslinks compared to four crosslinks for a traditional bifunctional epoxy.
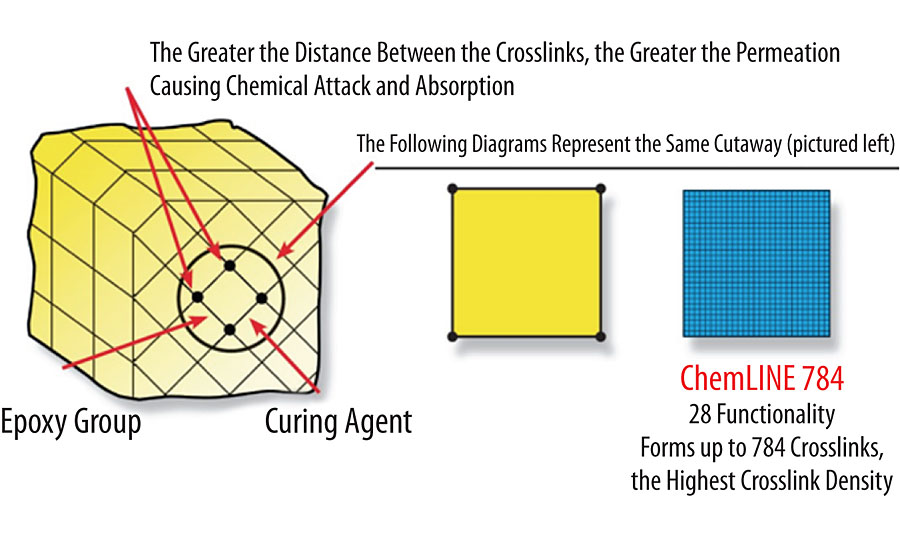
With a low crosslink density, the coating is susceptible to penetration from aggressive chemicals, which can eventually reach the substrate, causing corrosion and ultimately failure of the substrate. However, with a very high crosslink density, the coating forms a virtually impermeable barrier between the chemical and the substrate. In addition, chemicals do not penetrate the coating, which can occur in traditional epoxies, leading to blistering, cracking and general coating degradation. Figure 2 shows the penetration of chemicals in a thermoset of low crosslink density versus a thermoset of high crosslink density. In the low-crosslink-density coating, the chemicals are shown to penetrate through the coating to the substrate, causing substrate corrosion. In addition, because the solvent has penetrated the coating, both the epoxy and amine curing agent bonds are shown broken by chemical attack. In contrast, for the coating with high crosslink density, the chemicals are unable to penetrate the coating. This not only protects the substrate from corrosion, but also protects the coating itself from damage.
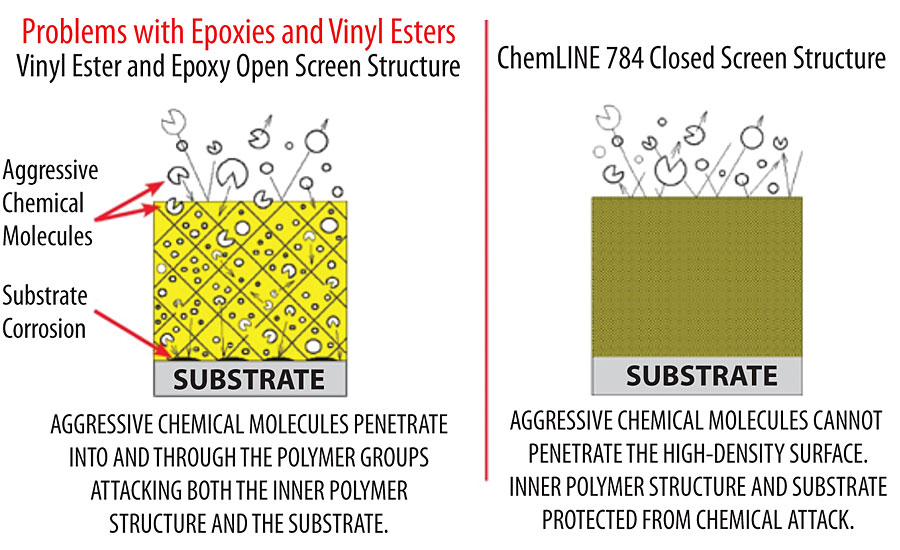
SEM images were also taken of a polymer-modified epoxy coating with very high crosslink density compared to a traditional epoxy novolac coating. The SEMs in Figure 3 clearly show that a higher crosslink density produces a coating that will form a virtually impermeable barrier for substrate protection.
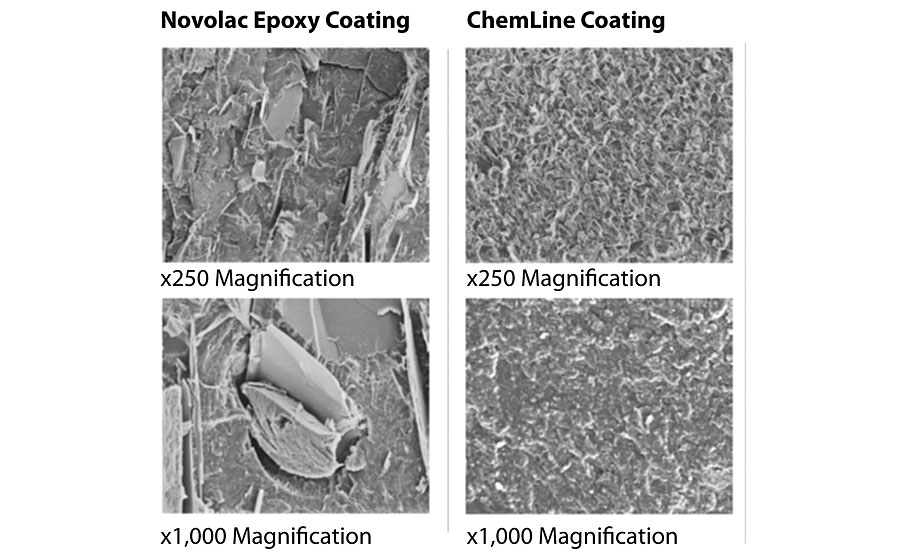
With the emerging needs of both industrial and marine applications, coatings have a wide range of technical requirements in addition to chemical resistance. This includes protection of the cargo from contamination due to the coating, easier inspection of the coating during and after application, dissipation of static electricity, improved abrasion resistance, and the need for easy repair of the coating in the field. The technical and market needs for each of these requirements will be reviewed along with recent developments to meet these demands.
Coatings for Sulfuric Acid
Sulfuric acid is an extremely important industrial chemical, with uses including the manufacture of phosphate fertilizers, explosives, plastics and other acids, along with being used as a pickling medium for metals, purification of petroleum, and in storage batteries. 1 The concentration of sulfuric acid carried and used for these applications can vary from below 50% up to 98% for a very high-purity grade of sulfuric acid. Because sulfuric acid is a very strong acid and oxidizer, specialty materials must be utilized in its transportation, storage and use. Rubber coatings are commonly used and specified for tank cars for sulfuric acid concentrations less than 50%. 2,3 Other commonly used materials to transport and store sulfuric acid include electrochemically maintained materials 4 and plastics, such as PTFE. 5 All of these materials can be very expensive and difficult to install and repair if needed. Two-component epoxy coatings show excellent resistance to sulfuric acid of most concentrations and transportation and storage temperatures, and have been used successfully for years, but unfortunately can darken upon exposure to sulfuric acid. Not only will the coating darken, but the sulfuric acid itself can develop some color from the coating, raising its APHA color slightly, which can be an issue for very high-purity grades of sulfuric acid. Typically, high-purity grades of sulfuric acid will require an APHA color less than 40.
Recent work to improve the discoloration of 2K epoxies upon exposure to sulfuric acid has shown that altering the amine curative chemistry can lessen the discoloration of both the acid and the coating while still maintaining the excellent chemical resistance to sulfuric acid.
Drawdowns of a chemically resistant 2K red epoxy basecoat were done with both a standard amine catalyst package and an improved catalyst package for less discoloration to concentrated sulfuric acid. The drawdowns were B-staged in ambient conditions for 24 hrs, after which time they were detached from the substrate and cut into 1.31 cm x 1.31 cm chips. These chips were cured in different conditions, and then placed in 8 oz. of 98% sulfuric acid for 8 weeks at 40 °C. The size of the chip compared to the volume of acid represents a 17 gal/ft 2 volume to surface area ratio, which is a typical volume to surface area ratio of a tank truck. The APHA color of the sulfuric acid was monitored over the 8 weeks, along with the color and weight gain of the chip itself. Table 1 shows the cure conditions along with the results for the standard and improved amine catalyst for sulfuric acid tested. The improved amine catalyst shows much less discoloration of the sulfuric acid, and the coating itself is much less discolored.
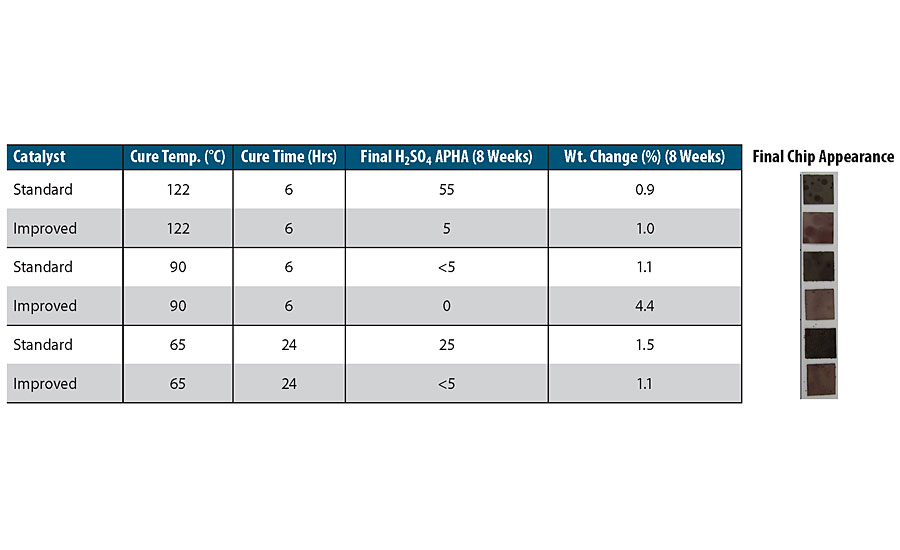
The data also shows the excellent chemical resistance of polymer-modified 2K epoxies to sulfuric acid by the very low weight change in both the standard and improved catalyst after 8 weeks in 98% sulfuric acid at 40 °C. Therefore, with the improved amine catalyst package, two-component specialty epoxy coatings can be a less-expensive and easy-to-install/repair coating for sulfuric acid, providing protection not only to the substrate but also ensuring purity of the sulfuric acid.
Coating Inspection Facilitation
Ensuring the integrity of the coating is critical for the protection of the substrate. Failure of the coating cannot only cause damage to the vessel, costing the owner both time and money, but it can also pose a danger to workers and the surrounding environment. Proper inspection of the coating itself can be time consuming and expensive, and based on the geometry of the vessel being inspected, some areas can be very hard to inspect. The coating must be inspected immediately after application and curing for holidays (holes, voids or discontinuities in the film) that can expose the substrate to corrosion. For non-conductive coatings, holiday inspection is typically done by spark testing as per NACE SP0188. 6 This testing can only be done once the coating is cured, and then any holidays detected must be repaired, which is a very time-consuming process. Likewise, coatings must periodically be inspected for damage to make sure that there are no cracks, holes or chips. The entire vessel must be inspected after draining and cleaning, which can be difficult again because of the complex geometries along with the hazards associated with sending workers into the vessels for inspection.
Coatings should therefore facilitate the inspection process, reducing chances of coating failure and overall simplifying the inspection process. The use of a fluorescent pigment in the basecoat of the coating greatly facilitates the inspection of the coating through the detection of holidays using UV light. Figure 4 shows a steel panel with a basecoat containing a fluorescent pigment, which is then coated with a standard gray topcoat. Defects were purposely introduced in the topcoat to demonstrate how the fluorescent basecoat highlights the defects and facilitates coating inspection. In Fig. 4, the picture on the left is the coating under ambient lighting and the picture on the right is the coating under UV lighting.
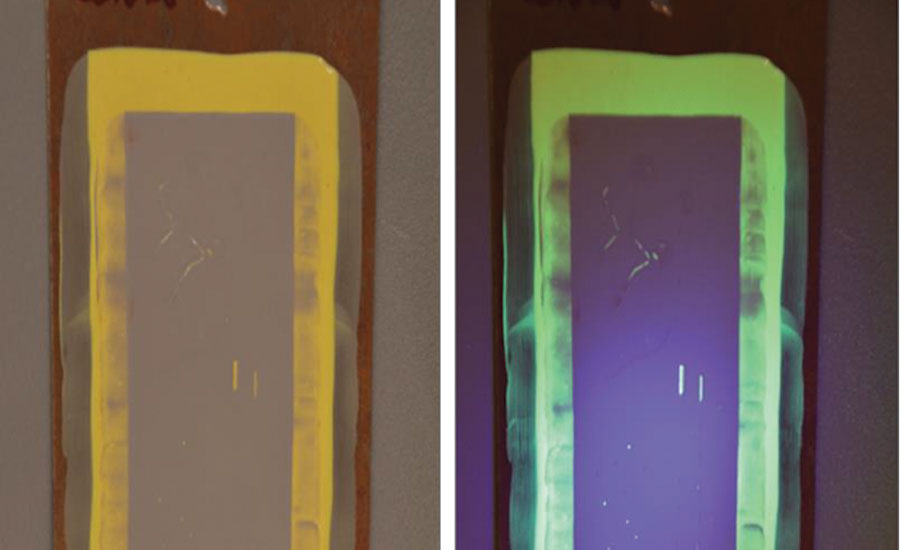
In addition to highlighting defects in a cured topcoat through damage or abrasion, a fluorescent basecoat can be used to highlight insufficient coverage of the topcoat during application. Figure 5 shows a gray 2K epoxy topcoat with a fluorescent basecoat, with the picture on the left being ambient lighting and the picture on the right with a UV light.
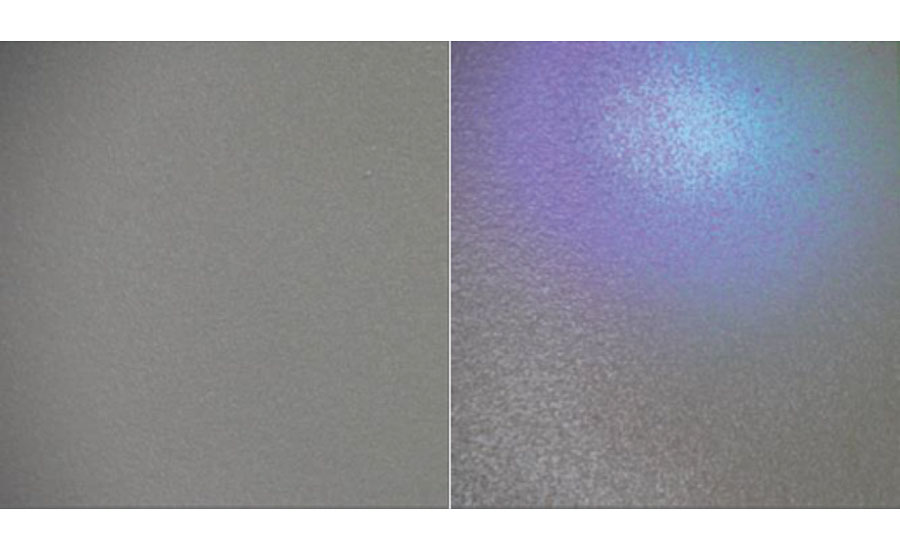
Under ambient lighting, it is very difficult to detect that the topcoat does not have enough coverage, and under normal inspection conditions, the coating would need to be cured first before it could be spark tested and shown that there is not complete coverage, costing the owner of the vessel time and money. With a fluorescent basecoat however, the coating can be inspected immediately after applying the topcoat and clearly shows that there is not enough coverage. This allows the coating to be corrected before curing, saving a significant amount of time and money.
In addition to facilitating coating inspection, the fluorescent basecoat should maintain the excellent chemical resistance of the coating. Panels were coated with a 2K epoxy fluorescent basecoat and a chemically resistant 2K epoxy topcoat. The panels were immersed in a wide variety of aggressive chemicals used in the marine and industrial markets, and were stored at either ambient or elevated temperatures and monitored for weight changes, along with visual signs of coating degradation. The panels with the fluorescent basecoat were compared to samples with a standard, chemically resistant basecoat, and the results are given in Table 2. After 49 days of immersion testing there is essentially no difference in results comparing a standard chemically resistant basecoat to a fluorescent basecoat. With the correct selection of fluorescent pigment then, it was shown that a coating that greatly facilitates inspection could be produced without sacrificing chemical resistance.
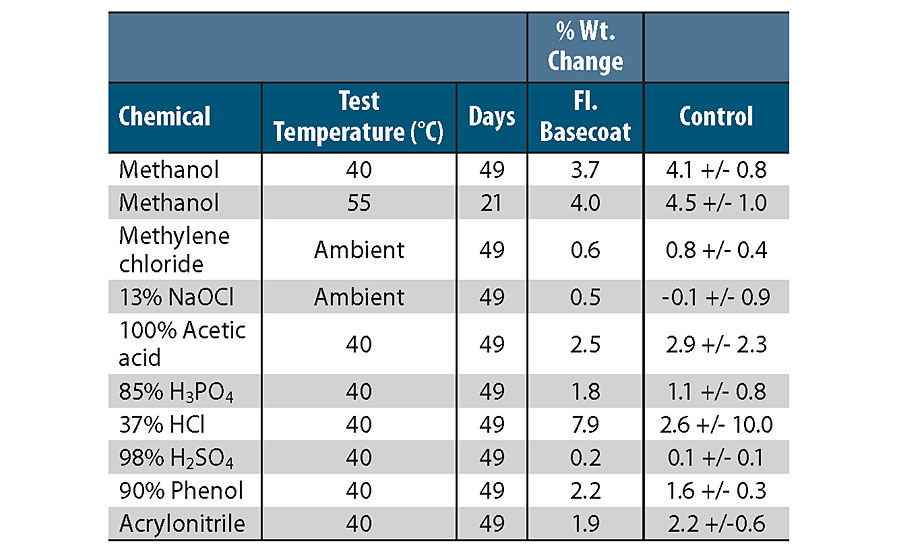
Antistatic Coatings
Static electricity presents a very significant hazard for not only safety of people and property but also of products that are sensitive to static electricity, such as electronics components. 7 The importance of dissipating static electricity to the safety of people and property is show in a case study from Barton Solvents in 2007. 8 In 2007, naphtha was unloaded from a tank truck into a bulk storage tank, as shown in Figure 6.
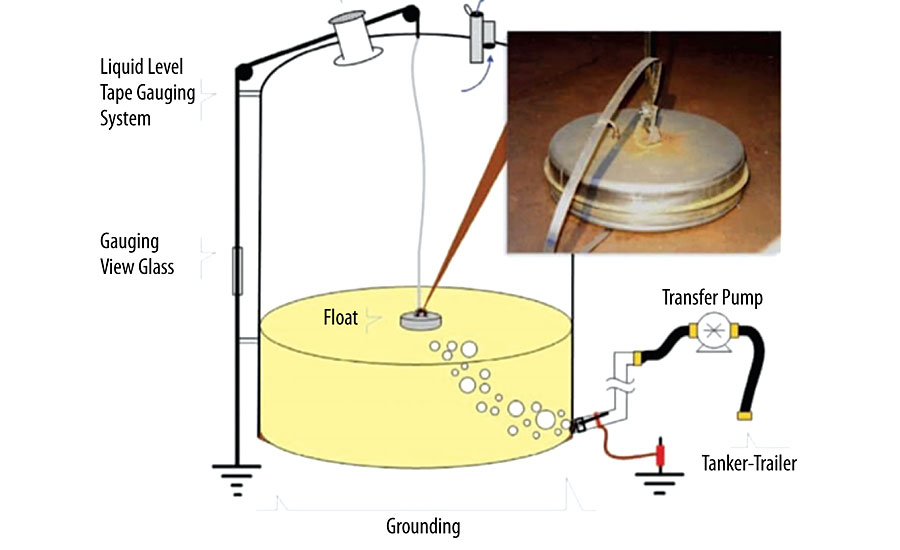
Naphtha, a non-conductive liquid, was unloaded from a tanker containing three separate compartments. During the unloading, air was introduced as the transfer hose was switched between compartments, creating a flammable mixture in the headspace of the bulk storage tank. The introduction of air also caused turbulence inside the tank, which caused the metal float to lose its grounding and to accumulate a static charge. At some point during the naphtha unloading, the accumulated static electricity was enough to produce a spark and ignite the flammable mixture above the liquid. The explosion was of enough force to throw the storage tank beyond the tank farm, causing two other vessels to explode, hurling metal fragments into nearby residences and businesses. Within minutes the entire tank farm was destroyed. This is a very extreme example, but it clearly shows the damage that can be caused by static electricity.
The ability for a coating to dissipate static electricity is usually measured in the surface resistivity per area, using a method such as ASTM D257. For typical 2K filled epoxy coatings, the surface resistivity is > 10 10 ohms/square, making them insulating materials. Figure 7 gives the surface and volume resistivity for conductive, static-dissipating and insulating materials.
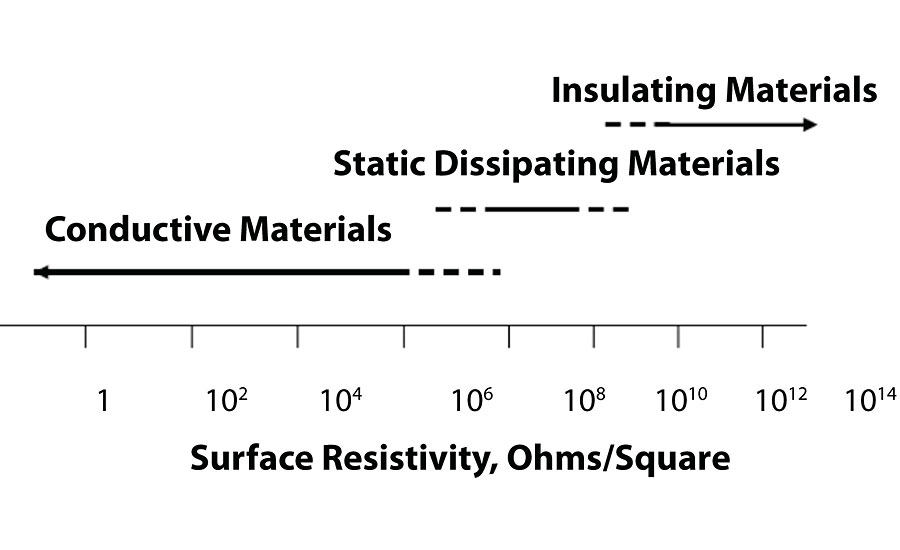
To reduce the surface resistivity of 2K epoxy coatings, conductive additives can be used. The additives must be used at low levels so that they do not affect the chemical resistance. One such additive that has found use in static dissipative coatings are carbon nanotubes. They can be added at levels as low as 0.05% to reduce the surface resistivity to 10 9 ohms/square.
A chemically resistant 2K epoxy coating with 0.01% carbon nanotubes and surface resistivity of 10 9 ohms/square was compared to a chemically resistant 2K epoxy coating without carbon nanotubes for resistance to aggressive chemical cargoes. Steel panels were coated with a 6-7 mil-thick basecoat and topcoat, with carbon nanotubes in both the basecoat and topcoat for the static dissipative coating. The panels were then immersed at either ambient conditions or elevated temperatures, and monitored for weight gain or loss. The data are presented in Table 3 and show that the addition of low levels of carbon nanotubes does not affect the chemical resistance of the coating. By adding the carbon nanotubes then, a static dissipative coating with outstanding chemical resistance is produced.

Improved Abrasion Resistance
Coatings used to store chemicals and other materials can sustain damage from abrasion, such as the loading and unloading of materials in the form of slurries or from cleaning procedures. Applications that could benefit from an improvement in abrasion resistance could include hopper cars, slurry pipes, legs of oil platforms, pumps, coal chutes, bag houses and ion exchange vessels. Epoxy coatings can provide excellent chemical resistance through a high degree of crosslinking and the correct chemical structure, but this can lead to a coating that can be brittle and subject to damage from abrasion. Often, formulators will solve this issue through the addition of low levels of abrasion-resistant additives or through the addition of abrasion-resistant fillers. By maintaining the same chemical structure and crosslink density, the chemical resistance of the coating is retained, while the abrasion resistance is improved with the additive or filler.
A typical abrasion-resistant filler is aluminum oxide. When used in place of traditional fillers such as silica, the abrasion resistance of the coating is significantly improved. To further improve the abrasion resistance, aluminum oxide can be used with a polymer-modified 2K epoxy coating, which shows excellent abrasion resistance compared to other coating technologies. Figure 8 shows the Taber abrasion of traditional coatings used for chemical resistance compared to a polymer-modified 2K epoxy coating with high crosslink density and containing aluminum. Compared to traditional epoxies without aluminum oxide, a 2K, high crosslink density polymer-modified epoxy coating with aluminum oxide shows almost an order of magnitude improvement in Taber abrasion. The chemical resistance of an epoxy coating containing aluminum oxide in most chemicals tested is similar to the control coating with traditional fillers.
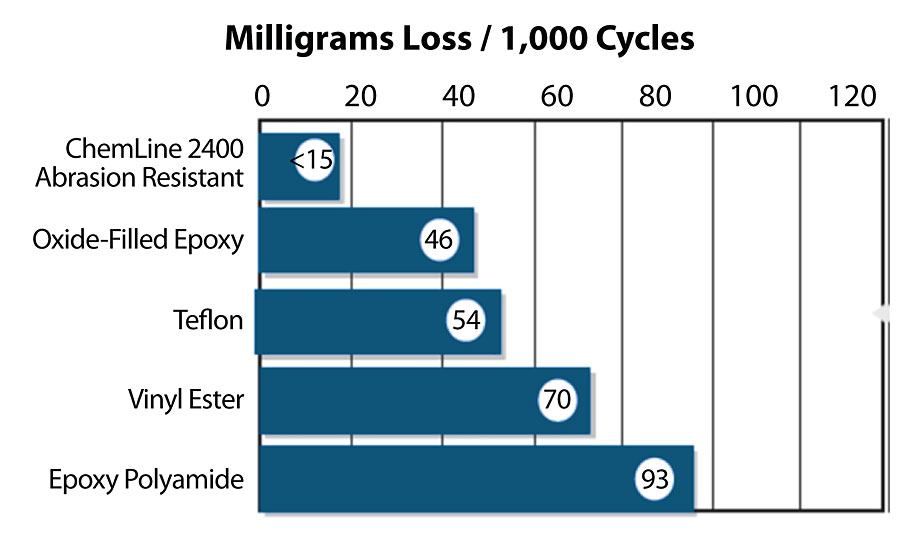
The incorporation of abrasion-resistant additives will still further improve a coating of high crosslink density containing aluminum oxide. Figure 9 shows the incorporation of either SiC whiskers or carbon nanotubes to a chemically resistant 2K polymer-modified epoxy coating containing aluminum oxide.
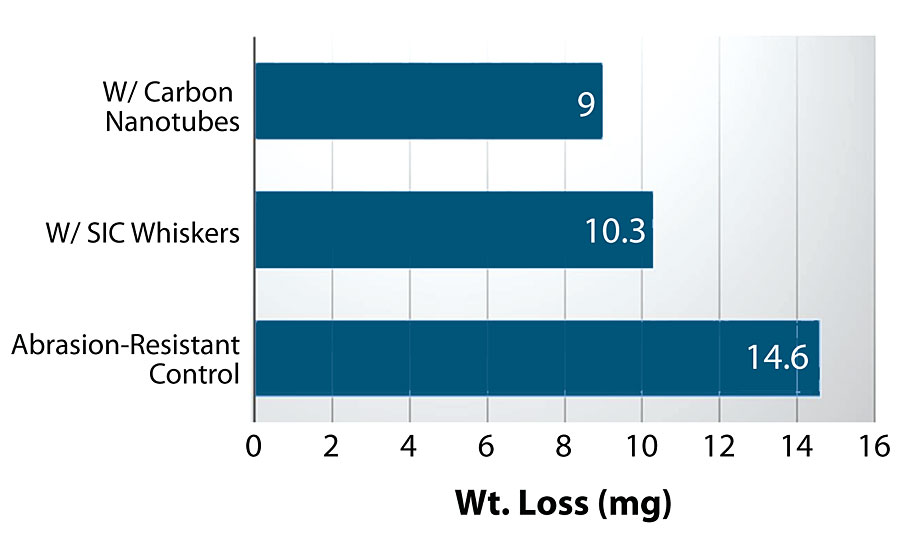
Field-Repairable Coatings
Recent changes to regulations from the American Association of Railroads (AAR) require that for a tank car facility to be certified, it must be able to demonstrate the procedure to repair coatings on a periodic basis. 9 High-bake phenolic coatings are widely used in the rail industry due to their excellent chemical resistance to a wide variety of products. Repair of high-bake phenolic coatings require that the tank car first be returned to the facility, where the coating repair would then be demonstrated. The coating repair of high-bake phenolics requires that the entire tank car be taken up to high temperatures (350 °F to 400 °F), which can damage the exterior paint and stencils. This adds an extreme amount of cost for the tank car facility, along with a great deal of time for the tank cars to be out of service. Having a coating that can have its repair demonstrated in the field is therefore very important to tank car facilities. Two-part epoxy coatings can meet these needs. They must first have excellent chemical resistance to the same products as the original coating. Secondly, the repair coating must be easy to apply and cure, and specifically they must be able to be applied to the tank car in the field so that it does not have to be sent back to the tank car facility for repair demonstration.
A field-repairable procedure using a two-part amine-cured epoxy with excellent chemical resistance follows. The repair procedure starts with a damaged coating, an example of which is shown in Figure 10.
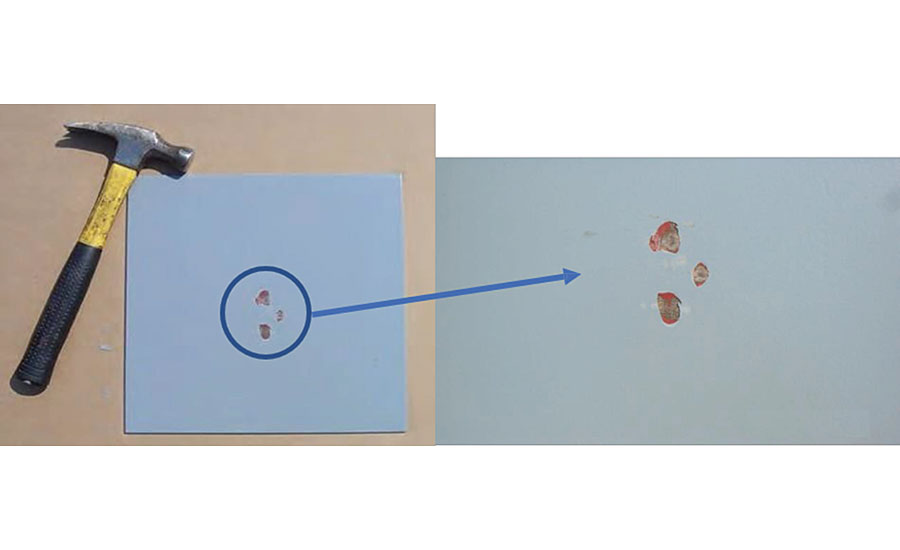
The initial preparation of the surface includes a detergent cleaning and water rinsing, followed by drying of the surface. If the damaged areas are small and independent (separate) from each other, the small damaged areas may be hand sanded with a medium-grit aluminum oxide sandpaper. Any rust spots must be removed to a near white metal, with approximately one inch around its periphery. The edges around the damaged area should be feathered so that there are no sharp edges of existing coating observable. After the sanding is complete, the prepared area should be vacuumed and then washed with solvent, preferably acetone or MEK. Figure 11 shows an example of a damaged area that has been prepared for repair.
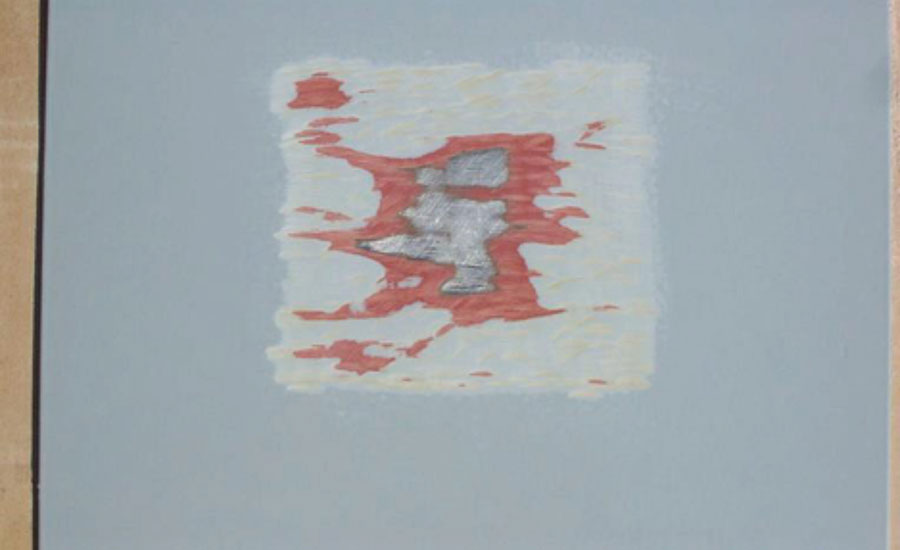
Part A and Part B of the epoxy repair basecoat are then mixed together, with a pot life of approximately 30 min at ambient temperature. A 6-7 mil-thick wet film is applied with a brush, and allowed to B-stage, which can take up to 24 hrs. The topcoat is then mixed and applied in the same manner. After the topcoat has B-staged, it can then be inspected for holidays as per NACE SP0188. For small areas, the coating is usually cured with a heat gun, raising the temperature of the substrate to 122 °C for a minimum of 2 hrs. For larger areas, electric or gas heaters, or forced air heat cure equipment is used to raise the substrate temperature to 122 °C for a minimum of 6 hrs. Figure 12 shows an example of a repaired coating.
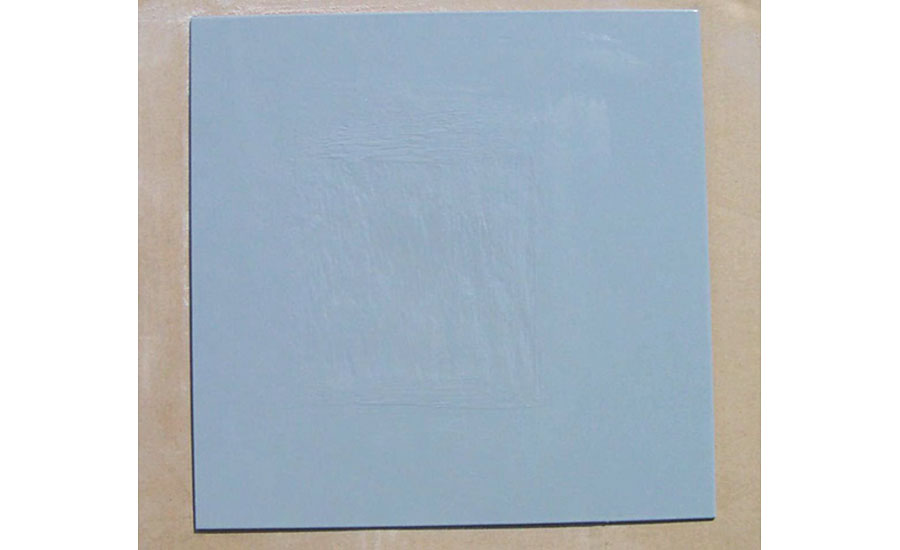
Two-component epoxy coatings therefore have a significant advantage over high-bake phenolics in the future of chemically resistant rail car coatings due to the ease of repair demonstration.
Unmet and Future Industry Needs
Vessel owners continue to look for ways to reduce operating expenses, and therefore chemical-resistant coatings must deliver opportunities to achieve these goals. One such opportunity is for coatings that release cargo from the walls faster than current technologies. This would allow for quicker unloading of vessels, along with easier clean, allowing for less time between unloading and loading. Ability to carry different chemicals would also save vessel owners time and money. The same asset could be used to transport or store a wide variety of chemicals, eliminating the need to either re-coat current vessels or to possess different storage options for each chemical. The coating should therefore be resistant to the widest variety of chemicals possible and should not absorb chemicals that can later be released and contaminate the next chemical loaded into the vessel. Coating of the vessel can be a time-consuming task, which can incur labor costs. The ability to apply a 2K epoxy coating in colder temperatures would widen the application window. Currently, 2K epoxies do not B-stage, cure properly or blush at lower temperatures, and altering the chemistry can save time by allowing faster B-staging in a wider range of conditions. To obtain maximum chemical resistance, epoxy coatings are heat cured, which is a time and labor-intensive process. Again, altering the curing would allow asset owners to save time through the elimination of this heat-curing step.
Conclusion
Developments in chemically resistant, 2K polymer-modified epoxy coatings have met several market needs, including carry of sulfuric acid, coating inspection facilitation, anti-static coatings, improved abrasion resistance and field-repairable coatings. These coating systems continue to be leaders in chemical-resistant applications in both marine and industrial applications, and will meet future market needs through continued innovation.
Acknowledgements
The author would like to thank the following individuals from Advanced Polymer Coatings for their contributions to this work: Charlie Simpson, Cheng Xiong, Jim Dechant and Kevin Balaban.
References
1 BMT Cargo Handbook, Retrieved from URL http://www.cargohandbook.com/index.php/Sulphuric_acid.
2 Blair Rubber Company, Retrieved from URL https://blairubber.com/rubber-linings-chemical- corrosion-protection/.
3
Sulfuric Acid on the Web™, Retrieved from URL http://www.sulphuric- acid.com/techmanual/Storage/
transportation.htm.
4 Corrosion Service, Retrieved from URL https://www.corrosionservice.com/core-services/anodic- protection/.
5 Chemical and Industrial Plastics, Retrieved from URL http://www.ptfeplastics.com/project/ptfe-tank- linings-and-equipment/.
6 NACE Standard RP0188-99, NACE Standard Recommended Practice “Discontinuity (Holiday) Testing of New Protective Coatings on Conductive Substrates”.
7 American Coatings Association, Coatings Care. “Generation and Control of Static Electricity in Coatings Operation”, James R. Reppermund January 2010.
8 Priebe, J. Are Conductive Linings Necessary for Tank Farms and Process Vessels? March 12th, 2018, Retrieved from URL https://www.corrosionpedia.com/are-conductive-linings-necessary-for-tank-farms- and-process-vessels/2/6685.
9 AAR Manual of Standards and Recommended Practices Specifications for Tank Cars; Appendix B Certification of Tank Car Facilities.
This article was presented at a meeting of the Thermoset Resin Formulators Association (TRFA) in Charleston, South Carolina, April 7-10, 2019. TRFA’s Annual Meeting is held in the spring each year. Visit www.trfa.org for details and to register.
Report Abusive Comment