1,5-Pentanediol Diacrylate: A Bio-Based Alternative for UV-Curable Coatings and Inks

UV-curable monomers and oligomers play a key role in a wide range of coatings due to their fast cure and the resulting excellent properties. With few exceptions, raw materials currently used in the manufacture of UV-curable monomers and oligomers are petroleum based. While this has been a reliable source of starting materials, the low-cost advantage for some of the petroleum-based materials for large-volume usage is a function of the current oil prices. As expected, both the availability and price can significantly vary over time. One of the largest UV-curable monomers by volume is 1,6-Hexanediol diacrylate (HDDA). Based on the acrylation of 1,6-Hexanediol (1,6-HDO), this monomer can be found in a wide range of coating formulations due to its moderate cost and overall good properties. As expected, the 1,6-HDO used by acrylate manufacturers is sourced from petroleum feedstocks.
There are many advantages to be able to source the key feedstock for these important resins from renewable sources, such as a minimum impact on the environment, availability and potentially competitive costs. Using technology that has been commercialized since 1942, furfural can be easily made from available biomass in large quantities and at low cost. Typical biomass feedstocks include corn stover, bagasse and wood, but primarily corncobs serve as the biomass today. However, the use of furfural as a starting material for a UV-curable acrylate monomer has been challenging so far as there has been no economically viable route to acrylates from furfural.
Based on work initially started at the University of Wisconsin-Madison and continued at Pyran, a multi-step continuous process has been developed to convert renewably sourced furfural to 1,5-Pentanediol (1,5-PDO). 1,5-PDO is a low-cost renewable replacement for 1,6-HDO, a diol intermediate currently used to produce coatings, adhesives and plastics (Figure 1).
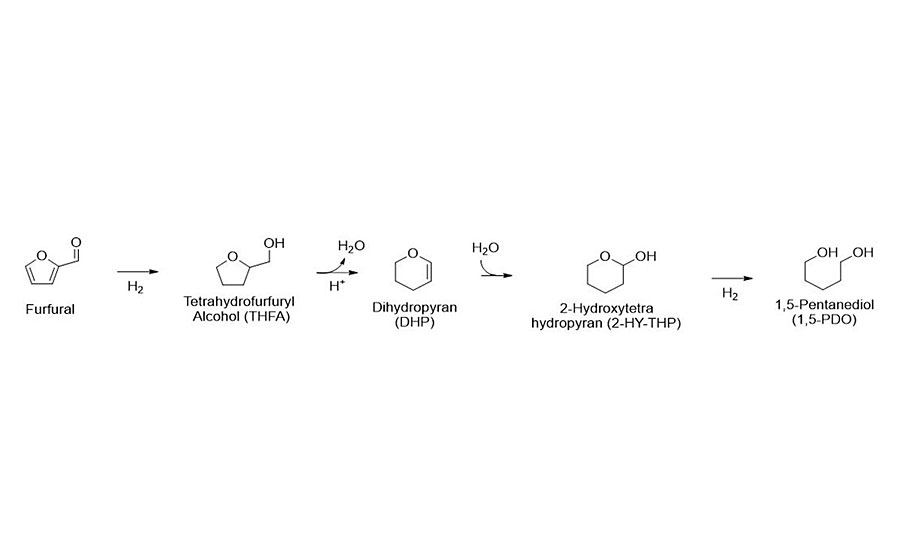
1,5-PDO is currently produced from dicarboxylic acid, a byproduct in caprolactam production. By starting with waste biomass such as corncobs, there is now a highly efficient, continuous, multi-step process to make this diol. The 1,5-PDO can be used to synthesize 1,5-Pentanediol diacrylate (PDDA), a difunctional linear acrylate monomer that is cost competitive with petroleum-based HDDA. While in general the monomer properties of PDDA are expected to be similar to those of HDDA, there may be other benefits to the use of PDDA in UV-curable formulations. Using a five-carbon monomer like PDDA may provide performance advantages compared to six-carbon HDDA, such as lower viscosity and reduced toxicity. Equally important in some cases, a biomass-based monomer will also allow a formulator to diversify their supply chain from petroleum by using a renewable feedstock. These formulators would also be able to market their products as a “green” alternative to end users.
PDDA vs HDDA
Typically, low-viscosity monomers act as a reactive solvent or diluent in a formulation. Their principal function is to dissolve solids such as the photoinitiator and tune the formulation viscosity for the selected applications. One of the largest monomers by volume used in UV-curable coatings is 1,6-Hexanediol diacrylate. More commonly known as HDDA, this workhorse aliphatic diacrylate has traditionally been the monomer of choice for coatings formulations due to its relatively low cost, low viscosity and excellent ability to serve as a diluent. HDDA’s fast cure speed can lead to increased productivity. In addition, HDDA can contribute to enhanced physical properties of the cured coating. Some of the attributes seen in coatings containing HDDA are increased scratch resistance, low water sensitivity, and improved elasticity, weathering and adhesion when compared to other commonly used monomers.
HDDA is manufactured on a commercial scale from 1,6-Hexanediol. As expected, 1,5-Pentanediol diacrylate (PDDA) can be produced using a similar process by replacing 1,6-Hexanediol with 1,5-Pentanediol. The manufacturing process itself is straightforward, resulting in PDDA in high yield. If the starting diols were at an equal cost, then the resulting diacrylate would roughly be similar with the exception of the resulting physical properties due to the smaller PDDA molecule.
Sharing a similar linear structure to HDDA, PDDA contains one less carbon in the backbone (Table 1). This results in a lower boiling point than HDDA (90-95 °C vs. 158-165 °C at 5 mmHg) along with other expected changes in physical properties of the diacrylate. However, what is more important is how PDDA performs compared to HDDA when used in coatings formulations in a range of applications.
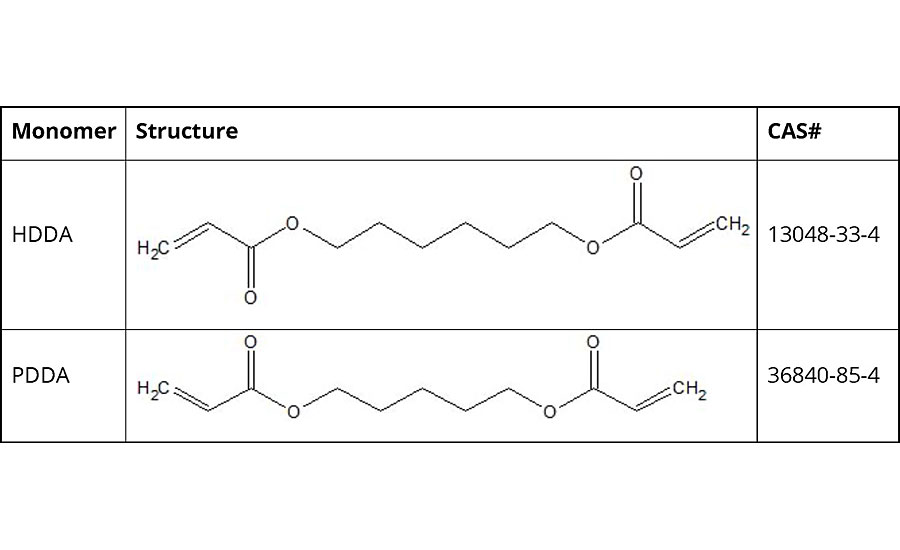
Application Testing
As mentioned previously, HDDA has been the industrial workhorse for applications that require a good monomer diluent at a competitive cost. For PDDA to be a viable candidate as an HDDA replacement, it should also perform at least at the same level of HDDA in technical performance. HDDA has traditionally been used in a wide range of coating formulations, so formulations for an overprint varnish (OPV), wood coating, UV flooring and an exterior automotive plastic protective coating were selected. The first two formulations are simplified systems, while the UV flooring and exterior automotive plastic protective coatings are actual commercial formulation starting points. This should give insight on whether PDDA would be an acceptable substitute for commercial UV-curable coatings where HDDA plays an important role as a monomer.
The formulations evaluated for the two simplified coatings applications are listed in Table 2. The OPV illustrates a limited number of components seen in low-cost commercial systems. Built around a Bisphenol A diacrylate as the oligomer, HDDA is a major component in the mix. The wood coating is also simple, with the HDDA or PDDA used in equal amounts to the urethane diacrylate oligomer. In both cases, CPK was used as the photoinitiator. These formulations were kept uncomplicated and may not perform up to current performance standards. However, the authors wanted to highlight any differences in performance when substituting PDDA for HDDA.
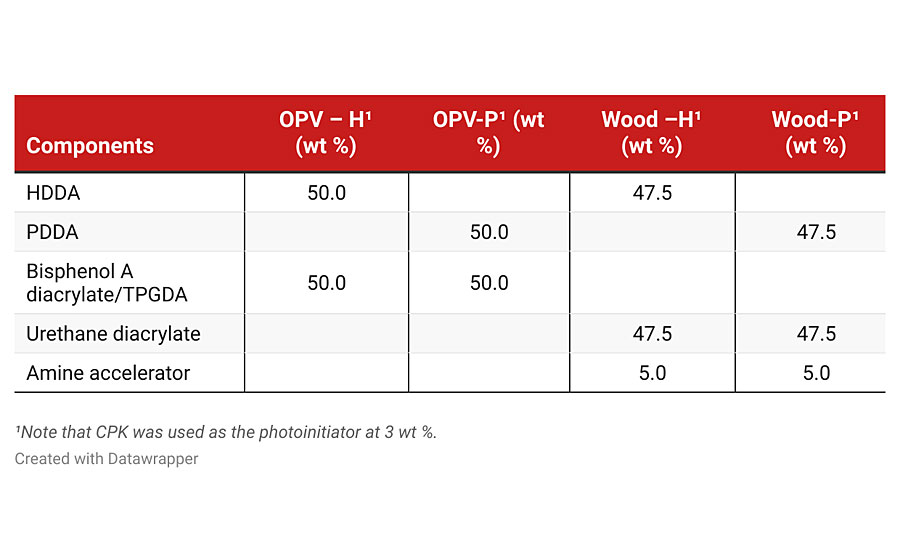
Using the formulations shown in Table 2, the coatings were tested for viscosity then coated and cured using a metal halide UV light at 30 mW/cm² for 1 min. The results are shown in Table 3. The viscosity, Shore Hardness and cure speed were virtually identical when PDDA was used as a replacement for HDDA. A slight difference was seen in the overall acrylate conversion. This test uses FTIR to measure the loss of the acrylate functionality in the monomer as the curing of the coating proceeds. While this small difference can be detected by FTIR, it will likely have little or no effect on the performance of the final coating. A detailed look at the conversion data as the OPV coating is cured is seen in Figure 2.
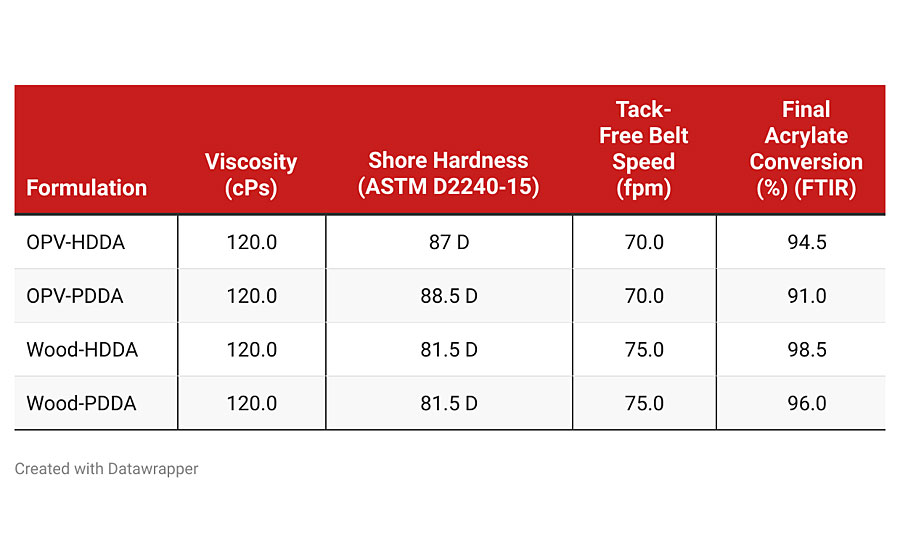

We were also interested in understanding how the mechanical properties of the coatings compared when PDDA was substituted for HDDA. These results are shown in Table 4. Based on our work looking at the cure speed, viscosity and hardness, we expected the mechanical properties to also match well. Surprisingly, the mechanical properties showed an improvement in several cases on substituting PDDA for HDDA. In particular, the tensile and flexural modulus and strength improved when PDDA served as the monomer diluent. The only exception that was seen in these series of tests was a decrease in the tensile modulus and strength for the PDDA-based OPV formulation. It appears that the C5 chain allows desirable configuration(s) to form, which has a positive effect on the mechanical properties. Additional work would be required to understand the mechanism responsible for the improved performance.
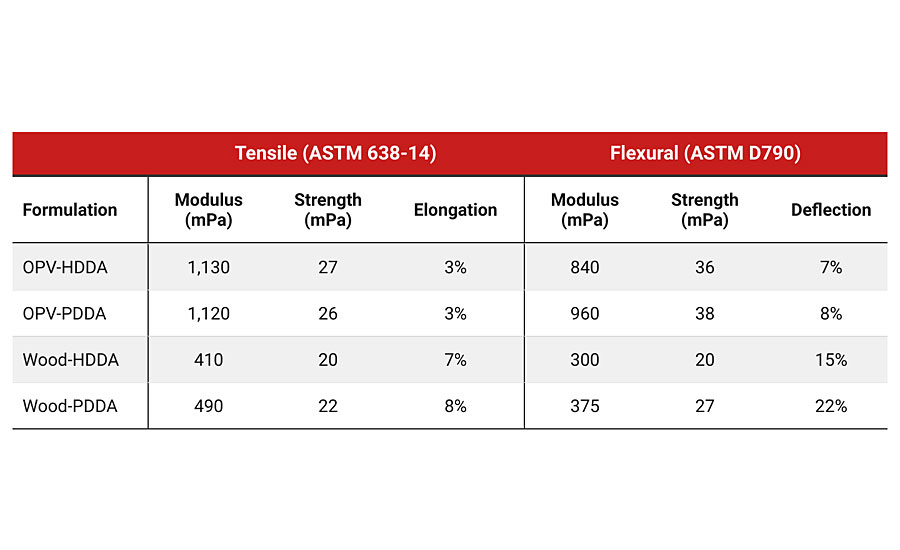
The second part of the study involved starting point formulations that have been used commercially. The formulations for the UV flooring and the exterior automotive plastic protective coating (EAPPC) are illustrated in Table 5.
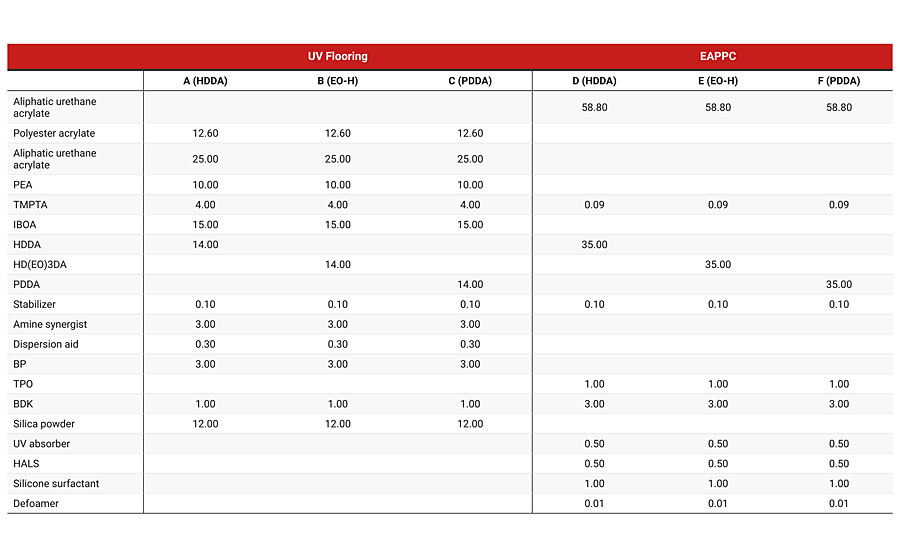
In addition to comparing PDDA to HDDA in these formulations, we also included Ethoxylated HDDA (EO-HDDA) in the evaluation. EO-HDDA is used as a replacement for HDDA when the application requires less irritating raw materials. A full evaluation comparing EO-HDDA with PDDA is in progress, but the initial test results for EO-HDDA are presented in Table 6. Each formulation was evaluated using test methods appropriate for the application.
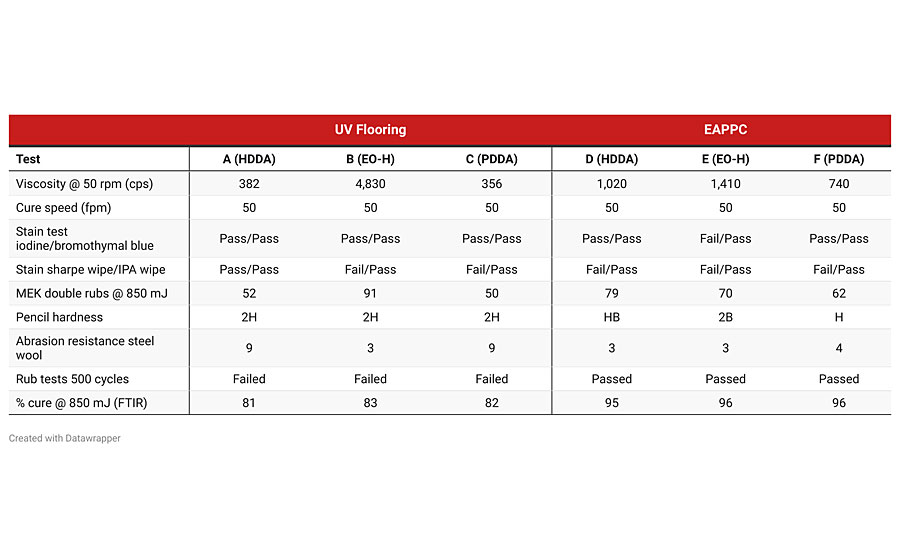
Based on the data shown in Table 6, the largest variation in test results is due to the overall formulation blend and not the substitution of PDDA for HDDA. As seen in the evaluation of the simplified coatings applications, the substitution of PDDA for HDDA had no significant effect on the cured properties. Interestingly, the few small differences in cured properties for the exterior automotive plastic protective coating in the MEK rubs and abrasion resistance were not seen in the commercial formulation for the UV flooring application. It is noted that PDDA does appear to lower the viscosity of the formulation when compared with HDDA, but additional lab work would be required to see if this is consistent across different formulations.
In addition to the test results reported in Table 6, QUV accelerated weatherometer testing is now underway on the six test formulations. At 240 hrs, the PDDA and HDDA formulations show almost identical Delta E values. The QUV accelerated weatherometer testing will be continued for additional time in order to enhance any differences in the Delta E values.
Summary
UV-curable monomers and oligomers play a key role in a wide range of coatings due to their fast cure and excellent cured properties. With few exceptions, raw materials currently used in the manufacture of these monomers and oligomers are petroleum based. To be able to source the key feedstock for these important resins from renewable sources has many advantages, such as a minimum impact on the environment, availability and potentially competitive costs. A process has been developed to make 1,5-Pentanediol (1,5-PDO) from renewable wood and crop wastes. This diol can be converted to 1,5 Pentanediol diacrylate (1,5-PDDA). A series of test formulations comprising both simplified test formulations along with several commercial formulations was selected due to the role that 1,6-Hexanediol diacrylate (HDDA) has in each formulation. PDDA and HDDA were compared through substitution of PDDA for HDDA in each case. Overall, there are no significant differences when PDDA is substituted for HDDA in the test formulations. While 1,6-HDDA is considered as one of the most useful low-viscosity monomers available for UV-curable coatings, 1,5-PDDA made from the renewably sourced 1,5-PDO compares favorably with this workhorse monomer in performance, safety issues and potential cost.
Please direct any inquiries about this article to Tony Franklin at tony.franklin@nagase-nam.com.
Looking for a reprint of this article?
From high-res PDFs to custom plaques, order your copy today!