Improved 2K-Polyurethane Coatings with Polycaprolactone Polyols

Polycaprolactone (PCL) polyols are used to enhance coatings that feature other polymer chemistries in both 1K and 2K coatings. Polycaprolactone polyols are low viscosity and 100% non-volatile, enabling high-solids and ultra-low-VOC coatings. The unique chemistry of these polyols promotes their use in numerous coating applications and on a variety of substrates. This article explores the performance benefits achieved when low-molecular-weight PCL tri- and tetra-functional polyols are blended with other hydroxyl-functional polymers in 2K coatings.
Polyurethane coating technology is well known for its high performance and versatility in thermosetting coating applications. Two-component (2K), solventborne polyurethane (PU) coating systems typically consist of an ‘A’ pack, which contains hydroxyl-bearing polymers (commonly referred to as “polyols”), along with a ‘B’ pack, which contains a polyisocyanate crosslinker. The polyol resin often contains solvent to help the formulator achieve reasonable application viscosities. One common polyol chemistry used is polyacrylic polyols, which can provide a coating with desirable properties such as weatherability, gloss retention, and hardness. Low-molecular-weight polycaprolactone (Capa®) polyols, at 100% solids, can be added to a coating formulation alongside polyacrylate polyols in a 2K-PU coating system to help improve properties such as flexibility and low-VOC levels. Two-component-PU topcoats consisting solely of an acrylate hydroxyl bearing binder, are often low in flexibility, yielding brittleness, which in turn can negatively affect the longevity of a coating in harsh environments.
Polycaprolactone (PCL) polyols offer unique performance compared to adipate polyester polyols due to the manufacturing process employed. During the manufacture of Capa polyols, ring opening polymerization takes place, which minimizes both acid values and active metal impurities in the aliphatic polyol. Thus, PCL polyols are more resistant to hydrolysis and show improved weatherability compared to polyester-adipate counterparts. Low-molecular-weight liquid polycaprolactone polyols are amorphous and 100% solids, which can contribute to a reduction in viscosity and increase in solid content of formulated coatings. The PCL polyols also feature primary functionality and narrow polydispersities.
Low-molecular-weight diols, triols, or tetrols can be added to the 2K PU system to complement the main binder properties. An acrylic polyol is commonly used as the main constituent in a solventborne 2K PU topcoat. This article will explore the change in properties when low-molecular-weight Capa polyols, consisting of a diol, triols, and a tetrol, are formulated into a solventborne, 2K coating system designed for exterior topcoat applications.
Solventborne 2K PU coatings were the first polyurethane coatings developed and are still a very important coating product second only to epoxy technology. The primary reaction is that of isocyanate with hydroxyl moieties. An important feature of these coatings is that they can cure at low temperatures, producing coatings with excellent properties.1 Low or ambient temperature curing is not only important from a cost and processing perspective, but it allows substrates that cannot be exposed to higher temperatures to be protected by coatings, such as plastic (due to heat sensitivity) or floors (due to the size and practicality). Due to the superior performance of polyurethane (PU) technology, PU-based coatings are very-well suited to topcoat applications and perform well when exposed to ultraviolet (UV) light and other harsh environmental conditions.
Polyacrylate polyols are used in a variety of different 2K PU topcoat applications. Common examples include marine and protective coatings, automotive, and plastic coatings. Aliphatic isocyanates, such as those that are based on hexamethylene-diisocyanate (HDI) trimer, are used to crosslink the coating and ensure excellent weatherability. These types of coatings are applied at approximately 60%-weight solids with an isocyanate index close to 100. Dibutyltin-dilaurate catalyst can be used to accelerate the drying time. Part of the reason for superior performance in PU coatings is the creation of hydrogen bonds between the urea-urea, urea-urethane, and urethane-urethane groups within the coating matrix.1
Flexibility is an extremely important property in many applications, including basecoats (where increased flexibility will also improve inter-coat adhesion) and topcoats. If a coating is too brittle, it is more likely to crack or chip when exposed to impact, drastically accelerating any degradation, thus reducing the overall performance of the coating system. Polyurethane coating systems are well known for having a balance between flexibility and durability.
The molecular weight of the di-, tri-, and tetra-functional Capa polyols can also affect the properties of the coating. Properties such as flexibility, impact resistance, scratch resistance, and hardness can be affected or tuned using varying molecular weights. Coatings that have short-chain, low-molecular-weight Capa polyols have the smallest effect on hardness of the coating system. This can be attributed to the typically higher hydroxyl value, which is more likely to result in the increased crosslinking for harder, less-flexible coatings. Longer-chain, higher-molecular-weight Capa polyols can help increase the flexibility due to the lower hydroxyl value, and therefore the presence of longer soft-segment chains of the polyol. The functionality of the polyol can also influence the properties mentioned above, being that lower-functionality coatings, or diols, can influence more-flexible elastomeric-type coatings due to the linearity of the polyol chains, whereas the higher functionality of a triol or tetrol can benefit coatings with higher crosslinking densities. Often formulators have the challenge of balancing the properties mentioned above with the degree of crosslinking, which is essential for the durability and other properties.
The glass transition temperature (Tg) is the temperature were a polymer changes from a rubbery state (above the Tg) to a glassy state (below the Tg).2 The glass transition temperature of a resin used to formulate a PU coating can impact and influence the coating’s final properties. The Tg of Capa polyols is about -60 ºC. A coating that contains low-Tg resins, such as Capa polyols, is typically more effective at influencing higher flexibility, especially when low environmental temperatures are a factor. The low Tg of the Capa polyols can allow a coating to maintain its ‘rubbery’ state at lower temperatures, favoring more flexible, elastic characteristics. Coatings with high-Tg resins will maintain a glassy state at lower temperatures, which means more-brittle, less-flexible mechanical properties.
Low and sub-zero temperatures can prove challenging for many exterior coating systems where high-Tg resins are used in the formulation. For example, protective coatings used to coat structures that are exposed to sub-zero temperatures and impacts from foreign objects are reliant on having elasticity and flexibility to allow the coating to rebound upon impact. Automotive refinish coatings rely on flexibility in the topcoat to help increase stone-chip resistance, and both aerospace and windmill rotary blade coatings rely on flexibility to protect leading edges from impact at high speed and low temperatures.
Another need for industrial coatings is self-healing. Self-healing coatings are highly desirable due to increases in the durability and longevity of a coating. Intrinsic self-heal coatings can repair damage by reversible physical or chemical interactions of the polymers. The mobility of the polymer chains is an important factor in ensuring self-heal ability, along with low Tg, of the polymers used within the coating itself. The use of low-molecular-weight Capa triols can help increase chain mobility of the polymer network within the coating and can help promote the reformation of hydrogen bonding required to facilitate the self-healing process. Tri-functional Capa polyols with high molecular weights can be especially effective at this due to the longer chain length of the oligomers, which can help increase chain mobility, and hydrogen bond reformation upon deformation.3
Coating Formulations and Application
Seven solventborne, clear, 2K PU topcoats were formulated based on an acrylic polyol. One formulation contained only the acrylic polyol, and the other six formulations contained a second polyol blended in. The additional polyol was either one of five Capa PCL polyols or a short-chain, di-functional, adipate-polyester polyol. The PCL polyols and short-chain polyester diol were blended with the acrylate polyol using a ratio of 90:10 (acrylate polyol:PCL/polyester polyol) on total solids. Each coating (‘A’ pack) contained a polyether-modified polydimethyl-siloxane wetting agent and a polymer-based defoamer. Each coating had 0.07%-DBTL solution (10% DBTL in butyl acetate) added (on solid binder content), and a blend of solvents was added to reduce viscosity (9.4% in the total formulation, 1:1:1 xylene, butyl acetate, propylene glycol methyl ether acetate). This was kept constant across all formulations. Additionally, seven more coatings (‘A’ pack formulations) were produced as above, but with 1.5% black pigment dispersion added to help aid the detection of defects in the topcoats during flexibility/impact testing.
A corresponding ‘B’ pack was produced to be used with all ‘A’ component parts so that an isocyanate index of 1.00 was achieved for each coating. The ‘B’ pack consisted of an HDI trimer, typical to those used in 2K PU topcoat applications. Each coating was applied to different metal substrates for testing, including aluminum and mild steel. A 2K-PU, high-build primer was also used to coat some of the metal panels before clear-coat application. Each coating was applied using the K-bar draw-down method, using a 100 µm bar. The target DFT (dry-film thickness) for the clear coat was 40-50 µm. This was measured using a Defelsko Positest DFT gauge. Coatings were left to fully cure at 23 °C and 50% relative humidity (RH) for seven days before testing. Properties of each polyol can be seen in Table 1. Table 2 shows an example coating formulation used for the testing.
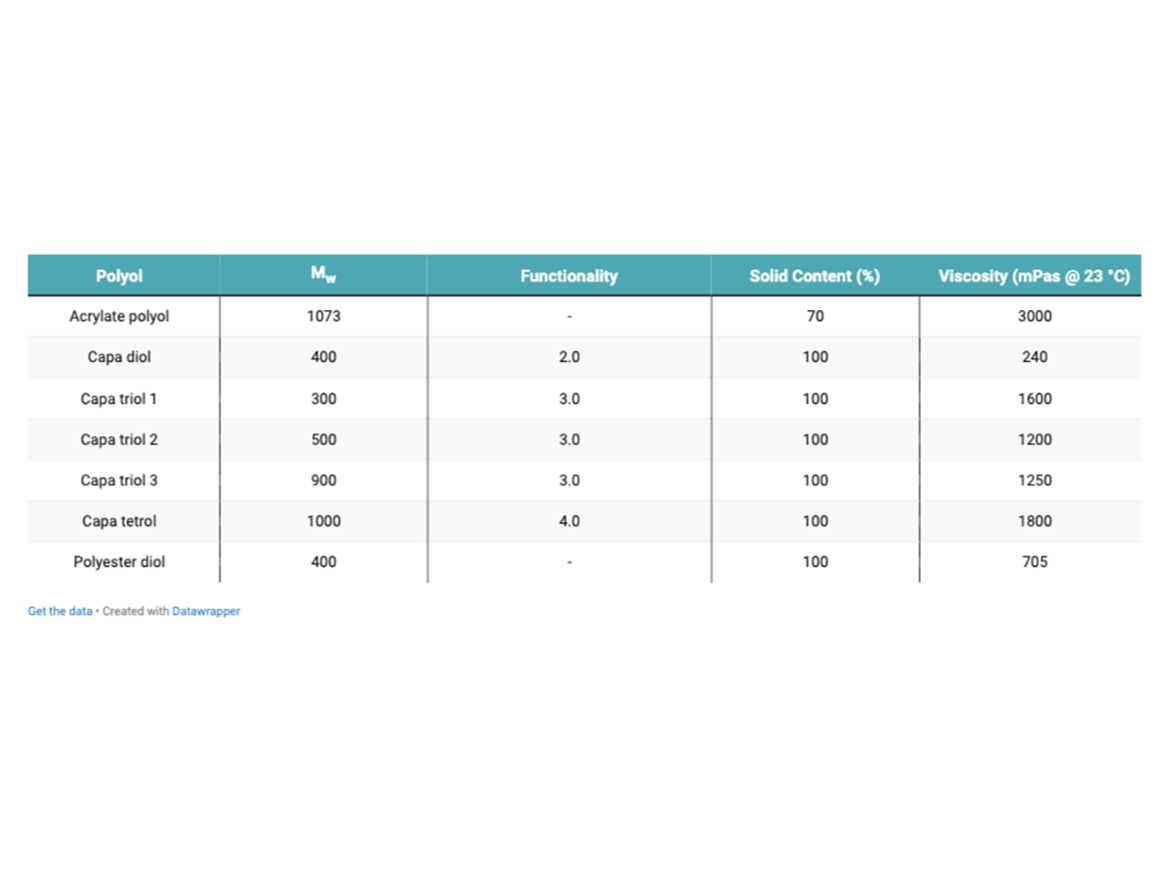
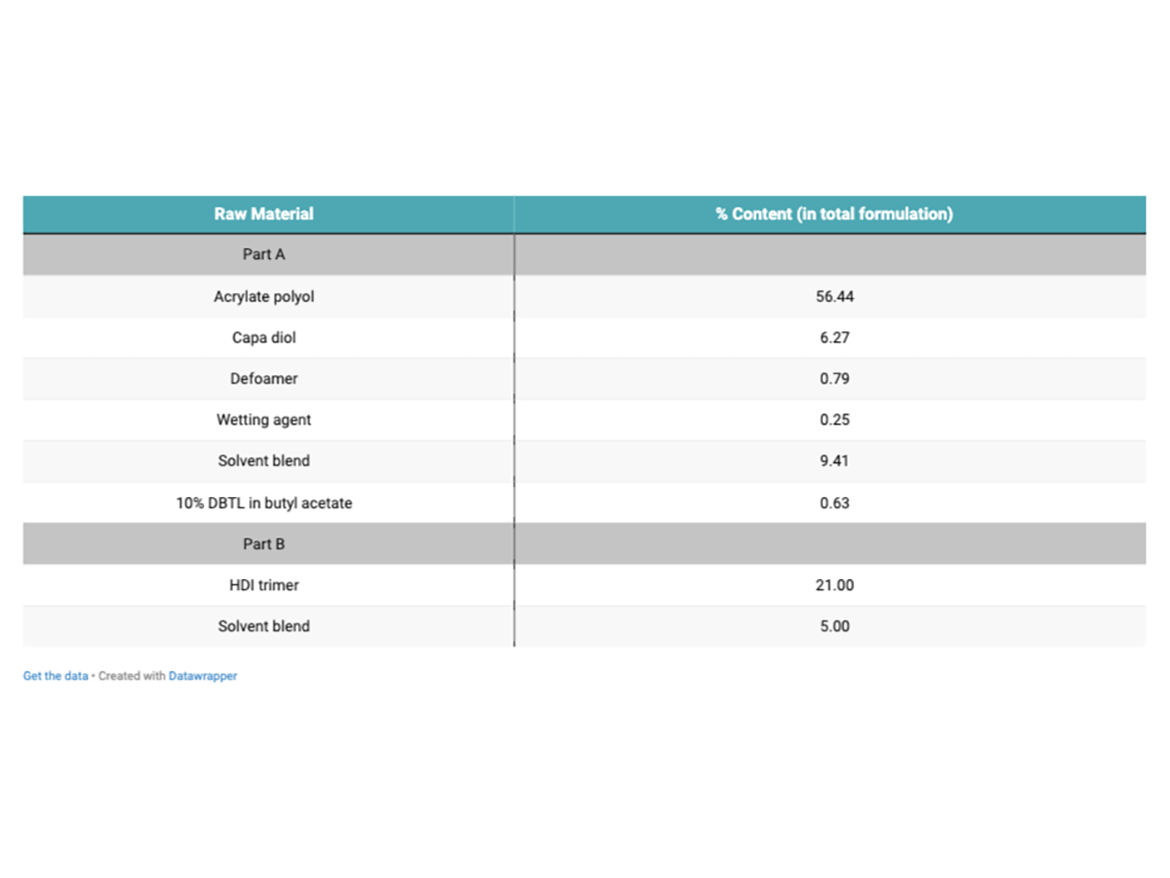
Experimental
Thermal Analysis
Differential-scanning-calorimetry (DSC) analysis was performed on each coating to evaluate the Tg values. The equipment used was a Discovery DSC 25 (TA Instruments). Cured coatings were scraped from aluminum substrates and approximately 5 mg of each were weighed into aluminum sample pans. Thermograms were produced using the following heat-cool, heat-cool cycles:
- Heat 10 °C/min to 100 °C
- Cool 10 °C/min to -50 °C
- Heat 10 °C/min to 100 °C
- Cool 10 °C/min to -50 °C
Taber Abrasion (ASTM D4060)
Mild steel panels were degreased with methyl-ethyl ketone (MEK) and coated with a 2K PU primer. The primer was left to dry for 30 minutes before topcoat application. Each coating was then applied onto the panels using a 100 µm wet-film K-bar and left to cure for seven days at 23 ± 2 °C at 50 ± 5% relative humidity. A dry-film thickness of 40-50 µm was achieved for each topcoat. Each panel was subjected to Taber testing, according to ASTM D4060 using Taber Model 1750, using CS-10 wheels and 1 kg weights. Each panel (panel 1=P1 and panel 2=P2) was pre-weighed then subjected to 400 cycles of abrasion, and each sample was weighed after 100 cycle intervals. After every 100 cycles, panels were removed, wiped with isopropyl alcohol (IPA), and weighed.
Self-Heal and Gloss Recovery
Coatings were applied onto de-greased, mild steel panels. Panels were left to cure for seven days at 50% RH at 23 °C. The specular gloss (60° angle) of each panel was measured, and then each panel was subjected to 40 double rubs of an abrasive media (Scotch-brite™), using an Erichson linear tester 249. A 20-N weight was used to add force. Gloss was measured after the 40 rubs, and then each panel was placed into an oven set at 50 °C for a total of 15 minutes to initiate accelerated gloss recovery. Panels were removed from the oven in five-minute intervals and gloss was measured. Gloss was measured immediately after the panel had been removed from the oven. Specular gloss was measured, and the 60° angle reported. Images of the coatings were taken at 2.5X magnification to demonstrate any visual changes in the best-performing coatings.
Impact Resistance Testing (Rapid Deformation Impact Resistance Test (ISO 6272-1) and Adhesion Testing (ISO 2409)
Panels of aluminum were taken and de-greased with MEK solvent. A 2K PU primer was applied as used previously. Panels were then top coated with the formulated coatings, with each coating containing 1.5%-black pigment dispersion added to the total formulation. The black tinter was used to help aid the visibility of any cracks in the coating film. Panels were left to cure using laboratory conditions of 23 °C and 50% RH. Impact weights were lifted to a height of 50 cm before release, and impacted at room temperature indirectly. Cross-cut adhesion was also performed on the panels to investigate any changes to adhesion. A 3x tape snatch was performed after performing the cross cut using TQC-sheen tape.
Results and Discussion
Thermal Analysis
Table 3 shows the Tg measurements of each sample. The Tg values were taken from the second heat cycle.
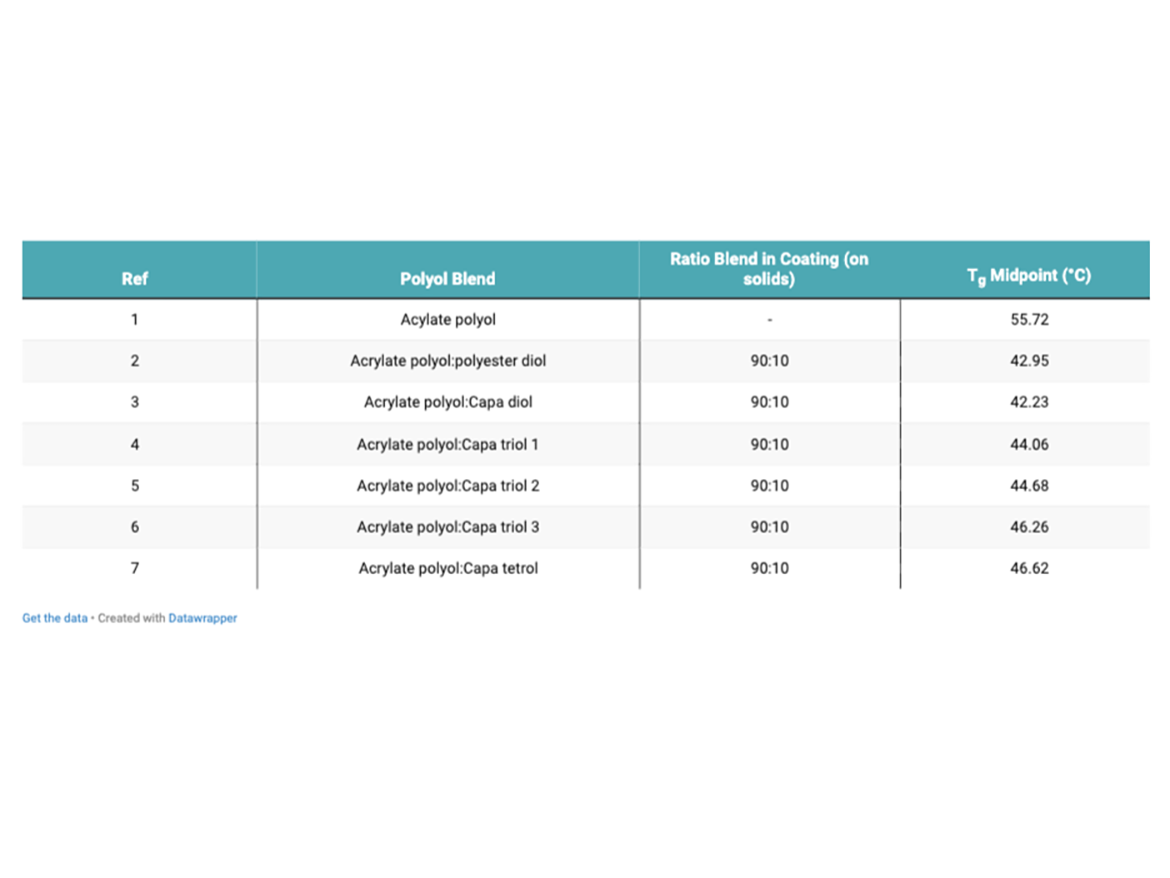
As expected, the Tg of the coatings that have been modified with both the adipate-polyester polyol and the Capa polyols was reduced. The incorporation of the more-flexible chains provided by the addition of the Capa polyols, which have relatively flexible chains because of easy rotation about main chain bonds, reduced the Tg of the coating system.4 The onset of the glass transition marks a significant change in the physical properties of the polymer. A glassy polymer will lose its stiffness and have a tendency to flow above the Tg.4 This influences the properties of a coating that can contain various crosslinked polymers. The polymer chains within a coating with a lower Tg, are more likely to become free to rotate and translate, promoting more-flexible coatings. Coatings that contain Capa triols and tetrol produced slightly higher Tg values. This may be explained by the presence of more chemical crosslinks within the coating film. The crosslinking process tends to reduce the specific volume of the polymer, which in turn means that the free volume is reduced, and so the Tg is raised due to restriction in movement.4 The Capa diol polyol showed the largest reduction in Tg. Diols, due to a lower functionality than that of a triol or tetrol, are anticipated to crosslink to a lesser degree, and therefore promote more free movement within the coating film. This, in turn, can translate to more elastic properties, along with even more flexibility.
Taber Abrasion Testing (ASTM D4060)
Table 4 shows total weight lost after 400 cycles of Taber abrasion. Each test was performed in duplicate. Figure 1 shows the graphical representation of the mass lost after 400 cycles.
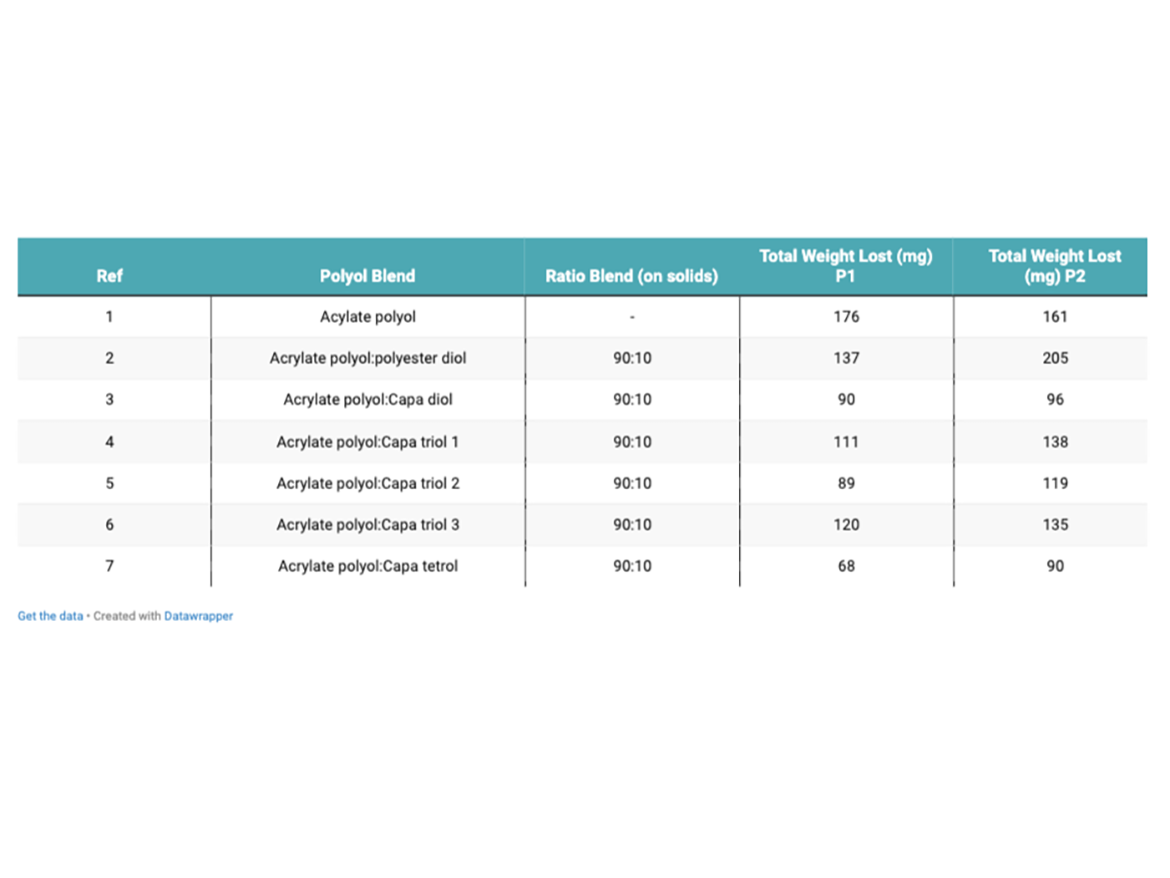
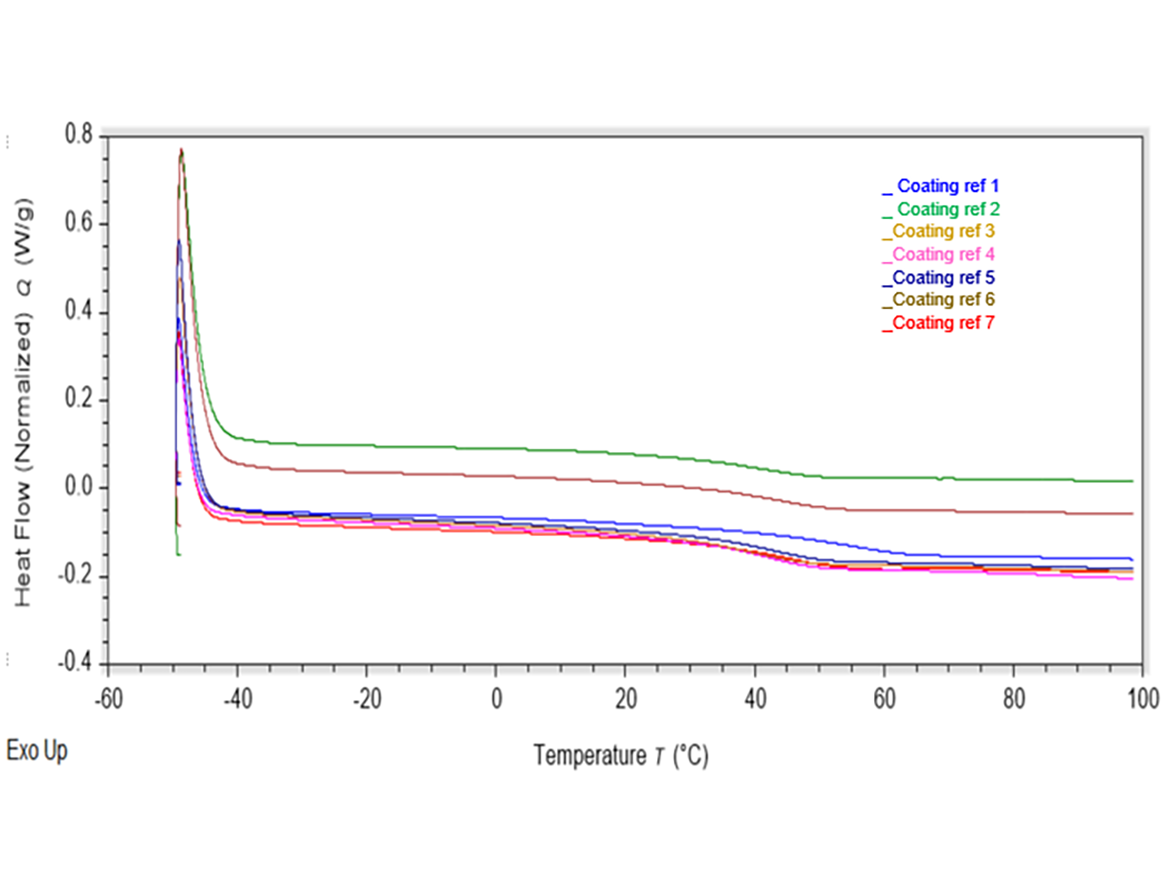
The control coating showed the largest amount of mass loss when subjected to Taber abrasion resistance testing (176 mg P1). The coating that contained Capa tetrol showed the least amount of mass lost during the abrasion resistance testing (68 mg P1). The coating that contained Capa diol also showed excellent abrasion resistance testing. It is likely that the higher degree of crosslinking, and therefore chemical bonding, expected to have occurred using a tetra-functional Capa polyol during curing has helped increase the coating’s resistance to abrasion. Abrasion resistance improvements seen in Capa diol could be attributed to the increased elasticity formed within the crosslinked network. Increased elasticity could help improve a coatings resistance to forced abrasion and increase toughness.
Self-Heal and Gloss Recovery
Table 5 shows the results of the change in specular gloss after panels were subjected to 40 abrasion rubs, and then placed in an oven and subjected to 50 °C, for 15 minutes. Gloss was measured in 5-minute intervals. Figure 3 shows a graphical representation of the change in gloss of each coating system after 5, 10, and 15 minutes exposure to 50 °C. Table 5 shows the visual changes at 2.5X magnification between the control and Capa triol 3.
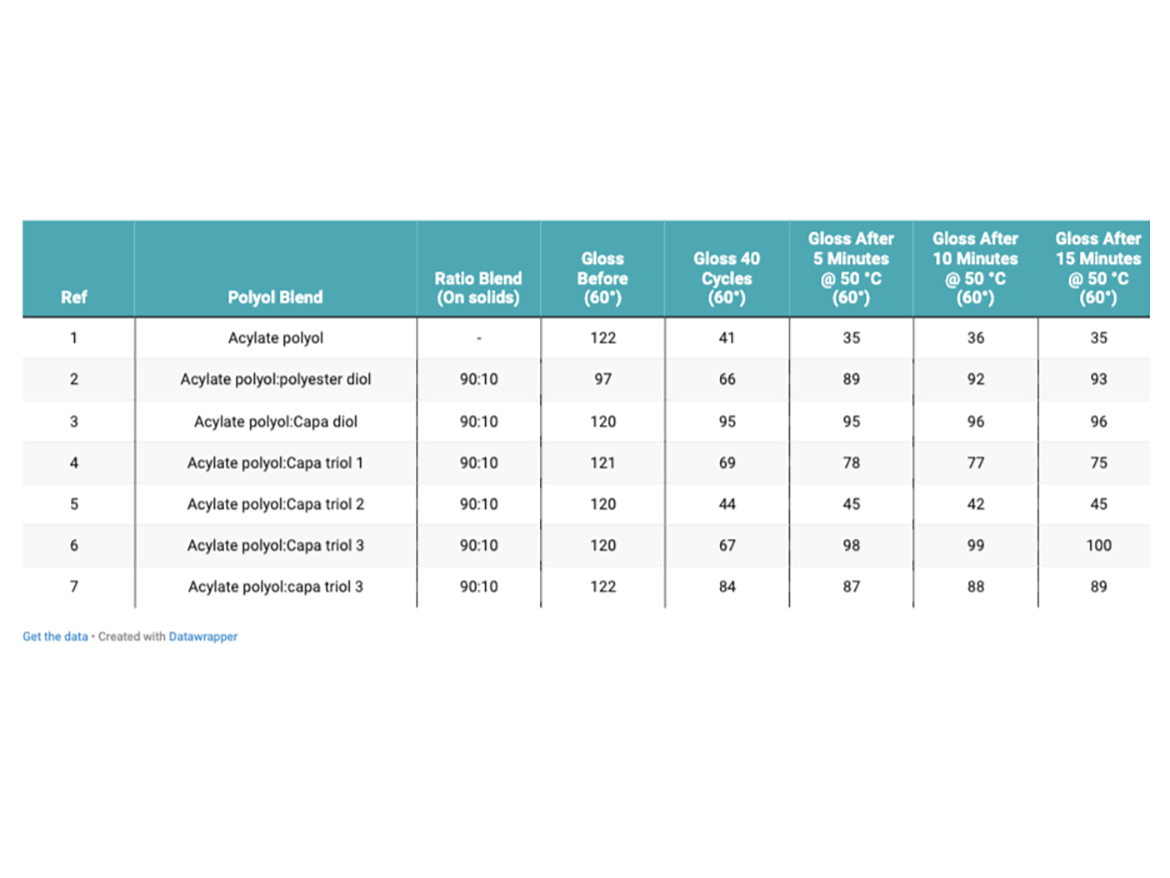
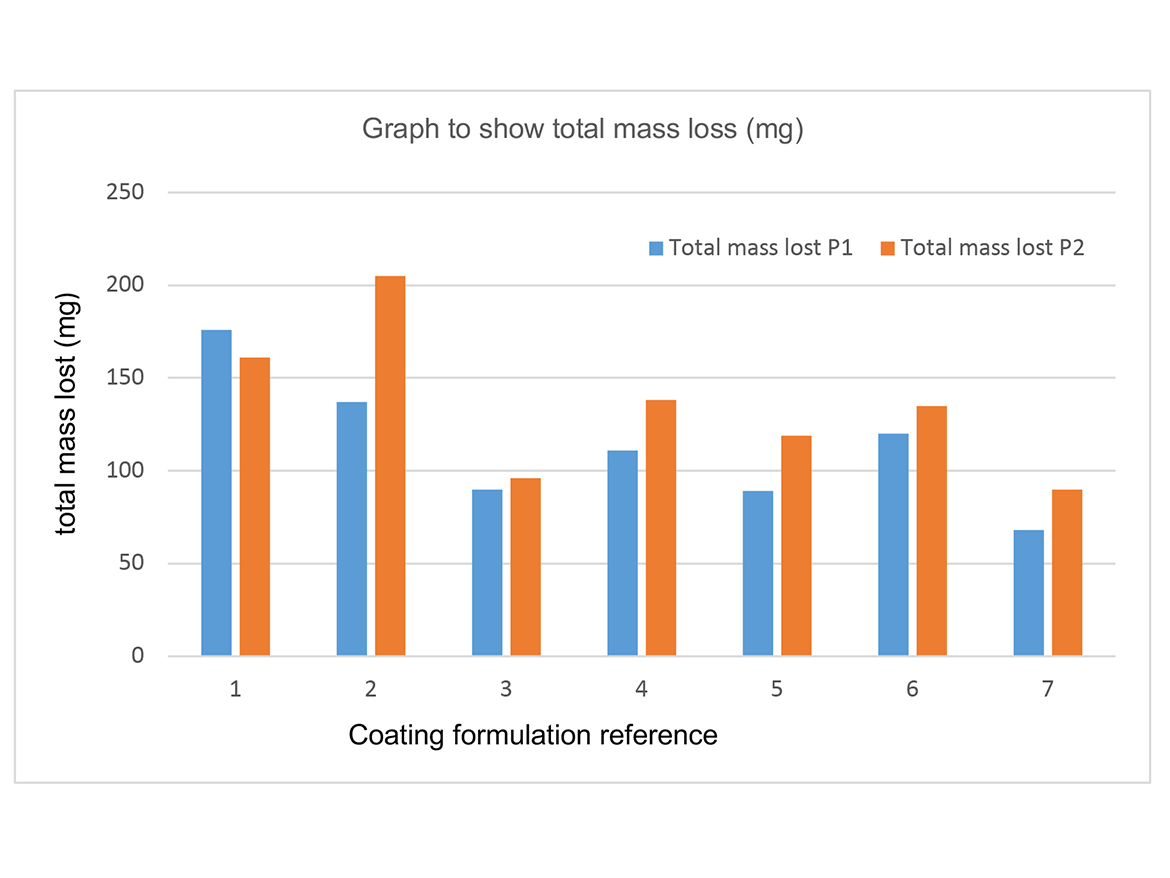
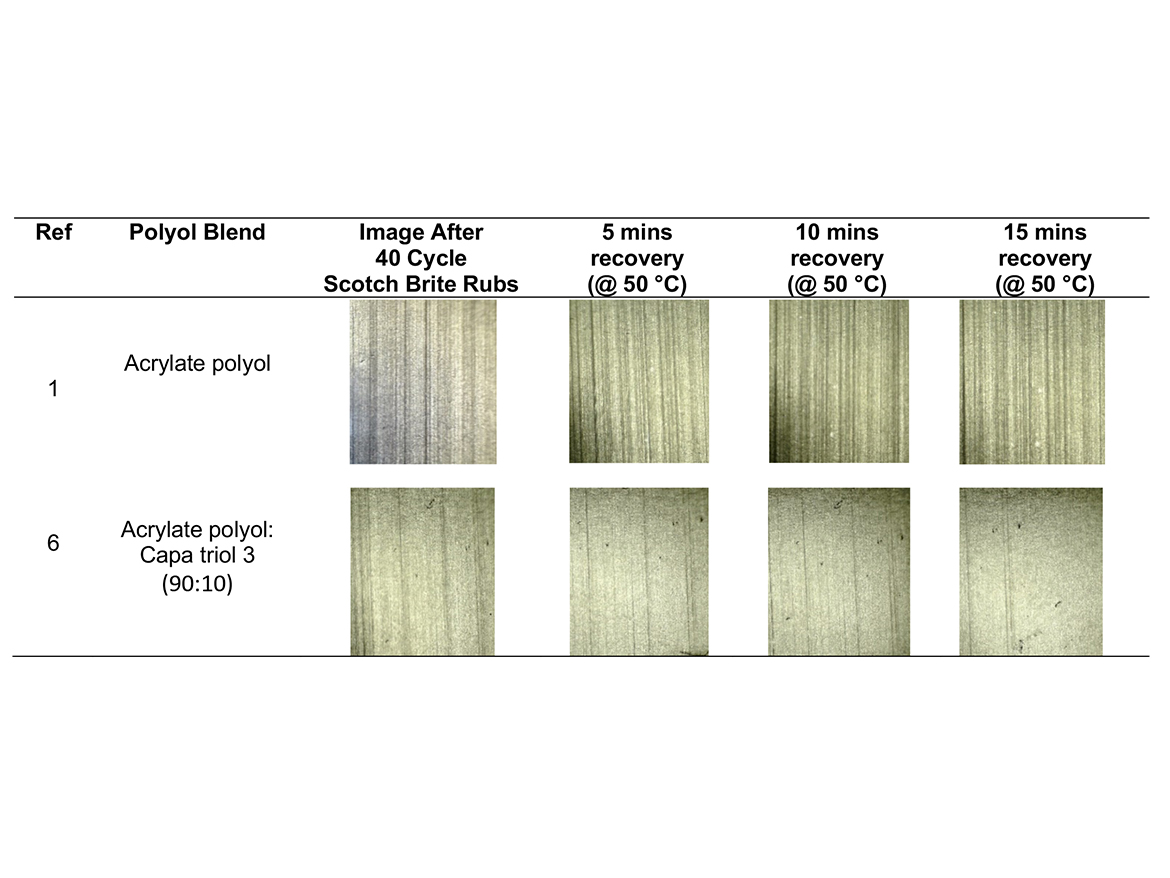
After panels were subjected to 40 double-linear rubs using Scotch-Brite as an abrasive media, the control showed the largest reduction in 60° gloss (41°), indicating the poorest resistance to Scotch-Brite abrasion. Magnification at 2.5X also confirms this. The coating that contained Capa diol showed the least reduction in gloss (95°) after 40 linear rubs using Scotch-Brite. The coating that contained Capa triol 3, which has a higher molecular weight, showed the best gloss recovery over time. This coating regained 82% of its original gloss after exposure to elevated temperatures. The control only regained approximately 29% of its original gloss after exposure to elevated temperatures. Reasons for this could be attributed to hydrogen bonding within the polyurethane coating network. The formation of hydrogen bonds can form a physical bonding network within the coating film. Hydrogen bonds can be separated under stress and can reform again upon release. This not only helps with self-healing properties, but also assist the coating to resist permanent deformation.5 The coating that contains Capa triol 3 is likely to have shown the best gloss recovery due to the longer chains found in the molecular structure, increasing chain mobility to allow hydrogen bonding to re-form, and therefore the polymers’ ability to intrinsically self-heal. 3 While Capa diol also showed excellent resistance to the ‘mar’ of the Scotch-Brite, this is likely due to the increased elasticity and flexibility within this coating helping to improve mar resistance.
Impact Resistance Testing and Cross-Cut Adhesion
Figure 4 shows the images of panels subjected to impact resistance testing and cross-cut adhesion testing.

All coatings passed cross-cut adhesion testing (5B result). The control formulation showed severe cracking when subjected to impact resistance testing from a height of 50 cm. All coatings modified with Capa polyols showed improvement in impact resistance testing, however, the coating that contained Capa diol showed superior results compared to all other modifications (including the 400-molecular-weight polyester-adipate polyol). The elasticity created from the flexible, linear chains of the Capa diol within the coating matrix is a likely contributor to the superior results. The increased elasticity is likely to have created a polymer network that is more likely and able to absorb the energy created from a quick impact, significantly reducing the chance of damage to the coating surface. Capa triol 2 also shows a significant improvement in impact resistance compared to the control. The ‘middle’ molecular weight of Capa triol 2 has shown a good combination of crosslinking, along with flexibility.
Conclusion
Polyurethane coatings are governed by a balance of hardness and flexibility. By the addition of Capa polyols to the acrylate polyol within a PU coating, flexibility was greatly improved with minimal effects on other properties. This improvement is essential to allow the PU topcoat to perform to the highest possible standard. This has been shown by the results of the impact-resistance testing. By incorporating a low-molecular-weight Capa diol into the coating system, the elasticity rebound properties were greatly improved. This is especially important in coating systems that need to retain toughness and flexibility as part of their function (e.g. automotive topcoats and leading-edge coatings). Capa triol 3, in particular, was shown to influence a coating’s ability to intrinsically self-heal, especially important in coatings that may need to resist marring. Although a reduction in Tg can be observed by incorporating low-molecular-weight Capa polyols, abrasion resistance and mar resistance is still greatly improved. In comparison to the Capa diol, the adipate-polyester polyol had inferior performance. The adipate-polyester polyol showed poorer abrasion resistance, impact resistance, and mar resistance. The low viscosity of Capa polyols, compared to both acrylic- and polyester-adipate technology, enable higher solids and lower-VOC coatings. Further investigation into optimal concentrations of Capa polyols within a coating could help improve properties of PU coatings even further.
Acknowledgements
The author would like to express acknowledgements to fellow team members who helped make this work possible: Amanda Tosh, Jamie Parsonage, Elizabeth Melia, Sian Higlett, Tom Duffy, Mike Aslet, and Graham Carr.
References
1 Randall, D.; Lee, S. Huntsman Polyurethanes. The Polyurethanes Book, 2002, 336-338.
2 Akkerman, J.; Mestach, D.; et al. Resins for Waterborne Coatings, 229.
3 Cuevas, J.; et al. Progress in Organic Coatings, Progress in Organic Coatings, 163, 2022, 106668.
4 Young, R.J.; Lovell, P.A. Introduction to Polymers, 292-300.
5 Wicks, Z. W.; Jones, F. N.; Pappas, S. P.; Wicks, D. A. (2007). Binders Based on Polyisocyanates: Polyurethanes. Organic Coatings: Science and Technology, 3, 231-270.
Looking for a reprint of this article?
From high-res PDFs to custom plaques, order your copy today!