Novel Sag Control Agents for a More Robust Paint ApplicationProcess and Reduced Telegraphing
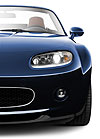
In order to obtain glossy coatings with a high-quality appearance it is necessary that surface irregularities created during paint application or during drying/curing of the paint level out sufficiently, while sagging problems are avoided. In this paper it is shown that paint thixotropy can be very useful in increasing sag resistance, improving coating appearance and widening the application window. Thixotropy can be introduced in paints by addition of sag control agents. New Sag Control Agents (SCAs) have been developed based on chiral amines, which are very efficient (%SCA needed to obtain a given amount of sag resistance) and are also able to suppress telegraphed roughness from the substrate more than the existing SCAs.
Introduction
One of the major requirements for glossy coatings, such as automotive clearcoats (CC), is to have a perfectly smooth surface after the curing process. Coating appearance is the result of the often-complex influence of many different parameters including the rheological properties of the paint; applied layer thickness; initial surface roughness created during the application process; surface tension of the paint and the development of gradients thereof; drying and curing conditions; solvent mix, and the roughness of the (coated) substrate on top of which the paint was applied.(1-11) Evidently, it is far from easy to determine the relation between for example the rheological properties of the paint on the one hand, and the final appearance of the paint on the other. Intuitively, it can be understood that the viscosity of the paint must be low enough to enable sufficient leveling out of all surface irregularities caused by the spraying process. On the other hand, the viscosity must be high enough to avoid the occurrence of sagging defects, like the formation of tears or sagging curtains. From this it can be understood that sufficient leveling and minimizing sagging are often conflicting requirements and, in practice, the rheological properties of paints have to be carefully controlled to get an optimum balance between the sag and leveling behavior of the paint.(12)Many years ago we introduced sag control agents(13-15) based on the reaction product of 1,6-hexamethylenediisocyanate (HDI) and benzylamine (BA), yielding so-called ‘opaque SCA’, named after its opalescent appearance in the paint. These opaque SCA crystalline particles form a weak, three-dimensional network in the paint. This network is disrupted under shear, and when the shear is decreased it will build up again in a certain period of time, thus providing the paint a thixotropic behavior. At higher temperatures, e.g., as used in OEM stoving applications (> 100 degreesC), these HDI-BA crystals completely melt or dissolve and become fully transparent in the final coating, making them applicable in clear coatings.
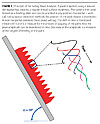
The Falling Wave Method
To determine the sag and leveling behavior of paints during drying and curing in a quantitative manner, we have developed an optical (contact-less) analyzing method, the so-called ‘falling wave’ method.(16) It uses paint layers with a well-defined initial surface roughness, created using a sinusoidal rippled application bar (Figure 1). Directly after paint application, the coated substrate is transferred to the temperature-controlled support plate of the falling wave apparatus, and the experiment is started. The paint surface is illuminated, and the reflections of the glossy paint surface are recorded using a camera and analyzed and stored on a PC using image analysis software. Dedicated analysis software is used to quantitatively calculate both the position and the shape of the waves from the measured reflection image. The insert in Figure 1 shows an example of the development of the position and shape of a single wave determined during drying and curing of a paint layer at various time intervals.The angle of inclination of the temperature-controlled support plate with the coated panel can be varied from 0° to 90° (60° in the example shown in Figure 1). In a typical falling wave test in this study, the wet paint is allowed to dry under ambient conditions for a certain period after which the temperature of the support plate is increased to 140 °C to simulate high-temperature curing of the paint as under automotive OEM conditions. The determined change of the shape (e.g., decrease of amplitude) of the waves is a measure of the degree of leveling. On non-horizontal panels, the amount of sagging is determined from the movement of the waves towards the bottom of the panel (referred to as ‘wave-shift’ hereinafter).
When determining telegraphing in the falling wave method, a substrate is used with a sinusoidal surface, albeit with a wavelength different from that of the rippled bar used to pre-shape the surface of the wet coating (as explained above). When telegraphing occurs, the sinusoidal waves of the substrate get super-positioned to the sinusoidal waves of the surface of the coating allowing discriminated detection and quantitative analysis.
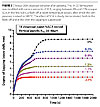
Telegraphing
Telegraphing is a phenomenon where the roughness of the substrate is reflected in the new surface of the drying paint. It is caused by local variations in shrinkage, especially when the viscosity of the drying or curing film has increased enough to hamper good leveling. Another cause for the occurrence of telegraphing is hidden in the development of surface tension gradients during drying and curing. It goes without saying that it is the paint formulator’s intention to suppress telegraphing as much as possible.In this study we have investigated options to help reduce the telegraphed roughness in clear coatings. The dominant notion is that if it would be possible to create a process where all shrinkage (physical shrinkage caused by solvent evaporation and chemical shrinkage caused by the curing reaction itself) would occur before the film loses its ability to level, then all surface roughness from whatever cause would be leveled out. The question is how to achieve this, especially when substrates can have all kinds of orientations.
Based on our experience with SCAs, where a judicious balance between leveling and sagging is needed, we looked for possibilities to create late-stage fluidity. For OEM-type applications this implies more fluidity in the oven. However, SCAs were introduced into the market with the purpose to prevent oven fluidity! The high temperature causes the viscosity of the still uncured paint layer to drop to very low levels resulting in severe sagging.
Figure 2 shows the typical sagging and leveling behavior of an OEM clear coating modified with opaque SCA. Note in this figure that SCAs are effective in reducing sagging in both the flash-off and in the oven; however it is most effective in the oven. Further, note that the total amount of paint sagging is represented by the wave-shift value at the end of the process. For this ‘total sag’ it is irrelevant if most of the sagging occurs in the beginning or towards the end of the process. When this was realized, we knew we had to look for different SCAs: SCAs that would be stronger during the flash-off and somewhat less effective in the oven.

Novel SCAs
There are two key-properties of SCAs: the first is the ability of the crystal particles to form (weak) 3-dimensional networks, providing the controlled rheology; the second requirement is the ability to completely disappear (for di-urea type SCAs: to melt and/or dissolve at elevated temperatures). For obtaining more fluidity in the oven, a lower melting/dissolving temperature is the first solution to look for. We have synthesized almost a hundred new SCA-like compounds. A specific group emerged as particularly suitable for our purposes: SCAs based on optically active (chiral) amines. We found SCAs based on these amines in general to be more efficient (i.e., the viscosity increase per % SCA added to the paint) than the reference opaque SCA. We were also able to make SCAs or SCA mixtures that had a wide range of melting temperatures. Figure 3 shows three completely different types of new SCAs based on chiral amines. Note the differences in both shape and size of the SCA crystals.
Application Process Efficiency and Robustness
Figure 4 shows the effect of using opaque SCA and one of the new SCAs; it is clearly demonstrated that the robustness of the paint process is improved by using SCA. Both show the sagging to be less dependent on the layer thickness (a more horizontal line in the figure). This figure also shows that the selected new SCA is (per amount added to the paint) more effective than the reference opaque SCA.
The effect on telegraphing is visible in the curves defined by the filled symbols. During heating most of the solvent evaporates, causing the film to shrink. The reference SCA is already very effective in the warming-up phase and beyond and prevents sagging, but also leveling; thus telegraphing increases rapidly. The new SCA, however, does allow leveling during warming-up and at the curing temperature. As this SCA was very effective in suppressing sag during the flash-off, there is some ‘buffer’ for late-stage sagging (i.e., leveling) without causing sagging defects. As can be seen in the telegraphed amplitude (blue line/filled symbols), again the film shrinks when the temperature goes up after about 400 seconds, but the increased fluidity of the coating is not completely suppressed. Therefore, a considerable fraction of the telegraphed roughness is leveled out. In the end the telegraphed substrate roughness is less than half of that of the reference case.


The behavior of the LW value at a layer thickness of about 54 um is not fully understood. Although the gain in LW is relatively modest, it is significant. Paint formulators may be better equipped to exploit the benefits of the new SCAs to the maximum.
Conclusions
For high-gloss coatings, such as automotive clear coats, it is challenging to obtain a perfect final appearance especially under varying application conditions. In order to facilitate paint development with an optimized balance between sufficient leveling out of surface irregularities and the avoidance of sagging defects, it is highly beneficial to study the sag and leveling behavior of paints during the drying and curing process in a quantitative manner.The falling wave technique can be used for this purpose and has proven to be useful in identifying the cause and nature of poor coating appearance. This method was used to study the influence of sag control agents, which consist of particles formed by the crystallization of urea molecules, on the sag and leveling behavior of paints. Addition of SCA to e.g., automotive clearcoat paints results in a considerable increase of the sag resistance both during flash-off drying as well as during high-temperature curing. Furthermore, the use of SCA’s has several unique advantages including a more robust sag/leveling balance with respect to variations in e.g., applied layer thickness during the application process (widening of the application window).
Newly developed SCAs allow (independent) tuning of the paint fluidity during the different stages in the flash-off drying and curing process. Optimization of the degree of late-stage fluidity was shown to be useful in reducing the effect of telegraphing for paints applied on uneven (coated) substrates.
This paper was presented at the Nürnberg Congress held during the European Coatings Show, Nürnberg, Germany, 2007 and organized by the Vincentz Network. See events@coatings.de. The paper was also published in ECJ 12/2007.
Looking for a reprint of this article?
From high-res PDFs to custom plaques, order your copy today!