Pearlescent Pigments in Coatings – a Primer

Pearlescent pigments are widely used in a variety of applications, from cosmetics to plastics and inks to automotive topcoats. The goal of pearlescent pigments is to mimic the inherent gleam and luster of natural pearls. This is achieved by utilizing the light reflection characteristics of microscopic platelets and the optimization of their diffraction and diffusion properties. There are several types of pearl pigments commercially available, including natural pearl essence, bismuth oxychloride crystals and oxide-coated micas. There are also several other types of substrates that can be oxide coated, such as glass flake and platy alumina.
The most commonly used type is the oxide-coated micas; this also includes synthetic mica or fluorphlogopite. They are plate-like flakes of mica that are coated with thin layers of titanium dioxide (TIO2) and/or iron oxide, and potentially other metal oxides. The broad face of the platelets can range from 4 microns to 1,000 microns across and are approximately 0.5 micron thick, although synthetic micas can achieve thicknesses of less than 0.25 micron. The platelets of coated mica are very smooth, so they are light reflective while maintaining a high degree of transparency, which means only a portion of the light is reflected. The portion that is not reflected is transmitted through the platelet to the next layer where it can be further reflected (Figure 1A).
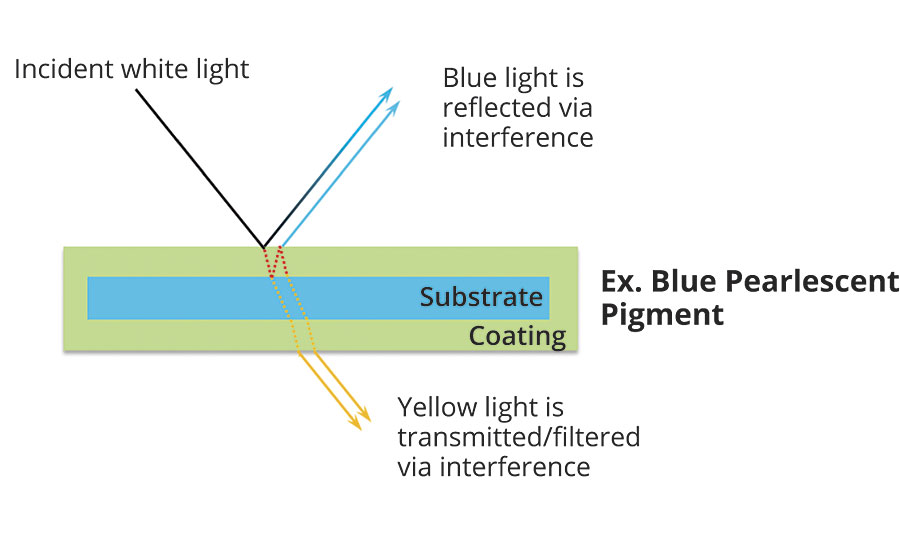
The results are multiple reflections from many layers. The eye cannot focus on any one layer, and a sense of depth is established, as seen in Figure 1B. Thus, a particular kind of shimmery luster called pearlescence is observed.
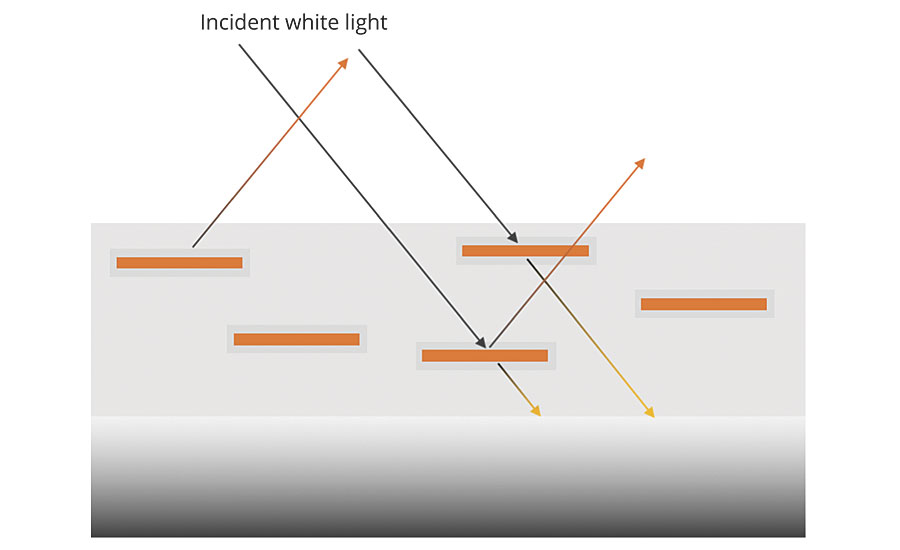
In addition to providing a pearlescent or lustrous look, certain titanium dioxide-coated micas are capable of showing colors through the optical effect of interference. The large difference in the refractive index of titanium dioxide (n ≈2.7) and mica (n ≈1.5) allows for a large degree of not only reflection of the light but bending and phase shift of the light waves as well. The color develops when certain wavelengths of light reflected from one layer interfere or cancel out the same wavelength from another layer. The result is that only a narrow band of wavelengths is reflected and a single color is seen. This is much the same as colors seen in films of oil on water or soap bubbles. Each interference color is determined by the thickness of the titanium dioxide layer on the mica. Increasing the titanium dioxide thickness results in the beginnings of interference, changing the reflection color to yellow. Increasing it further shifts the color to red, followed by blue and then green (Figure 2).
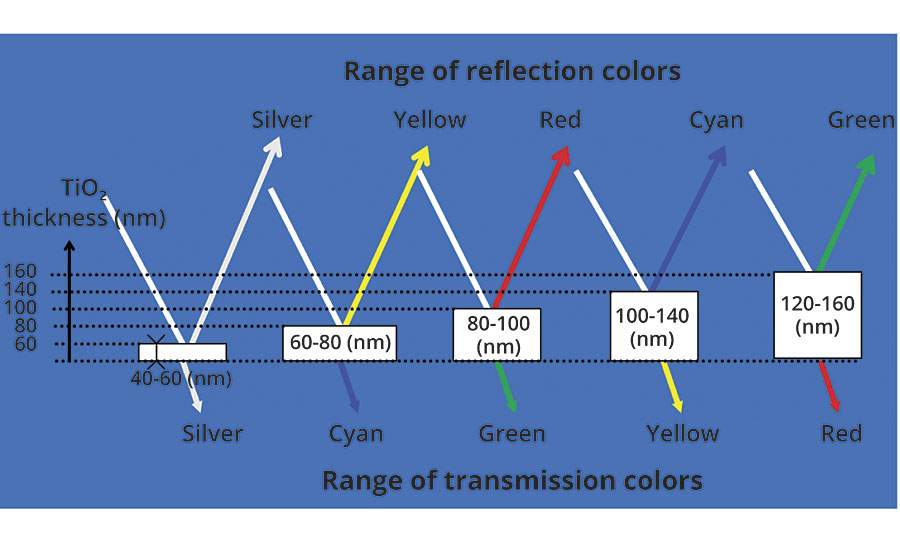
White pearl reflection color is produced from very thin, uneven titanium dioxide coatings, resulting in a mixture of colors being reflected. The reflective light is additive and combines back to form white light.
It is important to note that because these types of pigments do not absorb light, only redirect (reflect, refract and transmit), they will behave in accordance to the additive color scheme. This is different than the typical subtractive color scheme traditional pigments use. With additive color, the primary colors of reflected light (red, green and blue) can “add up” to white light (Figure 3).
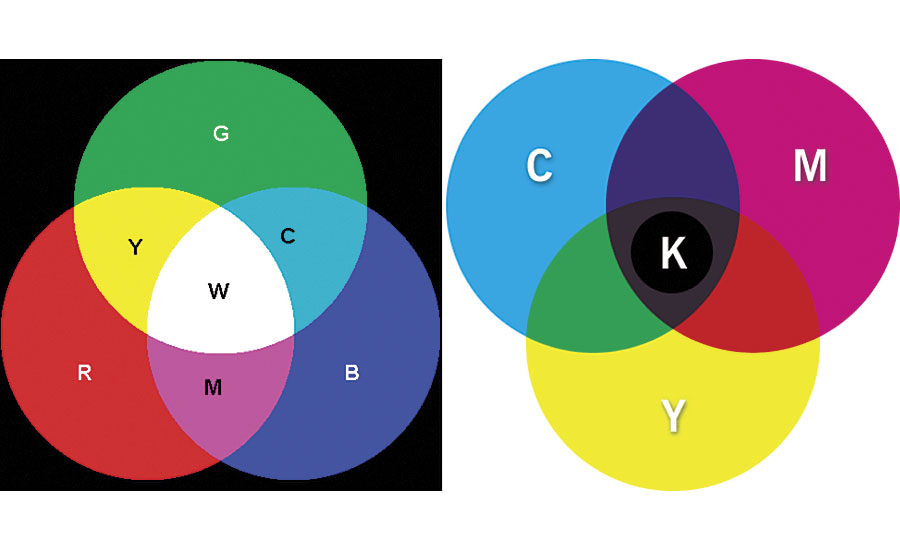
Traditionally, blue and yellow may be mixed to create green, but if a blue interference and yellow interference pearlescent pigment are mixed, a white reflection is created. For this reason, it is not advised to mix interference colors other than for mild shading.
The iron oxide coatings exhibit the same interference properties as the titanium dioxide coatings, except the iron oxide contributes color of its own due to absorption. Bronze colors correspond to the combination of a yellow absorption color due to the Fe2O3 and a yellow interference color due to the thickness of the Fe2O3 layer. Copper and russet colors are produced by similar effects (Figure 4).
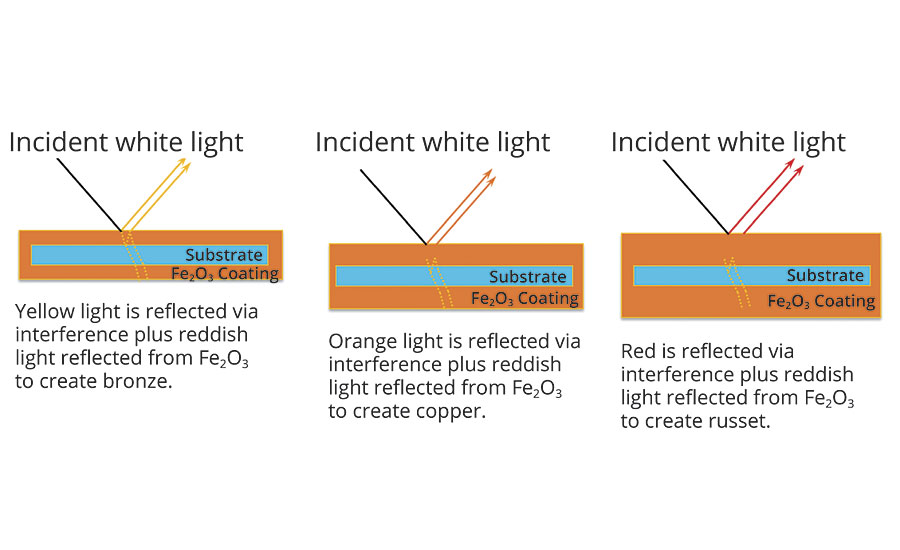
Due to their inherent transparency, the color of pearlescent pigments can be affected by the color of the material over which they are applied. When it is on a white background, the transmission color can be seen at all angles, and the interference color is not obvious. When it is on a black or dark substrate, the transmission color is adsorbed by the substrate, and the interference color is strong and bright at the specular angle. At the specular angle, the interference color is observed. At diffuse angles, the complementary color of that interference color is seen because the light is transmitted through the film.
For example, when an interference red pigment is present in a coating film, a red color is seen at the specular angle and a green at the diffuse angle. White pearls are white at specular and will transmit either the substrate or tinting color at diffuse angles. It is the sense of depth and color changes at different viewing angles that make a pearlescent pigment different from a metallic flake pigment.
In metallic flake pigments, such as Al, the aluminum flakes are opaque to light; no light is transmitted. All the light is reflected from one layer as in a mirror, and one cannot get a sense of depth as with pearlescent pigments. When absorption colorants are added to pearlescent pigments, light penetrates through the transparent platelets to the colorants and then reflects back. Thus, the colors from the absorption pigments are brightened and enhanced.
If colorants are added to metallic flake pigments, the metallic flakes being opaque do not allow the light to penetrate, and the colors are subdued. In the case of aluminum, the aluminum itself has a grayish color, and the colors from absorption colorants are actually muddied.
Metallic pigments, similar to pearlescent pigments in their size and shape, reflect light in a specular fashion. That is, light coming in at a 45° angle will exit at a 45° angle. As the viewing angle is increased, the reflection drops off and the color appears dark. When one looks at different viewing angles of a coating containing metallic pigment, only the lightness changes, not the color as seen with pearlescent pigments.
Appearance
There are several factors influencing the luster and appearance of a finished coating. Flake orientation, particle size, pigment concentration and coating film transparency are among the most important ones.
Particle Size
Pearlescent pigments are offered in several highly controlled particle size distributions. The size will influence luster, coverage and the appearance of coatings. Table 1 features a list of common distributions and their apparent effect.
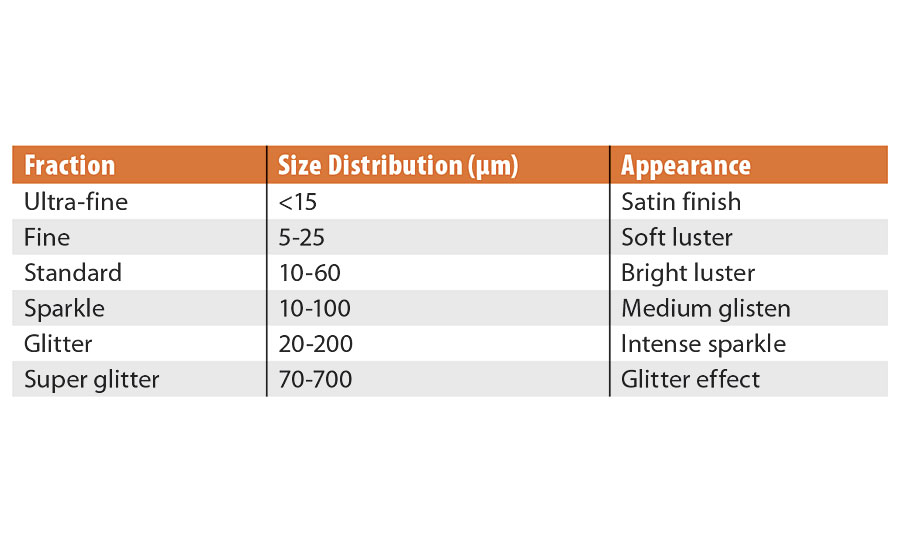
The luster will generally increase as the particle size increases, however, the optimum distribution is 10 to 60 microns (Figure 5).
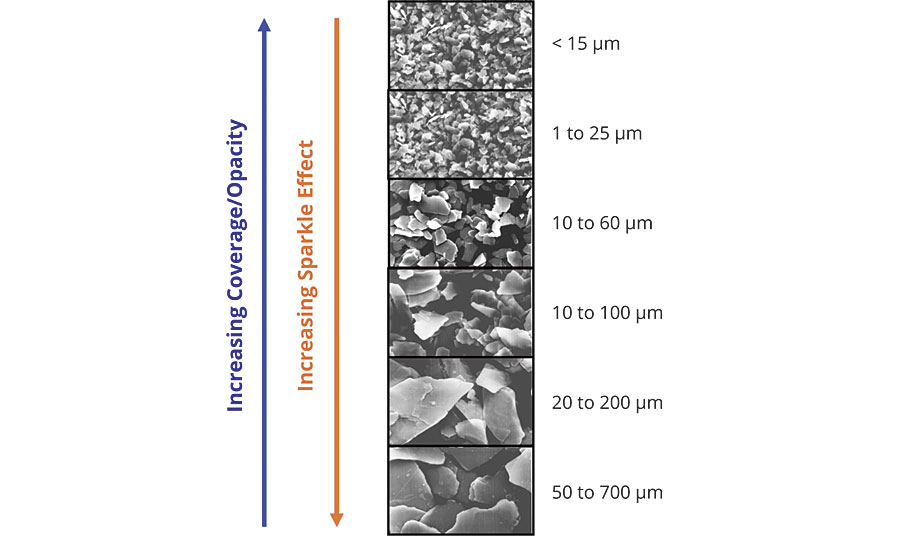
This particle size distribution is tight enough to ensure a uniform oxide coating across all the particles, helping to further boost the color intensity. It also creates a D50 that is optimal for light reflection with minimal edge scattering. An example of this type of product would be SunMICA High Chroma Blue, 281-1257. The larger distributions will appear sparkly or star-like and provide the least coverage, while the small distributions will appear with a satin effect and have more coverage.
Particle size can be measured by several methods, including visual observation using a microscope, sieving and laser light scattering, which is the most common approach. In this method, a pigment sample is dispersed in a liquid while a laser is trained on the liquid sample so that the platelets scatter the beam. Accurately positioned detectors measure the scattered light. Large particles scatter to a narrow angle and small particles to a large angle. A computer calculates a size distribution based on the intensity of scattered light at the different angles.
Laser light instruments provide several pieces of information. They can provide differential or cumulative size distributions, percent below a specified size, size below a specified percent (ex: D50), and a distribution mode (the most populous size interval). Each piece describes a different attribute. No single piece is capable of completely describing the size distribution or the effect it will produce in a paint. Therefore, it is often necessary to use several data points for this purpose.
An important point about light scattering instruments is that they assume the particle being measured is a sphere; not a platelet. Therefore, the size distribution is relative and not an absolute size measurement. In addition, different sizing instruments give different results. Large particles are emphasized because it takes thousands of small particles to equal the weight of one large particle.
Orientation
Maximum reflection and color travel are only achieved when the platelets are uniformly oriented parallel to the substrate. This is achieved primarily by film shrinkage and leveling of the coating while it is drying. It can also be affected by the size of the particles.
Film shrinkage is directly related to the total solids of the coating. Low-solids coatings shrink more than high-solids coatings, thereby improving the orientation and color travel. This is one of the primary reasons why high-solids coatings containing mica are a different color versus low-solids waterbornes, even though the pigmentation is the same. Better pigment dispersion, slow evaporating solvents used in the coating formulation, longer flashing time, or a ladder baking schedule will also improve orientation of the pigments and achieve maximum luster. Figure 6 demonstrates this influence of two different solids formulations.
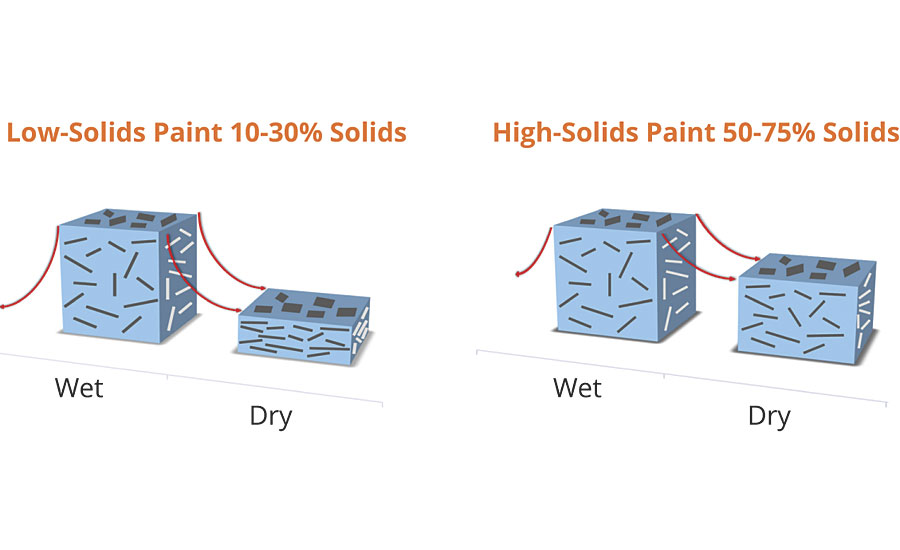
In addition to the degree of orientation, orientation uniformity is also a factor affecting appearance. Poor orientation uniformity is referred to as mottling. The result is light and dark patches of color and is usually visible on large flat areas. The dark areas are a result of platelets lying partially on edge. This problem is common to all flake pigments, including metallics. There can be several causes for this, including pigment flooding or floating, and convection currents created by solvent evaporation. Pigment flooding can be solved through proper dispersion and it will be discussed later.
Convection currents are caused by solvent evaporation producing cooling at the surface of the coating. As additional solvent and heat rise from within the coating, they create a current that can tilt the plates on edge. Mottling can be reduced by using pattern control agents. Cellulose acetate butyrate (CAB), NADs (non-aqueous dispersions) and waxes are commonly used.
These are high-molecular-weight additives that increase the viscosity of the paint in a Newtonian fashion during flash off and baking. The Newtonian increase in viscosity prevents the flakes from being tilted by the weak convection currents but allows the flakes to orient as the coating film shrinks. Thixotropic additives are usually not effective because they cause the viscosity to increase too quickly after spraying. They tend to lock or freeze the flakes in place in random orientation, not allowing them to flow out and level.
Pigment Concentration
While a certain amount of pigment is needed to create a color effect and reasonable hiding, excessive amounts of pigment will quickly degrade the appearance. When too much pigment is added, the pigment particles contact each other and prevent the free orientation of platelets, resulting in reduced luster. Another factor is edge scattering. Edge scattering is caused by light being scattered off the edge of the platelet, increasing the diffuse reflection as opposed to the bright, specular reflection.
The optimum loading is generally 10-20% pigment based on total solids of paint. A lower amount can be used to create subtle, soft effects. Sometimes, it may be more advantageous to use less pigment (1-1.5%) in order to obtain a pearlescent effect over a colored base coat.
It is also important to consider the particle size of the pigment when choosing a pigment loading. Larger-particle pigments are best used at lower loadings to avoid over-crowding. This results in a higher sparkle effect, as the individual platelets are evenly spaced and the pinpoints of reflected light can more easily be seen by the eye. Pigments in the >200 micron range can be used at loadings as low as 0.1%.
Film Transparency
Given the optics of pearlescent pigments, it is important that light enters and exits the film unobstructed. Therefore, any pigment or additive that provides opacity or decreases light transmission (i.e., light scattering) through the film will reduce or eliminate the luster. Some examples are pigmentary titanium dioxide, calcium carbonate and talc.
Developing Hiding
The disadvantage of the pearlescent pigment’s transparency is the lack of coverage. It is possible, however, to formulate colors with a fair degree of coverage with dry film thickness of 15-25 microns. There are several ways to improve the hiding during formulation.
1. Smaller particle size of pearlescent pigment can be used to increase hiding, but it will produce more satin and less brilliant luster. With the least appearance change, a portion of the large pearl pigment (not more than 20%) can be replaced by a smaller-size pearl pigment.
2. Because of the opaque character, metallic pigments, such as aluminum or bronze flakes can be added into coatings to improve the hiding. The amount is usually 5-10% of the pearl pigment.
3. When a dark color is formulated, a small amount of carbon black will provide good hiding. The addition of black will increase the pearl’s interference color.
4. For a light color, TiO2 is a good choice to improve hiding, although the brilliant luster of the pearlescent pigment will be reduced. A relative large amount of pearl pigment is suggested to use, so that the interference color is stronger at a specular angle, and minimum amount of TiO2 is needed for hiding.
Keep in mind, the brilliance of a pearlescent pigment is generally sacrificed when any opaque pigments or tints are added to improve hiding as described above.
Dispersion
Pearlescent pigments can be dispersed with general mixing, similar to that used for metallics. A key benefit of effect pigments, both pearlescent and metallic, is that there is no need to grind or mill the pigments to fully develop their color/effect. Nevertheless, a proper dispersion is still key to maximizing the appearance.
A good technique is to make a pre-mix of 25-35% pigment and 65-75% vehicle. Add increments of pigment to the stirred vehicle using a low-shear, axial flow mixer. The pigment will simply stir in quickly because of the relatively large particle size and be wetted out by the vehicle. Additional portions of pigment may be added as soon as the previous addition appears completely wetted. Another 15 minutes of mixing should ensure a good dispersion of pigment.
To prevent excessive fragmentation of the pigment platelets, or stripping of metal oxides off the mica substrates, high-shear equipment, such as ball or pebble mills, should be avoided. In general, pearlescent pigments should be added to a formulation at the end of mixing cycle, after all other ingredients have been thoroughly mixed. It is possible to use a radial flow, “saw tooth” high-speed disperser (Cowles dissolver), providing the pigment loading is below 25% and the tip speed of the blade is below 2,000 ft/minute. The height of the blade should be changed during the mixing cycle to distribute the material in the dead spot directly below the blade.
Incomplete dispersion of pigment can contribute to low tinting strength, poor rheological properties, appearance differences and even poor performance. The dispersion of pigment in coating can be verified visually using a microscope or by a relative technique using the settling rate and sediment volume of the pearlescent pigment.
In the microscopic technique, a visual determination is made to see if the platelets are agglomerated, as seen in Figure 7.
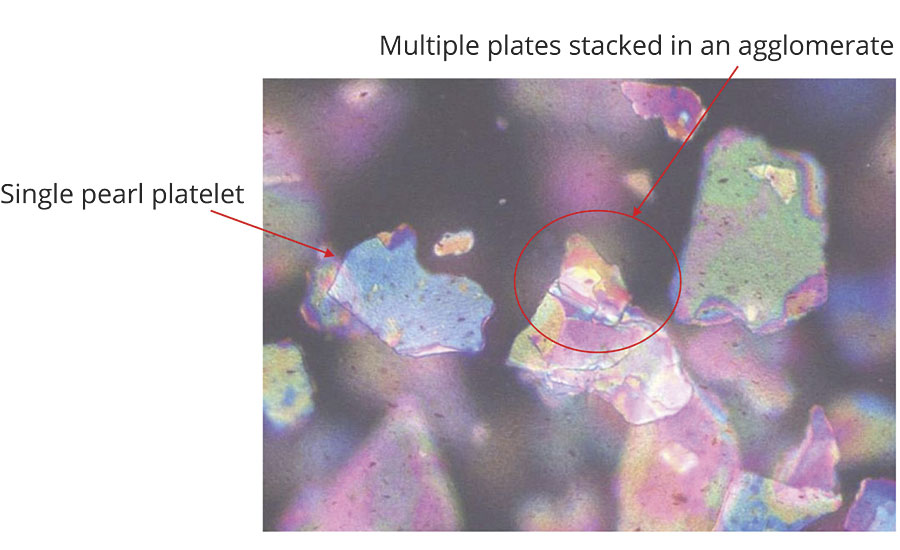
Precautions should be taken when using this technique because normally the pigment concentration is too high in a finished coating to accurately determine the dispersion. It is often necessary to reduce the pigment concentration in the coating with additional vehicle or solvent. This changes the system and may cause the pigment to flocculate or separate, leading to erroneous conclusions.
The settling technique uses the actual finished coating or a modified coating containing no rheology modifiers to determine the degree of dispersion. After several days of standing undisturbed, slow or incomplete settling indicates a good dispersion, as does the minimum sediment volume. The softness of packing is also considered for the evaluation because it is related to the re-dispersion. Due to the high density of pearlescent pigments, they will inevitably settle faster than most pigments, but re-dispersion should be simple if hard-packing is avoided. This is most difficult in waterborne systems.
Settling Prevention
Pearlescent pigments, like most inorganic pigments, have a specific gravity significantly higher than the vehicles in which they are dispersed, causing them to settle and accumulate in the bottom of a container. During storage, the pearl platelets will orient parallel to each other and compact close together, squeezing the vehicle from between them. The smooth surfaces of the platelets form a seal, resulting in hard packing, making redistribution difficult.
The occurrence of this hard packing layer can be mitigated not only by proper dispersion and suspension techniques, but also by the physical and chemical properties of the coating. Since this sedimentation occurs due to electrostatic interactions, the following actions can be taken to promote a softer sediment layer and allow for easy redispersion: adding non-polar solvents, increasing salt concentrations, decreasing the large aspect ratio particle sizes, and changing the high isoelectric point of the finished coating.
Suspension in Vehicles
Good suspension means the pigment particles are held well in the vehicles, providing more resistance to the settling tendency of pigment. Increasing viscosity of coatings is undoubtedly the simplest way to prevent settling by providing more resistance to pigment movement. However, it is limited by the application of coatings, and little can be done to change the viscosity. Furthermore, increasing viscosity will do little to prevent hard packing settling during long-term storage.
An alternative is to build a three-dimensional network structure in the vehicle by adding some special additives (suspending agent or thixotrope) like fumed silica or organophilic clay. These function by forming hydrogen bonds among themselves and with the vehicles, and even pigments. As a result, the association between pigment and vehicles creates a network that “traps” the pigment particles, and settling tendency is reduced. In addition, a clay or silica particle will also act as a spacer between the platelets if they do settle, preventing a tight seal from forming. The pigment can then quickly and easily be re-incorporated into the vehicle.
The efficiency of these additives is dependent on the type of solvent and resins. A variety of additives with different surface chemistry is available to fit different systems. Usually these additives should be incorporated during the wetting-dispersion step to achieve the best effect. However, some clays or silica require high shear and/or heat to be fully activated effectively. This should be done as a pre-grind prior to dispersing the pearl pigment. Care should be taken to follow the manufacturer’s guidelines.
Summary
Pearlescent pigments are a versatile group of effect pigments that are widely used in many coatings applications. Their color is a result of light interference based on their physical structure and composition. Their semi-transparent nature and specular reflection work together to produce mother-of-pearl effects and interesting color travel combinations. Pearlescent pigments are available in a wide range of sizes and colors that are easy to formulate and apply following a few simple rules.
For more information, e-mail Michael.Venturini@sunchemical.com or Anthony.Rohrer@sunchemical.com.
Looking for a reprint of this article?
From high-res PDFs to custom plaques, order your copy today!