Moisture-curing topcoats based on acrylic- and epoxy-alkoxysiloxane resins have been increasingly used as isocyanate-free alternatives in marine and protective applications. Similar to 2K polyurethanes, these systems display a broad range of performance characteristics, depending on their structure and composition. However, these alternatives have seen limited market penetration, due to an unfavourable cost/performance ratio.
This article presents a new family of polymers, which combine vinyl (neo)ester and vinyl alkoxysilane monomers. Variation of process parameters, monomer composition and alkoxysilane levels yielded a series of polymers with solids content between 70 and 100%, and exhibiting a wide range of attractive properties.
Performance evaluation of 1- and 2K moisture-cure coatings based on this cost-efficient and highly versatile technology demonstrates that it brings high solids content, fast hardness development and very long shelf life, in addition to being isocyanate-free. These factors make these vinyl silane copolymers an attractive alternative to 2K polyurethanes and acrylic-alkoxysiloxanes for several topcoat applications, especially protective coatings.
Moisture Curing Alkoxysilanes
Silicone-containing coatings play an ever-increasing role since their introduction in the mid-90’s. Today they are specified for a wide range of steel constructions, including highly demanding applications such as offshore platforms, storage tanks and pipes. They are particularly appreciated for their very high durability and have often replaced polyurethanes. The durability of polysiloxanes, [—Si—(O—Si)n—O—] can easily be understood considering that the Si—O bond is in an oxidized state and cannot be further oxidized, unlike carbon – carbon bonds in organic compounds. Furthermore, the bond dissociation energy for the Si—O bond is about 33% higher than that of C—C bonds. The extreme durability and resistance of glass, which is actually a giant polysiloxane network, exemplifies the outstanding properties of polysiloxanes well. Coatings based solely on polysiloxane resins, however, have limited market penetration. Instead, silicone coatings usually combine an inorganic polysiloxane with and organic resin.1
Today, most leading protective coatings suppliers offer silicone-containing coatings based on epoxy-polysiloxane and/or acrylic-polysiloxane chemistries. In both cases, an inorganic polysiloxane resin is reacted with the organic epoxy or acrylic resin to balance and optimize properties like viscosity, durability, cohesive strength and adhesion.2 To achieve optimal performance, the typical level of a methy-phenyl polysiloxane ranges from 37 to 77 wt%,2 which brings the cost of these systems to excessively high levels.
In the case of epoxy-polysiloxanes, the curing mechanism of the oxiranes is typically activated by an aminosilane monomer, like aminopropyltrimethoxysilane. The amine and the aliphatic epoxy must therefore be kept in two separate cans and mixed shortly before coating application to avoid premature curing (2K). After mixing and coating application, the curing via epoxy-amine organic crosslinking occurs within hours. This is complemented by an inorganic curing of silane groups, initiated by the ambient moisture (Figure 1). The combination of these two curing mechanisms, organic and inorganic, provides outstanding properties to the coatings.
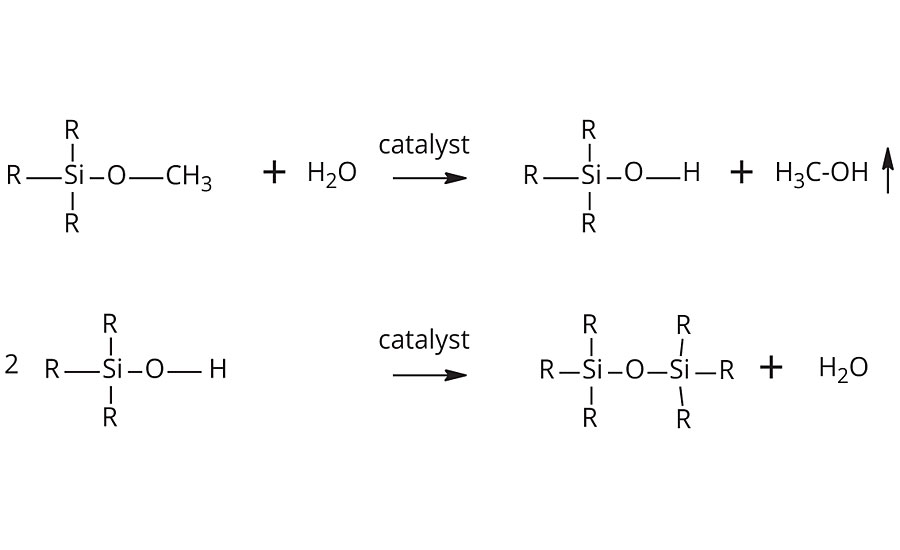
Acrylic-silane systems, on the other hand, cure only via the inorganic hydrolysis-condensation sequence of the silane groups.3 These systems are manufactured via radical copolymerization of silane-functional acrylates and (meth)acrylate monomers. Most commonly, gamma-methacrylopropyltrimethoxysilane (MPTMS) is reacted with methyl methacrylate, butyl acrylate and styrene or other vinyl monomers to form copolymers with pendant alkoxysilane groups.
Once a silane functional coating is applied, the moisture-curing process occurs in two steps. In the first step, the silane reacts with water to yield a silanol and an alcohol (typically methanol or ethanol). In the second step, two silanol groups condensate to form a siloxane bridge, with the release of one molecule of water. Half of the water consumed in the first step is thus released in the second step, ensuring further curing deeper into the coating. One or sometimes a mix of different catalysts is required to promote these hydrolysis-condensation reactions.
In theory, alkoxysilane-based acrylics could be easily formulated as single-component (1K) systems. The coatings should not begin to cure until they are applied to a surface and exposed to air and moisture. However, pigments and additives used in paint formulations usually contain some moisture, which can initiate premature curing in the can.4 Numerous solutions have been proposed to solve this issue, some with success. Certain solutions are based on the use of moisture scavengers5 while others use mixtures of reactive polysiloxanes and silane-free acrylic resins.6
Acrylic-silane polymers also need to be of sufficiently low molecular weight to achieve the required low viscosity for spraying, especially after being formulated into paints. Such low-molecular-weight polymers often require long curing times to develop mechanical properties, especially when applied at room temperature. It has therefore been proposed to mix these acrylic resins with polysiloxane resins to address this issue,2 however this solution leads to much higher cost.
Despite their high apparent potential, 1K moisture-cure alkoxysilane-acrylics have so far only achieved a fairly limited market penetration. The high cost of MPTMS monomer and the polysiloxane resins is probably partly responsible for this. Park et al. found excellent UV and weathering resistance in moisture-cured alkoxysilane-acrylic based coatings7 with a high level of MPTMS of up to 30 wt%.
Neocarboxylic Acid-Based Monomers for Coatings
In 1954, Koch and Huiskens of the Max Planck Institute in Germany described a three-step chemical reaction between mono-olefins, carbon monoxide and water leading to monocarboxylic acids8,9 with a high degree of branching. Acids prepared by this process, known as Koch acids, Versatic™ acids or neocarboxylic acids, can potentially be incorporated as such into polymers. However, they lack sufficient reactivity to achieve high conversion in conventional esterification reactions. This is why they are more commonly used in their vinyl or glycidyl (epoxy) ester derivative forms (Figure 2).
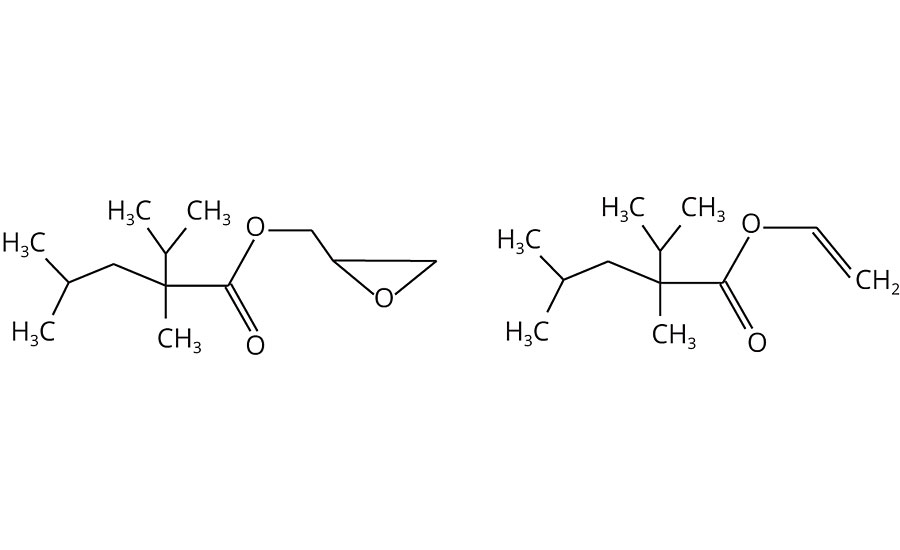
For more than 50 years, neoacid-based monomers have found most of their applications in the world of coatings, where they are well known for upgrading the performance and quality of vinyl, acrylic, polyester and other resins. The most common monomers used in these applications, based on C10 neoacids, are glycidyl neodecanoate and vinyl neodecanoate, with three to six methyl groups per molecule.
The chemical structure of these vinyl and glycidyl monomers, with a high number of methyl groups, contributes to a number of attractive properties of the derived coatings. Vinyl neodecanoate homopolymer was found to have a critical surface tension as low as 24 dyn/cm,10 and to provide high contact angles to derived coatings. Moreover, the tertiary structure of the original acid ensures excellent chemical stability, and the absence of aromatic structures explains excellent UV resistance. Vinyl neodecanoate and vinyl neononanoate are well known by resin and paint producers under their tradename VeoVa™ 10 and 9 monomers The homopolymer Tgs of these monomers are -3 °C and +70°C, respectively.
In the frame of the present work, an important difference between vinyl and (meth)acrylate esters derives from the orientation of their ester groups. In the case of (meth)acrylates, the ester group is electron withdrawing, whereas it is electron donating for the vinyl esters (Figure 3). This has a major influence on the reactivity of the respective double bonds in radical polymerization processes, as will be discussed below.
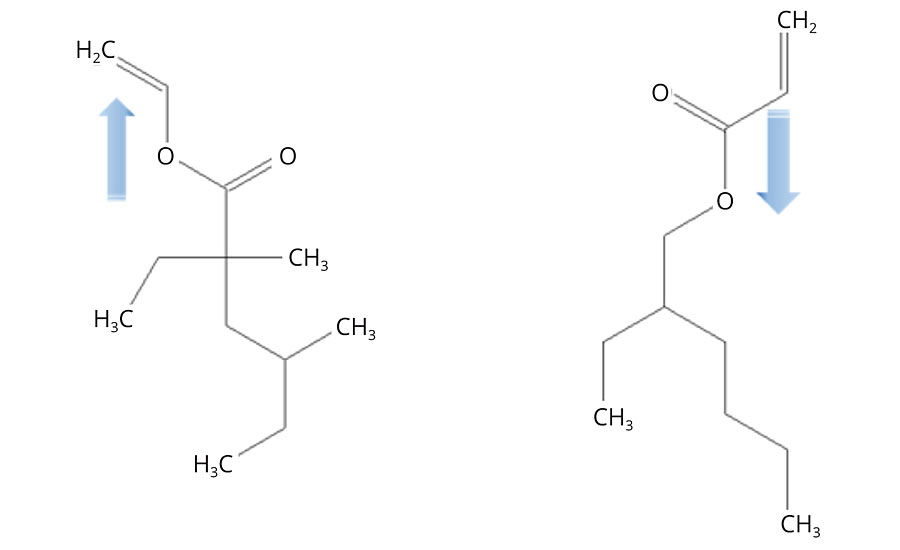
Vinyl Silanes
Vinyl trimethoxysilane (VTMOS) and the related vinyl triethoxysilane (VTES) are bi-functional compounds, featuring both a vinyl group and a hydrolytically sensitive alkoxy groups (Figure 4). Their alkoxy groups are activated and hence these silanes are extremely reactive towards water. The reason for this effect is an electronic interaction between the silicon atom and the electron donor in the a-position.11 VTMOS, in particular, is very well known by coatings formulators as an efficient and affordable water scavenger.
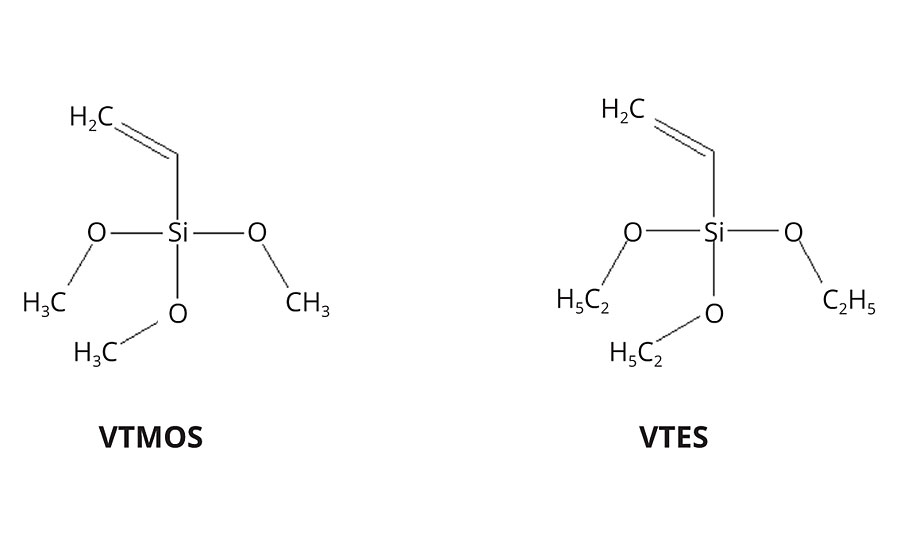
The vinyl group, on the other hand, has relatively low reactivity. It does therefore need highly activated radicals to be efficiently incorporated into polymer backbones by radical polymerization. Attempts to build VTMOS into (meth)acrylate polymers have therefore faced severe issues of final monomer conversion.12 VTMOS copolymers with more reactive radical monomers like ethylene are however well known, for example, in the field of electrical insulation for cables. Copolymers of VTMOS with vinyl acetate are for the same reason also well known in the field of emulsion paints.
Copolymerization of Vinyl Silanes and Vinyl Ester Monomers
To start the present work, we asked ourselves whether the vinyl silanes like VTMOS and VTES, and hydrophobic vinyl esters described above, could be combined into affordable and high-performance polymers for 1K, moisture-curing protective coatings. The reactivity ratios between these monomers are not available, but we could estimate them using an e and Q scheme as proposed by Alfrey and Price.13 Table 1 shows that calculated r1 and r2 are actually very close to 1. In practice, this means that vinyl silanes should distribute evenly in vinyl ester copolymer backbones. This important finding opens the possibility to use low-cost vinyl silane monomers as a crosslinker for high-performance protective coatings.

Experimental
The resins presented below combine vinyl alkoxysilane monomers with vinyl neodecanoate (VeoVa 10 monomer), vinyl neononanoate (VeoVa 9 monomer) and vinyl acetate monomers. Their detailed preparation procedure has been described in a recent patent application.14 Monomers were chosen in order to combine the unique properties of neoacid derivatives, such as hydrophobicity and durability, with the moisture-curing mechanism of silanes. In the first part of this work, resins were optimized for their performance in clear and pigmented topcoats. In a second step, selected vinyl silane resins for clear and pigmented protective topcoats were benchmarked against commercial systems: 2K polyurethanes and 1K acrylic-polysiloxanes.
Resin Optimization
The variables evaluated and the typical properties of resins are displayed in Tables 2 and 3. In particular, the glass transition temperatures of the polymers were manipulated by varying the ratios between vinyl esters. The molecular weight of the polymers was varied by modifying the process conditions and by using low levels of certain additional monomers. The resulting vinyl silane resins were then formulated into 1K moisture-curable clearcoats.
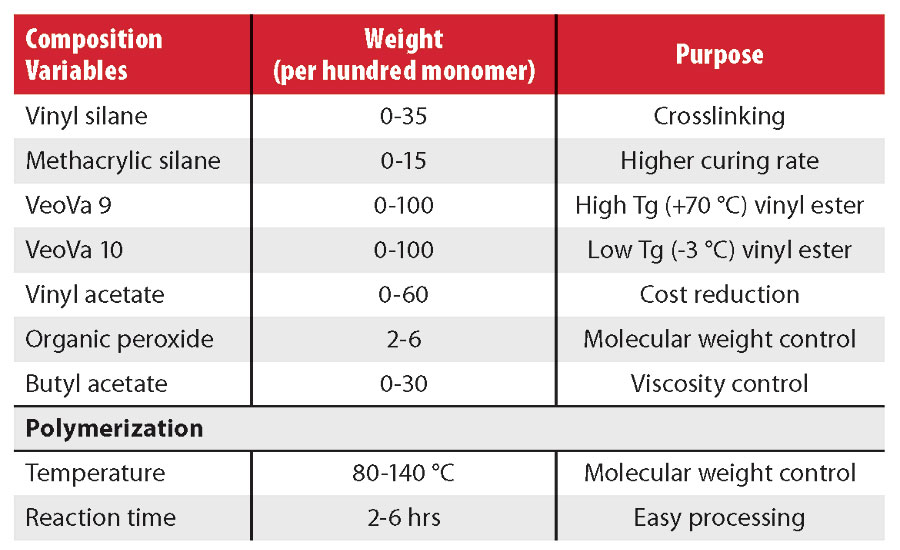
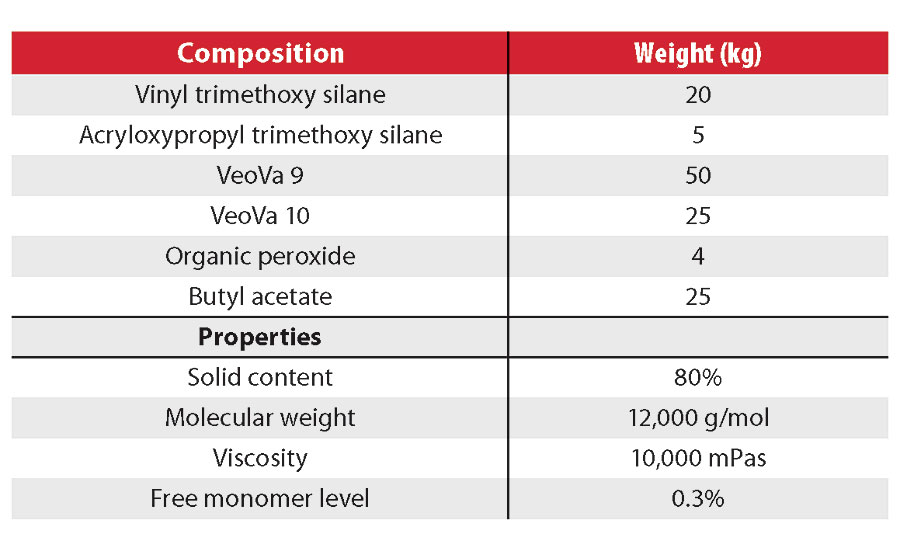
The various resins were mixed with catalysts and diluted with butyl acetate to the application viscosity (100 mPas). Films were then applied at 100 µm wet with a barcoater and allowed to dry at 23 °C and 50% relative humidity. Typical solids content of the clearcoats ranged from 65 to 70 wt%.
All formulated clearcoats (i.e. with catalyst) had a shelf life of at least several months. In some cases, skin formation was observed on top of the product in cans that had been open several times, indicating reaction with moisture from the air. In all cases, however, the bulk viscosity of the coatings remained constant. This important observation indicates that vinyl silane resins are suitable for true one-component (1K) coatings. For comparison, a similar clearcoat made from a reference acrylic silane resin had a shelf life of less than 1 hr, while the reference 2K polyurethane had a shelf life of 2 hrs.
The glass transition temperature (Tg) of the resins and the level and type of silane monomer were varied with the aim of optimizing cure speed, solvent resistance and coating flexibility. Figure 5 shows solvent resistance (MEK double rubs) of a series of clearcoats as a function of the level of silane after 7 days of drying at room temperature. Additional clearcoats with 25 wt% silane and Tgs ranging from +60 °C to -3 °C were also included in this evaluation. As expected, solvent resistance increases with the level of crosslinking monomers. However, the increase in solvent resistance with the decrease of the Tg may be somewhat surprising. This is possibly due to a limitation of the crosslinking density because of the reduced mobility of polymers with higher Tg.
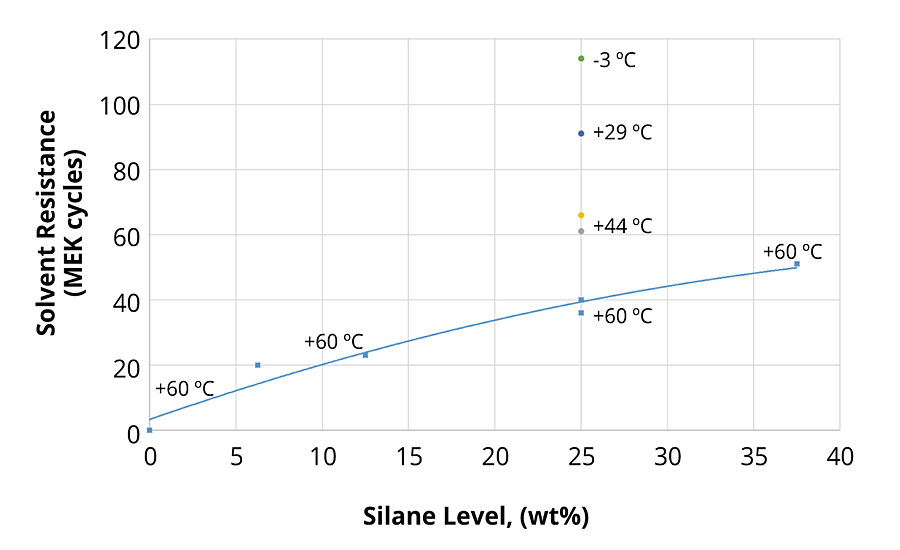
Silane groups attached to polymers with lower Tg, however, may have more opportunity to crosslink and thus to improve solvent resistance. This hypothesis is supported by the fact that the abrasion resistance of the clearcoats was also found to be better for resins with lower Tg. Further testing of both solvent and abrasion resistance of coatings cured at elevated temperatures supported this hypothesis. More details about this resin optimization work have been presented elsewhere.15
Benchmarking Exercise
After the optimization of the resins described above, a new series of resins were formulated into clear and pigmented topcoats (Table 4). A first resin was made using exclusively hydrophobic, branched vinyl esters (VeoVa 9 and 10 monomers) and methoxy silane monomers. In the second resin, ethoxy silanes replaced the methoxy silanes for HSE reasons. The third resin contains methoxy silane and 40 wt% vinyl acetate to minimize cost. The performance of the corresponding clearcoats was compared with a commercial 2K polyurethane. The pigmented topcoats were compared with both a commercial 2K polyurethane and two 1K acrylic-polysiloxane coatings (Table 5).
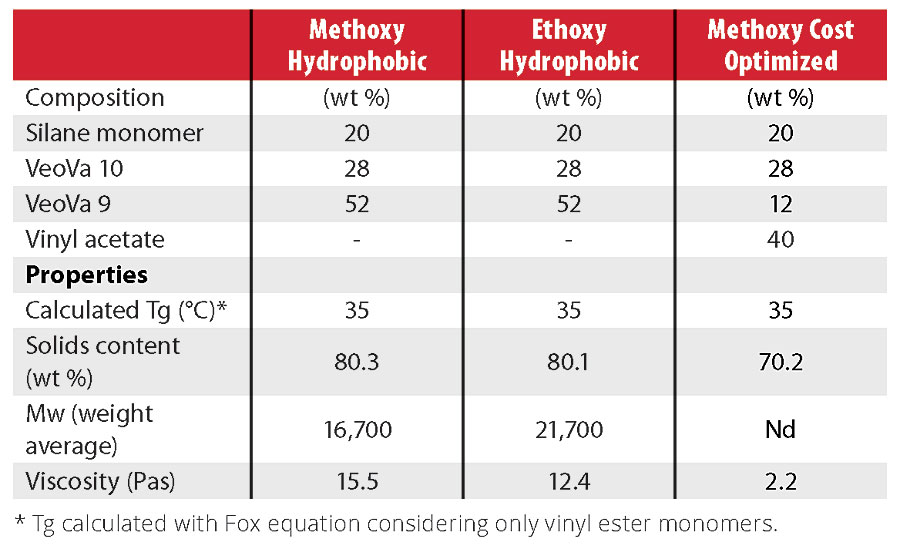
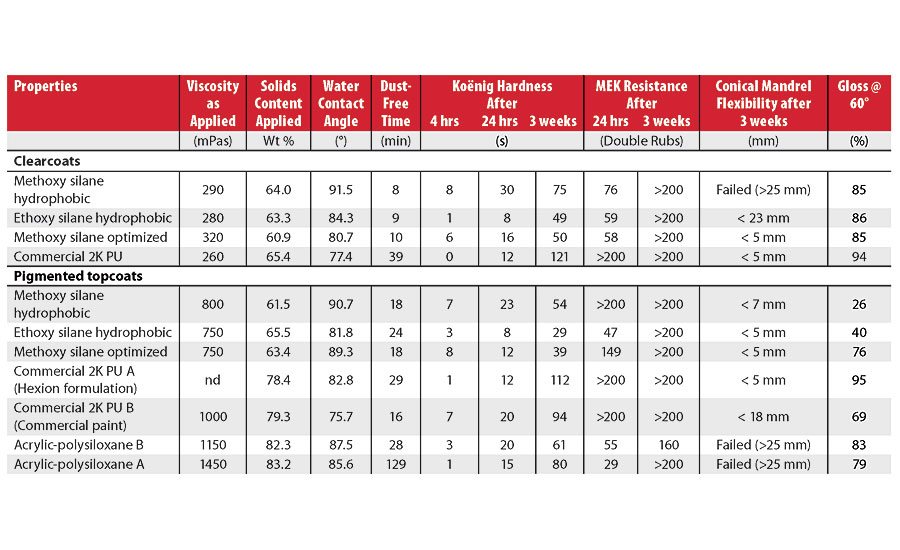
Clearcoat Performance
Table 5 shows that these vinyl silane systems have very short dust-free time and fast early hardness development when compared to the 2K PU system. These are critical properties for professional painters as they enable a higher productivity. The observed performance is probably mostly due to the high molecular weight of the vinyl silane resins combined with a Tg above room temperature. During the first four hours of drying, crosslinking of the methoxy-based vinyl silanes is also fast enough to ensure rapid hardness development and solvent resistance. The ethoxy silane system, on the other hand, cures slower than expected, yet also develops good performance over time. The cost-optimized system, containing vinyl-acetate, has slightly lower solvent resistance due to the more polar nature of vinyl acetate.
Pigmented Topcoat Performance
Figure 6 shows the development of Koënig hardness of the vinyl silane resins (solid lines) compared to the commercial 2K PU (dotted lines) and acrylic-polysiloxane (dashed lines) benchmarks. As expected, both methoxy silane-based topcoats show excellent hardness development during the first hours of drying.
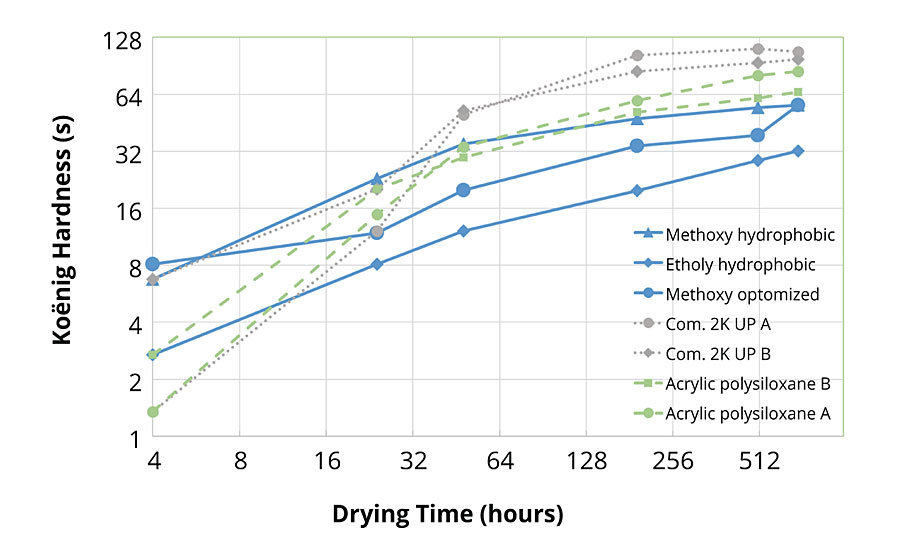
After 3 weeks, all polysiloxane systems exhibit lower hardness than the polyurethanes. Consequently, the softer vinyl silane systems exhibit better flexibility than the commercial acrylic-polysiloxanes (Table 5). The 2K PU A system, formulated in Hexion’s lab with a relatively soft isocyanate (HDI trimer), combines excellent hardness and flexibility after 3 weeks. However, this is at the expense of the early hardness development (<24 hrs). In contrast, the commercial 2K PU B, derived from the same polyol, lacks flexibility, probably because it is formulated with a hard isocyanate to ensure fast early hardness development.
Figure 7, which shows the balance of properties of the various systems on radar charts, illustrates the versatility of this new technology very well. As can be seen, a significantly better balance of properties than the commercial acrylic-polysiloxane paints is obtained.
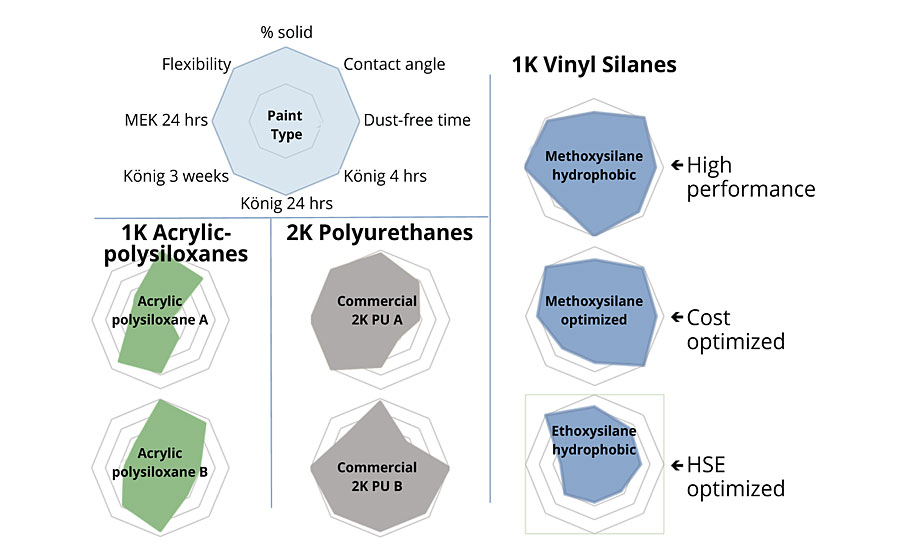
Conclusions
- Vinyl silane resins can be formulated into high-performance, true 1K protective coatings. Unlike with 2K PU systems, end users using these new systems do not need to mix two components shortly before use. Because true 1K systems have very long pot lives, users do not need to dispose of the unused mixed coating.
- Vinyl silane systems are free of isocyanates.
- High-solids coatings based on vinyl silane binders can be formulated to deliver very fast early hardness development, combined with good flexibility, solvent resistance and final hardness.
- Vinyl silane-based protective coatings exhibit better balance of properties compared to commercial 1K acrylic-polysiloxanes, at reduced cost.
References
1 Pierre, D. Dow Corning Belgium, European Coatings Conferences, Nuremberg, 2013.
2 Graversen, E. Hempel, International Paint and Coating Magazine, October 2011, 4-17.
3 Iezzi, R.; Martin, J.; Tagert, J.; Selbodnick, P.; Wegand, J.; Lemieux, E. NRL review, featured research, 2013, 1, 88-98.
4 Chang et al., PPG Industries Inc, US 4043953.
5 Nixon, S. et al, Akzo Nobel Coatings International BV, European Patent EP 1 292 650.
6 Nixon, S. et al, Akzo Nobel Coatings International BV, European Patent EP 1,587,889.
7 Hong-Soo Park et al., Journal of Applied Polymer Science, 2001, 81, 1614-1623.
8 Herbert Koch and Wilhelm Huisken, Max Plank Institute German patent DE972315C.
9 Falbe, J. New Synthesis with Carbon Monoxide, Springer-Verlag, 1980, ISBN 3-540-09674-4.
10 Basset, D. Journal of Coatings Technology, 2001, 73, 43-55.
11 Schindler, W. Wacker, European Coatings Conference, 2005 available at https://www.wacker.com/cms/media/publications/downloads/6190_EN.pdf.
12 D. Paquet et al., Dupont de Nemours, WO 2003078486 A1.
13 Alfrey, T.; Price, C.C.; J. Polym. Sci, Vol. 2, No. 1, 101 (1947).
14 Heymans D. and Romanowska C., Hexion Research Belgium, EP 3363827 A1.
15 Herszenhaut, M.; Romanowska, C.; Heymans, D. Hexion, SSPC Coatings conference, Orlando, 2019 February 11-14.
Report Abusive Comment